- お役立ち記事
- Elevating Excellence: Strategies for Quality Improvement in Japanese Manufacturing
月間76,176名の
製造業ご担当者様が閲覧しています*
*2025年3月31日現在のGoogle Analyticsのデータより
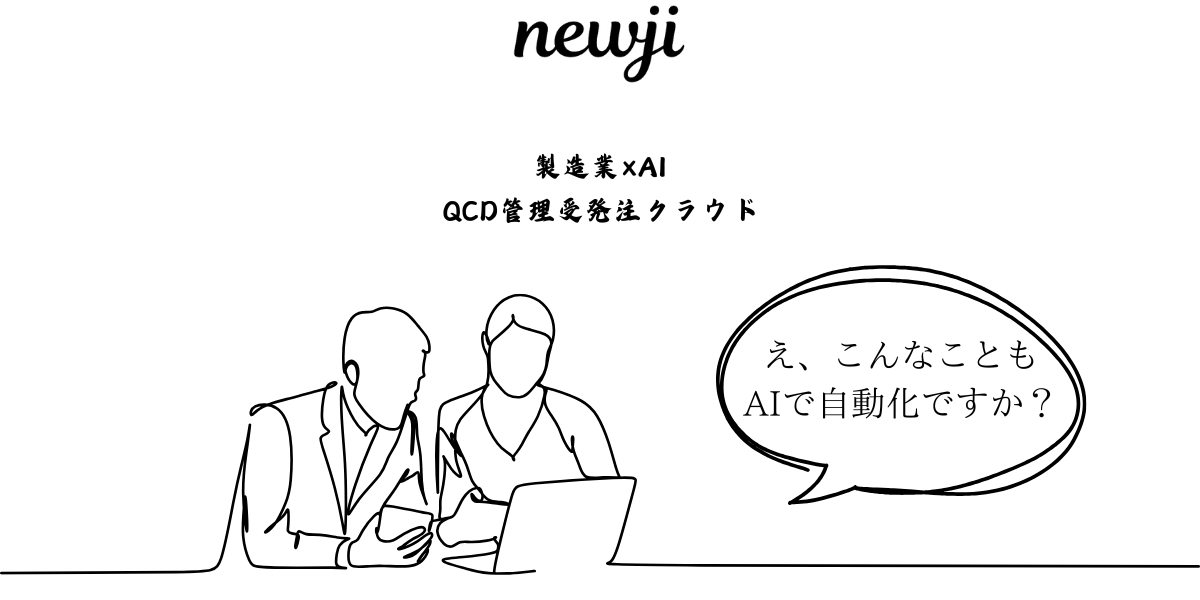
Elevating Excellence: Strategies for Quality Improvement in Japanese Manufacturing
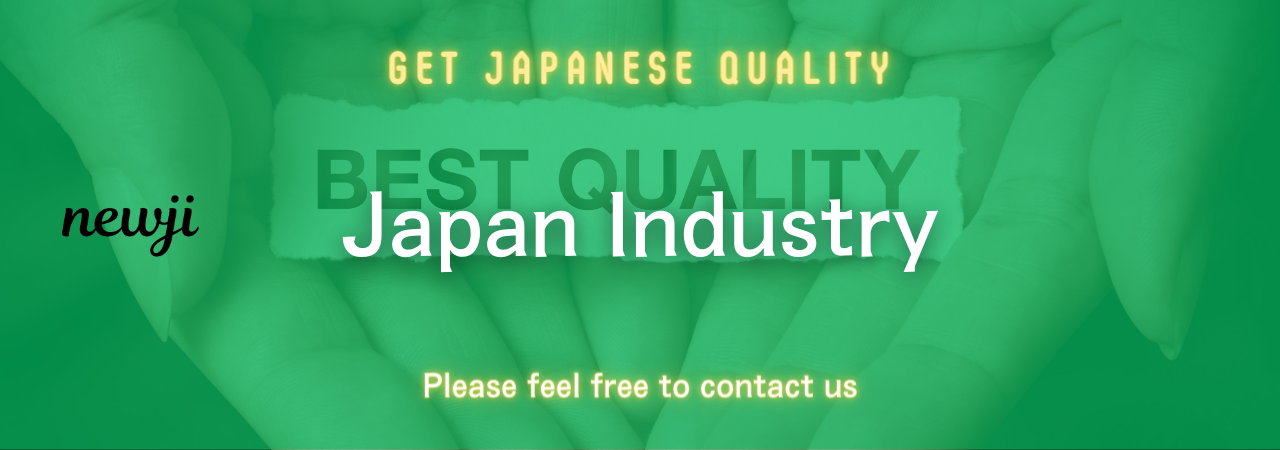
目次
Understanding Japanese Manufacturing Excellence
Japanese manufacturing has long been synonymous with quality, innovation, and efficiency.
