- お役立ち記事
- Efficient handling methods from design to manufacturing of EV chargers and related equipment
月間76,176名の
製造業ご担当者様が閲覧しています*
*2025年3月31日現在のGoogle Analyticsのデータより
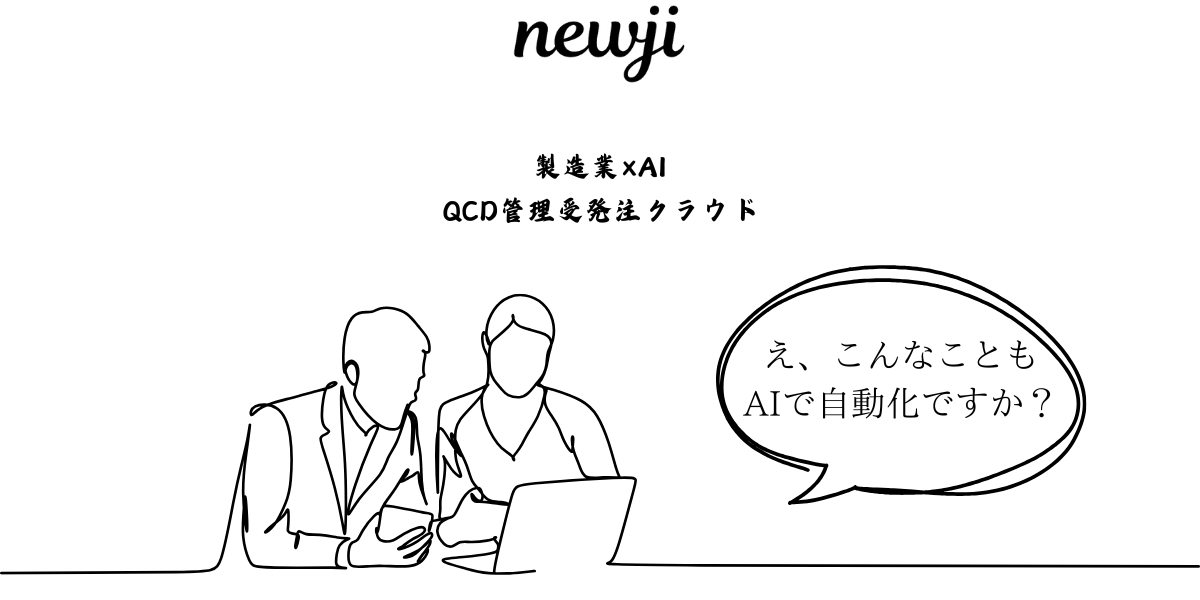
Efficient handling methods from design to manufacturing of EV chargers and related equipment
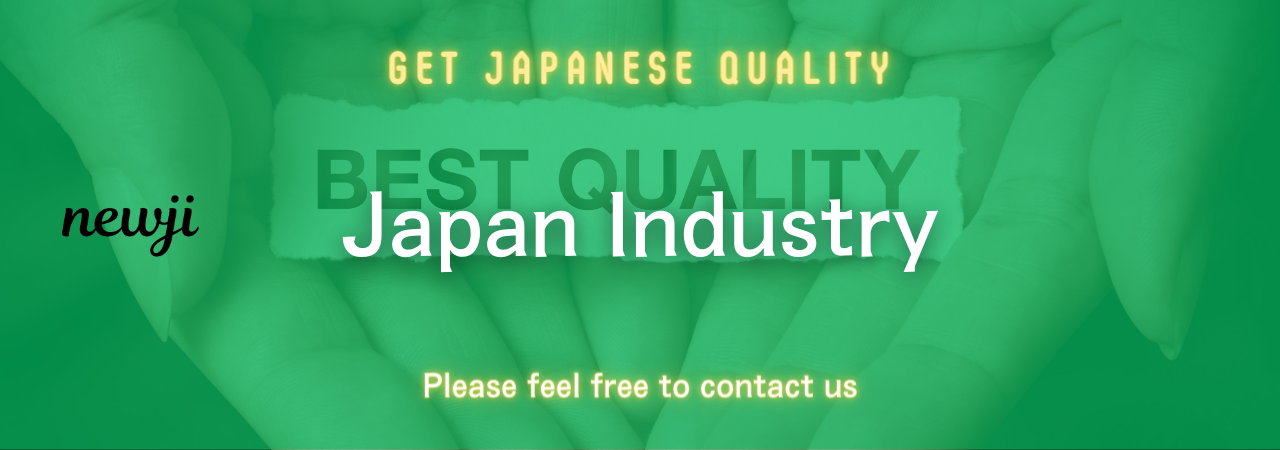
目次
Understanding the Basics of EV Chargers and Related Equipment
Electric vehicles (EVs) are growing in popularity due to their environmentally friendly nature and efficiency.
A key component of electric vehicles is the EV charger.
These chargers and their related equipment are crucial for powering electric cars and ensuring they can travel long distances without frequent stops.
Understanding the design and manufacturing of these chargers is essential for anyone involved in the EV industry.
Manufacturers must consider various factors like efficiency, safety, and cost when designing EV chargers.
Each of these elements plays a significant role in the final design and functionality of the equipment.
The Importance of Efficient Designs
Efficiency in design is crucial when it comes to EV chargers.
An efficient design reduces energy waste, ensuring that the maximum energy from the power source is transferred to the vehicle.
Manufacturers are constantly looking for innovative ways to improve energy transfer, reduce charging times, and minimize heat production.
