- お役立ち記事
- “Eliminating defective products” activities that the quality control department should carry out—to meet demands from management
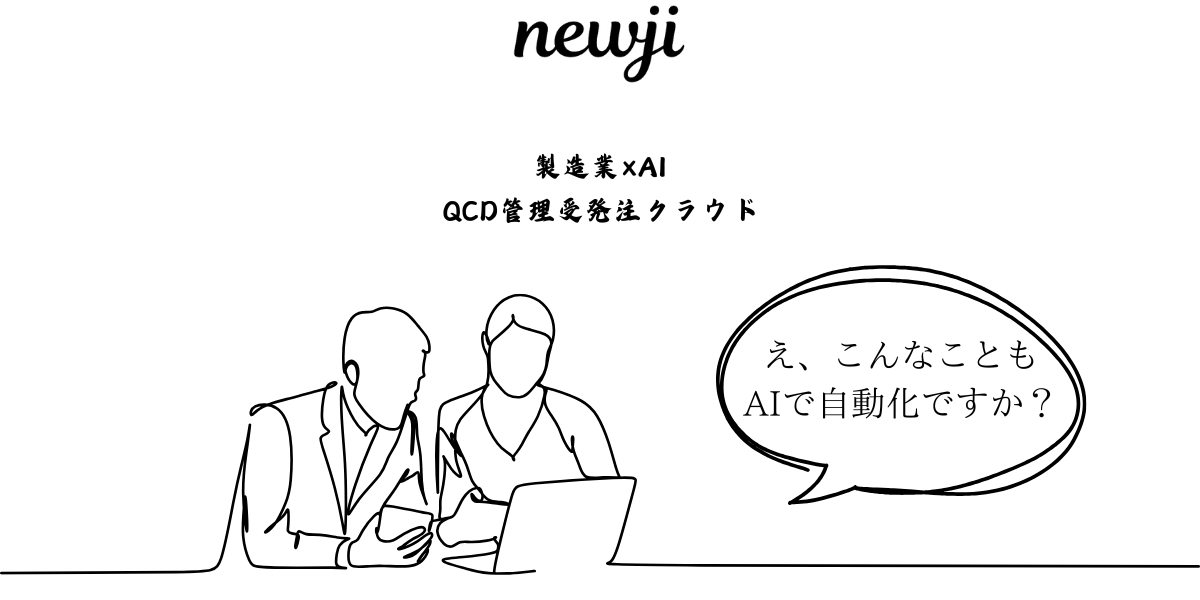
“Eliminating defective products” activities that the quality control department should carry out—to meet demands from management
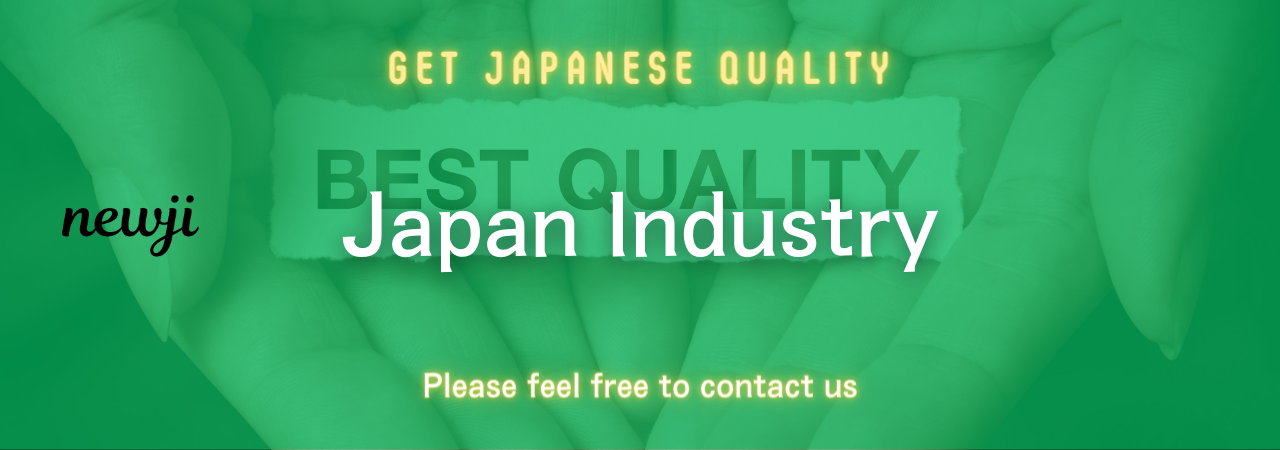
目次
Understanding the Importance of Eliminating Defective Products
In today’s competitive market, ensuring that products meet a high standard of quality is paramount for business success.
Eliminating defective products not only enhances customer satisfaction but also drives profitability.
The responsibility for maintaining this standard often falls on the quality control department.
These departments must implement effective strategies to meet the demands set forth by management and ensure products that reach customers are nothing but the best.
Identifying the Root Cause of Defects
The first step in eliminating defective products is identifying their root causes.
Without understanding what’s causing the defects, it’s challenging to eliminate them.
