- お役立ち記事
- Eliminate waste and improve productivity through thorough 5S activities at manufacturing sites
月間76,176名の
製造業ご担当者様が閲覧しています*
*2025年3月31日現在のGoogle Analyticsのデータより
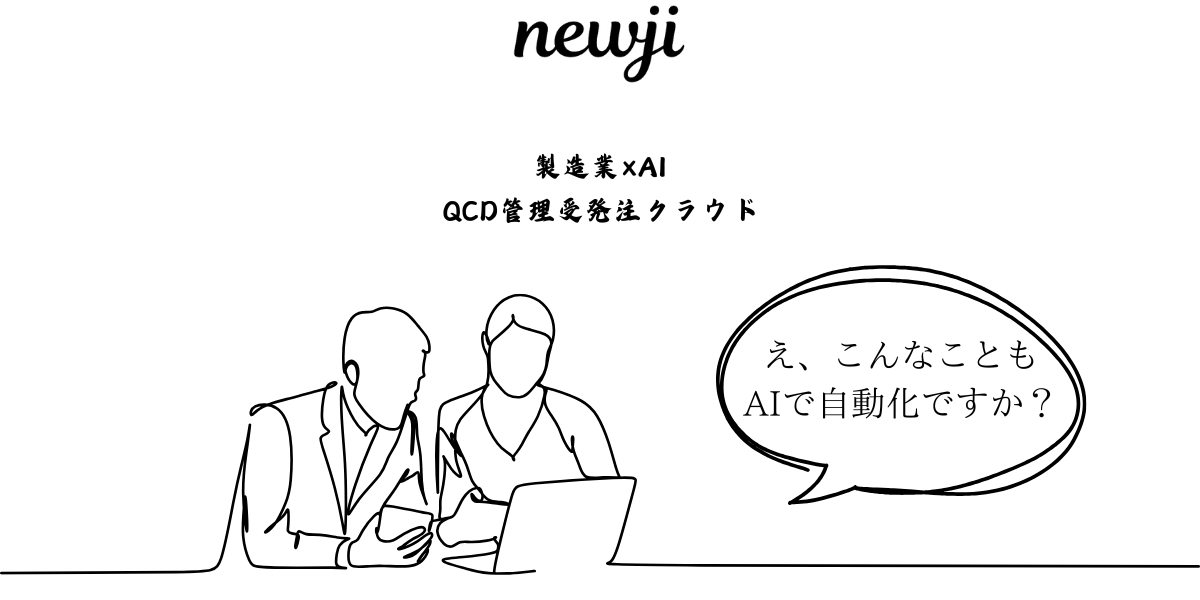
Eliminate waste and improve productivity through thorough 5S activities at manufacturing sites
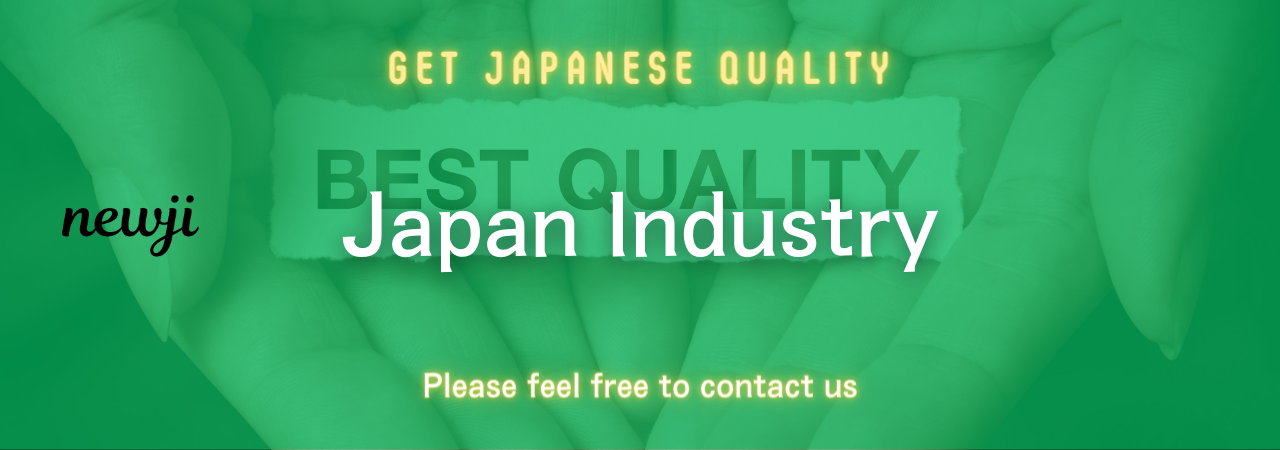
To improve productivity and eliminate waste at manufacturing sites, many companies turn to the powerful methodology known as 5S. This approach is designed to create a clean, organized, and efficient workplace, which in turn leads to higher levels of productivity and reduced waste. So, what exactly is 5S and how can it help your manufacturing site flourish? Let’s dive in.
