- お役立ち記事
- Electric Scooter Manufacturing Process and Battery Efficiency Improvement
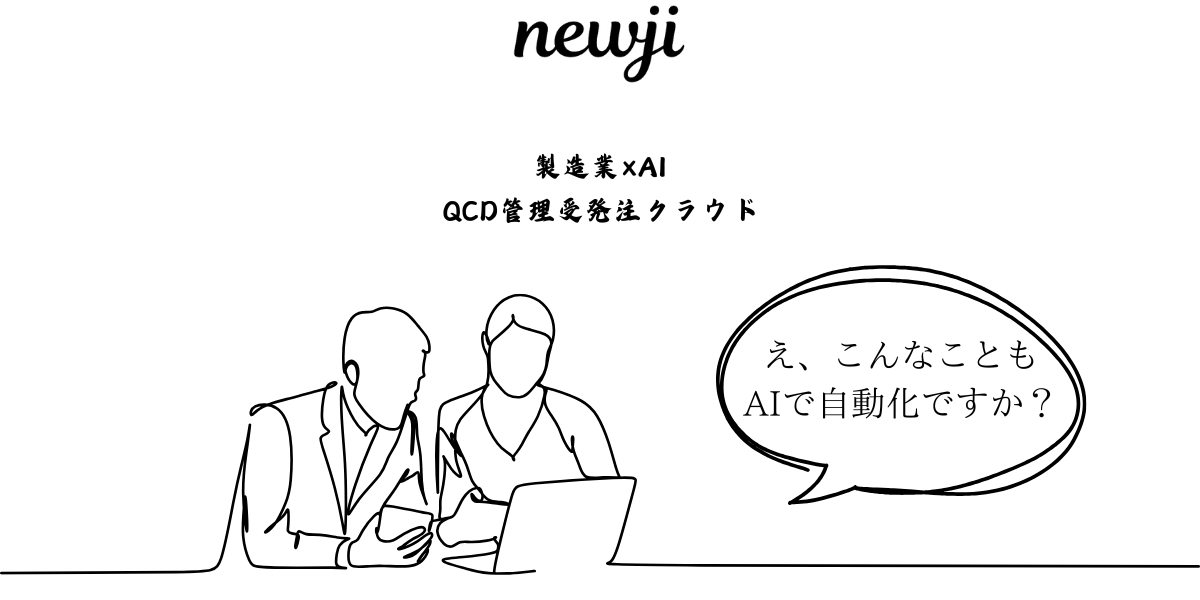
Electric Scooter Manufacturing Process and Battery Efficiency Improvement
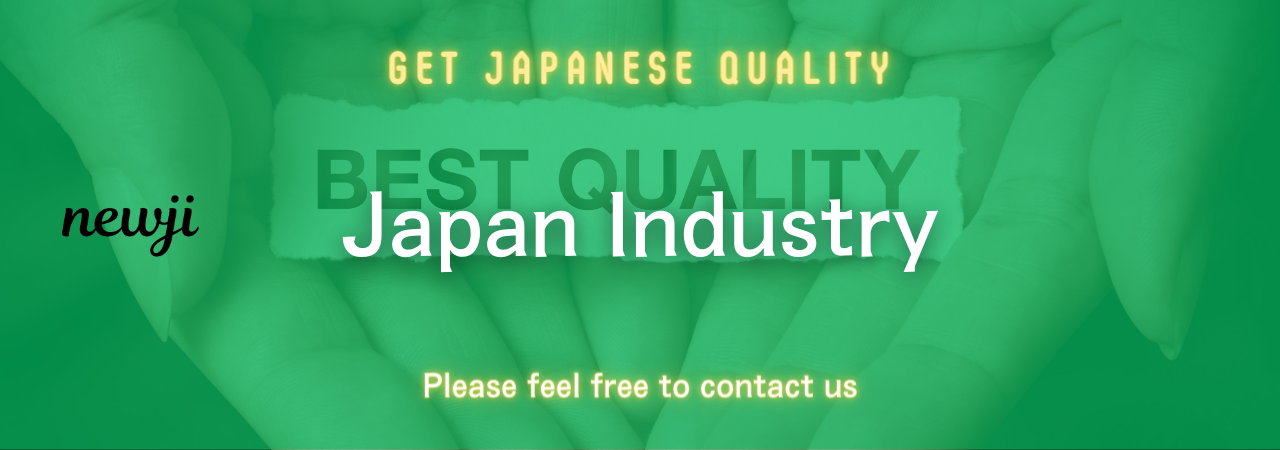
目次
Introduction to Electric Scooter Manufacturing
Electric scooters have rapidly gained popularity as a convenient, eco-friendly mode of transportation.
The rise in their demand has pushed manufacturers to focus on efficient production processes and improve battery performance.
Understanding the electric scooter manufacturing process and how to enhance battery efficiency is crucial in today’s competitive market.
Initial Design and Concept Development
The manufacturing process begins with designing the electric scooter.