The roots of this excellence can be traced back to post-war reconstruction, where Japan focused on rebuilding its industrial base with a strong emphasis on quality control and continuous improvement.
Today, Japanese manufacturers continue to set global standards, influencing industries worldwide through their commitment to superior craftsmanship and advanced technologies.
The Legacy of Quality in Japanese Manufacturing
The legacy of quality in Japanese manufacturing is built upon decades of dedication to precision and reliability.
Post-World War II, Japan sought to regain its economic footing by focusing on high-quality production.
This commitment led to the development of renowned methodologies such as Total Quality Management (TQM), Kaizen, and Just-In-Time (JIT) production.
These practices not only improved product quality but also enhanced operational efficiency, enabling Japanese companies to compete fiercely on the global stage.
Key Principles of Japanese Manufacturing
Several key principles underpin Japanese manufacturing excellence.
Firstly, there is a strong emphasis on continuous improvement, known as Kaizen, which encourages incremental enhancements in processes and products.
Secondly, the focus on eliminating waste through Lean manufacturing principles ensures resources are used efficiently.
Thirdly, a culture of respect and collaboration fosters strong relationships between employees, management, and suppliers.
Lastly, a commitment to innovation drives the adoption of advanced technologies and the development of cutting-edge products.
Strategies for Quality Improvement
Japanese manufacturers employ a variety of strategies to maintain and improve quality.
These strategies are integrated into every aspect of the manufacturing process, from initial design to final production.
By focusing on continuous improvement, waste reduction, and data-driven decision-making, Japanese companies consistently deliver high-quality products that meet and exceed customer expectations.
Kaizen: Continuous Improvement
Kaizen, meaning “change for the better,” is a cornerstone of Japanese manufacturing.
This philosophy encourages all employees to contribute ideas for improving processes and products regularly.
By fostering a culture of constant, incremental improvements, companies can enhance efficiency, reduce costs, and increase product quality.
Kaizen empowers employees at all levels to take ownership of quality, ensuring that improvements are sustainable and deeply embedded in the organizational culture.
Lean Manufacturing Principles
Lean manufacturing focuses on maximizing value while minimizing waste.
Japanese manufacturers implement Lean principles to streamline operations, reduce unnecessary processes, and optimize resource utilization.
Key Lean tools include value stream mapping, 5S workplace organization, and Just-In-Time (JIT) production.
By eliminating wasteful practices, companies can enhance productivity, lower costs, and maintain high-quality standards.
Six Sigma Implementation
Six Sigma is a data-driven methodology aimed at reducing defects and variability in processes.
By applying Six Sigma techniques, Japanese manufacturers can identify and eliminate sources of error, ensuring consistent product quality.
Six Sigma projects typically follow the DMAIC framework: Define, Measure, Analyze, Improve, and Control.
This structured approach allows companies to systematically address quality issues and achieve substantial performance improvements.
Procurement and Purchasing in Japanese Manufacturing
Effective procurement and purchasing strategies are vital for maintaining the high quality of Japanese manufacturing.
These strategies involve selecting the right suppliers, building strong relationships, and negotiating favorable terms.
By optimizing the supply chain, Japanese manufacturers can ensure the timely delivery of high-quality materials and components, supporting overall production excellence.
Building Strong Supplier Relationships
Building strong, long-term relationships with suppliers is a fundamental aspect of Japanese manufacturing.
Japanese companies often invest significant time and resources in selecting and developing suppliers who can meet their stringent quality standards.
Trust and mutual respect are essential, as suppliers are seen as partners rather than merely vendors.
This collaborative approach fosters open communication, joint problem-solving, and shared commitment to quality improvement.
Supplier Selection and Evaluation
The process of selecting and evaluating suppliers is critical for ensuring the consistency and reliability of materials and components.
Japanese manufacturers typically employ rigorous criteria, including quality certifications, production capabilities, financial stability, and compatibility with company values.