What is 5S?
The term 5S stands for five Japanese words that have been translated into English to describe a specific set of practices:
1. **Sort (Seiri)**: Separate needed items from unnecessary ones and remove the latter.
2. **Set in Order (Seiton)**: Arrange necessary items so they are ready and easy to use.
3. **Shine (Seiso)**: Clean the workplace and equipment regularly to maintain standards and identify defects.
4. **Standardize (Seiketsu)**: Establish standards for performing tasks consistently and correctly.
5. **Sustain (Shitsuke)**: Maintain and review standards through regular audits and continuous improvement.
Step 1: Sort (Seiri)
The first step in 5S involves evaluating what items are necessary for the job and removing anything that isn’t. This is crucial in identifying clutter and reducing the time workers spend looking for tools or materials. Start by:
– Conducting an inventory check to distinguish between essential and non-essential items.
– Using tags to mark items that are seldom used or potentially redundant.
– Creating a ‘red tag’ area where non-essential items are placed temporarily before deciding whether to dispose of them.
By sorting through items methodically, you can streamline operations and make it easier for workers to find the tools and materials they need quickly.
Step 2: Set in Order (Seiton)
After removing unnecessary items, it’s essential to organize the remaining tools and materials properly. This step ensures that everything has a designated place and is easily accessible. To achieve this, you can:
– Use shadow boards to outline where tools should be placed.
– Implement labeling systems for shelves, storage spaces, and bins.
– Develop a workflow layout that minimizes unnecessary movement and optimizes the production process.
Proper organization not only saves time but also reduces the mental load on workers, allowing them to focus on their tasks more efficiently.
Step 3: Shine (Seiso)
A clean workspace is pivotal to maintaining efficiency and identifying potential issues before they become problems. Regular cleaning helps you notice wear and tear on equipment, leaks, and other signs of trouble that could lead to downtime. Recommendations for shining include:
– Scheduling regular cleaning routines and making it part of the daily work schedule.
– Assigning specific cleaning tasks to different team members to ensure accountability.
– Using cleaning checklists to ensure no areas are overlooked.
By maintaining a spotless environment, you not only boost morale but also extend the lifespan of your equipment, contributing to long-term productivity gains.
Step 4: Standardize (Seiketsu)
Standardization is key to ensuring that cleanliness and orderliness become company habits rather than one-time actions. This step involves creating clear, standardized procedures for each task so everyone knows the best way to perform it. You can standardize by:
– Developing written procedures and visual guides for tasks.
– Implementing regular training sessions to keep everyone up-to-date on best practices.
– Using visual management techniques, such as color-coding and signage, to help staff follow the standards.
With standardized procedures in place, consistency and quality are significantly improved, reducing variation and errors in the production process.
