- お役立ち記事
- Enhancing Japanese Manufacturing Quality: The Critical Role of Visual Inspections
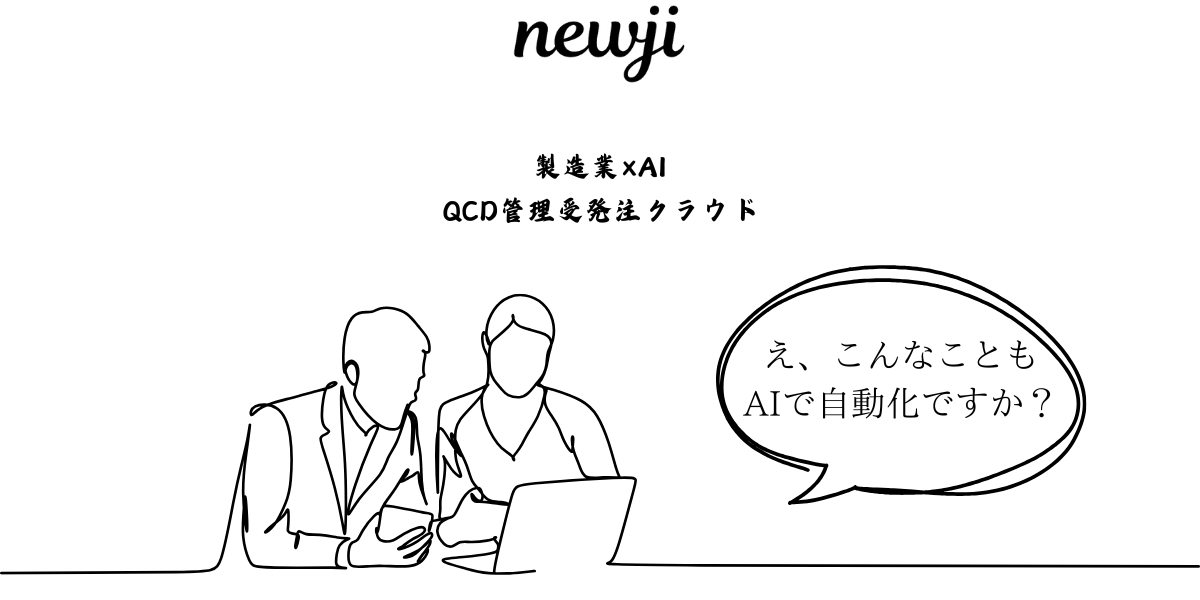
Enhancing Japanese Manufacturing Quality: The Critical Role of Visual Inspections
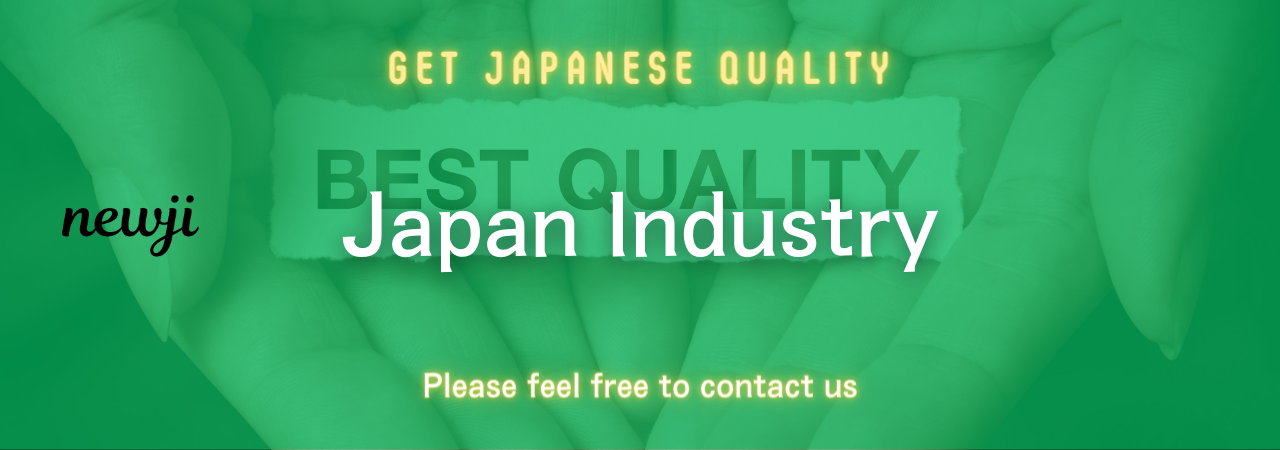
目次
Introduction to Japanese Manufacturing Quality
Japan is renowned globally for its exceptional manufacturing quality.
