- お役立ち記事
- Efficient response to FMEA and man-hour reduction measures in the automotive industry quality international standard IATF16949
月間76,176名の
製造業ご担当者様が閲覧しています*
*2025年3月31日現在のGoogle Analyticsのデータより
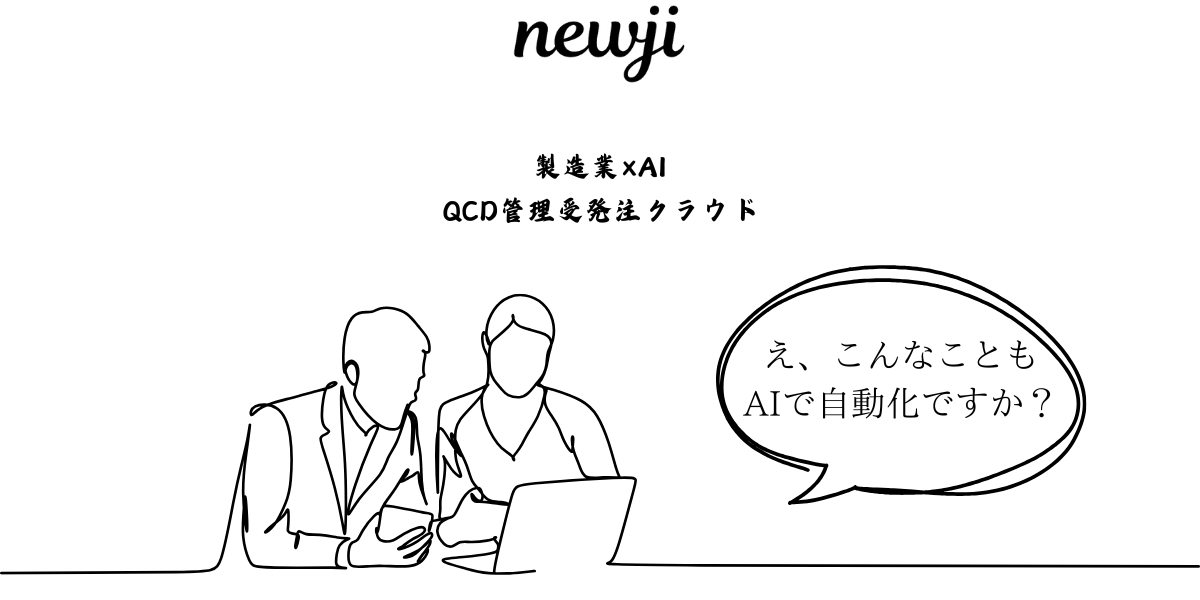
Efficient response to FMEA and man-hour reduction measures in the automotive industry quality international standard IATF16949
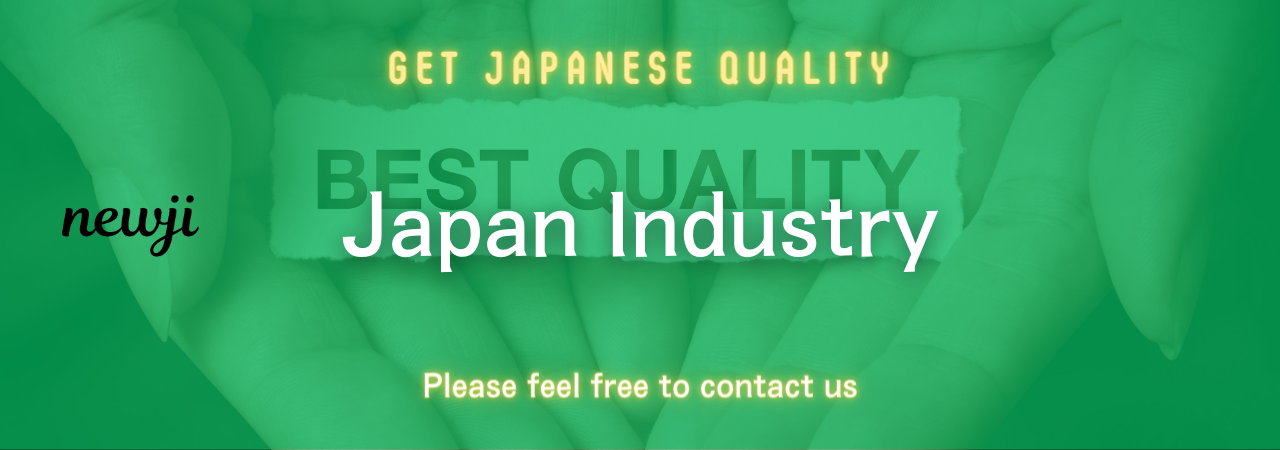
目次
Understanding FMEA in the Automotive Industry
The automotive industry is one of the most complex and competitive sectors in the world.
Ensuring the production of top-quality vehicles requires adherence to strict international standards, among which the IATF 16949 plays a pivotal role.
A crucial component of this standard is the Failure Mode and Effects Analysis, commonly known as FMEA.
This approach helps in identifying potential failures in the design and manufacturing process, thereby preventing defects in the final product.
FMEA is a structured method that focuses on finding possible failures, their causes, and effects, and prioritizing them based on severity.
By understanding these potential issues early, automotive manufacturers can devise appropriate strategies to mitigate them.
