- お役立ち記事
- Efficient process and material selection in vacuum forming plastic tray production
月間77,185名の
製造業ご担当者様が閲覧しています*
*2025年2月28日現在のGoogle Analyticsのデータより
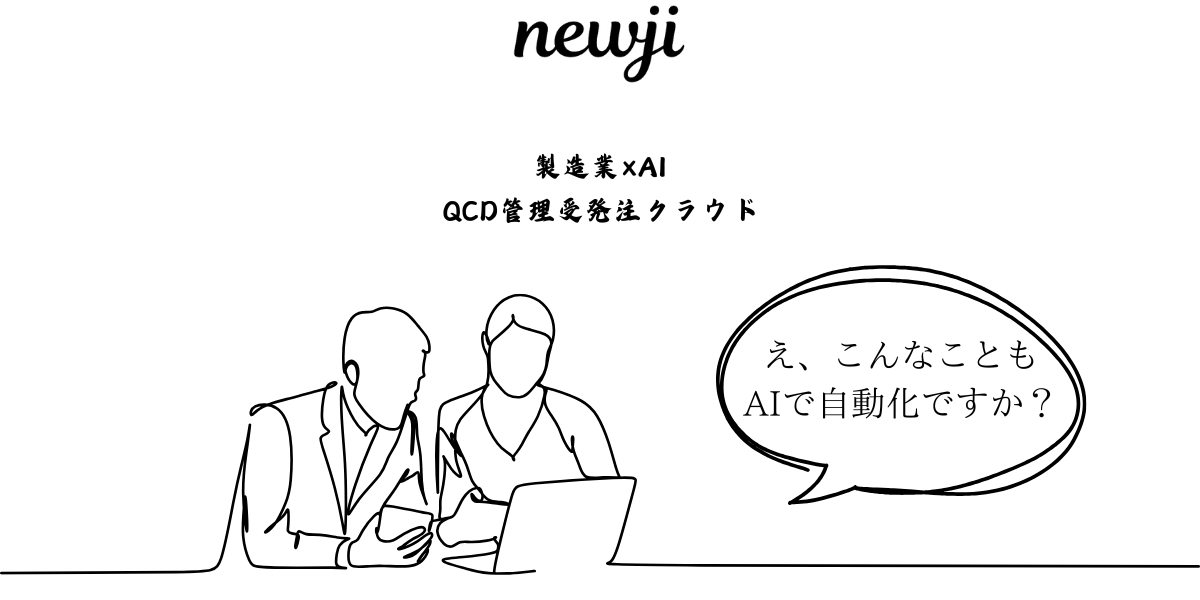
Efficient process and material selection in vacuum forming plastic tray production
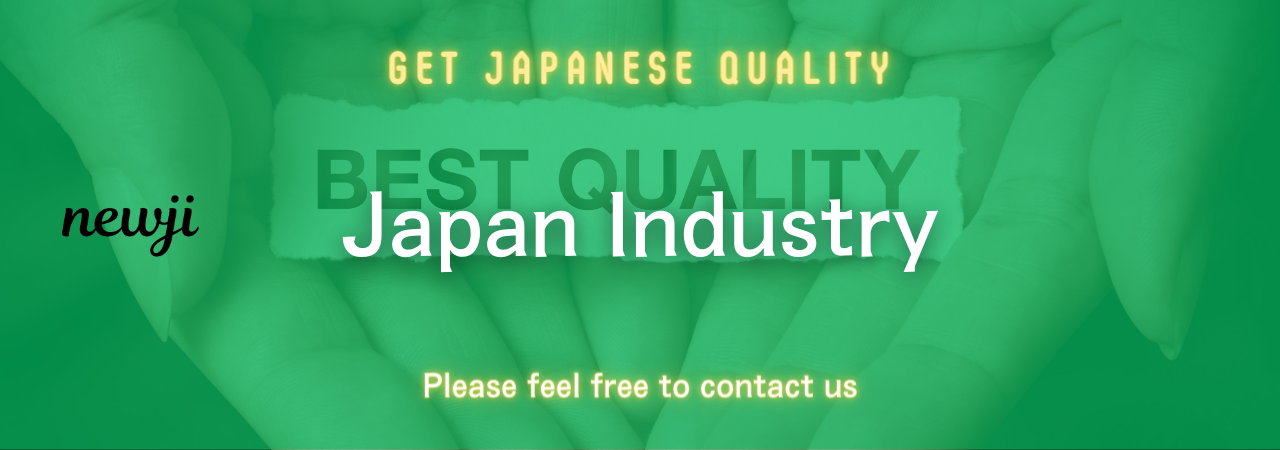
目次
Introduction to Vacuum Forming
Vacuum forming is a popular manufacturing process used to shape plastic materials into various forms.
