- お役立ち記事
- Effects of introducing DX technology in the manufacturing industry to update maintenance plans
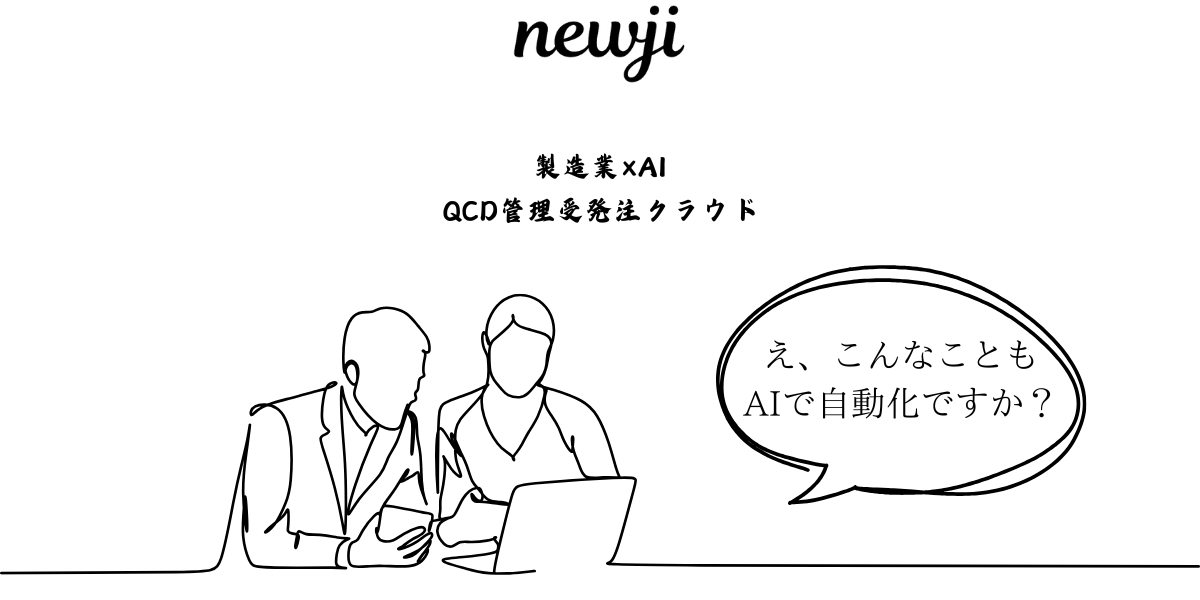
Effects of introducing DX technology in the manufacturing industry to update maintenance plans
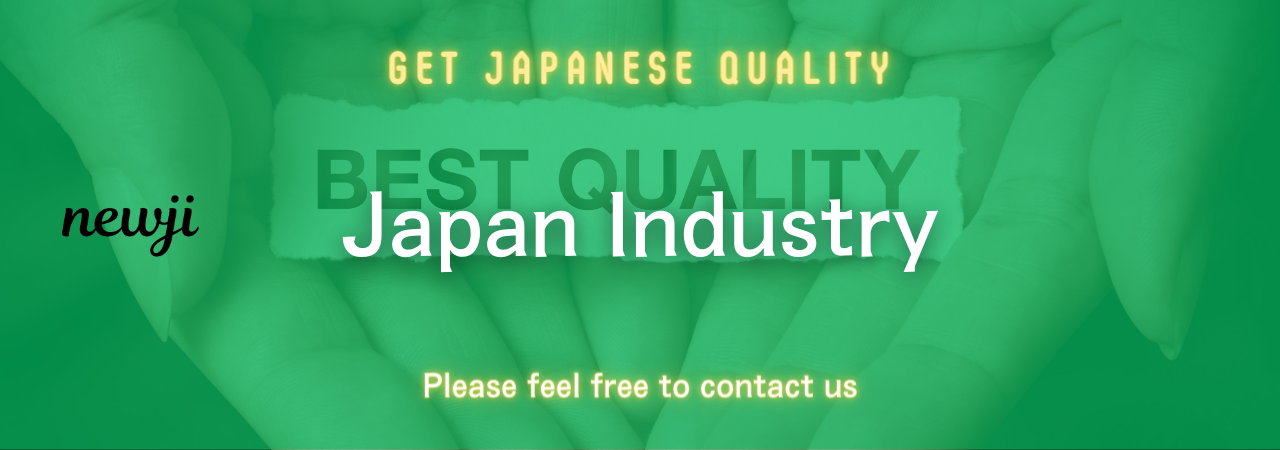
目次
Understanding DX Technology in Manufacturing
Digital transformation (DX) is revolutionizing industries across the globe, and the manufacturing sector is no exception.
In the context of the manufacturing industry, DX technology refers to the process of integrating digital technology into all areas of a business.
This transformation can improve processes, increase efficiency, and drive innovation.
In particular, DX technology plays a crucial role in updating maintenance plans for manufacturing companies.
By incorporating digital tools and techniques, manufacturers can enhance the way they maintain machinery and equipment, ensuring smoother operations and minimizing downtime.
Why Maintenance Plans Matter
Maintenance plans are vital for manufacturing companies because they outline how and when equipment and machinery should be serviced.
