- お役立ち記事
- Efficient processes and technological approaches in the design and fabrication of drying equipment
月間76,176名の
製造業ご担当者様が閲覧しています*
*2025年3月31日現在のGoogle Analyticsのデータより
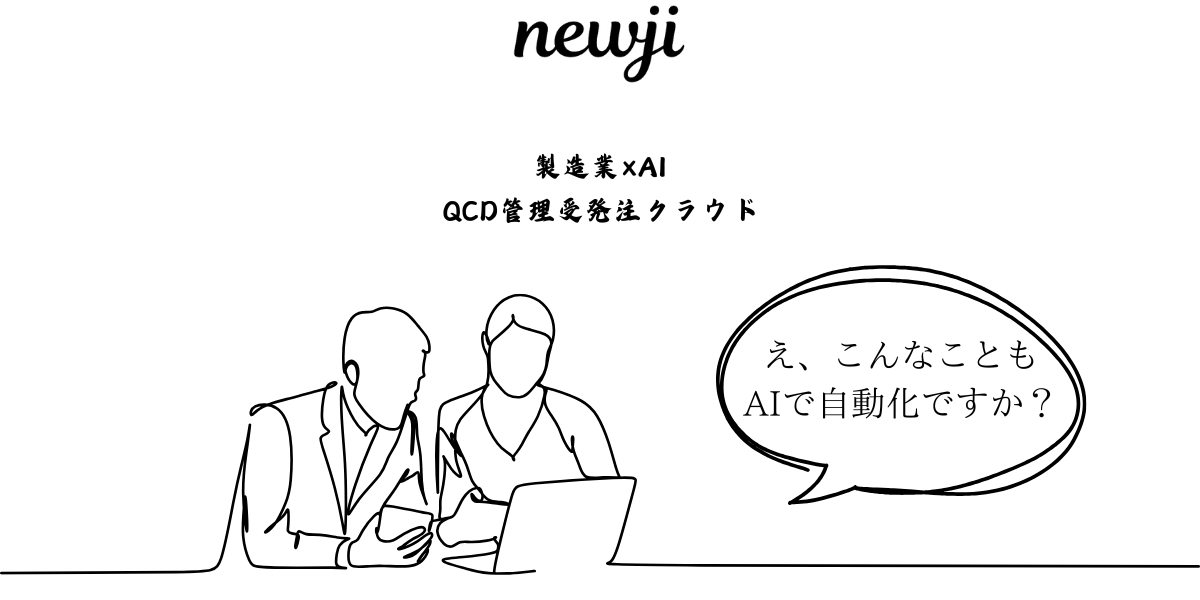
Efficient processes and technological approaches in the design and fabrication of drying equipment
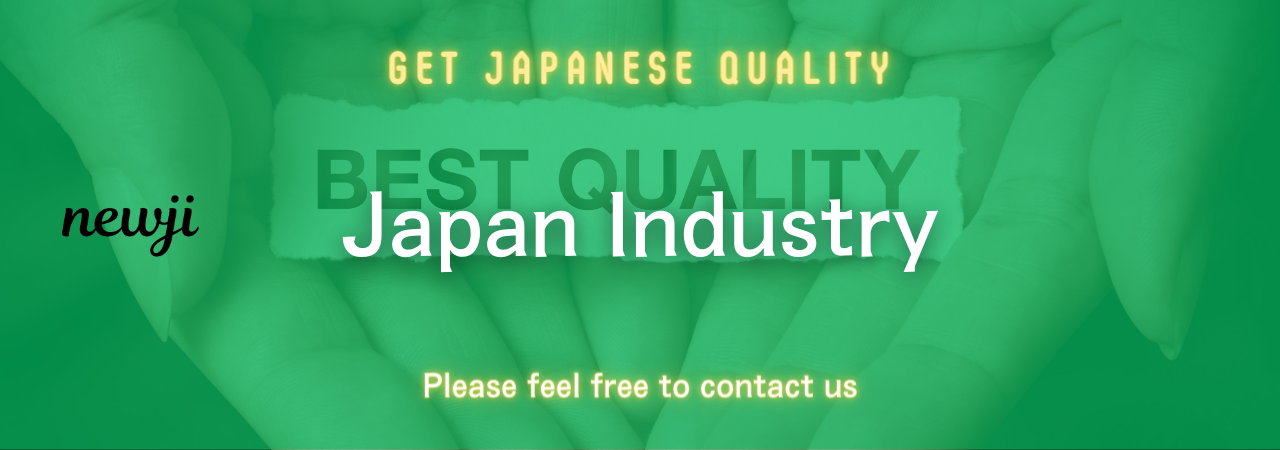
目次
Understanding Drying Equipment in Modern Industries
Drying equipment plays a crucial role in various industries, from food processing to pharmaceuticals.
The main purpose of these machines is to remove moisture from substances, ensuring longer shelf life and improved quality.
In today’s fast-paced industrial world, efficient processes and technological advancements are paramount in the design and fabrication of these pieces of equipment.
The Importance of Drying Processes
Drying is a critical step in the production and processing of many products.
