- お役立ち記事
- Embracing Risk-Based Thinking: How Japanese Manufacturing Leads the Way in Innovative Production Strategies
月間76,176名の
製造業ご担当者様が閲覧しています*
*2025年3月31日現在のGoogle Analyticsのデータより
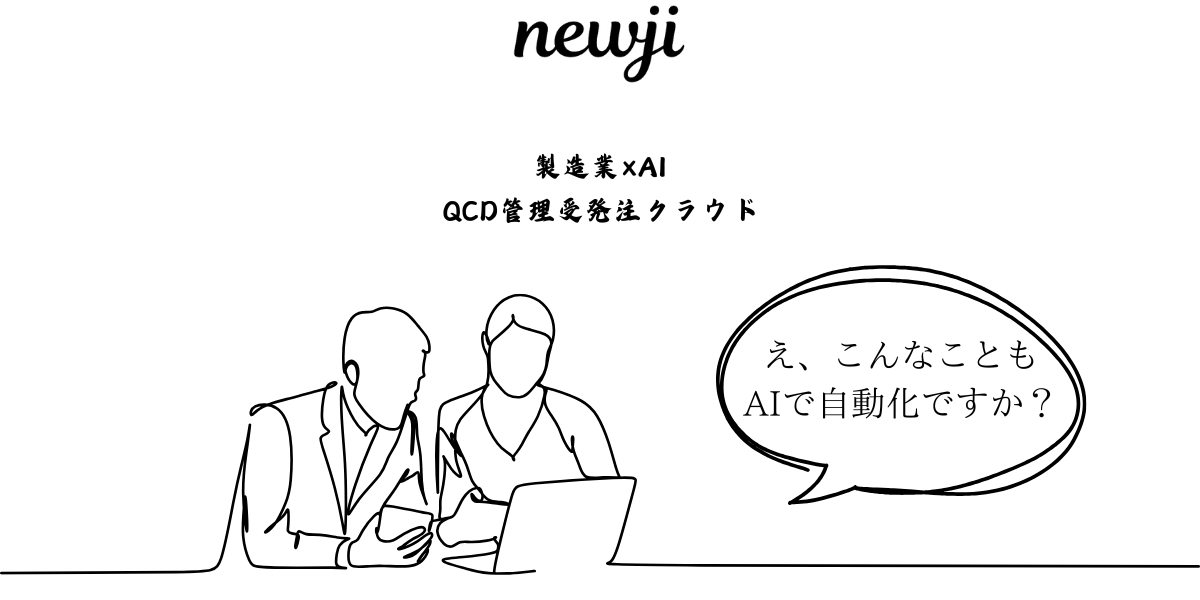
Embracing Risk-Based Thinking: How Japanese Manufacturing Leads the Way in Innovative Production Strategies
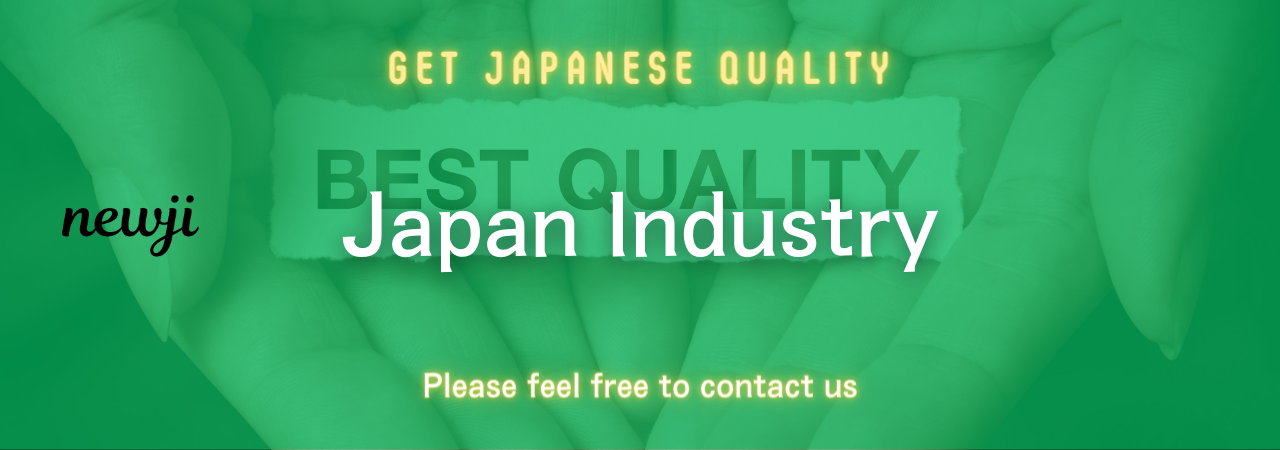
目次
Introduction to Risk-Based Thinking in Japanese Manufacturing
Risk-based thinking has become a cornerstone of modern manufacturing strategies, enabling companies to anticipate challenges and innovate effectively. Japanese manufacturing, renowned for its precision and efficiency, has been at the forefront of integrating risk-based thinking into its production processes. This approach not only enhances operational resilience but also drives continuous improvement and innovation.