This not only enhances product reliability but also helps in reducing overall manufacturing costs.
The application of FMEA involves a series of steps.
These include defining the system being analyzed, identifying potential failure modes, assessing the effects of these failures, and prioritizing them based on risk.
The systematic approach of FMEA ensures that potential failures are addressed before they can impact the product or the production process.
Benefits of Integrating FMEA with IATF 16949
Integrating FMEA with the IATF 16949 standard offers numerous benefits to automotive manufacturers.
It allows for a comprehensive understanding of risks associated with product development and production.
This integration also ensures that risk management becomes an intrinsic part of the quality management system.
One significant advantage of this integration is the reduction of warranty claims.
By addressing potential failures during the design and manufacturing stages, manufacturers can significantly reduce the likelihood of defects reaching the consumer.
This, in turn, enhances customer satisfaction and reduces costs associated with warranty repairs and product recalls.
Moreover, FMEA complements the continuous improvement strategy advocated by IATF 16949.
It facilitates systematic failure analysis and aids in pinpointing areas where improvements are needed, ensuring that changes are data-driven and effective.
Effective Response Strategies for FMEA
To respond efficiently to FMEA findings, automotive companies need to implement well-structured strategies.
These strategies should focus not only on identifying and documenting potential failures but also on developing robust action plans to address them.
Creating cross-functional teams can be particularly effective.
These teams should include members from design, engineering, quality assurance, and production.
Their diverse expertise can help in developing comprehensive action plans to mitigate identified risks.
Additionally, regular training sessions should be conducted to familiarize the workforce with FMEA processes and their significance.
Such training ensures that employees at all levels understand the importance of identifying potential failures and actively engage in risk mitigation.
The use of advanced software tools can also enhance the FMEA process.
These tools allow for better documentation, analysis, and tracking of potential failures and corrective actions.
Implementing technology-driven solutions facilitates a more streamlined and efficient FMEA process.
Reducing Man-Hours with FMEA
An efficient FMEA process not only enhances product quality but also contributes to the reduction of man-hours spent on addressing potential issues.
By proactively identifying and mitigating risks, companies can avoid costly reworks and delays in production.
Automation plays a critical role in achieving this.
By automating repetitive tasks within the FMEA process, such as data collection and report generation, companies can significantly reduce time spent on these activities.
This allows team members to focus on strategic tasks that require human expertise.
Furthermore, the use of predictive analytics can help in foreseeing potential issues before they arise.
By leveraging data, manufacturers can anticipate problems and take preemptive measures, thereby reducing the need for last-minute interventions.
Streamlining communication across departments is another effective man-hour reduction measure.
With clear communication channels in place, teams can share insights and findings more efficiently, leading to quicker resolution of issues identified through FMEA.
Implementing IATF 16949 for Better Outcomes
IATF 16949 provides a comprehensive framework for establishing a quality management system tailored to the automotive sector.
Implementing this standard ensures that manufacturers align their processes with global best practices, leading to improved product quality and operational efficiency.
A key aspect of implementing IATF 16949 is its focus on customer satisfaction.
By emphasizing defect prevention and process improvement, the standard helps manufacturers meet and exceed customer expectations.
Documentation is another crucial aspect.
Accurate and detailed documentation of all processes ensures traceability and facilitates audits, which are essential for maintaining compliance with the standard.
Additionally, regular internal audits and management reviews are recommended to ensure continuous adherence to IATF 16949.
These activities help in identifying gaps in the system and implementing corrective measures proactively.
Conclusion
Adopting FMEA and integrating it with the IATF 16949 standard is essential for any automotive manufacturer aiming for excellence.
Not only does it enhance product reliability and customer satisfaction, but it also contributes to significant man-hour savings.
By focusing on systematic failure analysis, manufacturers can ensure that potential issues are addressed well before they become problems, leading to smoother operations and better quality products.
With the right strategies and tools in place, automotive companies can make informed decisions, optimize their processes, and stand out in an intensely competitive market.
資料ダウンロード
QCD管理受発注クラウド「newji」は、受発注部門で必要なQCD管理全てを備えた、現場特化型兼クラウド型の今世紀最高の受発注管理システムとなります。
ユーザー登録
受発注業務の効率化だけでなく、システムを導入することで、コスト削減や製品・資材のステータス可視化のほか、属人化していた受発注情報の共有化による内部不正防止や統制にも役立ちます。
NEWJI DX
製造業に特化したデジタルトランスフォーメーション(DX)の実現を目指す請負開発型のコンサルティングサービスです。AI、iPaaS、および先端の技術を駆使して、製造プロセスの効率化、業務効率化、チームワーク強化、コスト削減、品質向上を実現します。このサービスは、製造業の課題を深く理解し、それに対する最適なデジタルソリューションを提供することで、企業が持続的な成長とイノベーションを達成できるようサポートします。
製造業ニュース解説
製造業、主に購買・調達部門にお勤めの方々に向けた情報を配信しております。
新任の方やベテランの方、管理職を対象とした幅広いコンテンツをご用意しております。
お問い合わせ
コストダウンが利益に直結する術だと理解していても、なかなか前に進めることができない状況。そんな時は、newjiのコストダウン自動化機能で大きく利益貢献しよう!
(β版非公開)