- お役立ち記事
- Energy-saving technology for automatic welding machines and examples of its application in the manufacturing industry
月間77,185名の
製造業ご担当者様が閲覧しています*
*2025年2月28日現在のGoogle Analyticsのデータより
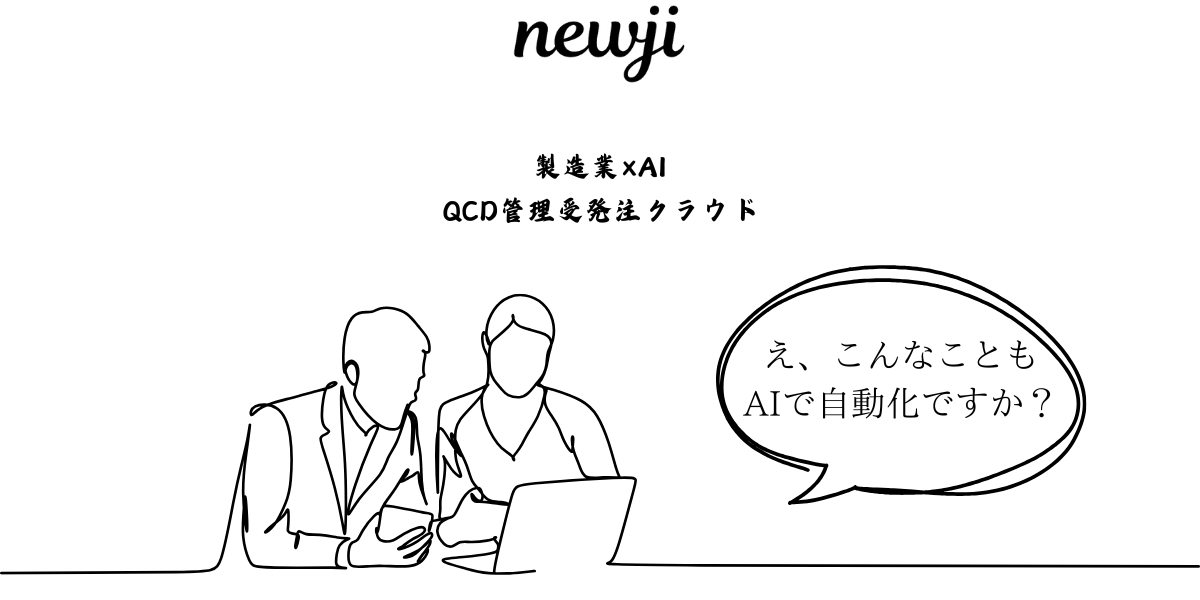
Energy-saving technology for automatic welding machines and examples of its application in the manufacturing industry
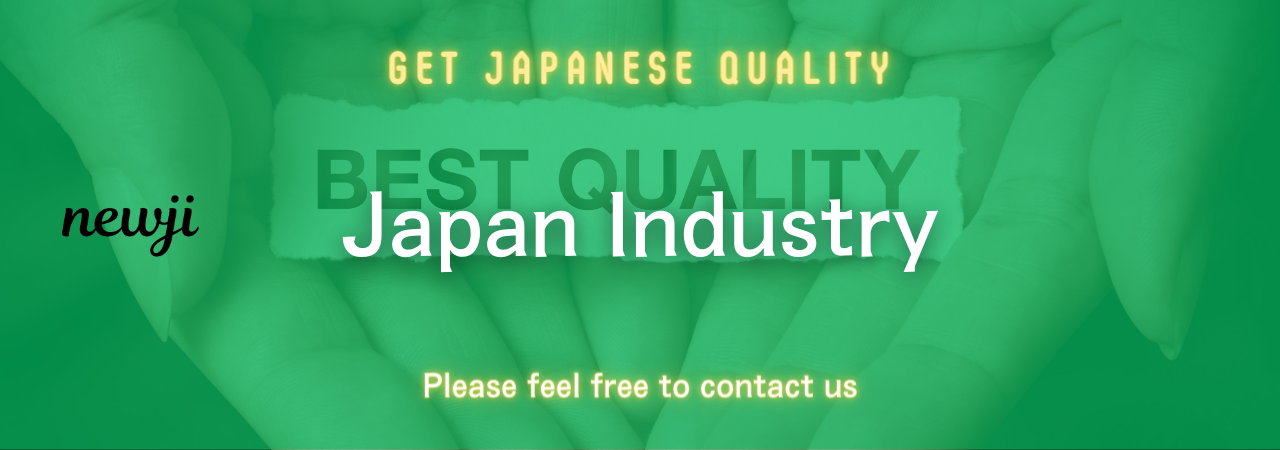
目次
Introduction to Energy-Saving Technology in Automatic Welding Machines
In recent years, the manufacturing industry has seen a significant shift toward sustainable practices, with energy-saving technology playing a pivotal role.
Automatic welding machines, critical for production efficiency, are no exception to this trend.
These machines, essential in various industries for joining metal parts, now incorporate advanced technologies that help save energy, reduce costs, and increase operational efficiency.
Why Energy Efficiency Matters in Welding
The manufacturing sector is one of the largest consumers of energy worldwide, and welding processes contribute substantially to this consumption.
Energy efficiency in welding is crucial for several reasons.
Firstly, reducing energy usage can lead to significant cost savings.
Secondly, it helps companies meet environmental targets by lowering carbon footprints.
