- お役立ち記事
- Electric Kettle Manufacturing Process and Assembly Methods
月間76,176名の
製造業ご担当者様が閲覧しています*
*2025年3月31日現在のGoogle Analyticsのデータより
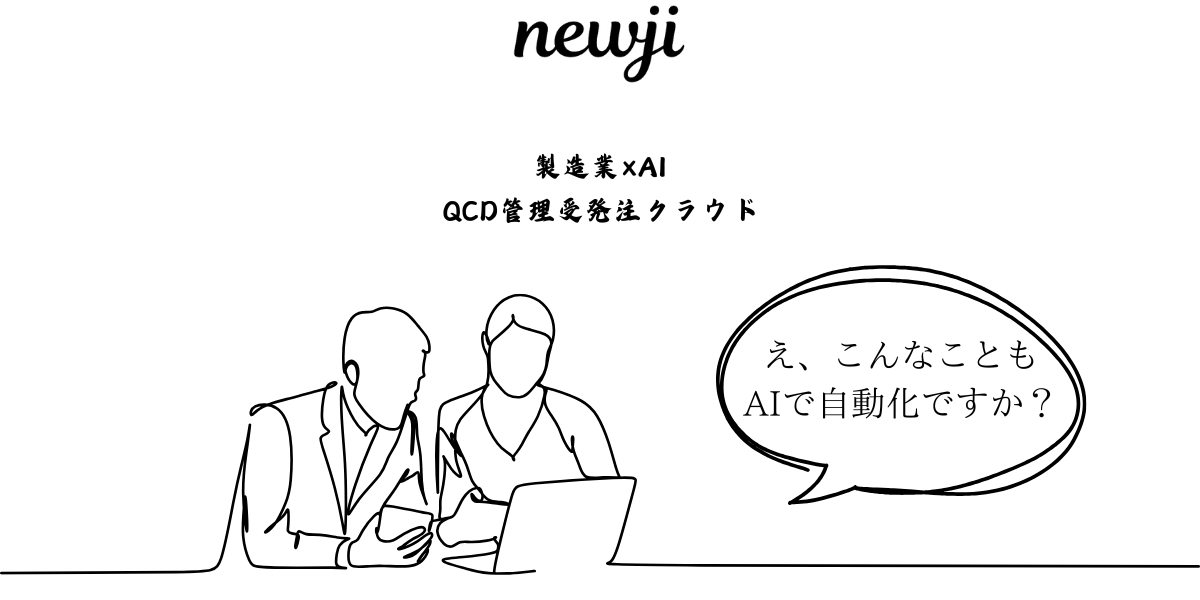
Electric Kettle Manufacturing Process and Assembly Methods
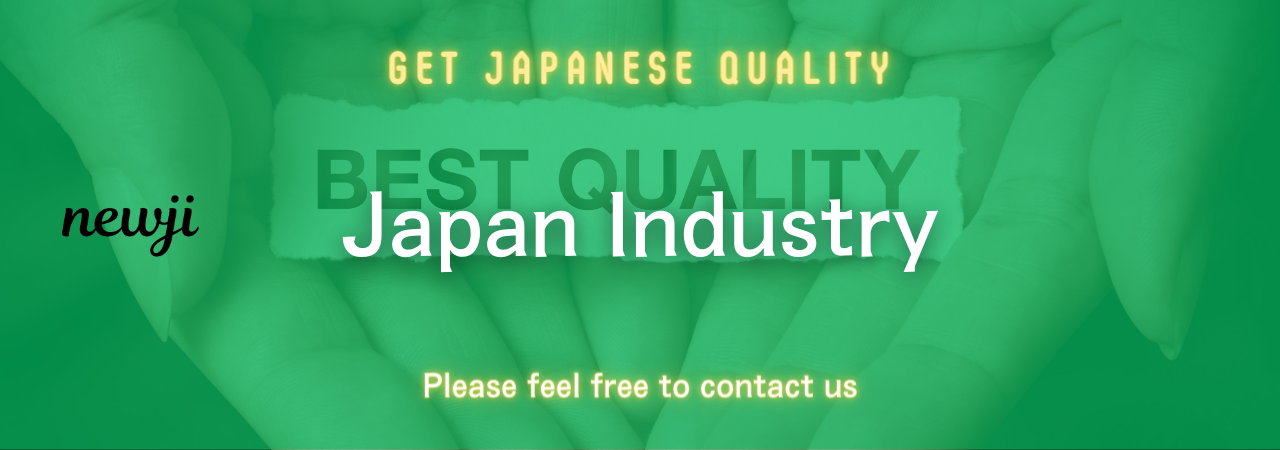
目次
Introduction to Electric Kettle Manufacturing
Electric kettles have become an essential appliance in modern kitchens, providing a convenient and efficient way to boil water quickly.
