- お役立ち記事
- Efficient Procurement Strategies and Technical Considerations for Ion Nitriding OEM
月間76,176名の
製造業ご担当者様が閲覧しています*
*2025年3月31日現在のGoogle Analyticsのデータより
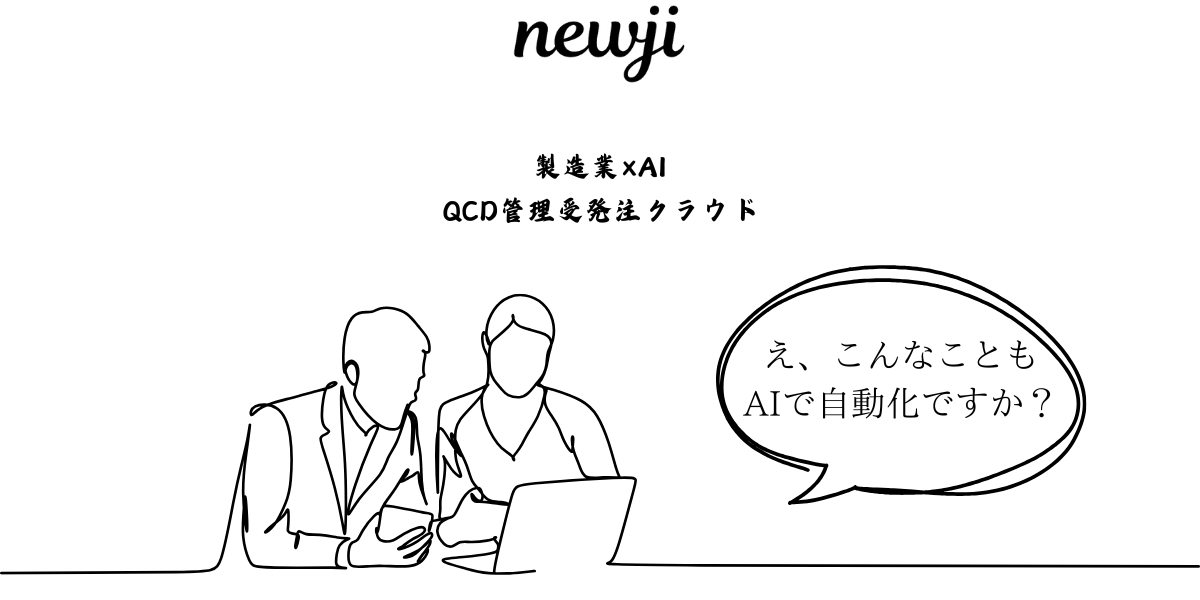
Efficient Procurement Strategies and Technical Considerations for Ion Nitriding OEM
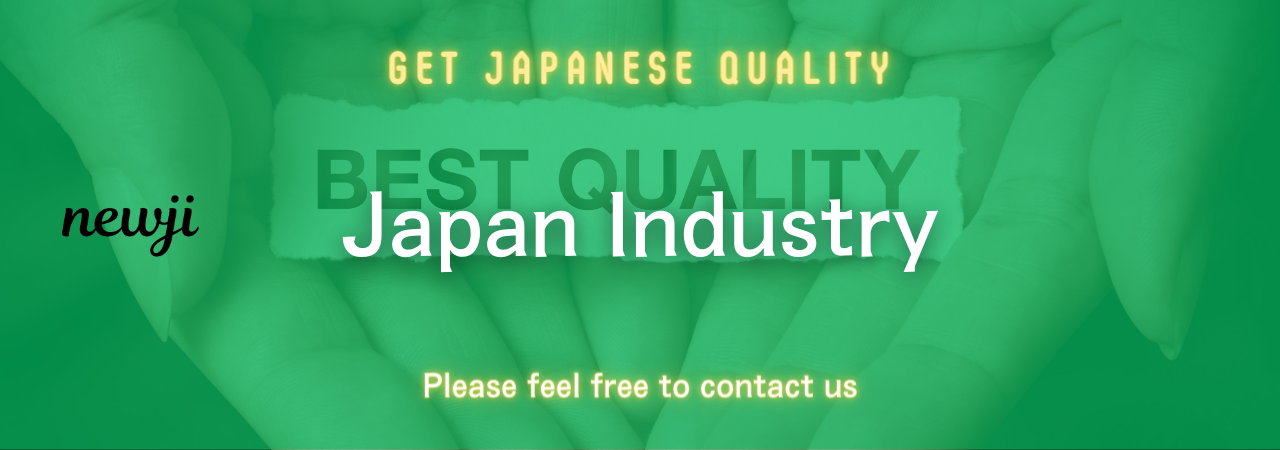
目次
Understanding Ion Nitriding OEM
Ion nitriding, also known as plasma nitriding, is a surface-hardening process that is crucial for enhancing the wear resistance, fatigue strength, and corrosion resistance of metallic components.
This advanced manufacturing technique is especially beneficial for Original Equipment Manufacturers (OEM) in various industries, including automotive, aerospace, and engineering.
To achieve efficient procurement strategies and meet the technical requirements for ion nitriding OEM, it’s essential to understand both the technical aspects and effective procurement practices.
Technical Considerations for Ion Nitriding
1. Material Selection
The first step in ion nitriding is selecting the right material.
Not all metals are suitable for this process.
Materials such as steels, titanium, aluminum, and their alloys are typically chosen for ion nitriding due to their ability to form stable nitrides.
