- お役立ち記事
- Enhancing Process Precision in Manufacturing with MEMS Sensors
Enhancing Process Precision in Manufacturing with MEMS Sensors
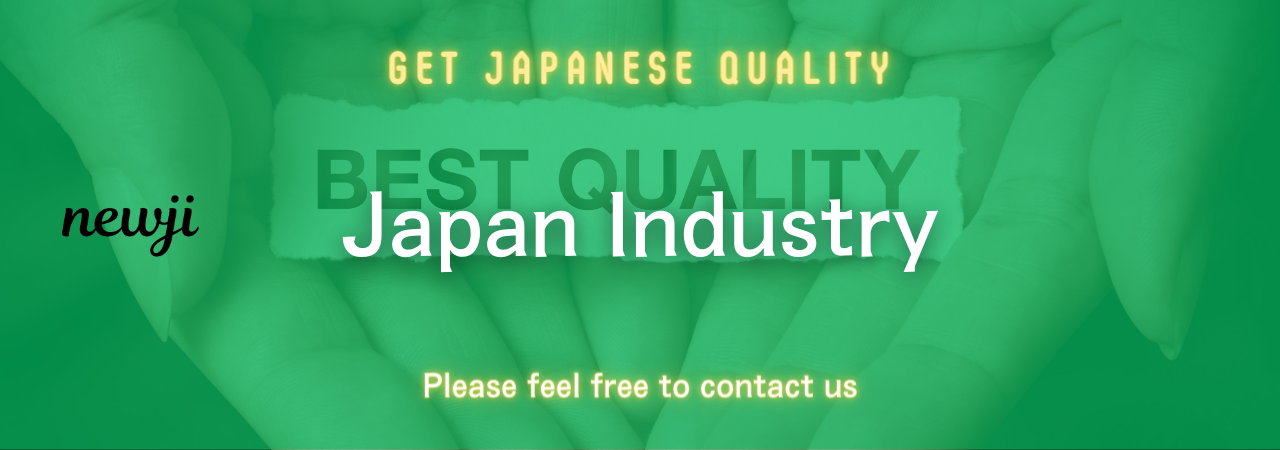
In today’s rapidly evolving manufacturing landscape, precision is not just a requirement; it’s an expectation.
As companies strive to produce items with impeccable quality, they turn to state-of-the-art technologies that ensure accuracy at every step of the production process.
Among these advanced technologies, MEMS (Micro-Electro-Mechanical Systems) sensors are proving to be a game-changer.
By enhancing process precision in manufacturing, MEMS sensors are providing manufacturers with the tools they need to stay ahead of the competition.
目次
What Are MEMS Sensors?
Micro-Electro-Mechanical Systems, or MEMS, are miniature devices that combine electronic and mechanical components.
MEMS sensors measure and respond to physical stimuli such as pressure, motion, temperature, and more.
Despite their small size, these sensors are incredibly powerful, offering high levels of precision and reliability.
Originally designed for applications in consumer electronics and automotive industries, MEMS sensors are now finding their way into the manufacturing sector where they can significantly enhance process precision.
Understanding MEMS Technology
The core of MEMS technology lies in its ability to integrate tiny mechanical elements, sensors, actuators, and electronics onto a single chip.
Manufactured using semiconductor fabrication techniques, these sensors can detect minute changes in their environment.
MEMS sensors convert physical parameters, such as pressure or acceleration, into electrical signals that can be monitored and analyzed in real time.
This real-time feedback is crucial for maintaining high precision in manufacturing processes, helping to reduce errors and improve product quality.
The Role of MEMS Sensors in Manufacturing
In the context of manufacturing, precision is paramount.
Even the slightest deviation from the specified parameters can result in defective products, leading to costly rework or scrap.
MEMS sensors play a critical role in minimizing these deviations by providing accurate, real-time data that guides the production process.
Quality Control and Assurance
One of the primary applications of MEMS sensors in manufacturing is in quality control and assurance.
By continuously monitoring various parameters, such as temperature, humidity, and pressure, these sensors ensure that the manufacturing environment remains within the desired specifications.
This constant monitoring helps in identifying any anomalies that could affect product quality.
For instance, MEMS sensors can detect any unusual vibrations in machinery, indicating potential mechanical failures.
This allows for timely maintenance, preventing costly downtimes and ensuring that the production process remains smooth and efficient.
Precision in Machining and Fabrication
Machining and fabrication processes require extreme precision.
Traditional methods often struggle to maintain the necessary accuracy due to factors such as tool wear and thermal expansion.
MEMS sensors mitigate these challenges by providing precise measurements of tool positions and environmental conditions.
For instance, MEMS accelerometers can detect minute changes in a tool’s position, allowing for real-time adjustments.
This capability ensures that each cut or fabrication step is executed with the utmost precision, resulting in higher-quality products.
Automation and Robotics
Modern manufacturing increasingly relies on automation and robotics to enhance efficiency and precision.