Without proper drying, products can spoil, become contaminated, or lose their desired properties.
In the pharmaceutical industry, for instance, accurate moisture control is essential to maintain the efficacy of drugs.
Similarly, in the food industry, drying helps in preserving the nutritional value and taste of products.
Technological Innovations in Drying Equipment
The advancement of technology has significantly influenced the design and efficiency of drying equipment.
Innovations such as automation, energy-efficient systems, and new drying methods have transformed the drying process.
One key innovation is the use of smart sensors and automation.
These components allow for real-time monitoring and control of the drying process.
With precise moisture detection and temperature regulation, products can be dried more uniformly, reducing the risk of over or under-drying.
Energy efficiency is another area of focus.
Modern drying equipment incorporates energy-saving technologies, reducing overall operational costs and environmental impact.
Heat recovery systems, improved insulation, and the use of renewable energy sources are common features in contemporary designs.
Moreover, new drying technologies like freeze drying, spray drying, and fluidized bed drying have emerged.
These methods cater to specific industry needs, offering improved drying rates and product quality.
Considerations in the Design of Drying Equipment
When designing drying equipment, several factors must be considered.
These include the type of product to be dried, the required drying rate, energy consumption, and equipment size.
The type of product is a primary consideration.
Different products require specific drying conditions to maintain their quality.
For instance, pharmaceuticals need to be dried at low temperatures to preserve their active ingredients, while ceramic materials may need high temperatures to achieve desired hardness.
The drying rate is another critical factor.
A faster drying rate may be advantageous for high-volume production but could compromise product quality if not managed correctly.
The design must ensure that moisture is removed at an optimal rate for the specific product being processed.
Energy consumption impacts both cost and environmental impacts.
Designers aim to minimize energy usage without sacrificing performance.
Innovative designs focus on optimizing airflow and heat transfer to enhance efficiency.
Lastly, equipment size affects installation and space requirements.
In some industries, space constraints necessitate compact designs, while others may prioritize equipment capable of handling large volumes.
The Design and Fabrication Process
The process of designing and fabricating drying equipment is complex, involving several stages.
It begins with understanding the specific needs of the industry and the properties of the materials to be dried.
Researching existing technologies and market needs is crucial for designing equipment that meets customer demands.
Next, the design phase involves creating detailed blueprints.
Here, engineers consider all the factors mentioned earlier, like product type and energy efficiency.
Computational simulations are often used to predict how the design will perform, allowing for adjustments before fabrication begins.
Fabrication is the next step, where advanced manufacturing techniques are employed to build the equipment.
Precision is vital, as even minor deviations can affect performance.
Quality control measures are implemented throughout this process to ensure the final product adheres to design specifications.
Finally, once assembled, the equipment undergoes rigorous testing.
This phase ensures that it operates as expected under various conditions.
Future Trends in Drying Equipment Technology
The industry is continually evolving, and future trends point towards even more sophisticated drying equipment.
One such trend is the integration of artificial intelligence (AI) in drying processes.
AI can enhance decision-making, improve process efficiency, and predict maintenance needs, leading to prolonged equipment lifespan.
Another trend is the development of more environment-friendly drying solutions.
With increasing environmental regulations, there’s a push towards reducing emissions and using sustainable energy sources in drying processes.
Additionally, customization and modular designs are becoming popular.
Modular equipment allows companies to adapt and expand their capabilities as needed, offering greater flexibility and scalability.
Conclusion
Efficient processes and technological advancements are driving the evolution of drying equipment in various industries.
From smart sensors and automation to energy-efficient systems and innovative drying methods, modern drying equipment is vastly superior to its predecessors.
As technology continues to advance, we can expect even more improvements, making drying processes quicker, more cost-effective, and environmentally friendly.
Understanding these developments can help industries select the right equipment to meet their needs, ensuring better product quality and operational efficiency.
資料ダウンロード
QCD管理受発注クラウド「newji」は、受発注部門で必要なQCD管理全てを備えた、現場特化型兼クラウド型の今世紀最高の受発注管理システムとなります。
ユーザー登録
受発注業務の効率化だけでなく、システムを導入することで、コスト削減や製品・資材のステータス可視化のほか、属人化していた受発注情報の共有化による内部不正防止や統制にも役立ちます。
NEWJI DX
製造業に特化したデジタルトランスフォーメーション(DX)の実現を目指す請負開発型のコンサルティングサービスです。AI、iPaaS、および先端の技術を駆使して、製造プロセスの効率化、業務効率化、チームワーク強化、コスト削減、品質向上を実現します。このサービスは、製造業の課題を深く理解し、それに対する最適なデジタルソリューションを提供することで、企業が持続的な成長とイノベーションを達成できるようサポートします。
製造業ニュース解説
製造業、主に購買・調達部門にお勤めの方々に向けた情報を配信しております。
新任の方やベテランの方、管理職を対象とした幅広いコンテンツをご用意しております。
お問い合わせ
コストダウンが利益に直結する術だと理解していても、なかなか前に進めることができない状況。そんな時は、newjiのコストダウン自動化機能で大きく利益貢献しよう!
(β版非公開)