- お役立ち記事
- Efficiency Methods in Production Management Inspired by the Toyota Production System
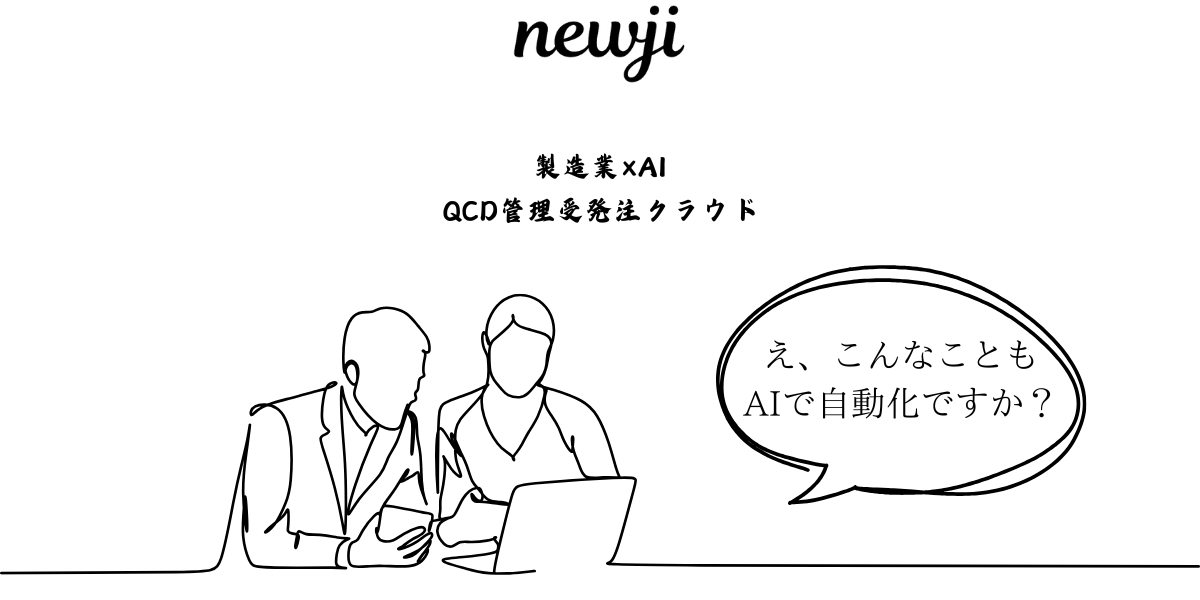
Efficiency Methods in Production Management Inspired by the Toyota Production System
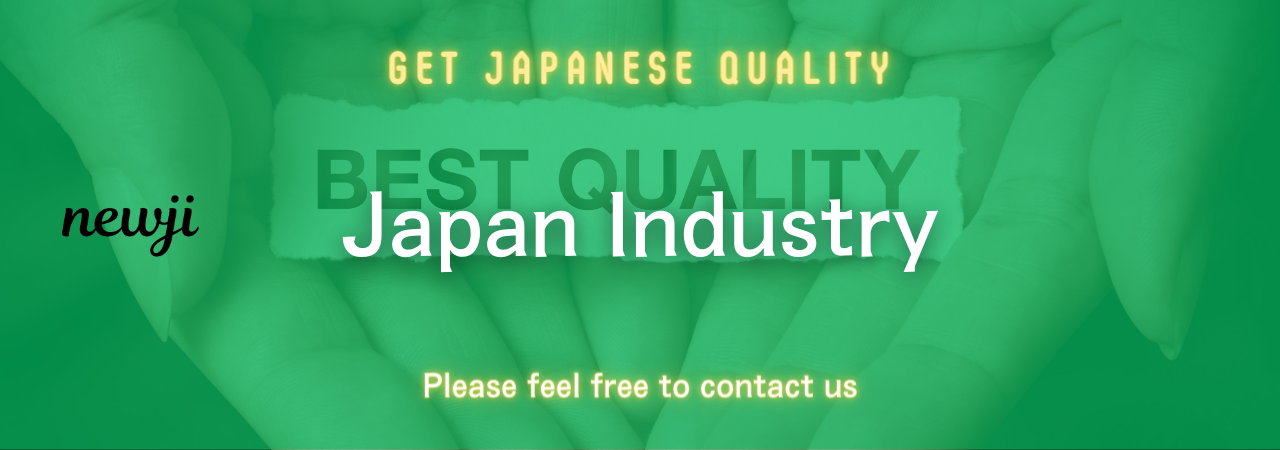
目次
Understanding the Basics of Production Management
Production management is the art of optimizing the manufacturing process to improve efficiency and effectiveness.
It involves planning, organizing, directing, and controlling all the production processes to ensure they meet the required standard of quality and quantity.
Understanding these basics sets the stage for adopting advanced efficiency methods inspired by successful models like the Toyota Production System (TPS).
The Toyota Production System: An Overview
The Toyota Production System is a manufacturing philosophy developed by Toyota that focuses on lean production and waste reduction.
This system has been praised and emulated by industries world over for its unparalleled success in improving production efficiency.
