- お役立ち記事
- Enhancing Production Efficiency and Cost Reduction Through Real-Time Data Analysis
Enhancing Production Efficiency and Cost Reduction Through Real-Time Data Analysis
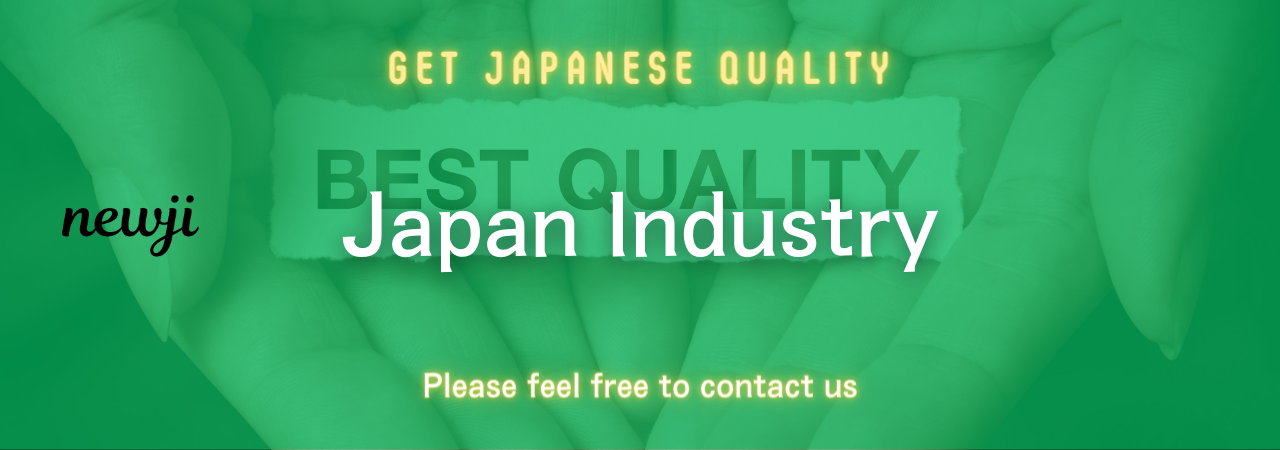
In today’s fast-paced manufacturing environment, enhancing production efficiency and reducing costs are primary objectives for any business.
The use of real-time data analysis is proving to be a game-changer in achieving these goals.
By leveraging real-time data, manufacturers can optimize various processes, minimize downtime, and make informed decisions that drive productivity and profitability.
目次
The Importance of Production Efficiency
Production efficiency is a measure of how well resources are used to produce goods.
It involves maximizing output while minimizing input such as labor, materials, and time.
Efficient production not only reduces costs but also leads to higher quality products and increased customer satisfaction.
Manufacturers face numerous challenges that can hinder production efficiency.
These include equipment failures, supply chain disruptions, and variations in quality.
To address these issues, companies are turning to real-time data analysis to monitor and improve their production processes.
What is Real-Time Data Analysis?
Real-time data analysis involves collecting and analyzing data as it is generated.
This contrasts with traditional data analysis, which is often done retrospectively.
By using sensors, IoT devices, and advanced software, manufacturers can capture and analyze data from machines, production lines, and even supply chains in real-time.
This immediate access to information allows businesses to respond quickly to any issues that arise, thus minimizing downtime and maintaining production flow.
Real-time data analysis can also identify trends and patterns that can inform future decision-making.
Key Benefits of Real-Time Data Analysis
There are several key benefits of implementing real-time data analysis in manufacturing:
1. Reduced Downtime
Downtime can be extremely costly for manufacturers.
Real-time data analysis can help identify and predict equipment failures before they occur.
By monitoring machine performance and identifying abnormalities, maintenance teams can address issues proactively, thereby reducing unplanned downtime.
2. Increased Productivity
With real-time data, manufacturers can optimize their production processes for maximum efficiency.
This might involve adjusting machine settings, reallocating labor, or streamlining workflows.
The result is increased throughput and higher overall productivity.
3. Cost Savings
Real-time data analysis helps in identifying inefficiencies and waste in the production process.
By addressing these issues promptly, manufacturers can reduce material wastage, lower energy consumption, and cut down on labor costs.
These cost savings directly impact the company’s bottom line.
4. Enhanced Product Quality
Consistent product quality is crucial for customer satisfaction.
Real-time data allows manufacturers to monitor quality parameters closely and in real-time.