The Foundations of Risk-Based Thinking in Japanese Manufacturing
Philosophical Underpinnings
Japanese manufacturing is deeply rooted in principles such as Kaizen, which emphasizes continuous improvement, and Just-In-Time (JIT) production, which focuses on reducing waste and improving efficiency. Risk-based thinking complements these philosophies by systematically identifying and mitigating risks that could hinder these processes.
Integration into Quality Management Systems
Japanese companies often incorporate risk-based thinking into their Quality Management Systems (QMS). This integration ensures that quality is maintained not just reactively but proactively by anticipating potential issues and addressing them before they escalate.
Advantages of Risk-Based Thinking in Procurement and Purchasing
Enhanced Supplier Relationships
By adopting risk-based thinking, Japanese manufacturers can assess the reliability and stability of their suppliers. This leads to stronger, more strategic partnerships, as suppliers are selected based on their ability to consistently meet quality and delivery standards.
Improved Supply Chain Resilience
Risk-based approaches help in identifying vulnerabilities within the supply chain. This enables companies to develop contingency plans, diversify their supplier base, and reduce dependency on single sources, thereby enhancing overall supply chain resilience.
Cost Efficiency
Proactively managing risks can prevent costly disruptions and quality issues. Japanese manufacturers often achieve significant cost savings by avoiding delays, reducing waste, and minimizing the need for rework through effective risk management.
Challenges and Disadvantages
Cultural Barriers
Implementing risk-based thinking can be challenging in organizations with deeply ingrained traditional practices. Japanese companies, however, have successfully navigated these challenges by fostering a culture that values continuous improvement and proactive problem-solving.
Resource Intensive
Risk assessment and management require dedicated resources and expertise. Small and medium-sized enterprises (SMEs) may find it difficult to allocate sufficient resources, although the long-term benefits often justify the initial investment.
Complexity in Implementation
Integrating risk-based thinking into existing processes can be complex. It requires a thorough understanding of both manufacturing operations and potential risk factors. Japanese companies typically address this through comprehensive training and the use of advanced risk management tools.
Supplier Negotiation Techniques
Collaborative Negotiation
Japanese manufacturers prefer a collaborative approach to supplier negotiations. By working together with suppliers to identify and mitigate risks, both parties can achieve mutually beneficial outcomes, fostering long-term partnerships.
Transparency and Communication
Open communication is essential in risk-based negotiations. Sharing relevant information about potential risks and expectations helps build trust and ensures that both parties are aligned in their risk management strategies.
Performance-Based Contracts
Contracts are often structured to include performance-based incentives. This encourages suppliers to maintain high standards and continuously improve their processes to meet agreed-upon risk mitigation measures.
Market Conditions and Their Impact
Global Supply Chain Dynamics
Globalization has introduced both opportunities and challenges for Japanese manufacturers. Risk-based thinking allows companies to navigate complex international supply chains by identifying geopolitical, economic, and environmental risks that could impact operations.
Technological Advancements
The rapid pace of technological change requires manufacturers to stay ahead of potential risks associated with new technologies. Japanese companies leverage risk-based thinking to assess the feasibility and impact of adopting new technologies, ensuring seamless integration into existing systems.
Regulatory Environment
Compliance with international and local regulations is critical. Risk-based approaches help manufacturers anticipate regulatory changes and adjust their processes accordingly, reducing the risk of non-compliance and associated penalties.
