- お役立ち記事
- Enhancing Product Quality and Reliability by Complying with Safety Standards
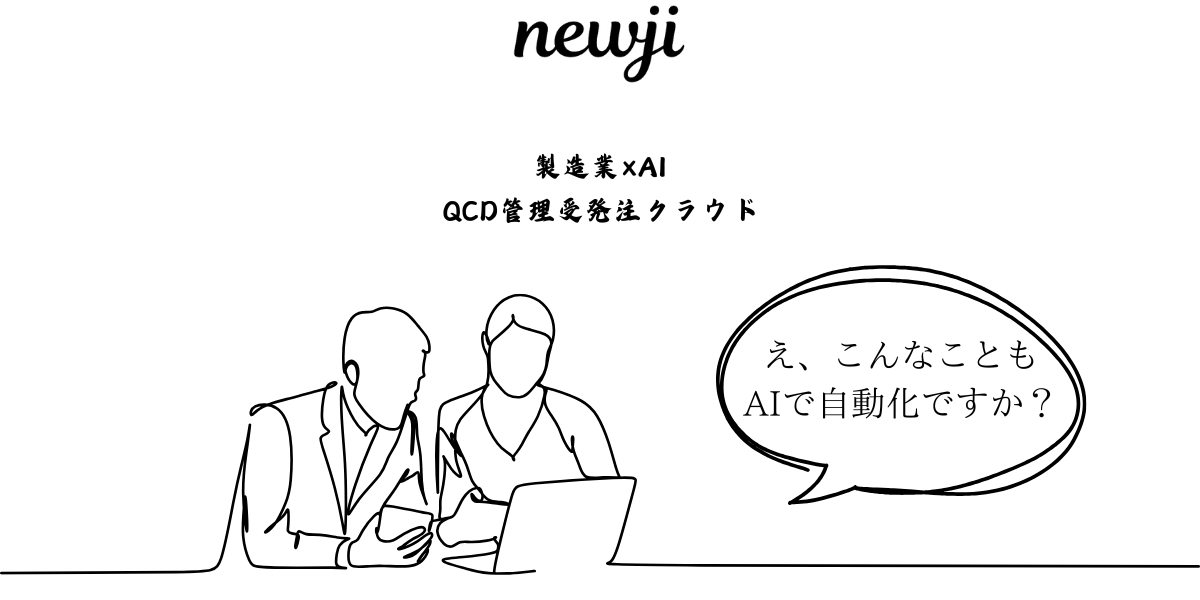
Enhancing Product Quality and Reliability by Complying with Safety Standards
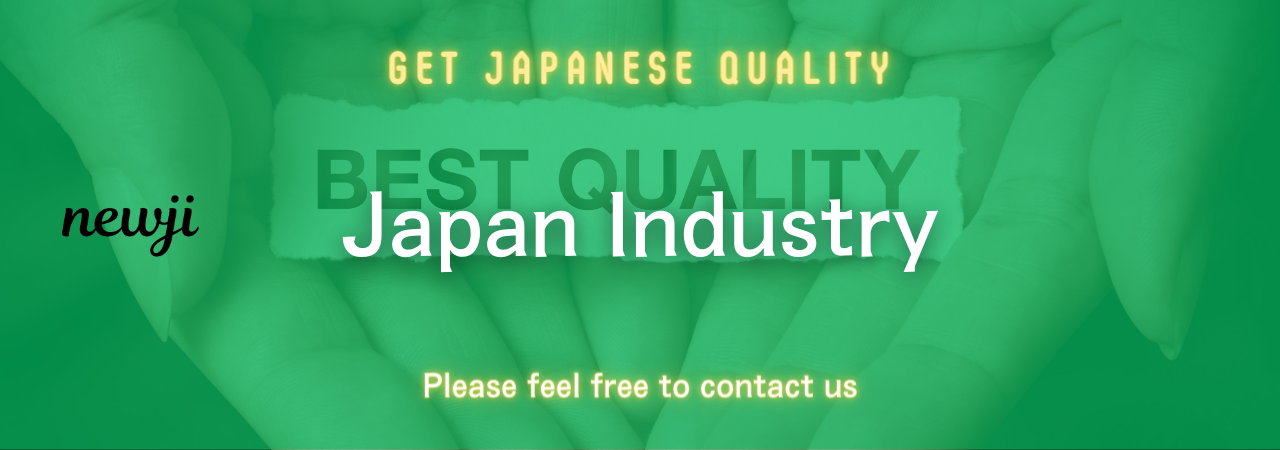
目次
Understanding Safety Standards
In today’s highly competitive market, ensuring the quality and reliability of products is essential for businesses to succeed.
An integral part of this process is complying with established safety standards.
These standards are designed to ensure that products are safe for consumer use, minimizing risk and liability for manufacturers.
By understanding and adhering to these guidelines, companies not only improve their product quality but also build trust with their customers.
Safety standards are established by regulatory bodies and industry organizations.
They provide specifications and criteria that products must meet to be deemed safe and fit for distribution.
These specifications often cover various aspects, such as materials used, performance under certain conditions, and user interaction.
Meeting these standards entails rigorous testing and quality control, which helps to identify potential hazards before a product reaches the market.
The Importance of Compliance
Compliance with safety standards is not just a regulatory requirement but also a strategic business decision.
First and foremost, it helps to prevent accidents and injuries that could arise from using unsafe products.
By reducing these risks, companies can avoid costly lawsuits and damage to their reputation.
