- お役立ち記事
- End Effector Design Optimization for Industrial Robots
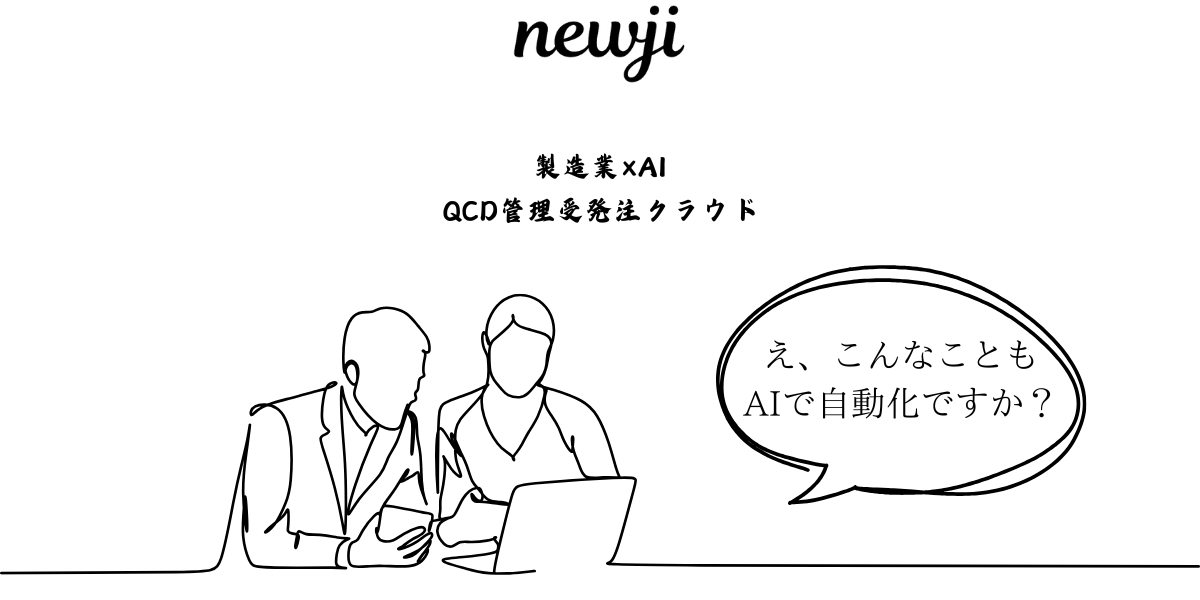
End Effector Design Optimization for Industrial Robots
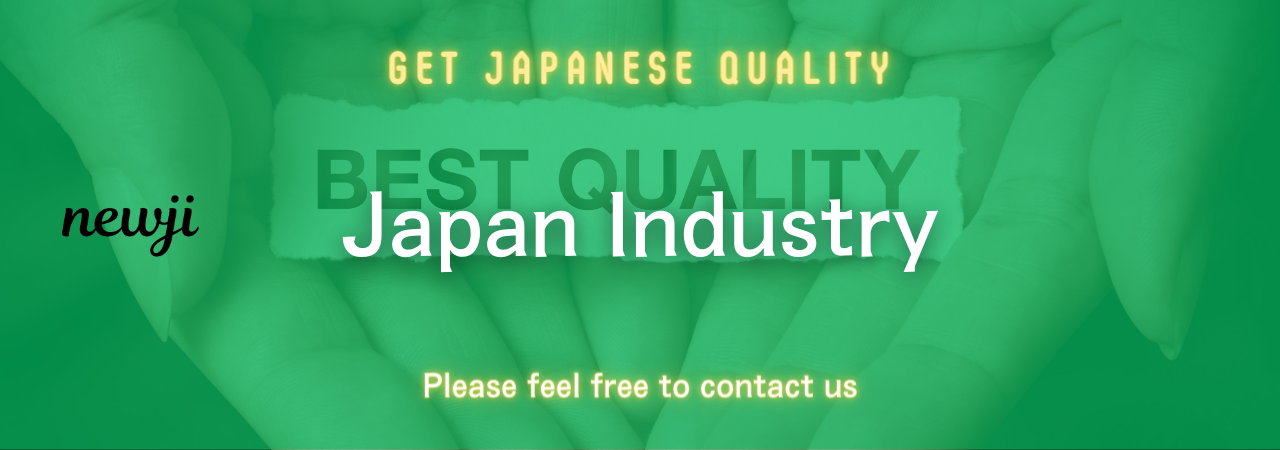
In the era of advanced manufacturing, industrial robots have become a crucial component in production lines across various industries. From automotive assembly to electronics manufacturing, these robots deliver unprecedented efficiency and precision. But for these robots to perform at their peak, the end effector design must be perfectly optimized. This article explores the significance of end effector design for industrial robots, techniques to achieve design optimization, and its benefits.
目次
Understanding End Effectors
End effectors are tools attached to the end of a robotic arm.
They interact with the environment to perform specific tasks like gripping, welding, painting, and more.
Each application has unique requirements, necessitating a tailored end effector design.
Innovative materials such as lightweight aluminum alloys and advanced composites are now used in the construction of end effectors.
The choice of material impacts the robot’s performance, from speed and dexterity to longevity and safety.
Additionally, sensors and actuators integrated into the end effector enhance its functionality, enabling precise control over complex tasks.
