- お役立ち記事
- Effective use of statistical quality control (SQC) and improvement of quality and reliability
月間77,185名の
製造業ご担当者様が閲覧しています*
*2025年2月28日現在のGoogle Analyticsのデータより
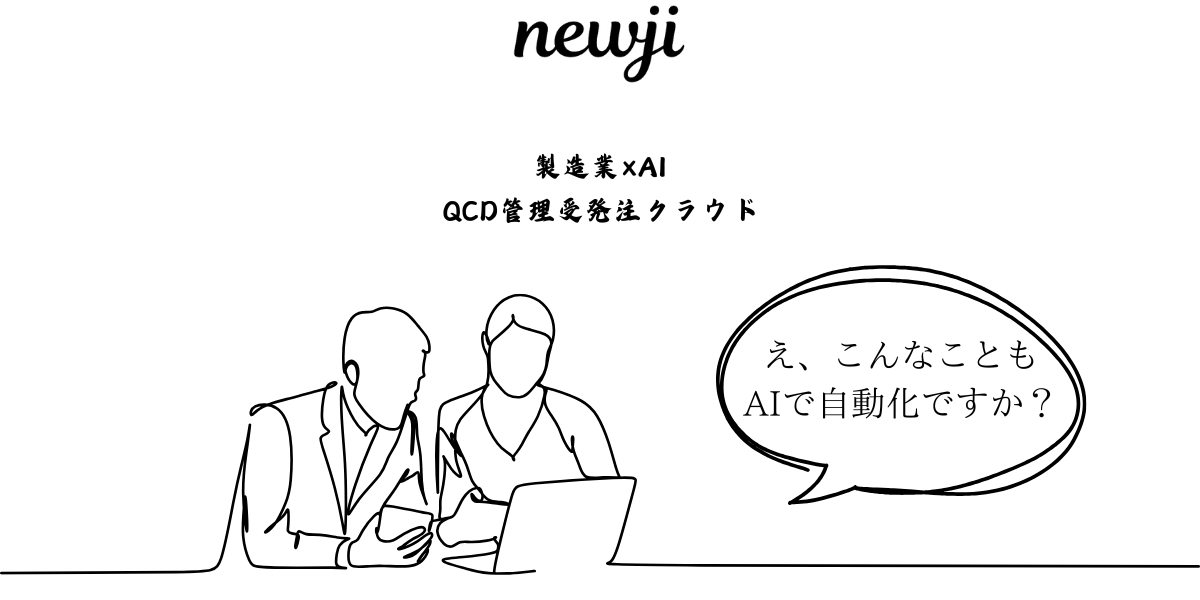
Effective use of statistical quality control (SQC) and improvement of quality and reliability
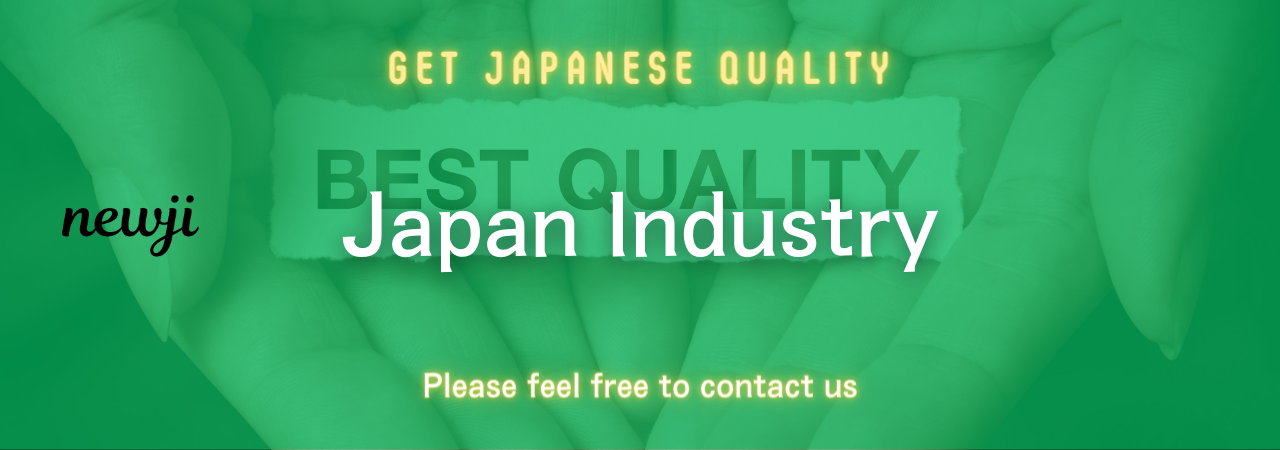
目次
Understanding Statistical Quality Control (SQC)
Statistical Quality Control (SQC) is a set of statistical methods and tools used to monitor and control the quality of products and services.
By applying these techniques, organizations can ensure that their production processes meet the required quality standards.
SQC is essential in identifying variations and defects in production, allowing for timely corrections and improvements.
This approach leverages statistical techniques to identify whether a process is stable and predictable, ensuring that any deviations from standard can be quickly addressed.
Implementing SQC in a business not only enhances product quality but also boosts customer satisfaction and company reputation.
The Importance of Quality and Reliability
Quality and reliability are critical aspects in any industry, directly impacting customer satisfaction and loyalty.
