- お役立ち記事
- Efficient methods and case studies for long aluminum frame processing
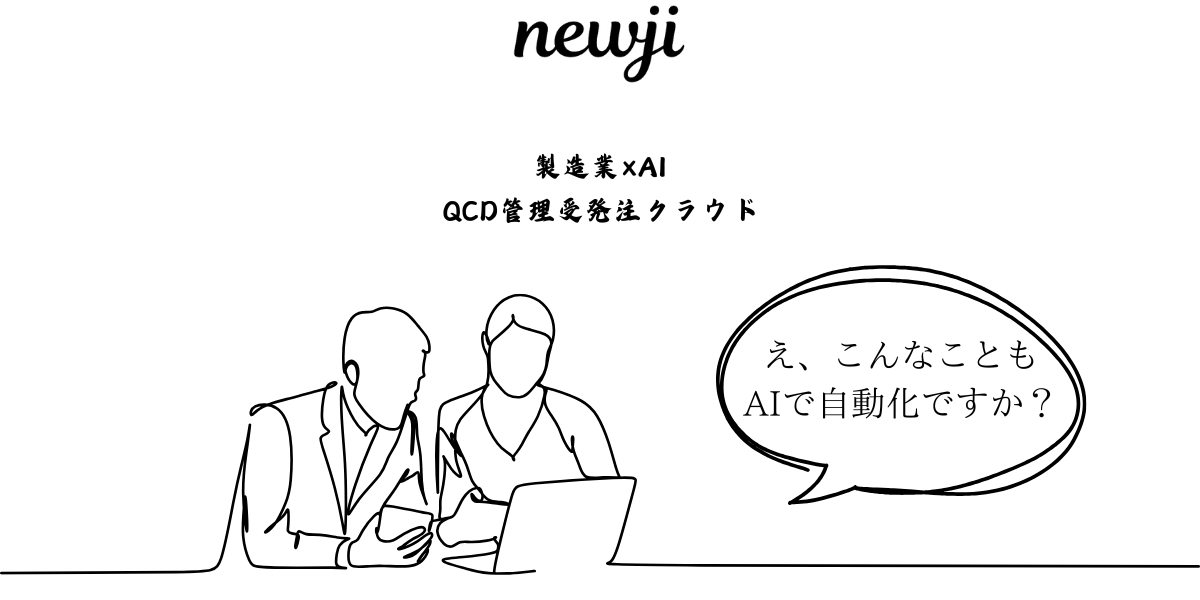
Efficient methods and case studies for long aluminum frame processing
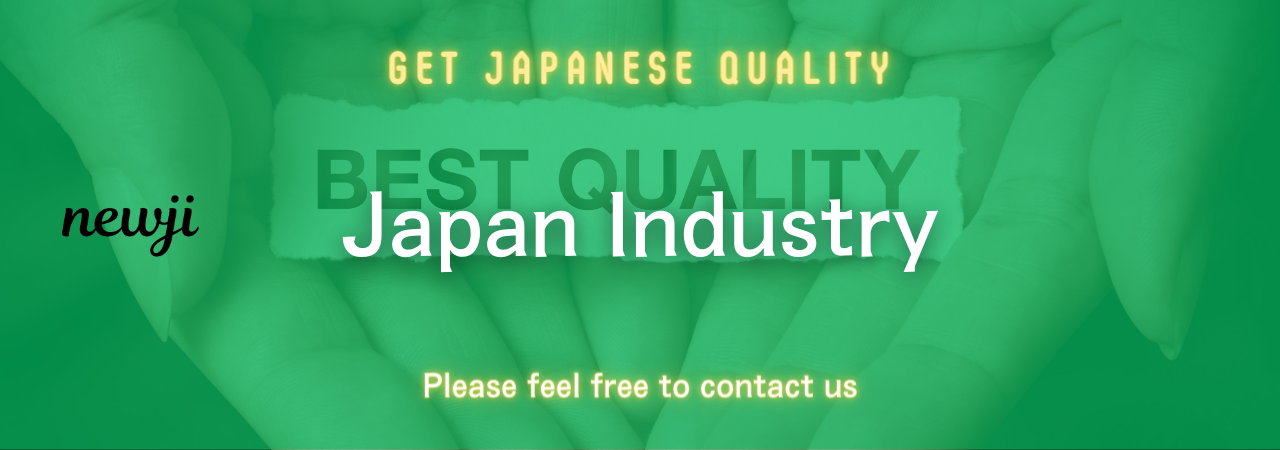
目次
Introduction to Aluminum Frame Processing
Aluminum frames are widely used in various industries due to their lightweight, strength, and corrosion resistance.
From construction to automotive, these frames are integral in providing the necessary structural support.
Processing long aluminum frames efficiently is crucial to maintain production quality and cost-effectiveness.
