- お役立ち記事
- Efficient accelerated reliability testing, various usage methods for design and life prediction, and examples of key points in practice
月間77,185名の
製造業ご担当者様が閲覧しています*
*2025年2月28日現在のGoogle Analyticsのデータより
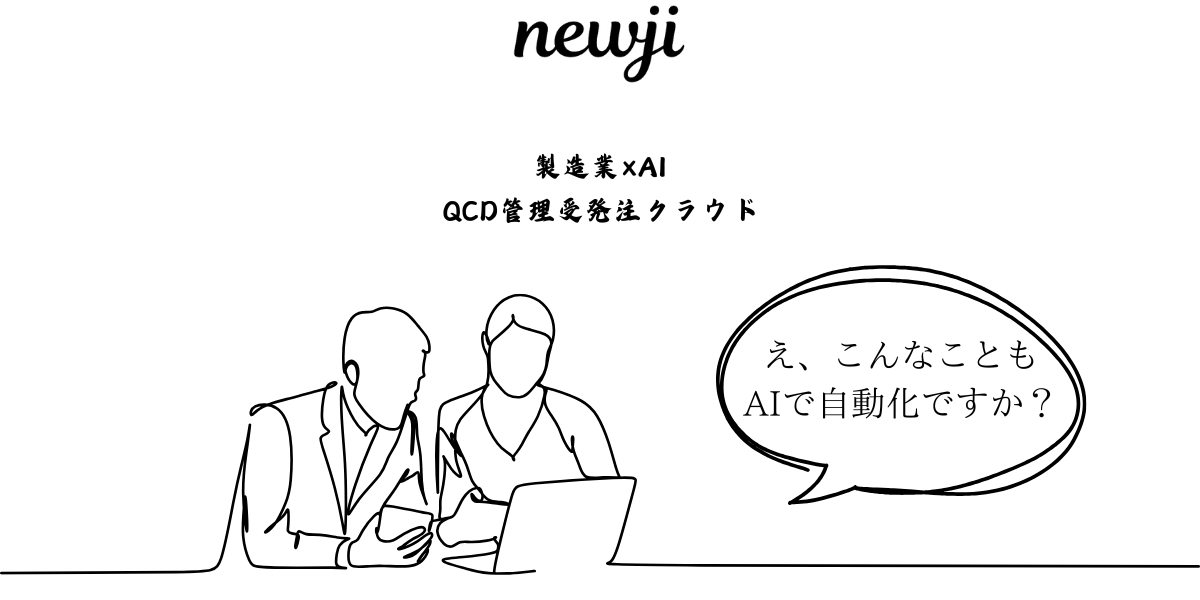
Efficient accelerated reliability testing, various usage methods for design and life prediction, and examples of key points in practice
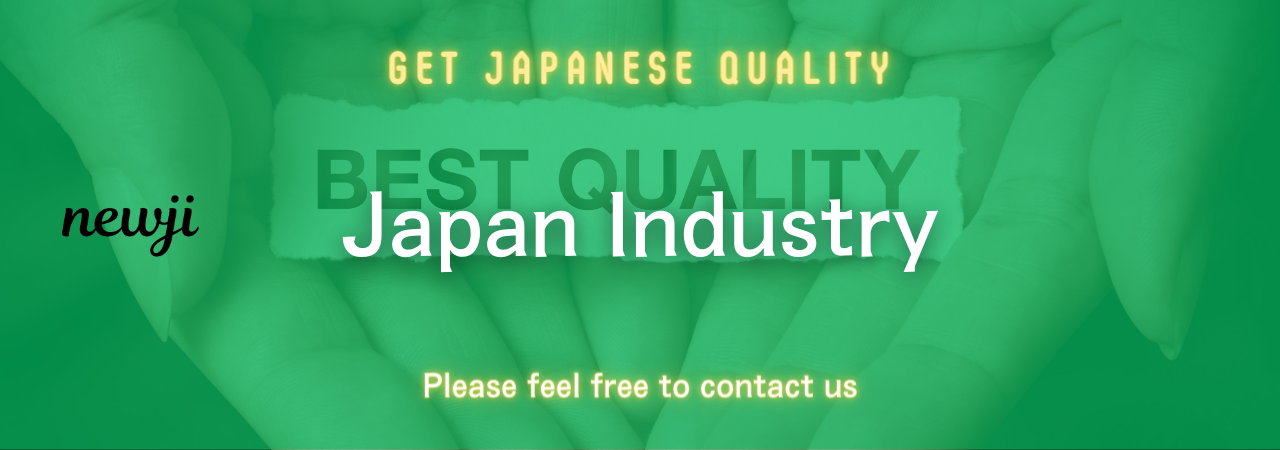
Accelerated reliability testing (ART) has become a crucial component in modern product development and design processes.
This testing method is designed to estimate a product’s lifetime and identify potential design flaws quickly and efficiently.
By doing so, manufacturers can predict how a product might fail, leading to improved designs and longer-lasting products.
ART helps in reducing time-to-market while ensuring that quality and reliability standards are met.
目次
Understanding Accelerated Reliability Testing
Accelerated Reliability Testing involves subjecting a product to stress conditions that are more severe than normal usage.
These conditions can include higher temperatures, increased humidity, or other environmental factors.
The idea is to simulate several years of usage within a much shorter time frame.
This testing allows engineers to observe how and when failures occur, which is invaluable data for improving product design and reliability.
Different types of ART exist, including Highly Accelerated Life Testing (HALT), Highly Accelerated Stress Screening (HASS), and Rapid Thermal Cycling.