Proper maintenance ensures that machines operate efficiently, reducing the risk of unexpected breakdowns that could disrupt production.
Regular maintenance minimizes costly repairs, extends the lifespan of equipment, and guarantees safety for workers.
However, traditional maintenance plans often rely on manual methods or outdated technology, which can be both time-consuming and prone to errors.
This is where DX technology steps in, offering innovative solutions to automate and optimize maintenance processes.
Benefits of Digital Transformation in Maintenance
Enhancing Predictive Maintenance
One of the most significant advantages of DX technology in the manufacturing industry is its ability to facilitate predictive maintenance.
Predictive maintenance uses data analytics, sensors, and machine learning to predict when equipment might fail, allowing manufacturers to address issues before they occur.
With the aid of IoT (Internet of Things) devices, sensors can continuously monitor equipment performance and collect valuable data.
This data is analyzed to identify patterns or anomalies, empowering manufacturers to conduct maintenance based on actual machine conditions rather than relying on predetermined schedules.
This approach significantly reduces downtime, lowers maintenance costs, and enhances overall operational efficiency.
Improving Real-time Monitoring
DX technology enables real-time monitoring of machinery and equipment.
Manufacturers can track performance metrics and receive instant alerts if a machine deviates from its normal operating conditions.
This real-time capability ensures that maintenance teams are informed immediately of any problems, enabling quick responses.
Mobile applications and cloud-based platforms allow technicians to access data from anywhere, providing flexibility and timely updates, resulting in faster decision-making and problem-solving.
Streamlining Maintenance Operations
With digital transformation, manufacturers can streamline their maintenance operations through automated workflows and digital checklists.
DX technology replaces paper-based records with digital systems, reducing paperwork and ensuring accuracy in record-keeping.
Additionally, scheduling and reporting can be automated, ensuring that the right technicians are available when needed and that all maintenance activities are logged correctly.
Such automation optimizes resource allocation, making maintenance operations more efficient and reducing administrative burdens on the staff.
Implementing DX Technology: Challenges and Solutions
Despite the clear benefits, implementing DX technology in maintenance plans can be challenging.
However, understanding these challenges and their solutions can help manufacturers successfully navigate the transition.
Overcoming Resistance to Change
One of the primary challenges in adopting DX technology is resistance to change from employees who are accustomed to traditional methods.
Training and shift in mindset are critical when transitioning to digital tools.
Manufacturers should invest in comprehensive training programs to familiarize their staff with new technologies.
With structured training and hands-on experience, employees will become more comfortable and confident in using digital tools.
Ensuring Data Security
As manufacturing processes become more digitalized, ensuring data security is paramount.
The increased connectivity of devices and systems can make networks vulnerable to cyber threats.
To mitigate these risks, manufacturers should implement robust cybersecurity measures.
Regular security audits, encryption, secure communication protocols, and employee awareness programs are essential to safeguard sensitive data and prevent unauthorized access.
Managing Costs
While digital transformation can be costly, the long-term benefits outweigh the initial investment.
Financial constraints might deter some companies from making the switch, but it’s essential to look at the long-term value.
Manufacturers should begin with small-scale pilots to test the impact of DX technology.
By demonstrating success in specific areas, they can build a business case for broader implementation and secure buy-in from stakeholders.
The Future of Maintenance in the Manufacturing Industry
The integration of DX technology into maintenance plans is transforming the manufacturing industry and paving the way for more innovative approaches.
As technology advances, manufacturers can expect even more sophisticated solutions.
Augmented reality (AR) for remote maintenance guidance, blockchain for more secure data sharing, and more advanced AI algorithms for predictive analytics are just some of the developments on the horizon.
By embracing DX technology, manufacturers not only enhance their maintenance strategies but also position themselves to stay competitive in an increasingly digital world.
Those who adapt to these changes are likely to see improved efficiency, reduced costs, and a stronger market position.
Ultimately, the transition to digital maintenance plans is not just an upgrade; it’s a necessity for the modern manufacturing landscape.
資料ダウンロード
QCD調達購買管理クラウド「newji」は、調達購買部門で必要なQCD管理全てを備えた、現場特化型兼クラウド型の今世紀最高の購買管理システムとなります。
ユーザー登録
調達購買業務の効率化だけでなく、システムを導入することで、コスト削減や製品・資材のステータス可視化のほか、属人化していた購買情報の共有化による内部不正防止や統制にも役立ちます。
NEWJI DX
製造業に特化したデジタルトランスフォーメーション(DX)の実現を目指す請負開発型のコンサルティングサービスです。AI、iPaaS、および先端の技術を駆使して、製造プロセスの効率化、業務効率化、チームワーク強化、コスト削減、品質向上を実現します。このサービスは、製造業の課題を深く理解し、それに対する最適なデジタルソリューションを提供することで、企業が持続的な成長とイノベーションを達成できるようサポートします。
オンライン講座
製造業、主に購買・調達部門にお勤めの方々に向けた情報を配信しております。
新任の方やベテランの方、管理職を対象とした幅広いコンテンツをご用意しております。
お問い合わせ
コストダウンが利益に直結する術だと理解していても、なかなか前に進めることができない状況。そんな時は、newjiのコストダウン自動化機能で大きく利益貢献しよう!
(Β版非公開)