- お役立ち記事
- Efficiency and risk management in manufacturing equipment maintenance
月間77,185名の
製造業ご担当者様が閲覧しています*
*2025年2月28日現在のGoogle Analyticsのデータより
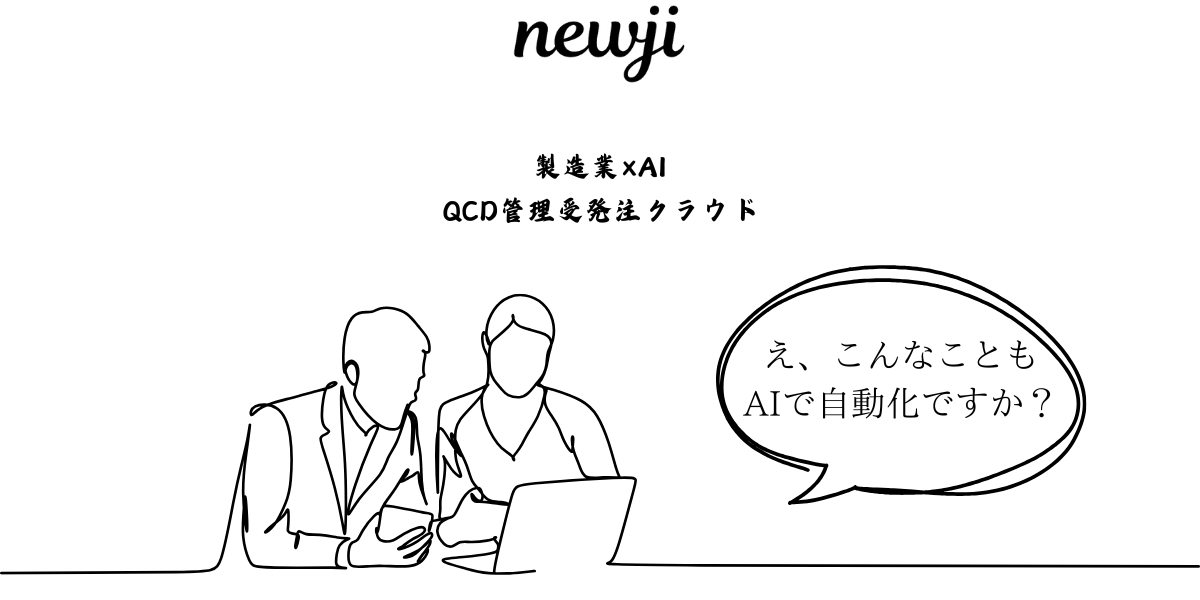
Efficiency and risk management in manufacturing equipment maintenance
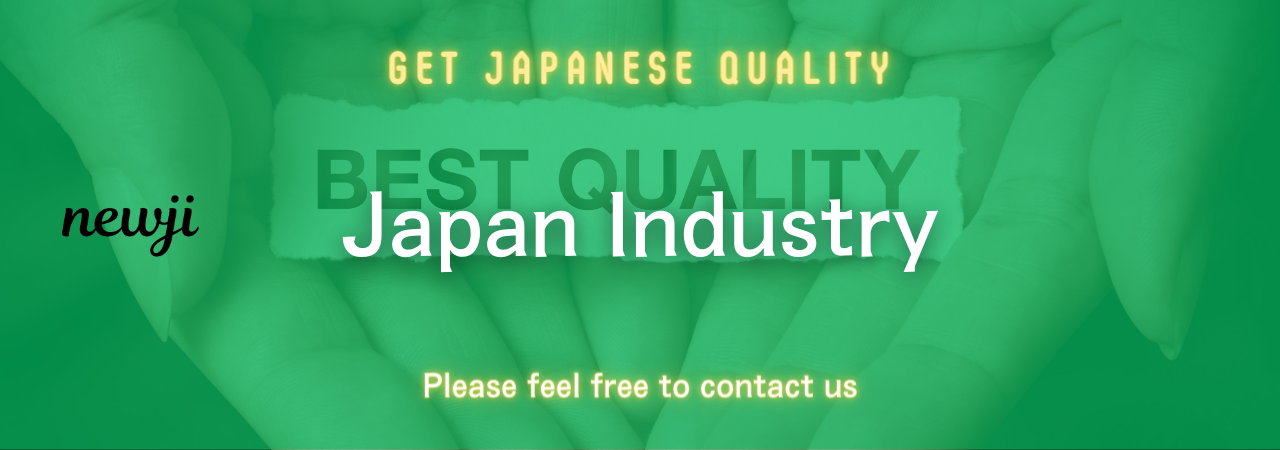
Understanding the Importance of Equipment Maintenance
Manufacturing equipment is the backbone of any production process.
The efficiency and reliability of this equipment are crucial for maintaining smooth operations.
Proper maintenance ensures that machines run at optimal performance, reducing downtime and enhancing productivity.
More importantly, effective equipment maintenance helps in minimizing the risks associated with unforeseen failures.
Understanding the significance of these aspects is the first step towards adopting a structured maintenance approach.