Quality control departments should conduct thorough root cause analyses whenever a defect is identified.
This involves investigating production processes, material quality, machinery maintenance, and even supplier performance.
Using tools like the Fishbone Diagram or the Five Whys can help uncover underlying issues that lead to defects.
Data Collection and Analysis
Collecting accurate data is essential for successful root cause analysis.
Quality control teams should gather data on every aspect of the production process, including input materials, machinery used, environmental conditions, and human involvement.
Once collected, analyzing this data can reveal patterns and trends that point to the sources of defects.
Powerful analytics tools can help teams visualize data and make informed decisions about necessary changes in the process.
Implementing Quality Management Systems
Quality Management Systems (QMS) are instrumental in reducing defects.
A QMS lays down a structured framework for consistent quality control throughout the production lifecycle.
Implementations such as ISO 9001 can help streamline processes and set benchmarks for quality that meet industry standards.
Having a robust QMS in place ensures that every team member understands their role in maintaining quality standards and that procedures are regularly audited and updated.
Standard Operating Procedures (SOPs)
Developing and adhering to Standard Operating Procedures is another critical element in maintaining product quality.
SOPs offer clear instructions and guidelines on how tasks should be performed to minimize deviation and potential for error.
Regular training sessions can help ensure that employees are well-versed in these procedures, reducing the likelihood of defects caused by human error.
Emphasizing Continuous Improvement
Eliminating defects is not a one-time task, but a continuous commitment to improvement.
Quality control departments should embrace methodologies such as Lean and Six Sigma, which focus on ongoing improvement and waste reduction.
Continuous improvement encourages teams to regularly assess and refine their processes, thus minimizing the chance of defects over time.
Employee Training and Engagement
To effectively implement continuous improvement, employee training and engagement are crucial.
Empowering employees with the skills and knowledge they need to identify potential defects and suggest improvements can lead to significant quality enhancements.
Involving frontline employees in quality circles or improvement teams can also foster a culture of ownership and accountability towards product quality.
Utilizing Advanced Technology and Automation
Leveraging advanced technology and automation can significantly reduce the incidence of defects.
The integration of Artificial Intelligence (AI) and Machine Learning (ML) in production lines can improve accuracy, speed, and consistency.
These technologies can predict and detect defects early on, preventing faulty products from being shipped.
Additionally, automation of repetitive or complex tasks can minimize human error and ensure more consistent results.
Implementing Real-Time Monitoring
Real-time monitoring systems monitor production processes continuously to detect and correct any anomalies instantly.
Such systems can provide quality control departments with immediate feedback on the performance of machinery and processes.
With real-time alerts and data, teams can make timely adjustments to prevent defects and maintain product quality consistently.
Focusing on Supplier Quality Management
The quality of input materials has a direct impact on the final product’s quality.
Establishing strong Supplier Quality Management ensures that the materials and components sourced meet the necessary quality standards.
Quality control departments must work closely with suppliers to establish clear quality expectations and conduct regular audits.
Building strong relationships with suppliers can also facilitate more effective communication and swift resolution of any quality issues.
Supplier Audits and Evaluations
Regular supplier audits and evaluations are essential in maintaining quality standards across the supply chain.
By assessing a supplier’s capacity to deliver quality materials, quality control departments can mitigate the risk of defects from the outset.
Vendor rating systems, based on past performance and quality metrics, can help identify reliable suppliers and cultivate long-term partnerships that support high-quality output.
Conclusion
The journey towards eliminating defective products is ongoing and requires a multifaceted approach.
Quality control departments play a vital role in implementing effective strategies and systems to ensure the consistent high quality of products.
By focusing on root cause analysis, adopting quality management frameworks, leveraging advanced technology, and engaging both employees and suppliers, companies can successfully minimize defects, satisfy management demands, and thrive in the competitive marketplace.
資料ダウンロード
QCD調達購買管理クラウド「newji」は、調達購買部門で必要なQCD管理全てを備えた、現場特化型兼クラウド型の今世紀最高の購買管理システムとなります。
ユーザー登録
調達購買業務の効率化だけでなく、システムを導入することで、コスト削減や製品・資材のステータス可視化のほか、属人化していた購買情報の共有化による内部不正防止や統制にも役立ちます。
NEWJI DX
製造業に特化したデジタルトランスフォーメーション(DX)の実現を目指す請負開発型のコンサルティングサービスです。AI、iPaaS、および先端の技術を駆使して、製造プロセスの効率化、業務効率化、チームワーク強化、コスト削減、品質向上を実現します。このサービスは、製造業の課題を深く理解し、それに対する最適なデジタルソリューションを提供することで、企業が持続的な成長とイノベーションを達成できるようサポートします。
オンライン講座
製造業、主に購買・調達部門にお勤めの方々に向けた情報を配信しております。
新任の方やベテランの方、管理職を対象とした幅広いコンテンツをご用意しております。
お問い合わせ
コストダウンが利益に直結する術だと理解していても、なかなか前に進めることができない状況。そんな時は、newjiのコストダウン自動化機能で大きく利益貢献しよう!
(Β版非公開)