Understanding the material’s composition, including carbon and alloying elements, is crucial because these factors influence the nitriding response and the characteristics of the nitrided layer.
2. Surface Preparation
Before the ion nitriding process begins, the surface of the material must be meticulously prepared.
This involves cleaning the surface to remove any contaminants like oils, oxides, and dust.
Proper cleaning ensures that the nitride layer forms uniformly and adheres well to the substrate.
Advanced techniques such as ultrasonic cleaning or using abrasive methods can be employed for surface preparation.
3. Process Parameters
Ion nitriding involves several critical parameters that need to be controlled precisely:
– **Temperature:** The process temperature typically ranges between 400°C to 600°C.
Higher temperatures can enhance diffusion rates but may also affect the core properties of the material.
– **Pressure:** Maintaining a controlled pressure inside the nitriding chamber ensures the proper formation of the plasma.
– **Gas Composition:** A mixture of nitrogen and hydrogen gases is used.
The ratio of these gases directly influences the nitriding kinetics and the properties of the nitrided layer.
– **Time:** The duration of the nitriding process depends on the desired depth and thickness of the nitrided layer.
4. Layer Characteristics
The primary goal of ion nitriding is to produce a hard, wear-resistant surface layer.
The nitrided layer comprises two zones:
– **Compound Layer:** This is the outermost layer, primarily consisting of iron nitrides in steels.
It provides excellent wear resistance and hardness but can be brittle if too thick.
– **Diffusion Layer:** Located beneath the compound layer, this zone exhibits a gradual nitrogen concentration.
It enhances fatigue strength and provides a more ductile support for the hard surface.
Procurement Strategies for Ion Nitriding OEM
Efficient procurement strategies are vital to ensure that the ion nitriding process is cost-effective and meets the quality requirements.
1. Supplier Evaluation
Choosing the right supplier is the cornerstone of a successful procurement strategy.
Evaluate potential suppliers based on:
– **Experience and Expertise:** Look for suppliers with a proven track record in ion nitriding services.
– **Certifications:** Ensure the supplier holds relevant certifications and adheres to industry standards.
– **Capacity and Capabilities:** Verify that the supplier has the capacity to handle your production volumes and capabilities to meet specific technical requirements.
2. Cost Analysis
Conduct a comprehensive cost analysis to determine the total cost of the ion nitriding process.
This includes:
– **Material Costs:** Assess the costs of the base materials suitable for nitriding.
– **Process Costs:** Factor in the expenses related to the ion nitriding process, including gas usage, energy consumption, and labor costs.
– **Quality Control Costs:** Consider costs associated with quality control measures such as testing and inspection to ensure the desired layer characteristics.
3. Quality Assurance
Quality assurance is paramount in the ion nitriding process.
Implement a robust quality assurance plan that includes:
– **Material Inspection:** Inspect incoming materials to confirm their suitability for ion nitriding.
– **In-Process Monitoring:** Monitor critical parameters during the nitriding process to ensure consistency and quality.
– **Final Inspection:** Conduct thorough testing and inspection of the nitrided components to verify compliance with specifications.
4. Lead Time Management
Effective lead time management is essential to meet production schedules and deadlines.
Communicate closely with suppliers to establish realistic lead times.
Consider factors such as:
– **Production Scheduling:** Coordinate production schedules to align with the nitriding process timeline.
– **Logistics:** Plan for transportation and handling of the nitrided components to avoid delays.
5. Sustainability Considerations
Incorporate sustainability practices into your procurement strategy to reduce environmental impact.
Consider:
– **Energy Efficiency:** Opt for suppliers who use energy-efficient equipment and processes.
– **Waste Management:** Ensure proper waste management practices are in place to handle by-products of the nitriding process.
– **Green Certifications:** Look for suppliers with green certifications to ensure they adhere to environmentally-friendly practices.
Conclusion
Implementing efficient procurement strategies and understanding the technical considerations associated with ion nitriding OEM are crucial for achieving high-quality, cost-effective results.
By focusing on material selection, surface preparation, process parameters, and forming robust supplier relationships, OEMs can enhance their manufacturing capabilities and produce components with superior wear resistance, fatigue strength, and corrosion resistance.
In today’s competitive manufacturing landscape, these strategies can provide a significant advantage and contribute to the overall success of the business.
資料ダウンロード
QCD管理受発注クラウド「newji」は、受発注部門で必要なQCD管理全てを備えた、現場特化型兼クラウド型の今世紀最高の受発注管理システムとなります。
ユーザー登録
受発注業務の効率化だけでなく、システムを導入することで、コスト削減や製品・資材のステータス可視化のほか、属人化していた受発注情報の共有化による内部不正防止や統制にも役立ちます。
NEWJI DX
製造業に特化したデジタルトランスフォーメーション(DX)の実現を目指す請負開発型のコンサルティングサービスです。AI、iPaaS、および先端の技術を駆使して、製造プロセスの効率化、業務効率化、チームワーク強化、コスト削減、品質向上を実現します。このサービスは、製造業の課題を深く理解し、それに対する最適なデジタルソリューションを提供することで、企業が持続的な成長とイノベーションを達成できるようサポートします。
製造業ニュース解説
製造業、主に購買・調達部門にお勤めの方々に向けた情報を配信しております。
新任の方やベテランの方、管理職を対象とした幅広いコンテンツをご用意しております。
お問い合わせ
コストダウンが利益に直結する術だと理解していても、なかなか前に進めることができない状況。そんな時は、newjiのコストダウン自動化機能で大きく利益貢献しよう!
(β版非公開)