MEMS sensors are integral to the functioning of these automated systems.
By providing real-time feedback on parameters such as position, orientation, and force, MEMS sensors enable robots to perform intricate tasks with high accuracy.
For example, in assembly lines, MEMS sensors help robots pick and place components with precision, reducing the chances of misalignment or damage.
This level of precision is crucial for maintaining consistent product quality and minimizing waste.
Benefits of Using MEMS Sensors in Manufacturing
The integration of MEMS sensors in manufacturing processes offers a multitude of benefits.
From improved product quality to reduced operational costs, the advantages are substantial.
Enhanced Product Quality
By providing accurate, real-time data, MEMS sensors help maintain tight control over manufacturing processes.
This control translates into higher product quality, with fewer defects and inconsistencies.
Consistent quality not only satisfies customer expectations but also enhances the reputation of the manufacturer, leading to increased business opportunities.
Cost Savings
Precision in manufacturing reduces the likelihood of defects and rework, leading to significant cost savings.
Additionally, the real-time feedback provided by MEMS sensors helps in optimizing the use of materials and energy, further reducing operational costs.
Preventive maintenance enabled by MEMS sensors also minimizes unexpected downtimes, ensuring that production schedules are adhered to and resources are used efficiently.
Increased Efficiency
MEMS sensors facilitate the automation of complex manufacturing processes, increasing overall efficiency.
With these sensors in place, manufacturers can achieve faster production cycles without compromising on quality.
The ability to monitor and adjust processes in real time also enhances the flexibility of manufacturing systems, allowing for quick adaptation to changes in demand or production requirements.
Sustainability
Sustainable manufacturing is becoming increasingly important in today’s environmentally conscious world.
The precision enabled by MEMS sensors contributes to sustainability by reducing waste and optimizing resource usage.
By ensuring that processes are as efficient and accurate as possible, MEMS sensors help manufacturers minimize their environmental footprint.
Applications of MEMS Sensors in Manufacturing
The versatility of MEMS sensors makes them suitable for a wide range of applications in the manufacturing sector.
Some notable examples include:
Condition Monitoring
MEMS sensors are widely used for condition monitoring of machinery and equipment.
By tracking parameters such as vibration, temperature, and pressure, these sensors provide valuable insights into the health of equipment.
This information allows for predictive maintenance, reducing the risk of unexpected failures and extending the lifespan of machinery.
Precision Measurement
In processes such as machining, MEMS sensors are used for precision measurement of tool positions and dimensions.
This capability ensures that final products meet exact specifications, reducing the need for rework and enhancing overall quality.
Environmental Monitoring
MEMS sensors are also used to monitor environmental conditions within manufacturing facilities.
By tracking parameters such as air quality, humidity, and temperature, these sensors help maintain optimal working conditions, ensuring the safety and well-being of workers.
The Future of MEMS Sensors in Manufacturing
As technology continues to advance, the role of MEMS sensors in manufacturing is expected to grow even further.
Innovations in sensor technology will lead to even more precise and reliable measurements, enabling manufacturers to achieve new levels of quality and efficiency.
Additionally, the integration of MEMS sensors with other advanced technologies, such as the Internet of Things (IoT) and artificial intelligence (AI), will open up new possibilities for smart manufacturing.
These advancements will further enhance the ability of manufacturers to monitor, control, and optimize their processes in real time.
The use of MEMS sensors in manufacturing is revolutionizing the industry by enhancing precision and reliability.
From ensuring superior product quality to achieving significant cost savings, the benefits of these sensors are manifold.
As the technology continues to evolve, MEMS sensors will undoubtedly play an increasingly crucial role in shaping the future of manufacturing, enabling companies to produce better products more efficiently and sustainably.
資料ダウンロード
QCD調達購買管理クラウド「newji」は、調達購買部門で必要なQCD管理全てを備えた、現場特化型兼クラウド型の今世紀最高の購買管理システムとなります。
ユーザー登録
調達購買業務の効率化だけでなく、システムを導入することで、コスト削減や製品・資材のステータス可視化のほか、属人化していた購買情報の共有化による内部不正防止や統制にも役立ちます。
NEWJI DX
製造業に特化したデジタルトランスフォーメーション(DX)の実現を目指す請負開発型のコンサルティングサービスです。AI、iPaaS、および先端の技術を駆使して、製造プロセスの効率化、業務効率化、チームワーク強化、コスト削減、品質向上を実現します。このサービスは、製造業の課題を深く理解し、それに対する最適なデジタルソリューションを提供することで、企業が持続的な成長とイノベーションを達成できるようサポートします。
オンライン講座
製造業、主に購買・調達部門にお勤めの方々に向けた情報を配信しております。
新任の方やベテランの方、管理職を対象とした幅広いコンテンツをご用意しております。
お問い合わせ
コストダウンが利益に直結する術だと理解していても、なかなか前に進めることができない状況。そんな時は、newjiのコストダウン自動化機能で大きく利益貢献しよう!
(Β版非公開)