- お役立ち記事
- Enhancing Japanese Manufacturing Excellence with Cutting-Edge Surface Treatment Support
Enhancing Japanese Manufacturing Excellence with Cutting-Edge Surface Treatment Support
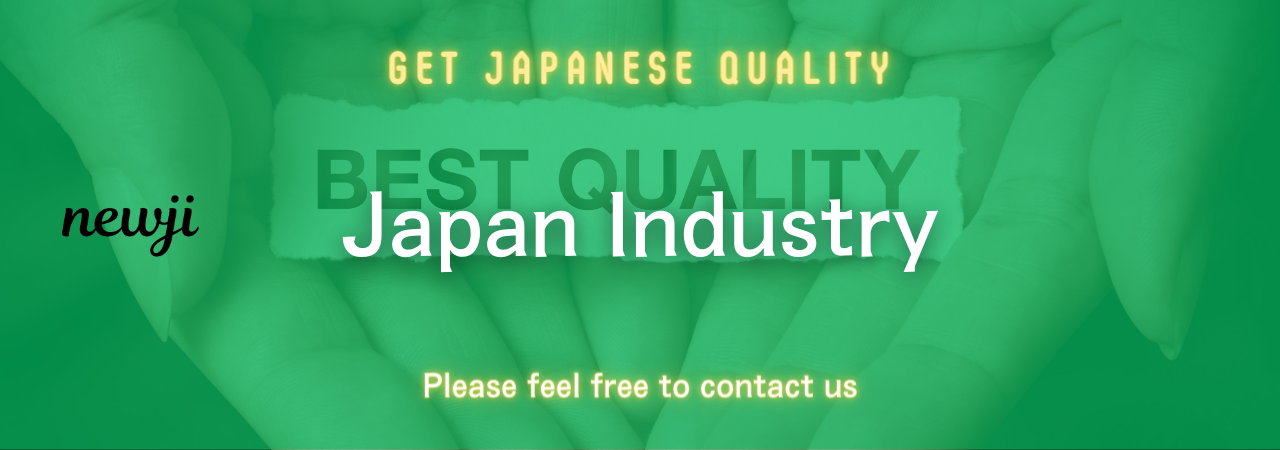
目次
Introduction
Enhancing manufacturing excellence is a paramount objective for companies striving to maintain a competitive edge in today’s global market.
Japanese manufacturing has long been revered for its precision, efficiency, and commitment to quality.
A critical component of this excellence lies in advanced surface treatment processes.
Surface treatment not only improves the aesthetic appeal of products but also enhances their durability and performance.
This article delves into how cutting-edge surface treatment support can elevate Japanese manufacturing, exploring procurement and purchasing strategies, supplier negotiation techniques, market conditions, and best practices.
Advantages of Japanese Manufacturing Excellence
Japanese manufacturing is synonymous with high standards and continuous improvement.
The principles of Kaizen, or continuous improvement, drive manufacturers to seek incremental advancements in processes and products.
This culture fosters innovation and leads to the development of superior manufacturing techniques.
Moreover, Japanese manufacturers emphasize quality control, ensuring that each product meets stringent specifications.
The integration of advanced technologies, such as automation and robotics, further enhances efficiency and precision.
These advantages collectively contribute to the global reputation of Japanese manufacturing excellence.
The Role of Surface Treatment in Manufacturing
Surface treatment plays a pivotal role in manufacturing by altering the surface properties of materials to achieve desired characteristics.
It encompasses various processes, including coating, plating, anodizing, and heat treating.
These treatments can improve corrosion resistance, increase hardness, reduce friction, and enhance aesthetic appeal.
In industries such as automotive, electronics, and aerospace, surface treatment is essential for ensuring product longevity and reliability.
By implementing advanced surface treatment techniques, manufacturers can meet the evolving demands of consumers and regulatory standards.
Cutting-Edge Surface Treatment Technologies
The landscape of surface treatment technology is continuously evolving, with innovations aimed at improving efficiency and performance.
Electroless plating is gaining traction for its ability to provide uniform coatings without the need for electrical current.
Pulsed laser deposition offers precise control over coating thickness and composition, ideal for high-performance applications.
Nanotechnology-based treatments are being explored to create surfaces with unique properties, such as superhydrophobicity and enhanced biocompatibility.
Electrochemical machining is another advanced technique that allows for the precise removal of material, shaping surfaces to exact specifications.