High-quality products reduce defects and wasted resources, ultimately leading to cost savings.
Reliability ensures that a product performs consistently over its expected life cycle, which is crucial for maintaining customer trust.
Organizations that focus on improving quality and reliability can differentiate themselves in competitive markets.
They can lead the way in innovation and customer satisfaction, achieving greater market share and business success.
Key Methods in Statistical Quality Control
There are several key methods used in SQC to achieve quality and reliability.
1. Control Charts
Control charts are tools used to plot data over time, helping to identify trends, variations, and shifts in a process.
They provide a visual representation of process stability, allowing for quick detection of abnormalities that need correction.
Control charts are particularly useful in determining whether variations are due to common causes or special causes, guiding process adjustments.
2. Process Capability Indices
Process capability indices, such as Cp and Cpk, measure how well a process can produce products within specified limits.
These indices give insights into the capability of a production process to meet quality standards, highlighting areas for potential improvement.
A higher process capability index indicates a more reliable process with fewer deviations.
3. Pareto Analysis
Pareto analysis applies the Pareto principle (80/20 rule) to quality control, identifying the most significant factors affecting quality.
By focusing on the few key contributors to defects, organizations can prioritize improvement efforts for maximum impact.
4. Cause-and-Effect Diagrams
Cause-and-effect diagrams, also known as fishbone or Ishikawa diagrams, help in identifying potential causes of defects or failures.
They organize potential causes into categories, making it easier to assess and address the root causes of quality issues.
Implementing Statistical Quality Control
Effective implementation of SQC involves several steps.
Training and Education
Training employees in SQC techniques is crucial to ensure successful implementation.
Staff should be proficient in using statistical tools and interpreting data effectively.
Data Collection and Analysis
Collecting accurate and relevant data is the backbone of SQC.
Organizations should implement robust data collection methods, ensuring that the gathered data helps in monitoring and analyzing quality effectively.
Continuous Monitoring and Feedback
Continuous monitoring through control charts and other SQC tools helps detect variations instantly.
Immediate feedback allows for timely corrective actions and improvements.
Integrating SQC with Other Quality Frameworks
Integrating SQC with other quality frameworks like Six Sigma and Total Quality Management (TQM) amplifies the benefits.
Such integration fosters a holistic approach to process improvement and quality management.
Benefits of SQC in Enhancing Quality and Reliability
Effective use of SQC can lead to numerous benefits.
Improved Product Quality
With SQC, organizations can achieve greater product consistency and fewer defects.
This improvement reduces rework and waste, leading to cost savings.
Increased Customer Satisfaction
High-quality and reliable products lead to happy customers, enhancing business reputation and customer loyalty.
Operational Efficiency
SQC promotes process efficiency by identifying and reducing variations, leading to streamlined operations and optimal resource utilization.
Better Decision Making
Statistical methods provide valuable insights into processes, aiding informed decision-making.
Organizations can adjust and control processes based on data, ensuring continuous improvement.
Challenges in Implementing Statistical Quality Control
While SQC offers many advantages, there are challenges that need addressing.
Data Quality
Accurate data collection is essential for successful SQC.
Improperly collected or inaccurate data can lead to misguided conclusions and ineffective improvements.
Resistance to Change
Employees may resist adopting new methods and tools.
Strong leadership and a culture of continuous improvement are necessary to overcome resistance and ensure successful SQC implementation.
Resource Intensive
Implementing SQC can be resource-intensive, requiring investment in training and tools.
Organizations must weigh the upfront costs against long-term benefits when considering SQC.
Conclusion
Effective use of Statistical Quality Control is key to improving the quality and reliability of products and services.
By implementing SQC, organizations can achieve greater consistency, reduced defects, and increased customer satisfaction.
Although challenges exist, they can be overcome with proper training, robust data collection, and a culture of continuous improvement.
Businesses that leverage SQC techniques are better positioned to succeed in competitive markets and meet increasing customer demands for high-quality products.
資料ダウンロード
QCD管理受発注クラウド「newji」は、受発注部門で必要なQCD管理全てを備えた、現場特化型兼クラウド型の今世紀最高の受発注管理システムとなります。
ユーザー登録
受発注業務の効率化だけでなく、システムを導入することで、コスト削減や製品・資材のステータス可視化のほか、属人化していた受発注情報の共有化による内部不正防止や統制にも役立ちます。
NEWJI DX
製造業に特化したデジタルトランスフォーメーション(DX)の実現を目指す請負開発型のコンサルティングサービスです。AI、iPaaS、および先端の技術を駆使して、製造プロセスの効率化、業務効率化、チームワーク強化、コスト削減、品質向上を実現します。このサービスは、製造業の課題を深く理解し、それに対する最適なデジタルソリューションを提供することで、企業が持続的な成長とイノベーションを達成できるようサポートします。
製造業ニュース解説
製造業、主に購買・調達部門にお勤めの方々に向けた情報を配信しております。
新任の方やベテランの方、管理職を対象とした幅広いコンテンツをご用意しております。
お問い合わせ
コストダウンが利益に直結する術だと理解していても、なかなか前に進めることができない状況。そんな時は、newjiのコストダウン自動化機能で大きく利益貢献しよう!
(β版非公開)