Each type serves a specific purpose and is chosen based on the product, its intended use, and the specific failure modes that are of concern.
Benefits of ART
One of the primary benefits of ART is the ability to quickly identify potential weaknesses in a product’s design.
By accelerating the testing process, manufacturers can discover which components are most likely to fail and take preventive measures.
This process not only saves time but also reduces costs associated with recalls, repairs, and warranty claims.
Another advantage is that ART helps in predicting product lifespan.
By understanding how long a product will last under accelerated conditions, manufacturers can provide more accurate warranty periods.
This predictive capability is especially important in industries where reliability is critical, such as aerospace, automotive, and consumer electronics.
Methods of Accelerated Reliability Testing
There are several methods used in ART, each with its own set of advantages.
Below, we explore some of the most popular methods.
Highly Accelerated Life Testing (HALT)
HALT is a testing methodology used early in the product development phase.
It involves exposing products to extreme conditions beyond the expected service life to discover potential weaknesses in design.
The aim is to push the product to its limits to ensure reliability under normal operating conditions.
HALT can reveal weaknesses that might not be apparent under regular testing conditions.
Highly Accelerated Stress Screening (HASS)
HASS is used during the production phase to ensure that manufactured units meet the reliability and quality standards established during HALT.
It involves applying variable stress levels to random samples from the production line to detect any defects in workmanship or materials.
HASS is critical for ensuring that every unit leaving a production facility is built to the high standards expected by consumers.
Rapid Thermal Cycling
This method involves rapidly cycling the temperature of a product to ensure it can withstand the stresses of different thermal environments.
It is commonly used for electronics and materials testing, where temperature changes can significantly impact reliability and performance.
Rapid Thermal Cycling can reveal issues like thermal cracking or other component failures that might occur with temperature fluctuations.
Application of ART in Design and Life Prediction
Implementing ART in the design phase allows engineers to identify and rectify potential failure points before a product reaches the market.
It enables a more robust product design, reducing the need for costly redesigns after market release.
In life prediction, ART provides valuable data that helps in estimating how long a product will function reliably under expected usage conditions.
This estimation is crucial for planning maintenance schedules, warranty terms, and product lifecycle management.
Design Improvements
By understanding the failure modes exposed during ART, designers can make informed decisions on component choice, material selection, and assembly methods.
This proactive approach results in more reliable products, enhancing consumer satisfaction and brand reputation.
Maintenance and Warranty Planning
Data from ART can be used to anticipate when and where a product may need maintenance.
This predictive insight allows for better planning of warranty periods and after-sale service strategies, supporting both clients and service providers in managing resources effectively.
Practical Examples of ART
Many industries benefit from implementing ART in their product development cycles.
Let’s look at a few practical examples to understand its impact better.
Automotive Industry
In the automotive industry, ART is used to test new car models under extreme conditions.
This includes temperature variations, vibration, and impact resistance.
By doing this, manufacturers can ensure that vehicles remain safe and operational regardless of external environmental conditions.
Consumer Electronics
For consumer electronics, ART is vital for optimizing battery life and durability.
Smartphones, for example, undergo ART to ensure they can withstand daily wear and tear over years of usage.
This testing helps manufacturers guarantee that their devices meet consumer expectations for durability and longevity.
Aerospace Sector
In the aerospace industry, reliability is non-negotiable.
ART ensures that each component of an aircraft can withstand the rigors of extended usage at high altitudes and speeds.
This includes testing the durability of engines, electronic systems, and structural components, making ART essential for flight safety and reliability.
Key Points for Successful ART Implementation
When implementing ART, being mindful of certain key points can enhance effectiveness and outcomes.
First, clearly define the accelerated conditions.
This includes determining what levels of stress (temperature, humidity, vibration) will accurately simulate real-world usage.
The conditions should be extreme enough to induce failure modes without causing unrealistic damage.
Next, ensure continuous monitoring during tests.
Data collection should be comprehensive to capture all aspects of product performance and failure modes.
This data will be crucial for analysis and improvements.
Finally, integrate findings from ART into the design and production processes.
Use the insights gained to make informed decisions that enhance product quality, reliability, and consumer satisfaction.
Incorporating ART into the workflow ensures a streamlined process from initial development to final production, helping companies maintain high standards and a competitive edge in the market.
資料ダウンロード
QCD管理受発注クラウド「newji」は、受発注部門で必要なQCD管理全てを備えた、現場特化型兼クラウド型の今世紀最高の受発注管理システムとなります。
ユーザー登録
受発注業務の効率化だけでなく、システムを導入することで、コスト削減や製品・資材のステータス可視化のほか、属人化していた受発注情報の共有化による内部不正防止や統制にも役立ちます。
NEWJI DX
製造業に特化したデジタルトランスフォーメーション(DX)の実現を目指す請負開発型のコンサルティングサービスです。AI、iPaaS、および先端の技術を駆使して、製造プロセスの効率化、業務効率化、チームワーク強化、コスト削減、品質向上を実現します。このサービスは、製造業の課題を深く理解し、それに対する最適なデジタルソリューションを提供することで、企業が持続的な成長とイノベーションを達成できるようサポートします。
製造業ニュース解説
製造業、主に購買・調達部門にお勤めの方々に向けた情報を配信しております。
新任の方やベテランの方、管理職を対象とした幅広いコンテンツをご用意しております。
お問い合わせ
コストダウンが利益に直結する術だと理解していても、なかなか前に進めることができない状況。そんな時は、newjiのコストダウン自動化機能で大きく利益貢献しよう!
(β版非公開)