Key Aspects of End Effector Design
End effector design isn’t just about picking suitable materials and attaching tools.
Several key factors must be considered:
Weight and Size
The weight and size profoundly influence the robot’s operational efficiency.
A lighter end effector can enhance speed and reduce energy consumption.
However, it should be robust enough to withstand operational stress.
Flexibility and Adaptability
The end effector must be flexible enough to perform a range of tasks.
For example, a gripper designed to handle various objects will be more useful than one specialized for a single item.
In addition, the ability to easily swap out different end effectors can greatly expand a robot’s versatility.
Precision and Accuracy
In applications like electronics manufacturing, precision and accuracy are paramount.
The end effector must maintain a high level of repeatability, ensuring consistent quality in every task it performs.
Durability
Industrial environments can be harsh.
The end effector must be durable, able to function effectively under high temperatures, corrosive conditions, and heavy loads without significant wear and tear.
Techniques for Design Optimization
Design optimization involves several techniques to ensure the end effector performs its best.
Here are some effective methods:
Finite Element Analysis (FEA)
FEA involves using computer simulations to analyze the end effector’s response to various stress conditions.
It helps engineers identify weak points and optimize the design for maximum durability and efficiency.
Topology Optimization
This technique uses algorithms to determine the best material distribution within a given design space.
It aims to achieve the desired performance with minimal material use, resulting in lightweight and strong end effectors.
Virtual Prototyping
Before physical prototypes are made, virtual models allow engineers to test different designs quickly.
This saves time and resources by identifying potential issues early in the development process.
Iterative Design Process
An iterative design process involves creating multiple versions of the end effector and testing them to refine performance.
Feedback from each iteration guides improvements, ensuring the final design is highly optimized.
Benefits of Optimized End Effector Design
An optimized end effector design brings multiple advantages to industrial operations:
Enhanced Productivity
With a well-designed end effector, robots can perform tasks faster and more accurately.
This accelerates production rates and boosts overall productivity.
Cost Efficiency
Efficient end effectors reduce material waste and energy consumption.
Durable designs lower maintenance costs, extending the lifespan of both the end effector and the robot.
Improved Quality
Precision in design ensures high-quality task execution.
Products manufactured with optimized end effectors exhibit consistent quality, reducing defects and rework.
Greater Flexibility
Versatile end effectors allow robots to handle diverse tasks, adapting to changing production demands.
This flexibility is valuable for industries with varied product lines.
Challenges in End Effector Design
While optimization presents numerous benefits, it also entails challenges.
Engineers must navigate these to achieve successful designs:
Complex Manufacturing Processes
Advanced designs often require intricate manufacturing processes.
Balancing complexity with feasibility is crucial to stay within practical constraints.
Cost Constraints
High-performance materials and cutting-edge techniques can be costly.
Optimizing designs involves finding a balance between performance and budget considerations.
Integration with Robotic Systems
The end effector must seamlessly integrate with the rest of the robotic system.
Compatibility challenges can arise, requiring careful alignment with the robot’s specifications.
Future Trends in End Effector Design
The field of end effector design is ever-evolving.
Here are some trends shaping its future:
Smart Materials
The development of smart materials that change properties based on external stimuli can revolutionize end effector design.
These materials enhance adaptability and performance in dynamic environments.
Advanced Sensors
The integration of advanced sensors allows for real-time monitoring and adjustments.
This enables greater precision, especially in complex tasks requiring fine motor skills.
AI and Machine Learning
Artificial intelligence and machine learning can analyze vast amounts of data to optimize end effector designs.
These technologies improve design processes, leading to innovative and highly efficient solutions.
Conclusion
End effector design optimization for industrial robots is a critical aspect that directly impacts operational efficiency, cost savings, and product quality.
By considering key factors such as weight, size, flexibility, precision, and durability, and employing advanced techniques like FEA, topology optimization, and virtual prototyping, engineers can create highly optimized end effectors.
The future of this field promises even more innovation with advancements in smart materials, sensors, and AI.
Through continuous improvement and adaptation, end effectors will continue to enhance the capabilities of industrial robots, driving progress across various industries.
資料ダウンロード
QCD調達購買管理クラウド「newji」は、調達購買部門で必要なQCD管理全てを備えた、現場特化型兼クラウド型の今世紀最高の購買管理システムとなります。
ユーザー登録
調達購買業務の効率化だけでなく、システムを導入することで、コスト削減や製品・資材のステータス可視化のほか、属人化していた購買情報の共有化による内部不正防止や統制にも役立ちます。
NEWJI DX
製造業に特化したデジタルトランスフォーメーション(DX)の実現を目指す請負開発型のコンサルティングサービスです。AI、iPaaS、および先端の技術を駆使して、製造プロセスの効率化、業務効率化、チームワーク強化、コスト削減、品質向上を実現します。このサービスは、製造業の課題を深く理解し、それに対する最適なデジタルソリューションを提供することで、企業が持続的な成長とイノベーションを達成できるようサポートします。
オンライン講座
製造業、主に購買・調達部門にお勤めの方々に向けた情報を配信しております。
新任の方やベテランの方、管理職を対象とした幅広いコンテンツをご用意しております。
お問い合わせ
コストダウンが利益に直結する術だと理解していても、なかなか前に進めることができない状況。そんな時は、newjiのコストダウン自動化機能で大きく利益貢献しよう!
(Β版非公開)