- お役立ち記事
- Enhancing Quality in Manufacturing with QFD: Success Stories and Practical Guide
Enhancing Quality in Manufacturing with QFD: Success Stories and Practical Guide
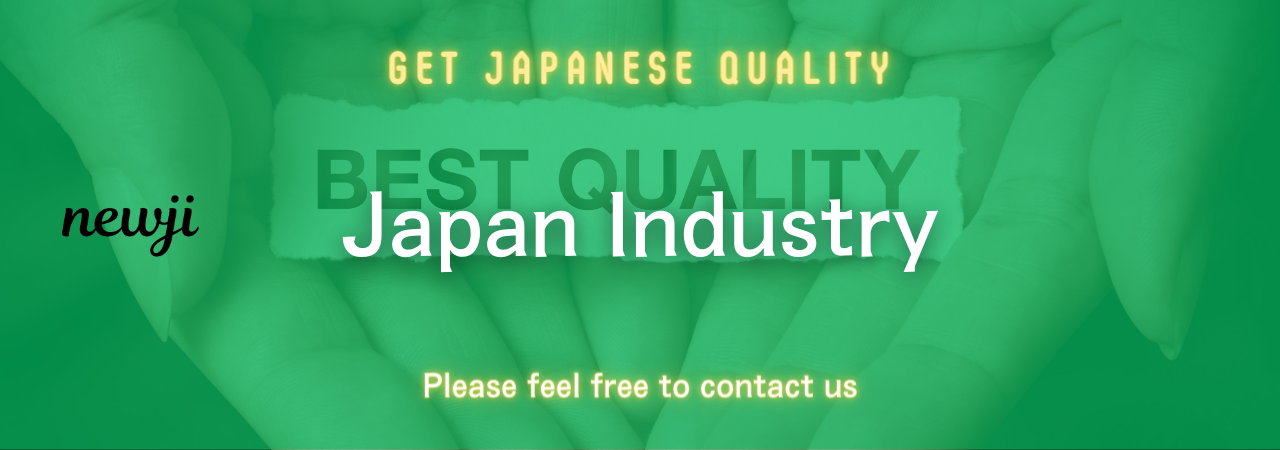
Quality Function Deployment (QFD) is a crucial methodology in manufacturing that aligns production with customer demands.
QFD helps businesses improve their product design and development by translating customer requirements into specific engineering characteristics.
By doing this, companies can ensure that they are producing goods that meet or exceed customer expectations.
In this article, we’ll dive into the concept of QFD, explore some success stories, and offer practical guidance on how to implement QFD in your manufacturing processes.
目次
Understanding Quality Function Deployment
What is QFD?
Quality Function Deployment is a structured approach used to define customer needs and convert them into detailed engineering specifications.
It involves creating a series of matrices to capture the voice of the customer and ensure it is accurately reflected in the final product.
The process typically begins with identifying key customer demands, known as the “Voice of the Customer” (VOC), and then translating these demands into technical requirements.
The Benefits of QFD
QFD enhances product quality by ensuring that customer needs are thoroughly understood and addressed in the design process.
It reduces the risk of miscommunication between different departments within an organization.
Additionally, QFD helps in prioritizing features based on customer desires, leading to more satisfied end-users.
Overall, the deployment of QFD can lead to shorter development cycles, reduced costs, and improved product quality.
Real-world Success Stories
Toyota’s Use of QFD
One of the most famous success stories of QFD is its adoption by Toyota in the 1970s.
By using QFD, Toyota was able to significantly improve the design and manufacturing of their automobiles.
The company focused on understanding customer desires for reliability, fuel efficiency, and driving comfort.
Through meticulous deployment of QFD, Toyota could translate these customer needs into specific design and production criteria.
This approach helped Toyota cement its reputation for producing high-quality and reliable vehicles, which in turn contributed to its becoming one of the top automotive manufacturers globally.
Boeing’s Aircraft Manufacturing
Boeing also reaped significant benefits by implementing QFD in its aircraft manufacturing processes.
The company used QFD to align its product development with the requirements of airlines and passengers.
By listening to the voice of their customers, Boeing was able to introduce innovative features, such as improved cabin comfort and enhanced in-flight entertainment systems.
