- お役立ち記事
- Enhancing Equipment Reliability in Manufacturing with MTBF (Mean Time Between Failures)
Enhancing Equipment Reliability in Manufacturing with MTBF (Mean Time Between Failures)
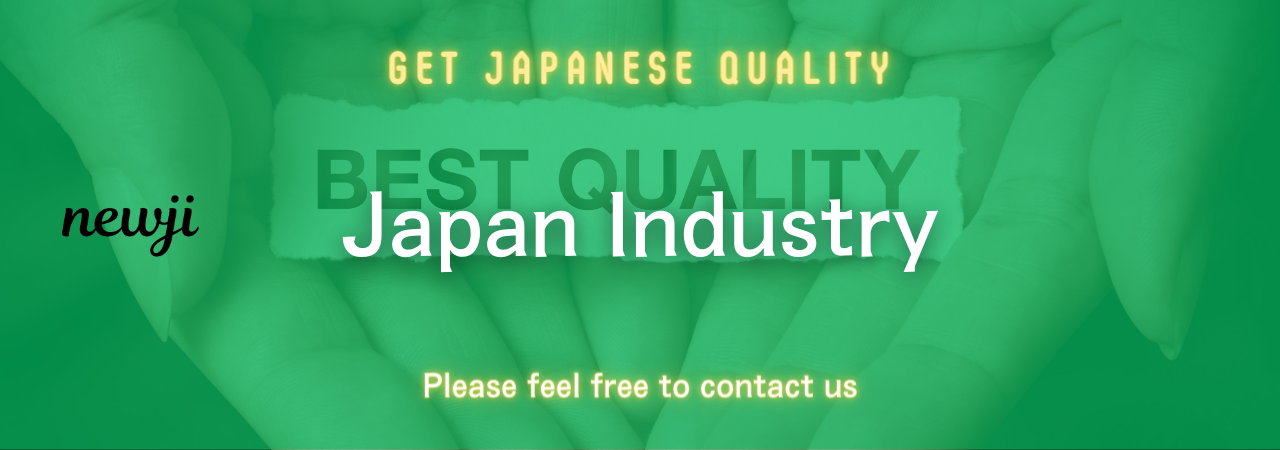
In today’s manufacturing industry, maintaining equipment reliability is crucial for ensuring smooth operations and reducing downtime.
One effective way to achieve this is by understanding and applying the concept of Mean Time Between Failures (MTBF).
Let’s explore how MTBF can enhance equipment reliability and contribute to the success of your manufacturing processes.
目次
What is Mean Time Between Failures (MTBF)?
MTBF is a key metric used to measure the reliability of equipment.
It represents the average time between two consecutive failures of a machine or system.
By calculating MTBF, manufacturers can predict the likelihood of equipment failures and schedule preventive maintenance accordingly.
How is MTBF Calculated?
Calculating MTBF is straightforward.
You divide the total operating time of the equipment by the number of failures that occurred during that period.
For example, if a machine operates for 1,000 hours and experiences 4 failures, the MTBF would be 1,000 hours divided by 4, which equals 250 hours.
This means, on average, the equipment is expected to operate for 250 hours before encountering a failure.
Formula for MTBF
The formula for MTBF is:
MTBF = Total Operating Time / Number of Failures
Utilizing this formula, you can easily estimate the reliability of your equipment over a specified timeframe.
Benefits of Using MTBF
Incorporating MTBF into your manufacturing processes offers several advantages that can significantly improve equipment reliability:
1. Improved Maintenance Scheduling
By knowing the MTBF of your equipment, you can better plan and schedule maintenance activities.
Rather than performing maintenance randomly or based on guesswork, you can use MTBF data to predict when a failure is likely to occur.
This allows for timely preventive maintenance, reducing the likelihood of unexpected breakdowns and minimizing downtime.
2. Increased Equipment Lifespan
Regular maintenance based on MTBF calculations can prolong the life of your machines.
By addressing potential issues before they lead to major failures, you can prevent excessive wear and tear on your equipment.
This results in longer-lasting machines and cost savings in the long run.
3. Enhanced Productivity
Equipment failures can disrupt the production process, leading to delays and decreased productivity.
With MTBF, you can minimize the frequency and duration of these disruptions.
Reliable equipment that operates without frequent breakdowns ensures a smooth production flow and helps meet production targets consistently.