Lastly, energy-efficient processes can enhance machine longevity and performance, thus reducing maintenance costs.
Advanced Technologies Used in Energy-Saving Welding Machines
Several cutting-edge technologies have been integrated into modern automatic welding machines to make them more energy-efficient.
Here are some notable advancements:
Inverter-Based Welding Power Supplies
Inverter technology is a game-changer for energy efficiency in welding machines.
Unlike traditional transformers, inverter-based power supplies offer enhanced efficiency by converting AC to DC with minimal energy loss.
This results in lower power consumption and better performance in terms of weld quality and speed.
Automated Shutdown Features
Many automatic welding machines now come equipped with automated shutdown features.
These machines are designed to switch to standby mode or turn off completely if they remain idle for a certain period.
This technology not only conserves energy but also prolongs the lifespan of the machine by reducing wear and tear.
Energy Monitoring and Management Systems
Modern welding machines often include sophisticated energy monitoring and management systems.
These systems allow manufacturers to track energy consumption in real time and adjust welding parameters accordingly to optimize efficiency.
Such systems can identify energy wastage and provide actionable insights for further improvement.
Reduced Energy Consumption Through Efficiency
Some machines incorporate advanced welding techniques like laser or hybrid welding, which are more efficient than traditional methods.
These techniques require less energy while delivering high-quality welds, making them ideal for applications where precision and efficiency are crucial.
Examples of Application in the Manufacturing Industry
Energy-saving technologies in automatic welding machines have been successfully implemented across various sectors in the manufacturing industry.
Here are some practical examples:
Automotive Industry
In the automotive industry, welding is a core process, crucial for the production of parts such as frames and engines.
Companies have adopted energy-efficient welding machines to cut production costs and improve environmental sustainability.
By utilizing inverter-based power supplies and automated systems, automotive manufacturers have witnessed a significant reduction in energy consumption.
Aerospace and Defense
The aerospace and defense sector requires precision welding for building highly specialized components.
Energy-efficient automatic welding machines are employed to ensure top-notch weld quality while minimizing energy use.
Laser and hybrid welding techniques, in particular, have gained popularity for their ability to create precise joints with minimal energy requirements.
Construction Industry
In construction, large-scale welding operations are common, especially in projects involving steel structures.
Energy-saving technologies in welding machines have proven beneficial in reducing operational costs.
Inverters and energy management systems are especially valuable, providing construction companies with the tools to monitor and manage energy use dynamically.
Benefits of Implementing Energy-Saving Technologies
Manufacturers who incorporate energy-saving technologies in their automatic welding machines enjoy several advantages:
Cost Reduction
One of the primary benefits is a substantial reduction in operational costs.
By lowering the energy consumption of welding machines, manufacturers can save on utility bills and reduce overall production expenses.
Environmental Impact
Adopting energy-efficient technologies contributes to reducing greenhouse gas emissions.
This not only supports environmental sustainability goals but also helps companies comply with stringent regulations aimed at curbing industrial pollution.
Enhanced Competitive Advantage
Manufacturing entities that invest in energy-saving technology often gain a competitive advantage.
They can market themselves as environmentally friendly and cost-effective, attracting customers and partners who value sustainability.
Future Trends in Energy-Saving Welding Technologies
The development of energy-saving technologies in welding machines is expected to continue as manufacturers strive for greater efficiency and sustainability.
Here are some anticipated trends:
Integration of AI and IoT
The use of artificial intelligence (AI) and the Internet of Things (IoT) in energy management will likely increase.
These technologies can enable real-time monitoring and adaptive control of welding processes, further enhancing efficiency and energy savings.
Advanced Materials and Designs
Research into advanced materials and innovative machine designs will continue to provide avenues for energy efficiency improvements.
These advancements will focus on minimizing energy losses and maximizing output.
Conclusion
Energy-saving technology for automatic welding machines is revolutionizing manufacturing processes, leading to increased efficiency, reduced costs, and more sustainable operations.
By adopting these technologies, manufacturers can not only improve their bottom line but also contribute positively to environmental conservation.
As this trend continues, the future of manufacturing looks both efficient and green, benefiting not only businesses but the planet as well.
資料ダウンロード
QCD管理受発注クラウド「newji」は、受発注部門で必要なQCD管理全てを備えた、現場特化型兼クラウド型の今世紀最高の受発注管理システムとなります。
ユーザー登録
受発注業務の効率化だけでなく、システムを導入することで、コスト削減や製品・資材のステータス可視化のほか、属人化していた受発注情報の共有化による内部不正防止や統制にも役立ちます。
NEWJI DX
製造業に特化したデジタルトランスフォーメーション(DX)の実現を目指す請負開発型のコンサルティングサービスです。AI、iPaaS、および先端の技術を駆使して、製造プロセスの効率化、業務効率化、チームワーク強化、コスト削減、品質向上を実現します。このサービスは、製造業の課題を深く理解し、それに対する最適なデジタルソリューションを提供することで、企業が持続的な成長とイノベーションを達成できるようサポートします。
製造業ニュース解説
製造業、主に購買・調達部門にお勤めの方々に向けた情報を配信しております。
新任の方やベテランの方、管理職を対象とした幅広いコンテンツをご用意しております。
お問い合わせ
コストダウンが利益に直結する術だと理解していても、なかなか前に進めることができない状況。そんな時は、newjiのコストダウン自動化機能で大きく利益貢献しよう!
(β版非公開)