This enables immediate corrective actions if any deviations from quality standards are detected, ensuring that only high-quality products reach the market.
5. Better Supply Chain Management
Supply chain disruptions can severely impact production schedules.
Real-time data provides visibility into every aspect of the supply chain, from raw material availability to shipping times.
Manufacturers can use this information to optimize inventory levels, reduce lead times, and ensure a smooth production flow.
Implementing Real-Time Data Analysis
Implementing real-time data analysis in a manufacturing setting involves several key steps:
1. Identify Key Metrics and Data Sources
The first step is to identify which metrics are most critical to your production process.
These could include machine performance, quality parameters, or supply chain data.
Next, determine the data sources for these metrics.
This might involve installing sensors on equipment, integrating IoT devices, or using data from existing enterprise systems.
2. Invest in the Right Technology
To analyze data in real-time, you need the right technology.
This includes hardware such as sensors and IoT devices and software platforms that can aggregate and analyze data.
Cloud-based solutions can offer scalability and flexibility, making it easier to handle large volumes of data.
3. Ensure Data Integration
For real-time analysis to be effective, data from various sources need to be integrated seamlessly.
This may involve using APIs, middleware, or custom integrations to ensure that all data streams are connected and accessible in real time.
4. Train Your Team
Your team needs to be well-versed in using real-time data analysis tools and interpreting the results.
Invest in training to ensure that your staff can make the most of the technology and apply data-driven insights to improve production efficiency.
5. Continuously Monitor and Optimize
Real-time data analysis is not a one-time task.
Continuously monitor your production processes and use the data to make iterative improvements.
Regularly review the data to identify new opportunities for optimization and cost reduction.
Case Studies of Real-Time Data Analysis in Manufacturing
Several companies have successfully implemented real-time data analysis to enhance production efficiency and reduce costs.
Here are a few examples:
Case Study 1: Automotive Manufacturer
An automotive manufacturer faced frequent production delays due to equipment failures.
By implementing real-time data analysis, the company was able to predict and prevent equipment breakdowns.
This resulted in a 20% reduction in downtime and significant cost savings.
Case Study 2: Food and Beverage Company
A food and beverage company used real-time data to monitor quality parameters during production.
This enabled them to detect and correct any deviations immediately, leading to a 15% improvement in product quality and reduced waste.
Case Study 3: Electronics Manufacturer
An electronics manufacturer integrated real-time data from its supply chain to optimize inventory levels.
This helped reduce lead times, avoid stockouts, and ensure a steady production flow.
As a result, the company saw a 10% increase in productivity and lower inventory costs.
The Future of Real-Time Data Analysis in Manufacturing
The future of manufacturing lies in data-driven decision-making.
As technology continues to advance, real-time data analysis will become even more sophisticated and accessible.
Machine learning and artificial intelligence will play a significant role in analyzing vast amounts of data and providing actionable insights.
Manufacturers that embrace real-time data analysis will be better positioned to adapt to changing market conditions, optimize their operations, and stay ahead of the competition.
In a world where efficiency and cost-effectiveness are paramount, real-time data analysis is not just an option, but a necessity.
資料ダウンロード
QCD調達購買管理クラウド「newji」は、調達購買部門で必要なQCD管理全てを備えた、現場特化型兼クラウド型の今世紀最高の購買管理システムとなります。
ユーザー登録
調達購買業務の効率化だけでなく、システムを導入することで、コスト削減や製品・資材のステータス可視化のほか、属人化していた購買情報の共有化による内部不正防止や統制にも役立ちます。
NEWJI DX
製造業に特化したデジタルトランスフォーメーション(DX)の実現を目指す請負開発型のコンサルティングサービスです。AI、iPaaS、および先端の技術を駆使して、製造プロセスの効率化、業務効率化、チームワーク強化、コスト削減、品質向上を実現します。このサービスは、製造業の課題を深く理解し、それに対する最適なデジタルソリューションを提供することで、企業が持続的な成長とイノベーションを達成できるようサポートします。
オンライン講座
製造業、主に購買・調達部門にお勤めの方々に向けた情報を配信しております。
新任の方やベテランの方、管理職を対象とした幅広いコンテンツをご用意しております。
お問い合わせ
コストダウンが利益に直結する術だと理解していても、なかなか前に進めることができない状況。そんな時は、newjiのコストダウン自動化機能で大きく利益貢献しよう!
(Β版非公開)