Regular audits and performance assessments help maintain high standards and identify areas for improvement.
By systematically evaluating suppliers, companies can mitigate risks and ensure a steady supply of quality inputs.
Negotiation Techniques with Japanese Suppliers
Negotiating with Japanese suppliers requires an understanding of cultural nuances and business practices.
Emphasis is placed on building rapport and establishing trust before discussing terms.
Negotiations are often conducted with a long-term perspective, focusing on mutual benefits and collaborative growth.
Key techniques include listening carefully, demonstrating respect, being patient, and seeking win-win solutions.
This approach fosters strong partnerships that contribute to sustained quality and operational success.
Advantages of Japanese Manufacturing
Japanese manufacturing offers numerous advantages that contribute to its global reputation for excellence.
These advantages stem from a combination of cultural values, advanced technologies, and efficient processes.
By leveraging these strengths, Japanese companies can consistently deliver high-quality products and maintain a competitive edge in various industries.
High-Quality Standards
One of the primary advantages of Japanese manufacturing is its unwavering commitment to high-quality standards.
From meticulous attention to detail in product design to rigorous quality control measures in production, Japanese companies prioritize excellence at every stage.
This dedication results in products that are reliable, durable, and meet or exceed customer expectations.
High-quality standards not only enhance brand reputation but also drive customer loyalty and long-term business success.
Advanced Technology and Automation
Japanese manufacturers are at the forefront of adopting and developing advanced technologies and automation.
Robotics, artificial intelligence, and Industry 4.0 innovations are integral to modern Japanese factories.
These technologies enhance precision, increase production speed, and reduce the likelihood of errors.
Automation also allows for greater flexibility in manufacturing processes, enabling companies to swiftly adapt to changing market demands and maintain consistent quality.
Efficiency and Waste Reduction
Efficiency and waste reduction are central to Japanese manufacturing practices.
Techniques like Lean manufacturing and Just-In-Time (JIT) production help minimize resource consumption and eliminate non-value-added activities.
By streamlining operations and optimizing workflows, Japanese companies achieve higher productivity and lower operational costs.
This focus on efficiency not only contributes to financial performance but also supports sustainability efforts by reducing environmental impact.
Disadvantages of Japanese Manufacturing
While Japanese manufacturing boasts numerous strengths, it also faces certain disadvantages.
These challenges can impact competitiveness and operational efficiency if not adequately addressed.
Understanding these potential drawbacks is essential for companies seeking to engage with Japanese manufacturers or implement similar practices.
Higher Costs
One of the notable disadvantages of Japanese manufacturing is the higher cost structure.
The emphasis on quality, advanced technologies, and skilled labor often results in increased production costs.
These higher costs can make Japanese products less price-competitive in certain markets, especially against lower-cost producers from other regions.
However, the value derived from superior quality and reliability often justifies the premium for many customers.
Cultural and Communication Barriers
Cultural and communication barriers can pose significant challenges in international business relationships with Japanese manufacturers.
Differences in business etiquette, language, and management styles may lead to misunderstandings and inefficiencies.
These barriers can complicate negotiations, project management, and day-to-day operations.
Overcoming these challenges requires cultural sensitivity, effective communication strategies, and sometimes the assistance of bilingual or culturally knowledgeable intermediaries.
Supply Chain Disruptions
Japanese manufacturing is highly integrated into global supply chains, making it susceptible to disruptions.
Natural disasters, geopolitical tensions, and global pandemics can significantly impact supply chain reliability.
These disruptions can lead to delays, increased costs, and challenges in maintaining consistent product quality.
Diversifying supply sources and enhancing supply chain resilience are critical measures to mitigate these risks.
Market Conditions Affecting Japanese Manufacturing
The dynamic global market conditions greatly influence Japanese manufacturing.
Factors such as rising competition, economic fluctuations, and technological advancements shape the industry’s landscape.
Japanese manufacturers must continuously adapt to these changes to sustain their competitive advantage and drive ongoing quality improvements.
Global Competition
Japanese manufacturers face intense competition from both established and emerging markets.
Countries like China, South Korea, and Germany offer strong alternatives in various sectors, often at competitive prices.
To maintain their edge, Japanese companies emphasize innovation, superior quality, and efficient production methods.
Staying ahead of competitors requires continuous investment in research and development and the ability to swiftly respond to market changes.