In this article, we will explore efficient methods and case studies for long aluminum frame processing to help manufacturers enhance their production processes.
Understanding the Key Challenges
Before delving into the efficient methods, it’s essential to recognize the challenges involved in processing long aluminum frames.
These challenges often include:
Material Handling
Long aluminum frames require careful handling to prevent bending, scratches, or other damage.
Proper equipment and techniques are necessary to support and move these frames throughout the processing line.
Precision and Consistency
Maintaining precision is vital, particularly for applications where exact dimensions are critical.
Long frames can be prone to warping or dimensional inaccuracies during processing.
Tool Wear and Maintenance
The tools and machines used in processing aluminum can experience significant wear.
Regular maintenance and timely replacements are necessary to ensure consistent quality and prevent downtime.
Efficient Methods for Long Aluminum Frame Processing
Automated Material Handling Systems
Automated systems play a crucial role in efficient aluminum frame processing.
Using conveyor systems, robotic arms, and servo-controlled equipment ensures gentle handling and reduces the risk of damage.
Automation also speeds up the process, increasing overall productivity.
Advanced Cutting Technology
Precision cutting is vital in aluminum frame processing.
Laser cutting and CNC machining are popular methods that allow for high precision and repeatability.
These technologies reduce waste and minimize the need for post-processing adjustments.
Quality Control Systems
Implementing quality control systems such as inline inspections and automated measuring equipment ensures accuracy throughout the process.
These systems can identify discrepancies early, reducing rework and ensuring quality standards are met.
Tool Management Programs
Incorporating tool management programs helps monitor tool conditions and schedules maintenance or replacements.
This proactive approach minimizes unexpected downtime and maintains high-quality outputs.
Case Studies Highlighting Successful Practices
Case Study 1: Automotive Frame Manufacturing
A leading automotive manufacturer sought to improve the efficiency of their aluminum frame production line.
By integrating automated material handling and laser cutting technology, they minimized manual handling and achieved a 30% increase in production speed.
The implementation of inline inspections further reduced defects, resulting in significant cost savings.
Case Study 2: Construction Frame Production
A construction company specializing in modular buildings needed to enhance the precision of their aluminum frame processing.
By upgrading to CNC machining and implementing a robust tool management program, they reduced waste and improved dimensional accuracy.
This change not only increased their production capacity but also enhanced the structural integrity of the frames.
Best Practices for Implementation
Assessing Current Processes
Before implementing new methods, it’s important to conduct a thorough assessment of existing processes.
Identify bottlenecks, areas of high material waste, and where precision can improve.
Investing in Technology
Technology investments can be substantial, but the long-term benefits often outweigh the initial costs.
Prioritize technologies that align with specific production goals and challenges.
Training and Development
Employees play a crucial role in successful implementation.
Provide comprehensive training on new equipment and technologies to ensure smooth transitions and maximize efficiency gains.
Monitoring and Adaptation
Regularly monitor the process’s performance and make necessary adjustments.
Continuous improvement should be an ongoing goal, ensuring the production process evolves with technology and market demands.
Conclusion
Processing long aluminum frames efficiently requires a combination of advanced technology, robust quality control, and strategic planning.
By understanding the challenges and implementing effective methods, manufacturers can enhance their production capabilities.
The case studies demonstrate the real-world benefits of investing in modern technologies and tools in improving efficiency, precision, and overall product quality.
With thoughtful implementation, these strategies can lead to significant operational improvements and cost savings.
資料ダウンロード
QCD調達購買管理クラウド「newji」は、調達購買部門で必要なQCD管理全てを備えた、現場特化型兼クラウド型の今世紀最高の購買管理システムとなります。
ユーザー登録
調達購買業務の効率化だけでなく、システムを導入することで、コスト削減や製品・資材のステータス可視化のほか、属人化していた購買情報の共有化による内部不正防止や統制にも役立ちます。
NEWJI DX
製造業に特化したデジタルトランスフォーメーション(DX)の実現を目指す請負開発型のコンサルティングサービスです。AI、iPaaS、および先端の技術を駆使して、製造プロセスの効率化、業務効率化、チームワーク強化、コスト削減、品質向上を実現します。このサービスは、製造業の課題を深く理解し、それに対する最適なデジタルソリューションを提供することで、企業が持続的な成長とイノベーションを達成できるようサポートします。
オンライン講座
製造業、主に購買・調達部門にお勤めの方々に向けた情報を配信しております。
新任の方やベテランの方、管理職を対象とした幅広いコンテンツをご用意しております。
お問い合わせ
コストダウンが利益に直結する術だと理解していても、なかなか前に進めることができない状況。そんな時は、newjiのコストダウン自動化機能で大きく利益貢献しよう!
(Β版非公開)