This method is especially effective for creating plastic trays, which are widely used in industries such as food service, industrial manufacturing, and retail.
The vacuum forming process involves heating a plastic sheet until it becomes pliable, then draping it over a mold.
A vacuum is applied to draw the plastic into the mold’s shape, creating a precise and consistent product.
Understanding the intricacies of vacuum forming and material selection can lead to more efficient production and higher-quality outputs.
Steps in Vacuum Forming Plastic Trays
The vacuum forming process can be broken down into several key steps:
1. Material Selection
Choosing the right material is crucial for the success of vacuum forming.
Common materials include ABS, PETG, PVC, and polycarbonate.
Each material has its characteristics, such as durability, flexibility, and cost, which should align with the specific requirements of the tray’s intended use.
2. Heating
Once the material is selected, it is cut into sheets and placed into the vacuum forming machine for heating.
The temperature must be carefully controlled to ensure the plastic is heated evenly without overheating, which can cause burning or warping.
3. Forming
After reaching the optimal temperature, the heated plastic sheet is placed over a mold.
The vacuum system removes the air between the sheet and the mold, ensuring the plastic conforms to the mold’s shape.
This step is crucial for achieving a high-definition and consistent product.
4. Cooling and Trimming
Once the plastic has formed and cooled sufficiently, it is removed from the mold.
The formed pieces are then trimmed and finished to remove any excess material.
Choosing the Right Material
Selecting the appropriate material for vacuum forming is a critical step in the production process.
Durability
Consider the durability required for the intended application of the plastic tray.
For example, a tray used in industrial settings may need to be more robust compared to one used for food packaging.
Temperature Resistance
Ensure the material can withstand the temperatures needed during the heating phase of vacuum forming without degrading or losing properties.
Cost Efficiency
Assess the cost-effectiveness of materials.
It’s essential to find a balance between quality and expense, especially for large production runs.
Benefits of Vacuum Forming for Plastic Trays
Vacuum forming offers several advantages:
Speed and Efficiency
The process is relatively fast, making it ideal for high-volume production.
Once set up, vacuum forming allows for quick production cycles, crucial for meeting tight deadlines.
Design Flexibility
Vacuum forming provides designers with flexibility to create complex shapes and designs.
This flexibility is key in customizing trays for specific applications.
Cost-Effective Tooling
Compared to other forming methods, vacuum forming requires less expensive tooling.
This lowers the initial investment costs, making it accessible for smaller operations.
High Quality
When executed properly, vacuum forming can produce parts with excellent surface finish and dimensional accuracy.
Challenges and Solutions in Vacuum Forming
Material Uniformity
Maintaining material uniformity throughout the sheet is essential for achieving consistent results.
Investing in high-quality plastic sheets can mitigate inconsistency issues.
Temperature Control
Precise temperature control is necessary to prevent warping and achieving optimal formation.
Using advanced heating systems can provide better control and efficiency.
Tooling and Mold Design
A well-designed mold is critical for avoiding defects such as webbing or thinning.
Collaborating with skilled mold designers helps create molds that account for shrinkage and other nuances of vacuum forming.
Conclusion
Vacuum forming is a versatile and efficient method for producing plastic trays.
By understanding and optimizing the process, from material selection to mold design, manufacturers can significantly enhance productivity and product quality.
Emphasizing proper temperature control, material uniformity, and precision molding will lead to successful outcomes.
As vacuum forming evolves with advancements in technology, it continues to be a valuable asset in plastic manufacturing.
資料ダウンロード
QCD管理受発注クラウド「newji」は、受発注部門で必要なQCD管理全てを備えた、現場特化型兼クラウド型の今世紀最高の受発注管理システムとなります。
ユーザー登録
受発注業務の効率化だけでなく、システムを導入することで、コスト削減や製品・資材のステータス可視化のほか、属人化していた受発注情報の共有化による内部不正防止や統制にも役立ちます。
NEWJI DX
製造業に特化したデジタルトランスフォーメーション(DX)の実現を目指す請負開発型のコンサルティングサービスです。AI、iPaaS、および先端の技術を駆使して、製造プロセスの効率化、業務効率化、チームワーク強化、コスト削減、品質向上を実現します。このサービスは、製造業の課題を深く理解し、それに対する最適なデジタルソリューションを提供することで、企業が持続的な成長とイノベーションを達成できるようサポートします。
製造業ニュース解説
製造業、主に購買・調達部門にお勤めの方々に向けた情報を配信しております。
新任の方やベテランの方、管理職を対象とした幅広いコンテンツをご用意しております。
お問い合わせ
コストダウンが利益に直結する術だと理解していても、なかなか前に進めることができない状況。そんな時は、newjiのコストダウン自動化機能で大きく利益貢献しよう!
(β版非公開)