The manufacturing process of an electric kettle involves various steps and assembly methods to ensure these appliances are both safe and durable.
Understanding the intricacies of this process can provide insights into how these everyday items are brought to life.
Material Selection and Design
The first step in the manufacturing process is selecting appropriate materials.
The body of the kettle is typically made from plastic, stainless steel, or glass.
Each material offers different benefits; stainless steel provides durability, plastic offers lightweight options, and glass allows for an aesthetic appeal with visibility of the boiling process.
Once the material is chosen, the design phase begins.
Engineers focus on creating a kettle that is ergonomic, energy-efficient, and aesthetically pleasing.
The design also involves planning the heating element’s placement, ensuring it is efficient in transferring heat to the water.
Component Manufacturing
The manufacturing of components involves several distinct processes:
– **Body and Base Formation**: The kettle’s body is typically formed using injection molding for plastic, sheet metal stamping for stainless steel, or glass blowing for glass kettles.
– **Heating Element Production**: The heating element is often made of nichrome, a metal alloy, which is wound and then covered with a layer of copper or silver for efficient electrical conductivity.
– **Assembly of the Handle and Lid**: Handles and lids are manufactured separately, usually from heat-resistant materials to ensure user safety during operation.
Each component is made to precise specifications to ensure functionality and safety standards are met.
Assembly Process
Once the individual components are prepared, the assembly process begins:
Base and Heating Element Integration
The first step in assembly involves integrating the heating element into the kettle’s base.
This is often done using specialized machinery that precisely fits the heating element in place, ensuring it makes direct contact with the kettle’s base for efficient heat conduction.
Body and Spout Assembly
The kettle’s body is then fitted over the base.
This stage considers design aspects such as insulation and energy efficiency.
The spout is also attached, with care taken to ensure it is watertight and aligned with the kettle’s design.
Attachment of the Handle and Lid
Next, the handle is securely fastened to the body of the kettle.
The lid is attached, often incorporating a hinge mechanism for easy use.
Both handle and lid fittings are tested for stability and comfort.
Quality Control and Testing
Once assembled, electric kettles undergo rigorous quality control to ensure they meet safety and performance standards.
Testing includes:
– **Leakage Tests**: Ensuring no water seeps from seals or joints when the kettle is filled and tilted.
– **Heating Efficiency Tests**: Assessing how quickly and efficiently the kettle heats water.
– **Durability Tests**: Subjecting the kettle to various stress conditions to test material strength and construction durability.
Each kettle is inspected for defects, and any unit that fails quality control is either reworked or recycled.
Packaging and Distribution
After passing quality control, kettles are cleaned, polished, and prepared for packaging.
Packaging involves placing the kettle, along with instructions and warranty information, into boxes designed to protect the product during shipping.
Boxes are then sealed and prepared for distribution.
From here, the kettles are distributed to retail locations, where they are made available to consumers worldwide.
Conclusion
The manufacturing process of an electric kettle involves precise engineering and meticulous quality control to produce a reliable, efficient product.
By understanding this process, consumers can appreciate the thought and technology that goes into creating these invaluable kitchen tools.
Next time you boil water in an electric kettle, remember the careful craftsmanship that ensures safety and convenience with every use.
資料ダウンロード
QCD管理受発注クラウド「newji」は、受発注部門で必要なQCD管理全てを備えた、現場特化型兼クラウド型の今世紀最高の受発注管理システムとなります。
ユーザー登録
受発注業務の効率化だけでなく、システムを導入することで、コスト削減や製品・資材のステータス可視化のほか、属人化していた受発注情報の共有化による内部不正防止や統制にも役立ちます。
NEWJI DX
製造業に特化したデジタルトランスフォーメーション(DX)の実現を目指す請負開発型のコンサルティングサービスです。AI、iPaaS、および先端の技術を駆使して、製造プロセスの効率化、業務効率化、チームワーク強化、コスト削減、品質向上を実現します。このサービスは、製造業の課題を深く理解し、それに対する最適なデジタルソリューションを提供することで、企業が持続的な成長とイノベーションを達成できるようサポートします。
製造業ニュース解説
製造業、主に購買・調達部門にお勤めの方々に向けた情報を配信しております。
新任の方やベテランの方、管理職を対象とした幅広いコンテンツをご用意しております。
お問い合わせ
コストダウンが利益に直結する術だと理解していても、なかなか前に進めることができない状況。そんな時は、newjiのコストダウン自動化機能で大きく利益貢献しよう!
(β版非公開)