4. Cost Savings
Unplanned equipment failures can be costly due to repair expenses and lost production time.
By utilizing MTBF to implement a proactive maintenance strategy, you can reduce the occurrence of such failures and save on repair costs.
Strategically scheduled maintenance also means less need for emergency repairs, which are often more expensive.
Best Practices for Enhancing Equipment Reliability with MTBF
To make the most out of MTBF and improve equipment reliability, consider the following best practices:
1. Collect Accurate Data
Accurate data is the foundation of reliable MTBF calculations.
Ensure that you consistently record operating hours and log every equipment failure.
This will provide a clear picture of your equipment’s performance and help you make informed decisions about maintenance schedules.
2. Analyze and Interpret Data
Once you have collected data, analyze it to identify patterns and trends.
Look for recurring issues or specific components that frequently fail.
Understanding the root causes of failures will allow you to address them effectively and prevent future occurrences.
3. Implement Predictive Maintenance
Predictive maintenance involves using data and analytics to predict when equipment is likely to fail.
By leveraging MTBF data, you can develop predictive models that indicate the optimal time for maintenance.
This enables you to fix potential problems before they cause an actual failure, maximizing equipment uptime.
4. Train Personnel
Ensure that your maintenance team is well-trained in using MTBF data and implementing preventive maintenance strategies.
Provide them with the necessary tools and resources to monitor equipment performance and respond to potential issues proactively.
A knowledgeable and skilled team is essential for maintaining equipment reliability.
5. Continuously Monitor and Adjust
MTBF is not a one-time calculation but a continuous process.
Regularly monitor your equipment’s performance and update your MTBF calculations as needed.
If you notice any changes in failure patterns, adjust your maintenance schedules accordingly to maintain optimal reliability.
Common Misconceptions About MTBF
Despite its usefulness, there are some common misconceptions about MTBF that need to be clarified:
1. MTBF is Not a Guarantee
MTBF provides an average time between failures, but it does not guarantee that failures will occur exactly at those intervals.
Equipment can fail earlier or later than the predicted MTBF, so it should be used as a guideline rather than an exact prediction.
2. MTBF is Not the Only Metric
While MTBF is valuable, it should not be the sole metric for assessing equipment reliability.
Other metrics, such as Mean Time to Repair (MTTR) and Overall Equipment Effectiveness (OEE), provide additional insights into equipment performance and maintenance needs.
3. MTBF Requires Context
MTBF values can vary based on operating conditions, usage patterns, and environmental factors.
It is essential to consider these variables when interpreting MTBF data and making maintenance decisions.
In conclusion, leveraging the concept of Mean Time Between Failures (MTBF) can significantly enhance equipment reliability in manufacturing.
By accurately calculating and utilizing MTBF, you can improve maintenance scheduling, increase equipment lifespan, boost productivity, and achieve cost savings.
Implementing best practices and addressing common misconceptions will ensure that you make the most out of MTBF, ultimately contributing to the success of your manufacturing processes.
資料ダウンロード
QCD調達購買管理クラウド「newji」は、調達購買部門で必要なQCD管理全てを備えた、現場特化型兼クラウド型の今世紀最高の購買管理システムとなります。
ユーザー登録
調達購買業務の効率化だけでなく、システムを導入することで、コスト削減や製品・資材のステータス可視化のほか、属人化していた購買情報の共有化による内部不正防止や統制にも役立ちます。
NEWJI DX
製造業に特化したデジタルトランスフォーメーション(DX)の実現を目指す請負開発型のコンサルティングサービスです。AI、iPaaS、および先端の技術を駆使して、製造プロセスの効率化、業務効率化、チームワーク強化、コスト削減、品質向上を実現します。このサービスは、製造業の課題を深く理解し、それに対する最適なデジタルソリューションを提供することで、企業が持続的な成長とイノベーションを達成できるようサポートします。
オンライン講座
製造業、主に購買・調達部門にお勤めの方々に向けた情報を配信しております。
新任の方やベテランの方、管理職を対象とした幅広いコンテンツをご用意しております。
お問い合わせ
コストダウンが利益に直結する術だと理解していても、なかなか前に進めることができない状況。そんな時は、newjiのコストダウン自動化機能で大きく利益貢献しよう!
(Β版非公開)