- お役立ち記事
- Efficiency and cost reduction strategies to consider when updating production lines
月間76,176名の
製造業ご担当者様が閲覧しています*
*2025年3月31日現在のGoogle Analyticsのデータより
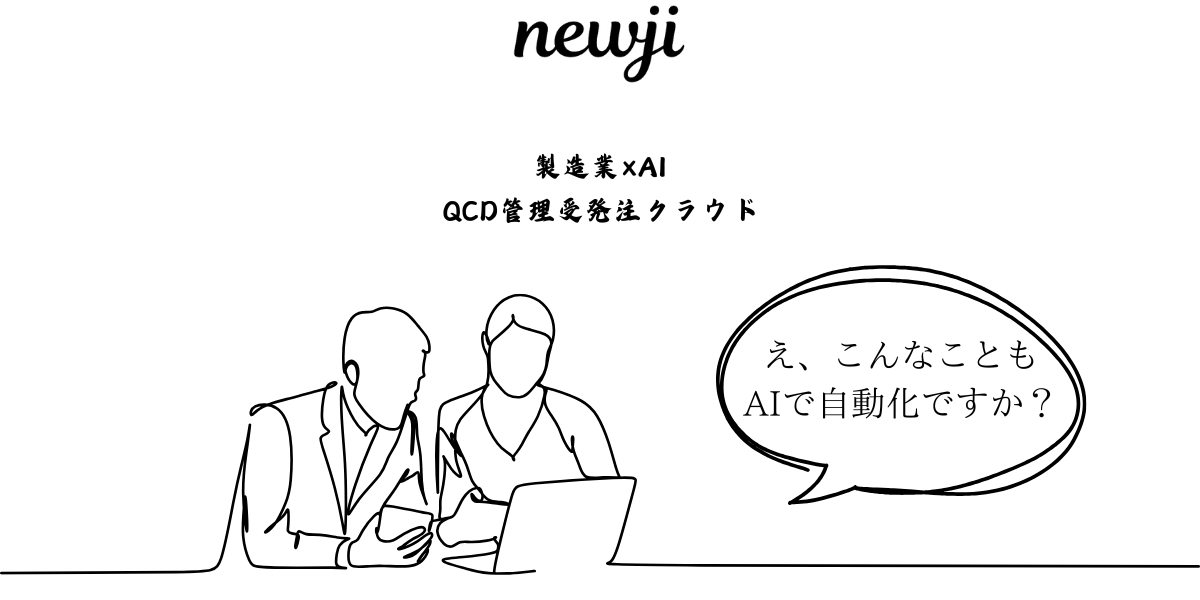
Efficiency and cost reduction strategies to consider when updating production lines
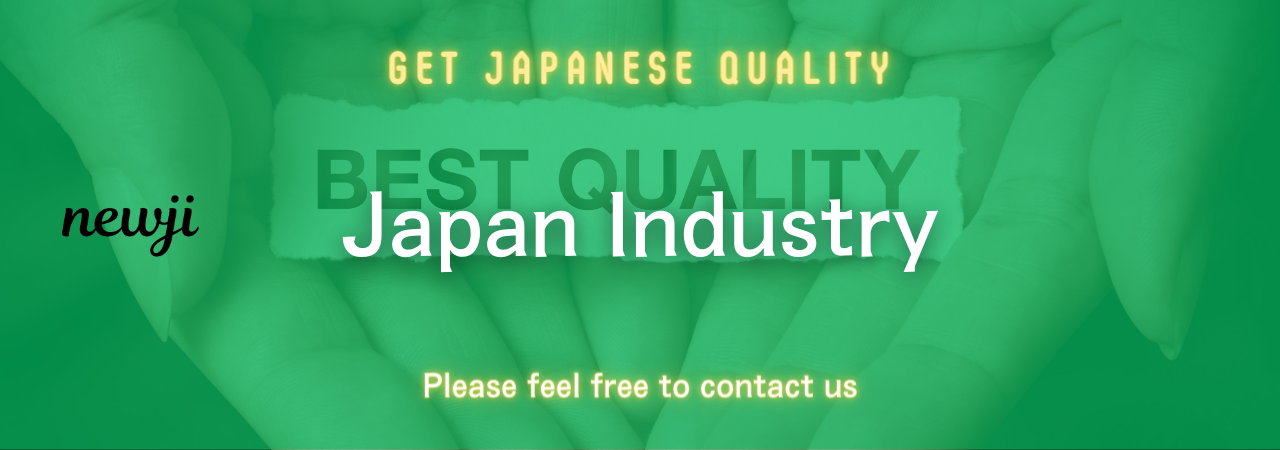
目次
Understanding the Importance of Production Line Updates
Updating production lines is a critical process for manufacturers aiming to maintain competitiveness and efficiency in today’s fast-paced industrial landscape.
Technological advancements and changing market demands continually push companies to improve their production processes.
Failing to update can lead to increased costs, reduced efficiency, and the inability to meet customer expectations.
Updating production lines is not just about replacing old equipment with new machinery.
It’s also about streamlining processes, leveraging new technologies, and enhancing worker productivity.
By doing so, companies can significantly reduce operational costs and improve their overall efficiency.
Identifying Areas for Improvement
Before embarking on any update, it’s essential to assess the current state of your production lines thoroughly.