Designers consider factors like aerodynamics, weight, and aesthetic appeal to ensure a balance between performance and style.
Using Computer-Aided Design (CAD) software, they create prototypes that undergo thorough testing and simulations.
This stage also involves researching consumer needs and market trends to develop a product that appeals to potential buyers.
Material Selection
Selecting appropriate materials is vital in the manufacturing process.
Manufacturers often use lightweight yet durable materials such as aluminum alloys or carbon fiber to construct the frame.
The selection aims to provide stability while keeping the scooter’s weight low for enhanced performance and battery efficiency.
Components and Parts
An electric scooter is composed of various components like the motor, battery, brakes, and wheels.
Manufacturers source high-quality parts to ensure reliability and longevity.
Each component plays a significant role in overall performance, so making informed decisions during this stage is essential.
Assembling the Electric Scooter
Once the design and materials are finalized, the next step is assembly.
Scaffolding provides the structural base where different components are mounted.
Workers assemble the frame, affix the wheels, and integrate the braking system.
Attention to detail during assembly ensures that all parts fit perfectly, reducing the chances of malfunctions.
Installing the Motor and Battery
The motor acts as the powerhouse that propels the scooter forward, while the battery provides the necessary energy.
Installing the motor involves precise adjustments to ensure optimal performance.
Batteries must be properly housed and connected to prevent any electrical issues.
Manufacturers aim to optimize these components to increase long-term efficiency and durability.
Quality Control and Testing
Quality control is a critical phase where assembled scooters undergo rigorous testing.
This process ensures that each unit meets safety and performance standards.
Testing might involve simulations of road conditions, performance assessments, and battery efficiency checks.
Quality control prevents defective products from reaching customers, maintaining the manufacturer’s reputation.
Improving Battery Efficiency
Battery efficiency is a key focal point for improving electric scooter performance.
By enhancing battery technology, manufacturers can extend the scooter’s range and reduce charging times.
Advancements in Battery Technology
Recent advancements in battery technology have contributed significantly to improved efficiency.
Lithium-ion batteries are commonly used due to their high energy density and long lifespan.
Researchers are developing solid-state batteries, which promise even greater energy capacity and faster charging times.
Battery Management Systems
A Battery Management System (BMS) ensures that the battery operates within safe parameters, prolonging its life.
The BMS monitors the battery’s state of charge and health, balancing the load across cells.
It prevents overcharging and discharging, which can degrade battery performance over time.
Optimizing Charging Practices
In addition to technological improvements, optimizing charging practices plays a vital role in enhancing battery efficiency.
Fast-charging stations and home chargers designed specifically for electric scooters aid in maintaining battery health.
Educating users about proper charging habits can significantly impact overall performance.
Environmental Considerations
While improving efficiency, manufacturers also focus on reducing the environmental impact of their production processes.
Sustainable practices in manufacturing and design help minimize carbon footprints.
Eco-friendly Materials
Using recyclable and biodegradable materials in scooter construction reduces environmental impact.
Manufacturers are increasingly adopting green materials to align with global sustainability goals.
Reducing Waste in Production
Minimizing waste during production processes is another critical area.
Implementing lean manufacturing techniques helps reduce material wastage and energy consumption.
Efforts like recycling scraps and using renewable energy sources contribute to a more sustainable operation.
Conclusion
The electric scooter manufacturing process involves numerous stages, from initial design to assembly and quality control.
By leveraging advancements in battery technology and adopting sustainable practices, manufacturers can improve both efficiency and environmental friendliness.
As the demand for electric scooters continues to grow, continuous innovation will be key to meeting consumer needs and promoting a sustainable future.
資料ダウンロード
QCD調達購買管理クラウド「newji」は、調達購買部門で必要なQCD管理全てを備えた、現場特化型兼クラウド型の今世紀最高の購買管理システムとなります。
ユーザー登録
調達購買業務の効率化だけでなく、システムを導入することで、コスト削減や製品・資材のステータス可視化のほか、属人化していた購買情報の共有化による内部不正防止や統制にも役立ちます。
NEWJI DX
製造業に特化したデジタルトランスフォーメーション(DX)の実現を目指す請負開発型のコンサルティングサービスです。AI、iPaaS、および先端の技術を駆使して、製造プロセスの効率化、業務効率化、チームワーク強化、コスト削減、品質向上を実現します。このサービスは、製造業の課題を深く理解し、それに対する最適なデジタルソリューションを提供することで、企業が持続的な成長とイノベーションを達成できるようサポートします。
オンライン講座
製造業、主に購買・調達部門にお勤めの方々に向けた情報を配信しております。
新任の方やベテランの方、管理職を対象とした幅広いコンテンツをご用意しております。
お問い合わせ
コストダウンが利益に直結する術だと理解していても、なかなか前に進めることができない状況。そんな時は、newjiのコストダウン自動化機能で大きく利益貢献しよう!
(Β版非公開)