- お役立ち記事
- Effective way to proceed with FMEA and DR and practical training course
月間76,176名の
製造業ご担当者様が閲覧しています*
*2025年3月31日現在のGoogle Analyticsのデータより
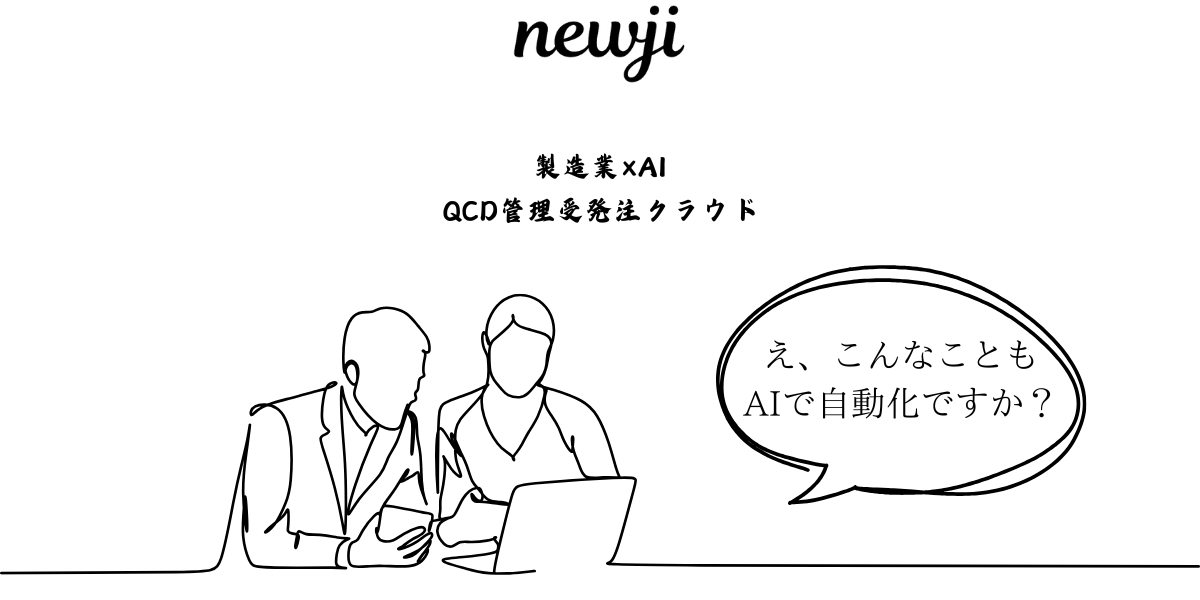
Effective way to proceed with FMEA and DR and practical training course
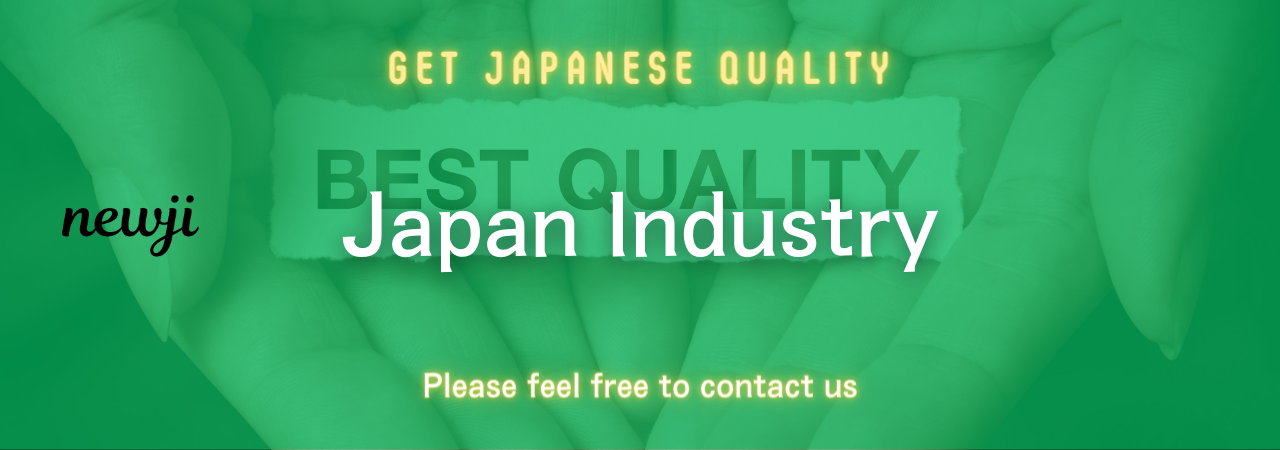
FMEA, or Failure Mode and Effects Analysis, and DR, Design Review, are two important processes used in product development and quality assurance.
They help organizations identify potential failure modes, improve product design, and minimize risks.
In this article, we will discuss effective ways to implement FMEA and DR, along with practical training courses to enhance these processes.
目次
Understanding FMEA and Its Importance
FMEA is a systematic approach used to identify and evaluate potential failures in a product or process.
It helps organizations analyze the effects of these failures and implement measures to prevent them.
By doing so, it ensures the reliability, safety, and quality of the product.