These cutting-edge technologies enable manufacturers to achieve superior surface characteristics, driving the excellence of Japanese manufacturing.
Procurement and Purchasing Strategies for Surface Treatment
Effective procurement and purchasing strategies are crucial for acquiring high-quality surface treatment materials and services.
Japanese manufacturers often adopt a strategic sourcing approach, focusing on building long-term relationships with reliable suppliers.
This approach ensures consistent quality and fosters collaboration in developing innovative surface treatment solutions.
Bulk purchasing can lead to significant cost savings, especially when negotiating with established suppliers.
Additionally, implementing just-in-time inventory practices minimizes storage costs and reduces the risk of material obsolescence.
Leveraging technology, such as procurement software, can streamline the purchasing process, enhance transparency, and improve supplier management.
Supplier Selection and Evaluation
Selecting the right suppliers is fundamental to the success of surface treatment processes.
Japanese manufacturers typically conduct rigorous evaluations, assessing potential suppliers based on quality standards, reliability, and technological capabilities.
Certifications such as ISO 9001 and industry-specific accreditations are often prerequisites.
Site visits and audits are conducted to verify the supplier’s facilities and production practices.
Performance metrics, including on-time delivery rates and defect rates, are monitored continuously to ensure sustained quality and reliability.
Cost Management and Negotiation
Managing costs effectively is essential for maintaining profitability without compromising quality.
Japanese manufacturers employ strategic negotiation techniques to secure favorable terms and pricing.
This includes volume discounts, long-term contracts, and flexible payment terms.
Understanding the supplier’s cost structure and market conditions allows for more informed negotiations.
Building strong relationships can also lead to preferential treatment, such as priority during high-demand periods or access to new technologies.
Supplier Negotiation Techniques with Japanese Manufacturers
Negotiating with suppliers in Japan requires a nuanced understanding of cultural and business practices.
Respect, patience, and building trust are key elements in successful negotiations.
Japanese businesses value long-term relationships over short-term gains, so demonstrating commitment and reliability is crucial.
Clear and open communication helps in aligning expectations and resolving conflicts amicably.
It’s also beneficial to approach negotiations with a collaborative mindset, seeking mutually beneficial outcomes rather than adversarial positions.
Understanding the supplier’s needs and constraints can lead to innovative solutions that enhance both parties’ operational efficiency.
Cultural Considerations
Japanese culture emphasizes harmony, respect, and indirect communication.
Negotiators should be mindful of these values, avoiding confrontational tactics and showing genuine respect for the supplier’s perspectives.
Formal attire, punctuality, and adherence to protocol are important in establishing credibility and trust.
Building rapport through small talk and understanding the cultural context can facilitate smoother negotiations.
Value-Based Negotiation
Focusing on value creation rather than solely on price can lead to more sustainable agreements.
This involves identifying areas where both parties can benefit, such as improving process efficiencies or developing new surface treatment technologies.
Offering support in areas like research and development or providing market insights can enhance the value proposition.
By prioritizing mutual benefits, manufacturers can foster stronger, more resilient supplier relationships.
Market Conditions and Trends in Surface Treatment
The surface treatment market is influenced by various factors, including technological advancements, regulatory changes, and shifting consumer preferences.
Environmental regulations are becoming increasingly stringent, prompting manufacturers to adopt eco-friendly surface treatment methods.
There is a growing demand for sustainable and non-toxic coatings, driving innovation in green surface treatment technologies.
Additionally, the rise of smart materials and the Internet of Things (IoT) are creating opportunities for surface treatments that enhance connectivity and functionality.
Economic fluctuations and global supply chain disruptions also impact market dynamics, necessitating agile procurement and supply chain strategies.
Impact of Technology
Emerging technologies such as additive manufacturing and advanced robotics are reshaping surface treatment processes.
These technologies enable more precise and customizable treatments, meeting the diverse needs of modern industries.
Automation and artificial intelligence are being integrated into surface treatment operations to enhance efficiency and reduce human error.
The adoption of Industry 4.0 principles facilitates real-time monitoring and data-driven decision-making, optimizing surface treatment outcomes.
Sustainability Trends
Sustainability is a key trend influencing surface treatment practices.
Manufacturers are increasingly adopting processes that minimize environmental impact, such as reducing waste and energy consumption.