The term “Made in Japan” is synonymous with reliability, precision, and longevity.
One of the pivotal elements contributing to this stellar reputation is the rigorous quality control processes employed by Japanese manufacturers.
Among these, visual inspections hold a significant place.
Visual inspections, conducted by skilled inspectors, ensure that each product meets stringent quality standards before it reaches the customer.
In this article, we’ll explore the importance of visual inspections in Japanese manufacturing, the methodologies employed, and the best practices that are integral to achieving top-tier quality.
The Importance of Visual Inspections in Manufacturing
In manufacturing, maintaining high quality is non-negotiable.
A product riddled with defects can damage a company’s reputation and lead to financial losses.
Visual inspections play a crucial role in catching anomalies that automated systems might miss.
Japanese manufacturing emphasizes the importance of human elements in quality control.
Despite advancements in automation and artificial intelligence, human inspectors bring a level of attention and discernment that machines cannot replicate.
Skilled inspectors can assess subtle imperfections, color inconsistencies, or minor deformities that are often overlooked by automated systems.
Advantages of Visual Inspections
Visual inspections, when performed by trained professionals, offer numerous advantages that contribute to maintaining high manufacturing standards.
Human Expertise and Intuition
Visual inspections leverage the unique ability of humans to recognize irregularities that are not easily quantifiable.
For instance, a minor discoloration or an unexpected texture may indicate a potential defect.
Experienced inspectors, familiar with the products and production processes, can quickly identify and address these issues.
Adaptability
Unlike automated systems, human inspectors can adapt to new challenges and changing inspection criteria with relative ease.
This flexibility is particularly valuable during the introduction of new products, modifications in production processes, or adjustments in quality standards.
Inspectors can promptly recalibrate their assessment criteria to align with the latest requirements.
Preventive Measures
Early detection of defects through visual inspections allows manufacturers to implement preventive measures promptly.
By identifying and addressing issues at an early stage, companies can minimize the risk of defective products reaching the market.
Furthermore, this proactive approach helps avoid costly recalls and damage to brand reputation.
Disadvantages of Visual Inspections
While visual inspections offer substantial benefits, there are certain limitations and challenges associated with their implementation.
Subjectivity
One of the primary drawbacks of visual inspections is the element of subjectivity.
Different inspectors may have varying interpretations of what constitutes an acceptable level of quality.
To mitigate this issue, it is essential to establish clear and consistent inspection criteria, supported by comprehensive training programs.
Labor Intensive
Visual inspections are labor-intensive and can be time-consuming, particularly for large-scale manufacturing operations.
Allocating sufficient resources, training, and supervision is necessary to ensure that the inspection process remains effective and efficient.
Fatigue
Inspectors may experience fatigue, which can affect their ability to accurately identify defects over prolonged periods.
Implementing regular breaks, job rotation, and ergonomic workstations can help mitigate the impact of fatigue on inspection accuracy.
Supplier Negotiation Techniques
Successful procurement and purchasing involve effective negotiation with suppliers, particularly in the context of ensuring high-quality visual inspections.
Here are some proven techniques for negotiating with Japanese suppliers to achieve optimal results.
Building Strong Relationships
In Japan, business relationships are built on trust and long-term collaboration.
Invest time in developing a strong rapport with your suppliers.
Regular communication, mutual respect, and understanding of each other’s needs and expectations are crucial for fostering a productive partnership.
Clarity of Expectations
Clearly articulate your quality requirements and inspection criteria to your suppliers.
Provide detailed specifications, samples, and reference materials to ensure that there is no ambiguity in what is expected.
This clarity will help in minimizing misunderstandings and ensuring that the products meet your quality standards.
Collaborative Problem Solving
Approach negotiations with a collaborative mindset.
Instead of focusing solely on price, engage in constructive discussions about quality improvement and defect prevention.
Encourage your suppliers to share insights and suggestions on enhancing the inspection process and addressing potential issues.
Performance Metrics
Establish performance metrics and key performance indicators (KPIs) to objectively evaluate the supplier’s performance.
Regularly review these metrics and provide feedback to your suppliers.
Recognize and reward exceptional performance, while also addressing areas that require improvement.
Best Practices in Visual Inspections
Implementing best practices in visual inspections can significantly enhance the overall quality of manufactured products.
Here are some key practices that can be adopted to ensure effective and efficient visual inspections.
Standardized Inspection Procedures
Develop standardized inspection procedures that outline the steps, criteria, and tools to be used during visual inspections.