This involves selecting the right components and materials that offer durability and efficient energy conductance.
Establishing a balance between cost and performance usually leads to a more efficient design.
Material and Component Selection
The selection of materials and components is another critical factor in designing EV chargers.
High-quality materials ensure longevity and reliable performance of the charger.
For instance, choosing copper wiring over aluminum can lead to better conductivity and less energy loss, although it might increase the cost.
Components like power inverters, diodes, and capacitors must be chosen for their efficiency and reliability.
These components influence the overall performance of the charger and determine how well it functions under various environmental conditions.
Proper selection and placement of these components can lead to significant improvements in the charger’s efficiency.
Streamlining the Manufacturing Process
Manufacturing EV chargers involves several steps, from assembling components to rigorous testing.
Streamlining this process is vital for reducing production costs and time, ultimately leading to more affordable chargers for consumers.
Automated Manufacturing Techniques
Automation in manufacturing has become a crucial element in producing EV chargers efficiently.
Using machines for assembly and quality checks ensures consistency and reduces the possibility of human error.
This technique can drastically speed up the production process, allowing manufacturers to meet growing demands promptly.
The implementation of robotics can also aid in assembling complex components of the charger, leading to more precise and reliable products.
Quality Control and Testing
Quality control is another significant aspect of the manufacturing process.
Each charger must undergo rigorous testing to ensure it meets all safety and performance standards.
Testing processes usually involve checking electrical performance, hardware integrity, and safety features.
These tests ensure that the charger can withstand different environmental conditions and provide reliable service throughout its lifespan.
Implementing a thorough quality control system can help detect any manufacturing defects and rectify them before the charger reaches the market.
Cost-Effective Approaches in Design and Manufacturing
Making EV chargers cost-effective without compromising quality is a crucial challenge for manufacturers.
Cost considerations influence every aspect of the design and manufacturing process, from material selection to assembly techniques.
Developing Affordable Solutions
To keep costs low, manufacturers often seek affordable alternatives in terms of materials and components.
This involves extensive research and testing to ensure these alternatives do not compromise the overall performance and safety of the charger.
Using advanced technologies like machine learning can help in analyzing performance data and finding cost-effective improvements in design.
Furthermore, economies of scale can significantly reduce costs as production volumes increase.
Manufacturers can take advantage of bulk purchasing and standardized parts to lower overall expenses.
Collaborative Efforts and Partnerships
Partnerships and collaborations with other companies can also lead to cost-effective manufacturing processes.
By working together, companies can share resources, technologies, and expertise.
This collaborative approach often leads to the development of innovative solutions that are both effective and economical.
Collaborating with suppliers can also lead to better pricing and availability of high-quality materials, further reducing manufacturing costs.
The Role of Innovation in EV Chargers and Equipment
Innovation plays a vital role in advancing the capabilities of EV chargers and related equipment.
Through innovative designs and technologies, manufacturers can develop chargers that offer better performance, efficiency, and convenience.
The Future of EV Charging
Looking ahead, the future of EV charging seems promising with continuous advancements in technology.
Wireless charging is one of the emerging trends that promise to revolutionize the way electric vehicles are charged.
This technology offers convenience and eliminates the need for physical connections between the charger and the vehicle.
Fast-charging technologies are also on the rise, providing solutions that significantly reduce charging times.
This progress will address one of the primary concerns of EV users—charging time—making electric vehicles even more appealing to a broader audience.
Encouraging Sustainable Practices
Sustainability is a growing concern in all manufacturing sectors, including that of EV chargers.
Innovative practices that focus on reducing environmental impact are becoming a key component of future designs.
Utilizing renewable energy sources for charger manufacturing and operation is one way to enhance sustainability.
This practice reduces the carbon footprint associated with the production and use of EV chargers.
Moreover, designing chargers with recyclability in mind ensures that end-of-life products do not contribute to environmental pollution.
Manufacturers are encouraged to design components that are easy to dismantle and recycle, promoting a circular economy in the EV industry.
In summary, the efficient handling methods in the design and manufacturing of EV chargers and related equipment play an essential role in the growing electric vehicle industry.
By focusing on efficiency, cost-effectiveness, and innovation, manufacturers can develop chargers that meet the demands of a rapidly changing market while considering sustainability and the future.
資料ダウンロード
QCD管理受発注クラウド「newji」は、受発注部門で必要なQCD管理全てを備えた、現場特化型兼クラウド型の今世紀最高の受発注管理システムとなります。
ユーザー登録
受発注業務の効率化だけでなく、システムを導入することで、コスト削減や製品・資材のステータス可視化のほか、属人化していた受発注情報の共有化による内部不正防止や統制にも役立ちます。
NEWJI DX
製造業に特化したデジタルトランスフォーメーション(DX)の実現を目指す請負開発型のコンサルティングサービスです。AI、iPaaS、および先端の技術を駆使して、製造プロセスの効率化、業務効率化、チームワーク強化、コスト削減、品質向上を実現します。このサービスは、製造業の課題を深く理解し、それに対する最適なデジタルソリューションを提供することで、企業が持続的な成長とイノベーションを達成できるようサポートします。
製造業ニュース解説
製造業、主に購買・調達部門にお勤めの方々に向けた情報を配信しております。
新任の方やベテランの方、管理職を対象とした幅広いコンテンツをご用意しております。
お問い合わせ
コストダウンが利益に直結する術だと理解していても、なかなか前に進めることができない状況。そんな時は、newjiのコストダウン自動化機能で大きく利益貢献しよう!
(β版非公開)