Key elements of TPS include the Just-In-Time (JIT) production model and Jidoka or automation with a human touch.
These elements work together to ensure timely production and the highest quality output.
Just-In-Time Production
The Just-In-Time (JIT) approach revolves around producing only what is needed, when it is needed, and in the amount needed.
This reduces waste and lowers inventory costs by preventing overproduction and minimizing excess inventory.
Implementing the JIT concept in production management requires detailed planning and strong supplier relationships to ensure the timely delivery of materials.
This approach not only reduces waste but also increases flexibility to respond to market demands.
Jidoka: Automation with a Human Touch
Jidoka, another pillar of the TPS, emphasizes the importance of quality control and automation.
It’s about designing machines that include features for automatic error detection.
When a machine detects an error, it stops production right away.
This allows human workers to address and resolve issues without compromising quality or losing time.
Incorporating Jidoka into production management ensures that quality is not sacrificed for quantity, leading to a more reliable production process.
Lean Manufacturing Principles
Lean manufacturing principles are closely tied to the Toyota Production System.
The goal is to maximize customer value while minimizing waste.
Several principles guide lean manufacturing, each of which can be adapted within production management to improve efficiency.
Value Stream Mapping
Value stream mapping is an essential tool for identifying every step in the production process and determining where value is added.
This helps to find bottlenecks, reduce waste, and improve the overall production flow.
By visualizing the entire process, producers can streamline work, ensuring resources are efficiently utilized and activities align with customer requirements.
Continuous Improvement (Kaizen)
The philosophy of Kaizen promotes a culture of continuous improvement where workers at all levels of an organization contribute to incremental changes.
This process involves continually seeking out ways to improve efficiency and reduce waste.
Encouraging feedback and ideas from all participants in the production process is crucial.
Incremental changes can make significant improvements over time, leading to enhanced productivity and morale.
Implementing Efficiency Methods in Your Production Management
Adopting efficiency methods from the Toyota Production System requires commitment and adaptation across all levels of your organization.
Consider starting small and gradually integrating TPS elements into your current processes.
Engage Employees
Involve everyone in the organization, from management to production line workers in the transition to a more efficient system.
Provide training and encourage employees to contribute ideas for potential improvements.
Employee engagement is vital for the successful adoption of new methodologies.
When people understand the benefits, they are more likely to embrace changes and help achieve efficiency goals.
Measure and Analyze
Regularly measure and analyze your production processes to identify areas of inefficiency.
Use data and insights from these analyses to guide decision-making and prioritize improvements.
Tools like performance metrics and key performance indicators (KPIs) can provide valuable insights and benchmarks.
These measurements inform management about what’s working and where there’s room for improvement.
Overcoming Challenges
Implementing new production methods can be challenging.
Resistance to change is natural but can be overcome with clear communication and guidance.
Addressing Resistance to Change
Explain the benefits of the new efficiency methods to all stakeholders.
Provide evidence of successes from the Toyota Production System to illustrate potential advantages.
Involve individuals in the process and offer support through training and education.
With the right preparation, teams will more likely welcome the change and actively participate in implementation.
Maintaining Consistency
Once new process improvements are in place, ensure they are consistently applied.
Regular reviews and updates of procedures help maintain alignment with efficiency objectives.
Recognize and reward employees who contribute to sustaining efficient processes.
Reinforcement through positive acknowledgment encourages continued adherence to new practices.
Conclusion
Adopting efficiency methods inspired by the Toyota Production System can significantly enhance productivity and reduce waste.
By focusing on the principles of lean manufacturing, such as Just-In-Time production and quality control through Jidoka, manufacturers can streamline operations.
Engaging employees, measuring performance, and continuously improving processes are integral to successfully implementing these strategies.
With commitment and strategic planning, organizations can transform their production management, leading to higher quality products and more satisfied customers.
資料ダウンロード
QCD調達購買管理クラウド「newji」は、調達購買部門で必要なQCD管理全てを備えた、現場特化型兼クラウド型の今世紀最高の購買管理システムとなります。
ユーザー登録
調達購買業務の効率化だけでなく、システムを導入することで、コスト削減や製品・資材のステータス可視化のほか、属人化していた購買情報の共有化による内部不正防止や統制にも役立ちます。
NEWJI DX
製造業に特化したデジタルトランスフォーメーション(DX)の実現を目指す請負開発型のコンサルティングサービスです。AI、iPaaS、および先端の技術を駆使して、製造プロセスの効率化、業務効率化、チームワーク強化、コスト削減、品質向上を実現します。このサービスは、製造業の課題を深く理解し、それに対する最適なデジタルソリューションを提供することで、企業が持続的な成長とイノベーションを達成できるようサポートします。
オンライン講座
製造業、主に購買・調達部門にお勤めの方々に向けた情報を配信しております。
新任の方やベテランの方、管理職を対象とした幅広いコンテンツをご用意しております。
お問い合わせ
コストダウンが利益に直結する術だと理解していても、なかなか前に進めることができない状況。そんな時は、newjiのコストダウン自動化機能で大きく利益貢献しよう!
(Β版非公開)