Step 5: Sustain (Shitsuke)
The final step ensures that the 5S culture is sustained over the long term. To sustain the improvements made, it’s crucial to:
– Conduct regular audits and check-ups to ensure compliance with the established standards.
– Encourage a culture of continuous improvement, where employees are motivated to suggest new ways to enhance productivity and reduce waste.
– Celebrate milestones and achievements related to 5S to keep employees engaged and invested in the process.
Sustaining the 5S effort guarantees that the benefits are not short-lived and that your manufacturing site remains productive and efficient over time.
Benefits of Implementing 5S
Implementing 5S offers several tangible and intangible benefits that contribute to the efficiency and success of manufacturing operations:
1. **Increased Productivity**: Through better organization and standardization, workers can complete their tasks more quickly and accurately.
2. **Reduced Waste**: Identifying and eliminating unnecessary items, processes, and inefficiencies help reduce overall waste.
3. **Improved Safety**: Clean and well-ordered workspaces are safer, reducing the risk of accidents and injuries.
4. **Higher Employee Morale**: A well-organized and clean workplace boosts employee morale and satisfaction.
5. **Better Use of Space**: By clearing out unnecessary items and organizing spaces efficiently, you can make better use of the available space.
Practical Examples of 5S in Action
To illustrate how 5S can be implemented, let’s consider a couple of practical examples at manufacturing sites:
1. **Assembly Line Optimization**:
– *Sort*: Remove outdated tools and parts that are no longer part of the current production requirements.
– *Set in Order*: Arrange tools and parts in the order they are used during the assembly process.
– *Shine*: Implement a cleaning schedule to ensure the assembly line is free from dirt and debris.
– *Standardize*: Create assembly line procedures and install visual cues like color-coded floor markings.
– *Sustain*: Regularly audit the assembly line procedures and hold team meetings to discuss potential improvements.
2. **Tool Room Management**:
– *Sort*: Conduct an inventory to remove unused or obsolete tools.
– *Set in Order*: Organize tools based on frequency of use and functionality.
– *Shine*: Establish a routine for cleaning and inspecting tools.
– *Standardize*: Develop a checkout system for tools and provide clear labels and designated places for each tool.
– *Sustain*: Perform regular reviews of the tool room system and encourage feedback for continuous improvement.
Conclusion
Implementing a thorough 5S program at your manufacturing site is a tried-and-true method for enhancing productivity and eliminating waste. By following the steps of Sort, Set in Order, Shine, Standardize, and Sustain, you can create a more efficient, safer, and pleasant working environment. This not only benefits your bottom line but also contributes to a more positive and engaging workplace culture. With consistent application and ongoing commitment, the principles of 5S can have a lasting, transformative impact on your manufacturing operations.
資料ダウンロード
QCD管理受発注クラウド「newji」は、受発注部門で必要なQCD管理全てを備えた、現場特化型兼クラウド型の今世紀最高の受発注管理システムとなります。
ユーザー登録
受発注業務の効率化だけでなく、システムを導入することで、コスト削減や製品・資材のステータス可視化のほか、属人化していた受発注情報の共有化による内部不正防止や統制にも役立ちます。
NEWJI DX
製造業に特化したデジタルトランスフォーメーション(DX)の実現を目指す請負開発型のコンサルティングサービスです。AI、iPaaS、および先端の技術を駆使して、製造プロセスの効率化、業務効率化、チームワーク強化、コスト削減、品質向上を実現します。このサービスは、製造業の課題を深く理解し、それに対する最適なデジタルソリューションを提供することで、企業が持続的な成長とイノベーションを達成できるようサポートします。
製造業ニュース解説
製造業、主に購買・調達部門にお勤めの方々に向けた情報を配信しております。
新任の方やベテランの方、管理職を対象とした幅広いコンテンツをご用意しております。
お問い合わせ
コストダウンが利益に直結する術だと理解していても、なかなか前に進めることができない状況。そんな時は、newjiのコストダウン自動化機能で大きく利益貢献しよう!
(β版非公開)