- お役立ち記事
- Efficient Equipment Selection Based on Production Capacity Analysis
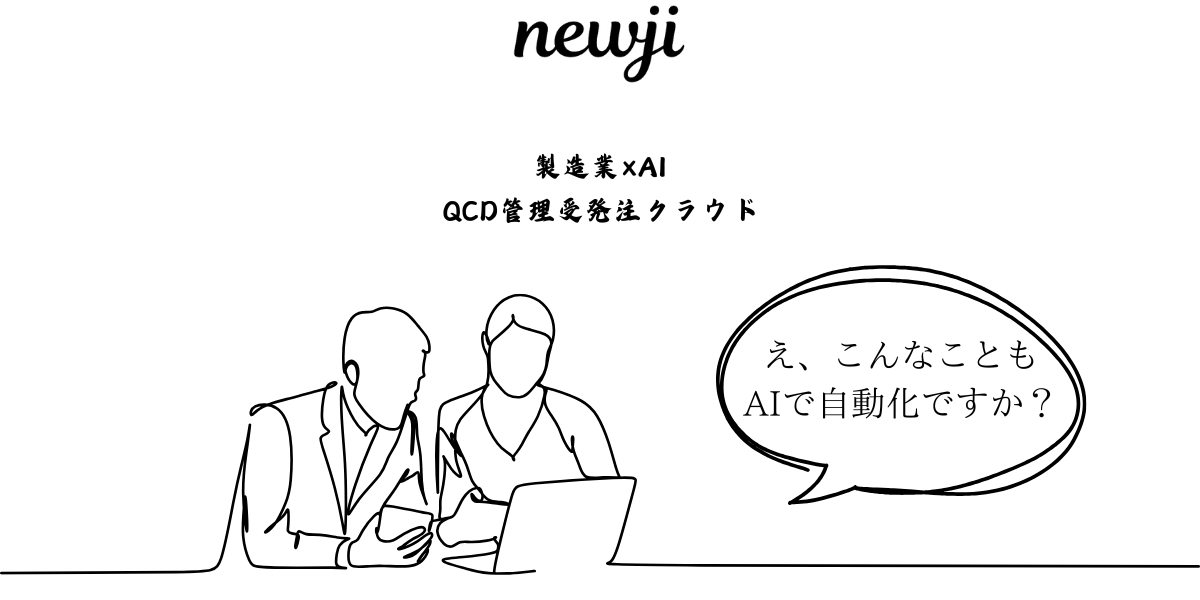
Efficient Equipment Selection Based on Production Capacity Analysis
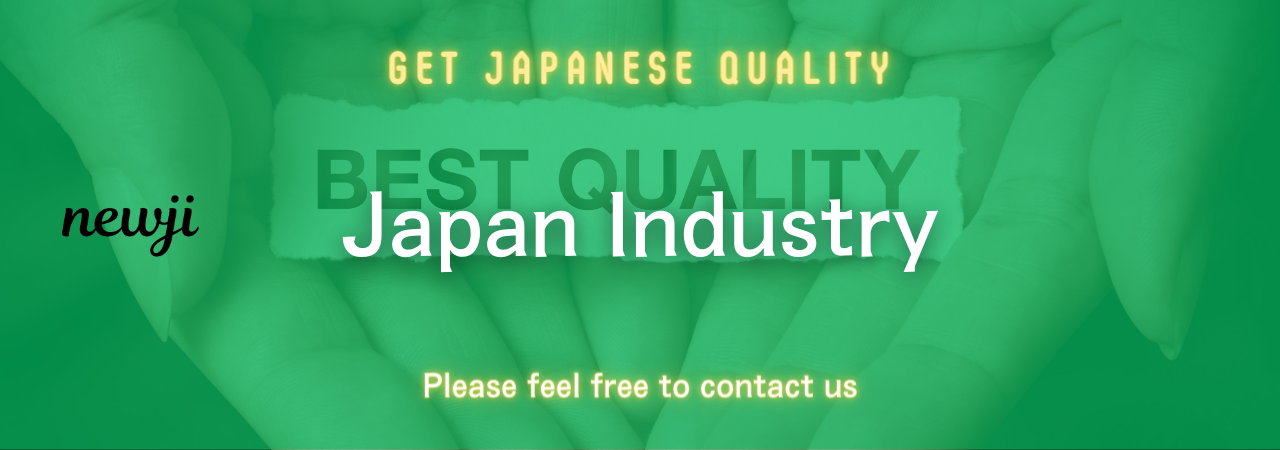
When it comes to manufacturing or any industrial activity, selecting the right equipment is crucial for achieving high productivity and efficiency.
Making informed decisions about equipment based on thorough production capacity analysis can save time, reduce costs, and improve overall output quality.
This article will delve into the importance of production capacity analysis, the factors to consider, and practical steps for selecting the most appropriate equipment for your needs.
目次
Understanding Production Capacity Analysis
Production capacity analysis helps businesses determine the maximum output their facilities can produce under ideal conditions.
This analysis involves evaluating the capabilities of current machinery, workforce, operational procedures, and other resources that contribute to production.
Why Conduct a Production Capacity Analysis?