Consistency is critical in ensuring that all products are evaluated uniformly.
Documenting these procedures also facilitates training and onboarding of new inspectors.
Training and Skill Development
Invest in comprehensive training programs for inspectors to enhance their skills and knowledge.
Provide regular updates on new products, technologies, and quality standards.
Encouraging skill development through workshops, certifications, and cross-training can improve the overall effectiveness of the inspection process.
Utilizing Advanced Tools
Leverage advanced tools and technologies to assist inspectors in their tasks.
This may include magnifying devices, color consistency meters, and digital imaging systems.
These tools can enhance the precision and accuracy of visual inspections, enabling inspectors to identify defects that might be otherwise overlooked.
Continuous Improvement
Adopt a culture of continuous improvement by encouraging feedback and suggestions from inspectors.
Regularly review and analyze inspection data to identify trends, recurring issues, and opportunities for enhancement.
Implementing changes based on these insights can lead to incremental improvements in the inspection process and overall product quality.
Market Conditions and Trends
Understanding market conditions and trends is essential for staying competitive in the manufacturing industry.
Here are some key insights into market conditions and emerging trends related to visual inspections in Japanese manufacturing.
Increasing Demand for High-Quality Products
Consumers and businesses worldwide are increasingly demanding high-quality products.
This trend is particularly pronounced in sectors such as automotive, electronics, and healthcare.
As a result, manufacturers are placing greater emphasis on rigorous quality control processes, including visual inspections, to meet these expectations.
Advancements in Inspection Technologies
Technological advancements are revolutionizing visual inspections.
Automated inspection systems, machine vision, and artificial intelligence are being integrated into the inspection process to enhance accuracy and efficiency.
While human inspectors remain indispensable, these technologies complement their efforts by handling repetitive tasks and analyzing complex data.
Focus on Sustainability
Sustainability is a growing concern in the manufacturing industry.
Consumers are increasingly conscious of the environmental impact of the products they purchase.
Manufacturers are responding by implementing sustainable practices, including reducing waste and minimizing defects through effective visual inspections.
This focus on sustainability aligns with the broader goals of corporate social responsibility.
Global Supply Chain Challenges
Global supply chain disruptions, such as those experienced during the COVID-19 pandemic, have highlighted the importance of robust quality control practices.
Manufacturers are prioritizing the reliability and resilience of their supply chains.
Visual inspections play a critical role in verifying the quality of incoming materials and components, ensuring that production processes remain uninterrupted.
Conclusion
Visual inspections are a cornerstone of Japanese manufacturing quality.
Their role in ensuring that products meet stringent quality standards cannot be overstated.
Despite the advancements in automation and inspection technologies, human expertise remains invaluable in detecting subtle defects and inconsistencies.
By adopting best practices, investing in training, and leveraging advanced tools, manufacturers can enhance the effectiveness of visual inspections.
Additionally, understanding market conditions, negotiating effectively with suppliers, and focusing on continuous improvement are essential strategies for maintaining high-quality standards.
In an era where quality and sustainability are paramount, the insights and techniques shared in this article can serve as a valuable resource for manufacturers aiming to achieve excellence in their production processes.
As we continue to navigate the evolving landscape of manufacturing, the principles of visual inspections will remain integral to upholding the reputation of “Made in Japan” products.
資料ダウンロード
QCD調達購買管理クラウド「newji」は、調達購買部門で必要なQCD管理全てを備えた、現場特化型兼クラウド型の今世紀最高の購買管理システムとなります。
ユーザー登録
調達購買業務の効率化だけでなく、システムを導入することで、コスト削減や製品・資材のステータス可視化のほか、属人化していた購買情報の共有化による内部不正防止や統制にも役立ちます。
NEWJI DX
製造業に特化したデジタルトランスフォーメーション(DX)の実現を目指す請負開発型のコンサルティングサービスです。AI、iPaaS、および先端の技術を駆使して、製造プロセスの効率化、業務効率化、チームワーク強化、コスト削減、品質向上を実現します。このサービスは、製造業の課題を深く理解し、それに対する最適なデジタルソリューションを提供することで、企業が持続的な成長とイノベーションを達成できるようサポートします。
オンライン講座
製造業、主に購買・調達部門にお勤めの方々に向けた情報を配信しております。
新任の方やベテランの方、管理職を対象とした幅広いコンテンツをご用意しております。
お問い合わせ
コストダウンが利益に直結する術だと理解していても、なかなか前に進めることができない状況。そんな時は、newjiのコストダウン自動化機能で大きく利益貢献しよう!
(Β版非公開)