Identifying bottlenecks, inefficiencies, and areas where improvements are possible can guide the updating process.
A comprehensive audit may involve analyzing production data, reviewing workflow processes, and consulting with plant operators and engineers.
Focus on key performance metrics such as production time, downtime, defect rates, and capacity utilization.
These metrics will provide a clear picture of where improvements are most needed.
By understanding these areas, you can prioritize updates that will offer the most significant impact.
Incorporating Sustainable Practices
In today’s environmentally conscious world, implementing sustainable practices in production updates is not only responsible but also beneficial for cost efficiency.
Energy-efficient machinery, waste reduction, and recycling initiatives can lead to significant savings while reducing environmental impact.
Consider renewable energy options or integrating systems that maximize energy usage with minimal waste.
Sustainable practices can also enhance brand reputation and meet regulatory requirements, further reducing potential costs and liabilities.
Utilizing resources efficiently and minimizing carbon footprints can set your brand apart as a leader in sustainable manufacturing.
Leveraging Automation and Technology
One of the most impactful strategies in modernizing production lines is the integration of automation and advanced technologies.
Automation can handle repetitive tasks with precision, reducing human error and increasing production speed.
Automated systems such as conveyor belts, robotic arms, and automated guided vehicles (AGVs) can significantly enhance workflow efficiency.
Additionally, technologies such as the Industrial Internet of Things (IIoT) enable real-time monitoring and data collection, providing insights into machine performance and facilitating predictive maintenance.
This proactive approach minimizes downtime and prolongs equipment lifespan, further reducing costs.
Investing in Workforce Training
Updating production lines often involves new technologies and processes.
To maximize the benefits of these updates, invest in training your workforce to operate and maintain the new systems effectively.
Skilled workers can identify potential issues quickly, ensuring seamless continuity in production.
Training programs should focus on safety, machine operation, process management, and technical skills pertinent to new equipment.
A well-trained workforce not only enhances efficiency but also fosters a culture of innovation and continuous improvement.
Ongoing Maintenance and Upkeep
Once production lines are updated, the work does not stop there.
Regular maintenance and continual assessment are vital in ensuring these systems remain efficient and effective over time.
Scheduled maintenance checks and prompt repairs are crucial in preventing unexpected breakdowns that can halt production.
Implement a maintenance management system to keep track of service schedules and repair histories.
This system aids in scheduling maintenance activities without disrupting production workflows, hence maximizing uptime and prolonging equipment functionality.
Cost-Benefit Analysis
Conduct a thorough cost-benefit analysis before commencing any production line update.
Consider both the initial investment costs and the long-term benefits such updates will yield.
Factors such as increased productivity, energy savings, improved product quality, and reduced waste contribute to the return on investment.
Engage stakeholders in the planning process to align on expected outcomes and financial implications.
A well-documented analysis aids in decision-making, ensuring that updates provide value and align with business goals.
Collaborating with Experts
Collaboration with industry experts, consultants, and technology providers can enhance the success of production line updates.
These professionals offer insights and recommendations based on industry best practices and technological advancements.
They help in designing efficient workflows and selecting appropriate machinery and systems.
Experts can also assist in project management, ensuring updates are completed within budget and on schedule.
By leveraging the knowledge of experienced professionals, you can make informed decisions that drive sustainable growth and efficiency in your production lines.
Adapting to Market Changes
Finally, always be ready to adapt your production lines to shifting market demands.
Consumer preferences, regulatory changes, and emerging technologies may require further updates.
Staying informed about industry trends allows you to anticipate changes and implement updates proactively.
Adaptability ensures that production processes remain agile and responsive, maintaining a competitive edge in the market.
Regularly review market demands and adjust production capabilities accordingly to stay ahead of the competition.
Updating production lines with efficiency and cost reduction in mind is a multifaceted process that, when executed strategically, can offer substantial benefits.
It requires careful planning, investment in new technologies, workforce development, and regular maintenance to achieve excellence in manufacturing.
By prioritizing these strategies, manufacturers can enhance productivity and continue to thrive in an ever-evolving industrial environment.
資料ダウンロード
QCD管理受発注クラウド「newji」は、受発注部門で必要なQCD管理全てを備えた、現場特化型兼クラウド型の今世紀最高の受発注管理システムとなります。
ユーザー登録
受発注業務の効率化だけでなく、システムを導入することで、コスト削減や製品・資材のステータス可視化のほか、属人化していた受発注情報の共有化による内部不正防止や統制にも役立ちます。
NEWJI DX
製造業に特化したデジタルトランスフォーメーション(DX)の実現を目指す請負開発型のコンサルティングサービスです。AI、iPaaS、および先端の技術を駆使して、製造プロセスの効率化、業務効率化、チームワーク強化、コスト削減、品質向上を実現します。このサービスは、製造業の課題を深く理解し、それに対する最適なデジタルソリューションを提供することで、企業が持続的な成長とイノベーションを達成できるようサポートします。
製造業ニュース解説
製造業、主に購買・調達部門にお勤めの方々に向けた情報を配信しております。
新任の方やベテランの方、管理職を対象とした幅広いコンテンツをご用意しております。
お問い合わせ
コストダウンが利益に直結する術だと理解していても、なかなか前に進めることができない状況。そんな時は、newjiのコストダウン自動化機能で大きく利益貢献しよう!
(β版非公開)