FMEA is crucial in reducing costs associated with failures, enhances customer satisfaction, and improves overall product performance.
It is widely used across various industries, including automotive, aerospace, healthcare, and manufacturing.
Key Steps in Conducting FMEA
1. Assemble a Cross-Functional Team
To conduct an effective FMEA, it is important to assemble a team with diverse expertise and knowledge about the product or process.
This team should include members from design, manufacturing, quality, and other relevant departments.
2. Define the Scope and Objectives
Before starting the FMEA process, clearly define its scope and objectives.
Understand what products or processes are to be analyzed and determine the specific goals of the analysis.
3. Identify Potential Failure Modes
List all possible failure modes that could occur during the product’s lifecycle.
Collaborate with team members to brainstorm and identify as many failure modes as possible.
These could range from design issues to material weaknesses.
4. Analyze the Effects of Failures
Evaluate the effects of each potential failure mode on the product, process, and end-user.
Consider both direct and indirect impacts and document them meticulously.
5. Prioritize Failure Modes
Assign a risk priority number (RPN) to each failure mode based on its severity, occurrence, and detection probability.
Prioritize failure modes with higher RPN values for immediate attention and resolution.
6. Develop Action Plans
Create action plans to address and mitigate the prioritized failure modes.
Assign responsibilities, deadlines, and required resources for each action item.
7. Implement and Monitor Corrective Actions
Execute the action plans, continuously monitor their effectiveness, and update the FMEA documentation accordingly.
Regular reviews are necessary to address any emerging issues promptly.
Effective Design Review (DR) Process
A Design Review is an objective evaluation of a product’s design to ensure it meets all specified requirements and functions correctly.
It helps identify potential design flaws early in the development cycle, preventing costly modifications later.
1. Schedule Regular Reviews
Plan regular design review meetings throughout the product development process.
These meetings should be scheduled at key milestones to ensure timely evaluations and feedback.
2. Involve Relevant Stakeholders
Invite all relevant stakeholders to participate in the design review process.
This includes engineers, designers, quality experts, customers, and suppliers.
Their input and feedback are essential for a comprehensive assessment.
3. Prepare Comprehensive Documentation
Provide detailed documentation of the product design, including specifications, drawings, and related data.
This documentation serves as a reference point during the review and helps stakeholders make informed decisions.
4. Conduct In-Depth Reviews
Conduct thorough reviews of the design against the established criteria and requirements.
Identify potential issues, assess risks, and propose solutions to improve the design.
5. Document Review Outcomes
Record all feedback, suggestions, and decisions made during the design review process.
Ensure that these outcomes are communicated to the relevant teams for implementation and follow-up.
6. Implement Agreed Changes
Implement the necessary changes to the design based on the review outcomes.
Ensure that modifications align with project timelines and do not compromise quality and performance.
Practical Training Courses for FMEA and DR
Training is an essential component for successfully implementing FMEA and DR in any organization.
Practical training courses can enhance the skills of team members, equipping them to carry out these processes effectively.
1. Choose the Right Training Provider
Select a reliable training provider that specializes in FMEA and DR courses.
Check their credentials, reviews, and course content to ensure they offer comprehensive and updated training.
2. Tailor Training to Your Needs
Opt for training programs that can be customized to meet your organization’s specific needs.
Tailored training ensures that participants gain relevant insights and practical skills applicable to their roles.
3. Hands-On Learning Experience
Select courses that emphasize hands-on learning and real-world applications.
Case studies, simulations, and group exercises help participants understand and apply concepts effectively.
4. Certification and Continuous Learning
Aim for training courses that offer certification upon completion.
Certification not only verifies the participant’s skills but also adds value to their professional profile.
Encourage continuous learning by offering advanced courses and workshops periodically.
Implementing effective FMEA and DR processes, coupled with practical training, can greatly benefit organizations in delivering high-quality products and enhancing customer satisfaction.
By identifying and addressing potential issues early, companies can minimize risks, reduce costs, and ensure smooth product development cycles.
資料ダウンロード
QCD管理受発注クラウド「newji」は、受発注部門で必要なQCD管理全てを備えた、現場特化型兼クラウド型の今世紀最高の受発注管理システムとなります。
ユーザー登録
受発注業務の効率化だけでなく、システムを導入することで、コスト削減や製品・資材のステータス可視化のほか、属人化していた受発注情報の共有化による内部不正防止や統制にも役立ちます。
NEWJI DX
製造業に特化したデジタルトランスフォーメーション(DX)の実現を目指す請負開発型のコンサルティングサービスです。AI、iPaaS、および先端の技術を駆使して、製造プロセスの効率化、業務効率化、チームワーク強化、コスト削減、品質向上を実現します。このサービスは、製造業の課題を深く理解し、それに対する最適なデジタルソリューションを提供することで、企業が持続的な成長とイノベーションを達成できるようサポートします。
製造業ニュース解説
製造業、主に購買・調達部門にお勤めの方々に向けた情報を配信しております。
新任の方やベテランの方、管理職を対象とした幅広いコンテンツをご用意しております。
お問い合わせ
コストダウンが利益に直結する術だと理解していても、なかなか前に進めることができない状況。そんな時は、newjiのコストダウン自動化機能で大きく利益貢献しよう!
(β版非公開)