These improvements helped Boeing maintain a competitive edge in the aerospace industry.
Apple’s Product Development
Apple has been known for its commitment to customer satisfaction, and part of its success can be attributed to the use of QFD.
The company uses QFD to ensure that every new product release addresses customer needs and preferences.
From the sleek design of the iPhone to the intuitive user interface of Mac computers, Apple has consistently demonstrated the effectiveness of integrating QFD into its product development strategy.
How to Implement QFD in Your Manufacturing Process
Step 1: Identify Customer Needs
The first step in implementing QFD is to gather and analyze customer needs.
This can be done through various methods, including surveys, focus groups, and direct customer feedback.
It’s crucial to capture the voice of the customer accurately to ensure their needs are properly addressed.
Step 2: Create the House of Quality
The House of Quality is a key tool in the QFD process.
It’s a matrix that helps organizations translate customer requirements into engineering characteristics.
Start by listing customer needs on the left side of the matrix and engineering characteristics across the top.
Next, use a scoring system to assess the relationship between customer needs and technical requirements.
This visual representation helps teams understand how changes in engineering characteristics affect customer satisfaction.
Step 3: Prioritize Requirements
With the House of Quality in place, the next step is to prioritize both customer needs and engineering characteristics.
This involves determining which customer requirements are most critical and which technical features will have the greatest impact on those needs.
Assign weights or scores to indicate the relative importance of each factor.
Step 4: Develop Actionable Plans
After prioritizing requirements, create actionable plans to address the most critical customer needs and technical characteristics.
This might involve redesigning certain aspects of the product, adjusting manufacturing processes, or incorporating new technologies.
Ensure that these plans are communicated clearly to all relevant departments within the organization.
Step 5: Implement and Monitor
Once actionable plans are in place, proceed with implementation.
Monitor the progress regularly to ensure that the changes are effectively meeting customer needs.
Collect feedback from customers and make adjustments as necessary.
Regular monitoring and feedback loops are essential to maintaining the efficacy of QFD.
Challenges and Considerations
Resource Allocation
Implementing QFD can be resource-intensive, requiring a significant investment of time and effort from various departments.
Ensure that your organization is prepared to allocate the necessary resources to fully embrace the QFD process.
Cultural Shift
QFD represents a significant shift from traditional product development approaches.
It requires a collaborative culture where departments work together to understand and address customer needs.
Be prepared to invest in training and change management to foster this culture within your organization.
Continuous Improvement
QFD is not a one-time process but rather a continuous commitment to quality improvement.
Encourage your team to regularly revisit and refine the QFD matrices as customer needs evolve over time.
Continuous improvement helps ensure that your products remain competitive and aligned with market demands.
By implementing QFD in your manufacturing processes, you can enhance product quality, improve customer satisfaction, and gain a competitive edge in your industry.
With careful planning and commitment, your organization can successfully navigate the challenges and reap the benefits of this powerful methodology.
資料ダウンロード
QCD調達購買管理クラウド「newji」は、調達購買部門で必要なQCD管理全てを備えた、現場特化型兼クラウド型の今世紀最高の購買管理システムとなります。
ユーザー登録
調達購買業務の効率化だけでなく、システムを導入することで、コスト削減や製品・資材のステータス可視化のほか、属人化していた購買情報の共有化による内部不正防止や統制にも役立ちます。
NEWJI DX
製造業に特化したデジタルトランスフォーメーション(DX)の実現を目指す請負開発型のコンサルティングサービスです。AI、iPaaS、および先端の技術を駆使して、製造プロセスの効率化、業務効率化、チームワーク強化、コスト削減、品質向上を実現します。このサービスは、製造業の課題を深く理解し、それに対する最適なデジタルソリューションを提供することで、企業が持続的な成長とイノベーションを達成できるようサポートします。
オンライン講座
製造業、主に購買・調達部門にお勤めの方々に向けた情報を配信しております。
新任の方やベテランの方、管理職を対象とした幅広いコンテンツをご用意しております。
お問い合わせ
コストダウンが利益に直結する術だと理解していても、なかなか前に進めることができない状況。そんな時は、newjiのコストダウン自動化機能で大きく利益貢献しよう!
(Β版非公開)