Best Practices in Implementing Risk-Based Thinking
Comprehensive Risk Assessment
A thorough risk assessment involves identifying potential risks, evaluating their likelihood and impact, and prioritizing them based on their significance. Japanese manufacturers utilize advanced analytical tools to conduct detailed risk assessments, ensuring no critical risk is overlooked.
Continuous Monitoring and Review
Risk management is an ongoing process. Continuous monitoring allows companies to track risk indicators and make timely adjustments to their risk mitigation strategies. Regular reviews ensure that risk management practices evolve in line with changing market conditions and organizational goals.
Employee Training and Engagement
Educating employees about risk-based thinking and involving them in the risk management process fosters a proactive culture. Japanese companies invest in training programs that equip their workforce with the skills and knowledge needed to identify and manage risks effectively.
Case Studies: Japanese Manufacturing Success Stories
Toyota’s Approach to Risk Management
Toyota is a prime example of how risk-based thinking can drive manufacturing excellence. By implementing the Toyota Production System (TPS), the company has successfully minimized risks related to inventory management, production delays, and quality control. Toyota’s focus on continuous improvement and employee involvement has been instrumental in maintaining its reputation for reliability and efficiency.
Panasonic’s Supplier Collaboration
Panasonic has leveraged risk-based thinking to enhance its supplier relationships. By conducting regular risk assessments and collaborating closely with suppliers, Panasonic ensures that its supply chain remains robust and adaptable to changing market demands. This proactive approach has enabled Panasonic to maintain high standards of quality and consistency across its product range.
Future Trends in Risk-Based Manufacturing
Digital Transformation
The integration of digital technologies such as the Internet of Things (IoT), artificial intelligence (AI), and big data analytics is transforming risk management in manufacturing. These technologies provide real-time data and predictive insights, enabling more accurate risk assessments and faster decision-making.
Sustainability and Risk Management
Sustainability is becoming increasingly important in manufacturing. Risk-based thinking is essential for identifying and mitigating environmental risks, ensuring that manufacturing practices are not only efficient but also environmentally responsible. Japanese manufacturers are at the forefront of developing sustainable production strategies that balance profitability with ecological stewardship.
Global Collaboration
As manufacturing becomes more global, collaboration across borders is essential. Risk-based thinking facilitates better coordination and cooperation among international teams, allowing companies to manage risks that arise from diverse regulatory environments, cultural differences, and logistical challenges.
Conclusion
Risk-based thinking is integral to the continued success and innovation of Japanese manufacturing. By proactively identifying and managing risks, Japanese manufacturers enhance their operational resilience, foster strong supplier relationships, and drive continuous improvement. As the global manufacturing landscape evolves, the principles of risk-based thinking will remain essential for companies seeking to maintain competitiveness and achieve sustainable growth. Embracing these strategies not only ensures the mitigation of potential risks but also paves the way for groundbreaking innovations and long-term success.
資料ダウンロード
QCD管理受発注クラウド「newji」は、受発注部門で必要なQCD管理全てを備えた、現場特化型兼クラウド型の今世紀最高の受発注管理システムとなります。
ユーザー登録
受発注業務の効率化だけでなく、システムを導入することで、コスト削減や製品・資材のステータス可視化のほか、属人化していた受発注情報の共有化による内部不正防止や統制にも役立ちます。
NEWJI DX
製造業に特化したデジタルトランスフォーメーション(DX)の実現を目指す請負開発型のコンサルティングサービスです。AI、iPaaS、および先端の技術を駆使して、製造プロセスの効率化、業務効率化、チームワーク強化、コスト削減、品質向上を実現します。このサービスは、製造業の課題を深く理解し、それに対する最適なデジタルソリューションを提供することで、企業が持続的な成長とイノベーションを達成できるようサポートします。
製造業ニュース解説
製造業、主に購買・調達部門にお勤めの方々に向けた情報を配信しております。
新任の方やベテランの方、管理職を対象とした幅広いコンテンツをご用意しております。
お問い合わせ
コストダウンが利益に直結する術だと理解していても、なかなか前に進めることができない状況。そんな時は、newjiのコストダウン自動化機能で大きく利益貢献しよう!
(β版非公開)