Conducting a production capacity analysis offers several benefits.
Firstly, it provides clear insights into existing capabilities, helping to identify bottlenecks or inefficiencies that might limit output.
Secondly, understanding production capacity allows for better planning and resource allocation.
Lastly, this analysis can guide the selection of new equipment that aligns with the production goals and growth strategies.
Key Factors to Consider
Selecting equipment based on production capacity analysis involves considering multiple factors:
Current and Projected Demand
Before selecting any equipment, it’s essential to understand the current demand for your products and project future growth.
This helps ensure that the equipment chosen can handle present needs and scale up as demand increases in the future.
Machine Compatibility
It’s imperative to select machines that are compatible with existing systems in the production line.
Incompatibility can lead to inefficiencies and additional costs, negating the benefits of new equipment.
Efficiency and Downtime
Evaluate the efficiency rates of potential equipment.
Highly efficient machines contribute to greater output, but it’s also vital to consider the downtime required for maintenance or repairs.
Low downtime ensures that production remains consistent over time.
Energy Consumption
With a growing focus on sustainability, energy consumption is a significant factor in equipment selection.
Opt for machinery that consumes less power but delivers high performance.
This not only reduces operational costs but also minimizes the environmental impact.
Cost Considerations
While advanced machinery may offer numerous benefits, budget constraints cannot be ignored.
Assess the cost of acquiring, maintaining, and operating the equipment.
Sometimes, a higher upfront investment can lead to long-term savings due to reduced operational costs and increased efficiency.
Steps for Efficient Equipment Selection
Once you’ve thoroughly analyzed your production capacity and considered all essential factors, follow these steps to choose the most efficient equipment:
Conduct a SWOT Analysis
A SWOT (Strengths, Weaknesses, Opportunities, Threats) analysis can provide valuable insights into the needs and capabilities of your production facility.
Identify what your current equipment does well (strengths), where it falls short (weaknesses), opportunities for improvement or growth, and potential threats from competitors or market changes.
Set Clear Requirements
Define the specific requirements of the equipment you need.
Take into account production speed, quality, energy consumption, and compatibility with existing systems.
Clear requirements ensure that you search for equipment that fits your precise needs.
Consult with Experts
Engaging with industry experts, engineers, or consultants can provide a fresh perspective.
They might offer insights or identify potential pitfalls that you haven’t considered.
Their expertise can assist in making a more informed decision.
Research and Compare Options
Manufacturers and suppliers often offer various models and types of machinery.
Conduct thorough research and compare the features, benefits, and costs of different options.
Reading reviews, case studies, and user testimonials can also provide real-world efficacy data.
Test Before Buying
If possible, test the equipment before making a final purchase.
Trial runs can reveal how well the machinery integrates with your production line and whether it meets all your requirements.
This hands-on approach can prevent costly mistakes.
Case Study: A Real-Life Example
To illustrate the importance of efficient equipment selection, consider the following example from a textiles manufacturing company:
Initial Production Challenge
The company faced increasing demand for its textiles but was struggling with outdated machinery that hindered production capacity.
After conducting a comprehensive production capacity analysis, several bottlenecks were identified.
Analysis and Equipment Selection
The company performed a SWOT analysis, set clear requirements, and consulted with industry experts.
Based on their research and trial runs, they selected modern, energy-efficient weaving machines compatible with their existing setup.
Outcome
Post-implementation, the company saw a 30% increase in production capacity and a 20% reduction in energy costs.
The new equipment also required less downtime, ensuring more consistent output.
Conclusion
Selecting the right equipment based on thorough production capacity analysis is vital for achieving efficiency and meeting production goals.
By understanding your current and future needs, evaluating key factors, and following a systematic selection process, you can make informed decisions that significantly boost your operational productivity.
Engage with experts, conduct detailed research, and don’t hesitate to test equipment before committing.
It’s an investment in the future of your production capabilities that pays dividends in the long run.
資料ダウンロード
QCD調達購買管理クラウド「newji」は、調達購買部門で必要なQCD管理全てを備えた、現場特化型兼クラウド型の今世紀最高の購買管理システムとなります。
ユーザー登録
調達購買業務の効率化だけでなく、システムを導入することで、コスト削減や製品・資材のステータス可視化のほか、属人化していた購買情報の共有化による内部不正防止や統制にも役立ちます。
NEWJI DX
製造業に特化したデジタルトランスフォーメーション(DX)の実現を目指す請負開発型のコンサルティングサービスです。AI、iPaaS、および先端の技術を駆使して、製造プロセスの効率化、業務効率化、チームワーク強化、コスト削減、品質向上を実現します。このサービスは、製造業の課題を深く理解し、それに対する最適なデジタルソリューションを提供することで、企業が持続的な成長とイノベーションを達成できるようサポートします。
オンライン講座
製造業、主に購買・調達部門にお勤めの方々に向けた情報を配信しております。
新任の方やベテランの方、管理職を対象とした幅広いコンテンツをご用意しております。
お問い合わせ
コストダウンが利益に直結する術だと理解していても、なかなか前に進めることができない状況。そんな時は、newjiのコストダウン自動化機能で大きく利益貢献しよう!
(Β版非公開)