Types of Equipment Maintenance Strategies
Manufacturers can approach equipment maintenance in various ways.
The most common strategies include reactive maintenance, preventive maintenance, and predictive maintenance.
Reactive Maintenance
Often referred to as “breakdown maintenance,” reactive strategies involve repairing equipment after it has failed.
While it might seem cost-effective in the short term, relying solely on breakdown maintenance can lead to significant risks and inefficient operations.
This approach often results in unplanned downtime, affecting production schedules and potentially causing substantial financial losses.
Preventive Maintenance
Preventive maintenance involves regular, scheduled servicing of equipment to reduce the likelihood of failure.
This proactive approach is guided by predetermined schedules based on time or usage cycles.
Implementing preventive maintenance can lead to cost savings over time and reduce the risks associated with unexpected machine breakdowns.
It is particularly beneficial in extending the lifespan of manufacturing equipment.
Predictive Maintenance
Predictive maintenance utilizes advanced technologies to assess the condition of machinery in real time.
By monitoring equipment performance and analyzing data collected through various sensors, predictive maintenance aims to predict when failures might occur.
This approach allows for maintenance to be performed precisely when necessary, minimizing downtime and maximizing equipment efficiency.
Predictive maintenance is often perceived as a more advanced and efficient maintenance strategy, offering significant cost and time savings.
The Role of Technology in Maintenance Efficiency
Technological advancements are transforming the way maintenance is conducted in manufacturing environments.
Tools such as the Internet of Things (IoT), artificial intelligence (AI), and machine learning are being integrated into maintenance strategies.
Internet of Things (IoT)
The IoT plays a crucial role in connected manufacturing environments.
Through IoT-enabled sensors, detailed information about equipment status, performance, and anomalies can be gathered in real-time.
This data is invaluable for making informed maintenance decisions and enhancing equipment reliability.
Artificial Intelligence and Machine Learning
AI and machine learning algorithms analyze vast amounts of data collected from IoT devices.
These technologies help predict equipment failures before they occur, allowing maintenance teams to address potential issues proactively.
Machine learning models can continuously learn from historical data, improving the accuracy of predictions and ensuring that maintenance activities are optimized.
Risk Management in Equipment Maintenance
Risk management in manufacturing equipment maintenance involves identifying, assessing, and prioritizing potential risks.
Effective risk management strategies can prevent accidents, equipment downtime, and financial losses.
Identifying Risks
The first step in risk management is identifying potential risks associated with equipment maintenance.
This includes mechanical failures, technology malfunctions, human errors, and environmental factors.
Regular risk assessments and evaluations of equipment conditions can highlight vulnerabilities that need to be addressed.
Assessing and Prioritizing Risks
Once risks are identified, they should be assessed based on their likelihood and potential impact.
More critical risks should be prioritized, ensuring that resources are allocated efficiently.
Tools such as Failure Mode and Effects Analysis (FMEA) can be used to systematically assess risks and prioritize maintenance tasks accordingly.
Implementing Risk Mitigation Strategies
Based on the prioritized risks, appropriate strategies should be implemented to mitigate them.
These strategies might include refining maintenance schedules, investing in advanced monitoring technologies, or providing enhanced training for maintenance personnel.
Engaging in continuous improvement practices is vital to ensure that risk mitigation strategies remain effective.
Conclusion: The Balance Between Efficiency and Risk
Efficiency and risk management in manufacturing equipment maintenance are intertwined components.
Optimizing maintenance strategies not only enhances operational efficiency but also helps mitigate potential risks.
Manufacturers must adopt a balanced approach that integrates modern technologies, such as IoT and AI, with meticulous risk management practices.
By doing so, they can ensure that their equipment operates smoothly, safely, and cost-effectively.
Implementing these strategies will not only safeguard equipment but also contribute to a more resilient, productive manufacturing environment.
資料ダウンロード
QCD管理受発注クラウド「newji」は、受発注部門で必要なQCD管理全てを備えた、現場特化型兼クラウド型の今世紀最高の受発注管理システムとなります。
ユーザー登録
受発注業務の効率化だけでなく、システムを導入することで、コスト削減や製品・資材のステータス可視化のほか、属人化していた受発注情報の共有化による内部不正防止や統制にも役立ちます。
NEWJI DX
製造業に特化したデジタルトランスフォーメーション(DX)の実現を目指す請負開発型のコンサルティングサービスです。AI、iPaaS、および先端の技術を駆使して、製造プロセスの効率化、業務効率化、チームワーク強化、コスト削減、品質向上を実現します。このサービスは、製造業の課題を深く理解し、それに対する最適なデジタルソリューションを提供することで、企業が持続的な成長とイノベーションを達成できるようサポートします。
製造業ニュース解説
製造業、主に購買・調達部門にお勤めの方々に向けた情報を配信しております。
新任の方やベテランの方、管理職を対象とした幅広いコンテンツをご用意しております。
お問い合わせ
コストダウンが利益に直結する術だと理解していても、なかなか前に進めることができない状況。そんな時は、newjiのコストダウン自動化機能で大きく利益貢献しよう!
(β版非公開)