- お役立ち記事
- Effectiveness verification process of Igusa products at nursing care facilities and contractor selection
月間76,176名の
製造業ご担当者様が閲覧しています*
*2025年3月31日現在のGoogle Analyticsのデータより
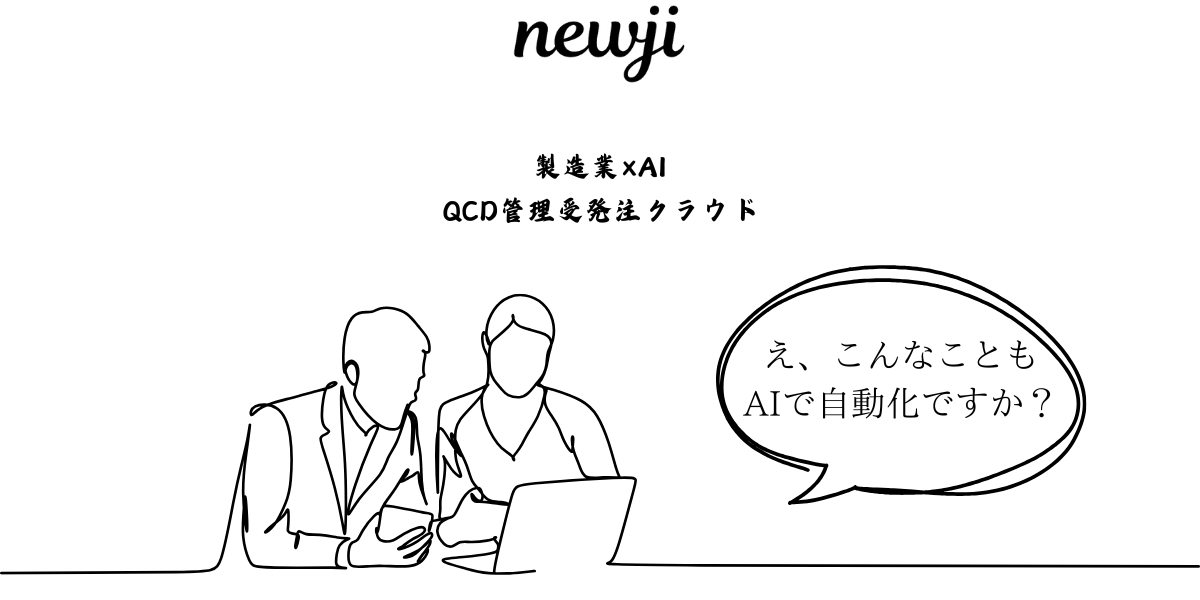
Effectiveness verification process of Igusa products at nursing care facilities and contractor selection
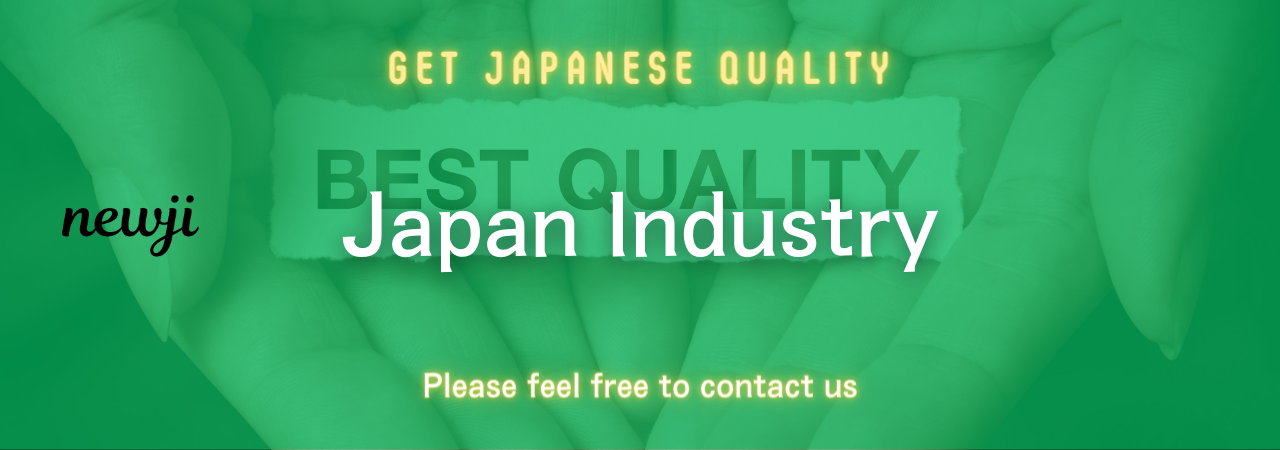
目次
Understanding the Effectiveness Verification Process
When nursing care facilities look to adopt new products, the primary focus is often on improving the quality of care provided to residents.
One innovative material gaining attention in this sector is Igusa, a traditional rush grass known for its durability and antimicrobial properties.
However, before these products are widely adopted, they must undergo a rigorous effectiveness verification process.
Understanding this process is crucial for facilities to make informed decisions about product implementation.
What is Igusa?
Igusa, also known as Japanese rush grass, has been used traditionally in tatami mats.
Its natural properties make it a promising material for use in various settings, including nursing care facilities.