Economic Factors
Global economic conditions, including exchange rates, trade policies, and economic growth rates, significantly impact Japanese manufacturing.
Fluctuations in the yen can affect the cost competitiveness of Japanese products in international markets.
Trade policies and tariffs can influence market access and profitability.
Economic downturns may lead to reduced consumer demand, necessitating adjustments in production and strategic planning to navigate challenging times.
Technological Advancements
Rapid technological advancements present both opportunities and challenges for Japanese manufacturers.
Staying at the forefront of innovation is essential to maintain competitiveness and meet evolving customer needs.
Adopting new technologies like artificial intelligence, the Internet of Things (IoT), and advanced robotics can enhance production capabilities and product features.
However, integrating these technologies requires significant investment and the development of new skill sets within the workforce.
Best Practices for Quality Improvement
Implementing best practices is crucial for Japanese manufacturers aiming to sustain and enhance their quality standards.
These practices encompass comprehensive quality management systems, employee engagement, and the effective use of data analytics.
By adopting these strategies, companies can achieve continuous improvement and maintain their leadership in manufacturing excellence.
Implementing Total Quality Management (TQM)
Total Quality Management (TQM) is a holistic approach to long-term success through customer satisfaction.
TQM involves all members of an organization in improving processes, products, services, and the culture in which they work.
Japanese manufacturers utilize TQM to foster a quality-centric environment where continuous improvement is ingrained in daily operations.
Key components of TQM include leadership commitment, employee involvement, process-centered approaches, and strategic planning focused on quality objectives.
Employee Training and Involvement
Employee training and involvement are essential for sustaining high-quality manufacturing.
Japanese companies invest in comprehensive training programs to equip employees with the necessary skills and knowledge.
Encouraging employee involvement in decision-making processes and quality improvement initiatives empowers workers and fosters a sense of ownership.
By cultivating a motivated and skilled workforce, companies can enhance productivity, reduce errors, and drive innovation.
Utilizing Advanced Analytics and Data-Driven Decision Making
Advanced analytics and data-driven decision-making play a pivotal role in quality improvement.
Japanese manufacturers leverage big data, machine learning, and predictive analytics to gain insights into production processes and identify areas for improvement.
Data-driven approaches enable precise monitoring of quality metrics, early detection of potential issues, and informed decision-making.
By utilizing advanced analytics, companies can optimize operations, enhance product quality, and achieve greater operational efficiency.
Conclusion
Japanese manufacturing continues to set benchmarks for quality, efficiency, and innovation on the global stage.
Through the implementation of strategies like Kaizen, Lean manufacturing, and Six Sigma, companies maintain their commitment to excellence.
Effective procurement and purchasing practices, coupled with strong supplier relationships, ensure the consistent delivery of high-quality materials and components.
While challenges such as higher costs and cultural barriers exist, the advantages of Japanese manufacturing—such as superior quality standards and advanced technology—remain significant.
By embracing best practices and adapting to dynamic market conditions, Japanese manufacturers can sustain their leadership in quality improvement and continue to thrive in a competitive international landscape.
資料ダウンロード
QCD管理受発注クラウド「newji」は、受発注部門で必要なQCD管理全てを備えた、現場特化型兼クラウド型の今世紀最高の受発注管理システムとなります。
ユーザー登録
受発注業務の効率化だけでなく、システムを導入することで、コスト削減や製品・資材のステータス可視化のほか、属人化していた受発注情報の共有化による内部不正防止や統制にも役立ちます。
NEWJI DX
製造業に特化したデジタルトランスフォーメーション(DX)の実現を目指す請負開発型のコンサルティングサービスです。AI、iPaaS、および先端の技術を駆使して、製造プロセスの効率化、業務効率化、チームワーク強化、コスト削減、品質向上を実現します。このサービスは、製造業の課題を深く理解し、それに対する最適なデジタルソリューションを提供することで、企業が持続的な成長とイノベーションを達成できるようサポートします。
製造業ニュース解説
製造業、主に購買・調達部門にお勤めの方々に向けた情報を配信しております。
新任の方やベテランの方、管理職を対象とした幅広いコンテンツをご用意しております。
お問い合わせ
コストダウンが利益に直結する術だと理解していても、なかなか前に進めることができない状況。そんな時は、newjiのコストダウン自動化機能で大きく利益貢献しよう!
(β版非公開)