Eco-friendly coatings, derived from renewable resources or designed for easy recyclability, are gaining popularity.
The move towards circular economy models encourages the development of surface treatments that facilitate product reuse and recycling.
Best Practices for Enhancing Manufacturing Efficiency
Implementing best practices is essential for maximizing the benefits of advanced surface treatment support.
Continuous improvement methodologies, such as Lean and Six Sigma, can streamline processes and eliminate inefficiencies.
Investing in employee training ensures that the workforce is skilled in the latest surface treatment technologies and techniques.
Regular maintenance of equipment minimizes downtime and extends the lifespan of machinery.
Collaboration across departments, including procurement, production, and quality control, fosters a holistic approach to manufacturing excellence.
Quality Assurance and Control
Maintaining high-quality standards is critical in surface treatment.
Implementing robust quality assurance and control measures ensures that each treatment meets the required specifications.
Regular inspections, testing, and documentation help identify and rectify defects promptly.
Adopting statistical process control (SPC) techniques allows for the monitoring of process variations and the implementation of corrective actions before defects occur.
Data-Driven Decision Making
Leveraging data analytics can enhance decision-making processes in surface treatment.
Collecting and analyzing data on process performance, material properties, and customer feedback provides valuable insights.
These insights can inform process optimizations, material selections, and quality improvements.
Implementing a data-driven approach enables manufacturers to anticipate trends, respond to market changes, and maintain a competitive edge.
Challenges and Disadvantages
Despite the numerous advantages, integrating cutting-edge surface treatment support presents certain challenges.
High initial investment costs for advanced technologies can be a barrier, especially for smaller manufacturers.
The complexity of new surface treatment processes may require extensive training and adaptation.
Supply chain disruptions, such as delays in material acquisition or transportation issues, can impede production timelines.
Additionally, balancing cost-efficiency with the need for high-quality treatments can be challenging, necessitating careful strategic planning.
Technical Limitations
Some advanced surface treatment technologies may have technical limitations, such as compatibility with certain materials or scalability issues.
Manufacturers must assess the feasibility of integrating these technologies into existing production lines.
Research and development efforts are often needed to overcome technical hurdles and tailor solutions to specific manufacturing needs.
Regulatory Compliance
Navigating the regulatory landscape is another challenge, particularly concerning environmental and safety standards.
Compliance with local and international regulations requires ongoing monitoring and adaptation of surface treatment processes.
Failure to comply can result in legal penalties, reputational damage, and operational disruptions.
Conclusion
Enhancing Japanese manufacturing excellence through cutting-edge surface treatment support is a multifaceted endeavor that encompasses strategic procurement, effective supplier negotiations, and the adoption of advanced technologies.
By leveraging best practices and navigating the associated challenges, manufacturers can achieve superior product quality, increased efficiency, and sustained competitiveness.
The integration of innovative surface treatment solutions not only meets the current market demands but also paves the way for future advancements in manufacturing.
Japanese manufacturers, with their commitment to excellence and continuous improvement, are well-positioned to lead the way in this dynamic and essential aspect of production.
資料ダウンロード
QCD調達購買管理クラウド「newji」は、調達購買部門で必要なQCD管理全てを備えた、現場特化型兼クラウド型の今世紀最高の購買管理システムとなります。
ユーザー登録
調達購買業務の効率化だけでなく、システムを導入することで、コスト削減や製品・資材のステータス可視化のほか、属人化していた購買情報の共有化による内部不正防止や統制にも役立ちます。
NEWJI DX
製造業に特化したデジタルトランスフォーメーション(DX)の実現を目指す請負開発型のコンサルティングサービスです。AI、iPaaS、および先端の技術を駆使して、製造プロセスの効率化、業務効率化、チームワーク強化、コスト削減、品質向上を実現します。このサービスは、製造業の課題を深く理解し、それに対する最適なデジタルソリューションを提供することで、企業が持続的な成長とイノベーションを達成できるようサポートします。
オンライン講座
製造業、主に購買・調達部門にお勤めの方々に向けた情報を配信しております。
新任の方やベテランの方、管理職を対象とした幅広いコンテンツをご用意しております。
お問い合わせ
コストダウンが利益に直結する術だと理解していても、なかなか前に進めることができない状況。そんな時は、newjiのコストダウン自動化機能で大きく利益貢献しよう!
(Β版非公開)