Igusa is notable for its resilience, ability to absorb moisture, and natural antimicrobial qualities, making it ideal for environments that require high hygiene standards.
These features can potentially enhance the comfort and health of facility residents, reducing the spread of infections and improving air quality.
The Importance of Effectiveness Verification
When introducing any new product into a sensitive environment like a nursing home, understanding its impact is critical.
Conducting a thorough effectiveness verification process helps ensure the product meets safety and efficacy standards.
Evaluation Criteria
To verify the effectiveness of Igusa products, several key criteria are typically assessed:
1. **Durability and Maintenance**: The product’s longevity and resistance to wear and tear are crucial.
Facilities need products that can withstand daily use without frequent replacement or repair.
2. **Hygiene and Antimicrobial Properties**: Given the vulnerability of nursing home residents to infections, the product’s ability to deter microbial growth is vital.
Tests must demonstrate the material’s capacity to maintain hygiene over time.
3. **Comfort and Aesthetic**: Nursing care facilities seek to create comforting environments for residents.
The tactile feel and visual appeal of Igusa products must meet these requirements.
4. **Environmental Impact**: Sustainability is becoming increasingly important, with many facilities looking to minimize their environmental footprint.
Igusa’s natural composition supports eco-friendly initiatives and contributes to sustainable practices.
Steps in the Verification Process
The effectiveness verification process typically involves the following steps:
1. **Preliminary Assessment**: An initial evaluation of the product’s features and potential benefits is conducted.
This involves reviewing existing studies and data about Igusa’s properties.
2. **Controlled Testing**: Controlled, small-scale trials in nursing home settings are performed to observe the product in action.
During this phase, feedback from staff and residents is collected to analyze performance in real-world conditions.
3. **Compliance and Safety Checks**: All products must adhere to local regulations and safety standards.
This step involves rigorous testing to ensure compliance with applicable health and safety codes.
4. **Data Analysis**: Information from trials is analyzed to determine the product’s overall effectiveness and any areas for improvement.
5. **Final Report and Recommendations**: A comprehensive report summarizing the findings and offering recommendations is prepared.
This helps decision-makers understand the implications and benefits of adopting Igusa products.
Selecting the Right Contractor
Once a product has passed the effectiveness verification process, the next step is to select a reliable contractor for implementation.
Criteria for Selecting a Contractor
Choosing the right contractor is essential to ensure the quality and success of product integration.
Key criteria to consider include:
1. **Experience**: Contractors with experience in installing similar products in nursing care facilities can provide valuable insights and expertise.
2. **Reputation**: Consider contractors with a strong reputation for reliability and quality work.
Reviews and references from previous clients can be informative.
3. **Certification and Compliance**: Ensure the contractor is certified and compliant with industry standards and regulations related to health care facilities.
4. **Cost and Budgeting**: While quality should not be compromised, it’s important to select a contractor whose pricing aligns with the facility’s budget.
Steps in Contractor Selection
The process of selecting a contractor involves several strategic steps:
1. **Identify Potential Contractors**: Compile a list of qualified contractors based on the criteria outlined above.
2. **Request Proposals**: Solicit detailed proposals from each contractor to understand their approach, timelines, and cost estimates.
3. **Conduct Interviews and Site Visits**: Interviews with the contractors and visits to their past project sites can provide additional insights into their capabilities.
4. **Evaluate Proposals**: Assess each proposal against a predetermined set of requirements and criteria to identify the most suitable candidate.
5. **Make a Decision**: Based on evaluations, make an informed decision and proceed with a contract agreement with the chosen contractor.
Conclusion
The integration of Igusa products in nursing care facilities can potentially revolutionize care environments, enhancing both comfort and health standards.
A rigorous effectiveness verification process ensures the product’s suitability and safety, while careful contractor selection ensures quality installation and implementation.
By following these structured processes, nursing care facilities can make confident, informed decisions that benefit their residents and staff.
資料ダウンロード
QCD管理受発注クラウド「newji」は、受発注部門で必要なQCD管理全てを備えた、現場特化型兼クラウド型の今世紀最高の受発注管理システムとなります。
ユーザー登録
受発注業務の効率化だけでなく、システムを導入することで、コスト削減や製品・資材のステータス可視化のほか、属人化していた受発注情報の共有化による内部不正防止や統制にも役立ちます。
NEWJI DX
製造業に特化したデジタルトランスフォーメーション(DX)の実現を目指す請負開発型のコンサルティングサービスです。AI、iPaaS、および先端の技術を駆使して、製造プロセスの効率化、業務効率化、チームワーク強化、コスト削減、品質向上を実現します。このサービスは、製造業の課題を深く理解し、それに対する最適なデジタルソリューションを提供することで、企業が持続的な成長とイノベーションを達成できるようサポートします。
製造業ニュース解説
製造業、主に購買・調達部門にお勤めの方々に向けた情報を配信しております。
新任の方やベテランの方、管理職を対象とした幅広いコンテンツをご用意しております。
お問い合わせ
コストダウンが利益に直結する術だと理解していても、なかなか前に進めることができない状況。そんな時は、newjiのコストダウン自動化機能で大きく利益貢献しよう!
(β版非公開)