Furthermore, complying with safety standards often opens up new markets that require certification, thereby expanding a company’s customer base.
Additionally, product recalls can be devastating for any business.
They not only incur direct costs but also lead to a significant loss of consumer confidence.
A focus on safety compliance significantly reduces the likelihood of recalls, thus safeguarding the company’s brand image and financial stability.
Moreover, by consistently delivering safe products, manufacturers strengthen customer loyalty and establish themselves as leaders in their respective fields.
Impact on Product Development
Incorporating safety standards into the product development process ensures that safety is a priority from the very beginning.
This approach requires collaboration between design, engineering, and testing teams to assess safety risks at every stage.
As a result, potential issues are identified early, reducing the time and cost associated with later-stage modifications or corrections.
Moreover, adopting a safety-first mindset fosters innovation.
It challenges teams to find new materials and design techniques that not only meet safety requirements but also improve product performance.
By integrating safety with creativity, companies can produce cutting-edge products that captivate consumers and set trends in the industry.
Adapting to Evolving Standards
Safety standards are not static; they evolve in response to technological advancements, consumer feedback, and new research findings.
Staying updated with these changes is crucial for maintaining compliance.
Companies must invest in ongoing training and development programs to ensure that their teams are knowledgeable about the latest safety protocols and technologies.
Proactively monitoring industry trends and participating in standard-setting activities helps businesses anticipate changes before they are formally introduced.
This foresight allows companies to adjust their processes in advance, maintaining compliance without disrupting product development cycles.
Furthermore, being at the forefront of such initiatives can position a business as an industry leader, respected by peers and consumers alike.
Implementing Quality Control Systems
To effectively comply with safety standards, robust quality control systems must be in place.
These systems help consistent monitoring and enforcement of safety requirements throughout the production process.
Implementing such systems involves defining clear procedures for testing and inspection.
Every component and step in the manufacturing process should have specific guidelines to follow.
This ensures that any deviations from the standard are quickly identified and corrected.
Moreover, documentation plays a critical role in maintaining quality control.
Recording testing results, corrective actions, and process adjustments provides a transparent record of compliance efforts.
This not only aids in external audits but also facilitates internal reviews, driving continuous improvement.
Supplier Relationships and Quality Assurance
An essential aspect of complying with safety standards is ensuring that suppliers also adhere to quality criteria.
Building strong relationships with suppliers based on trust and transparency is vital.
Setting clear expectations and conducting regular audits of supplier facilities can confirm that the materials and components they provide meet required safety standards.
Additionally, collaborating with suppliers can lead to mutual benefits.
Sharing knowledge and insights about safety expectations can enhance overall supply chain quality, reduce costs, and lead to product innovations.
Together, manufacturers and suppliers can work towards achieving the highest safety standards, benefiting the end consumer.
Utilizing Technological Advancements
Recent technological advancements offer new opportunities for improving product safety and quality.
Automation and artificial intelligence can help streamline testing processes, making them more accurate and less time-consuming.
These technologies allow for real-time monitoring and data collection, which can swiftly identify any potential safety issues.
Moreover, digital twins and simulation software enable detailed analysis of product behavior under various conditions without physical prototypes.
This not only saves resources but also allows for rapid iteration and testing of design modifications.
Manufacturers can leverage these tools to enhance their products while ensuring adherence to safety standards.
The Role of Feedback and Iteration
Consumer feedback provides valuable insights into product performance and safety.
Encouraging and actively seeking feedback helps identify areas for improvement that may not have been evident during internal testing.
Regularly reviewing and updating products based on real-time data and consumer insights supports ongoing compliance with safety standards.
By responding to consumer needs and expectations, companies can continually improve their offerings and maintain a reputation for quality and reliability.
Embracing a feedback loop also encourages a culture of continuous improvement.
It ensures that safety and quality remain at the forefront of product development and production strategies.
In conclusion, complying with safety standards is not just about meeting regulatory requirements.
It is a strategic approach that enhances product quality and reliability.
Through understanding and implementing these standards, companies can protect their brand reputation, build customer loyalty, and open up new market opportunities, all while ensuring the safety and satisfaction of their consumers.
資料ダウンロード
QCD調達購買管理クラウド「newji」は、調達購買部門で必要なQCD管理全てを備えた、現場特化型兼クラウド型の今世紀最高の購買管理システムとなります。
ユーザー登録
調達購買業務の効率化だけでなく、システムを導入することで、コスト削減や製品・資材のステータス可視化のほか、属人化していた購買情報の共有化による内部不正防止や統制にも役立ちます。
NEWJI DX
製造業に特化したデジタルトランスフォーメーション(DX)の実現を目指す請負開発型のコンサルティングサービスです。AI、iPaaS、および先端の技術を駆使して、製造プロセスの効率化、業務効率化、チームワーク強化、コスト削減、品質向上を実現します。このサービスは、製造業の課題を深く理解し、それに対する最適なデジタルソリューションを提供することで、企業が持続的な成長とイノベーションを達成できるようサポートします。
オンライン講座
製造業、主に購買・調達部門にお勤めの方々に向けた情報を配信しております。
新任の方やベテランの方、管理職を対象とした幅広いコンテンツをご用意しております。
お問い合わせ
コストダウンが利益に直結する術だと理解していても、なかなか前に進めることができない状況。そんな時は、newjiのコストダウン自動化機能で大きく利益貢献しよう!
(Β版非公開)