- お役立ち記事
- Enhancing Quality Management in Manufacturing by Implementing Poka-Yoke (Foolproofing)
Enhancing Quality Management in Manufacturing by Implementing Poka-Yoke (Foolproofing)
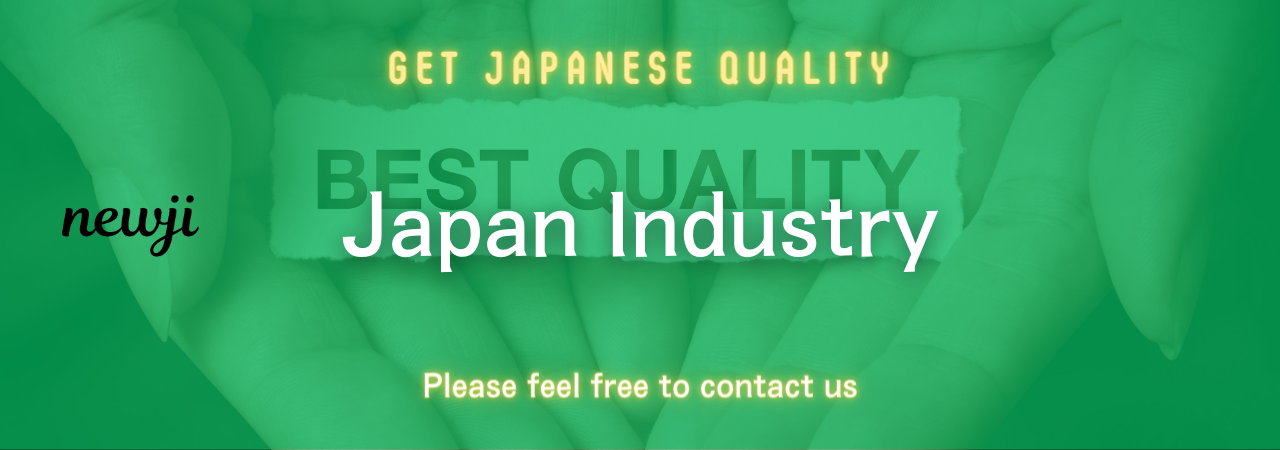
In today’s highly competitive manufacturing environment, maintaining high-quality standards is essential for success. One effective strategy to enhance quality management is by implementing poka-yoke, also known as foolproofing. This method helps prevent errors and defects in the production process, ensuring that products meet consistent quality standards.
目次
Understanding Poka-Yoke
Poka-yoke is a Japanese term that translates to “mistake-proofing” or “foolproofing.” It was introduced by Shigeo Shingo, a pioneer in the Toyota Production System. The concept behind poka-yoke is to design processes and systems that prevent errors or make them immediately evident so they can be corrected before causing defects.
The goal of poka-yoke is not to blame workers for mistakes but to create an environment where errors are less likely to occur. By embedding quality control measures into the process, manufacturers can catch mistakes early, reducing waste and increasing efficiency.
Types of Poka-Yoke
There are two primary types of poka-yoke techniques: prevention and detection.
Prevention
Prevention-based poka-yoke focuses on designing processes in such a way that errors are impossible to make. This could include design features that only allow components to be assembled in the correct way or systems that guide workers to perform tasks correctly.
For example, a device that ensures screws cannot be inserted unless aligned properly is a prevention-based poka-yoke. Such measures eliminate the chance of human error, greatly improving the quality of the final product.
Detection
Detection-based poka-yoke aims to identify errors as soon as they occur. This allows for immediate correction before the mistake can lead to defects in the product. An example of a detection-based poka-yoke is a sensor that stops a machine when a part is missing or incorrectly positioned.
Detection mechanisms are crucial in catching errors that prevention methods might miss, offering a secondary layer of defense against defects.
Benefits of Implementing Poka-Yoke
Implementing poka-yoke in manufacturing processes offers a range of benefits, including:
Improved Product Quality
By reducing the likelihood of errors, poka-yoke helps ensure that products meet high-quality standards consistently. This results in fewer defects and less rework, leading to higher customer satisfaction.
Increased Efficiency
Error prevention and quick detection reduce downtime and scrap rates. This means that resources are used more efficiently, leading to cost savings and faster production times.
Enhanced Safety
Some poka-yoke measures are designed to prevent hazardous situations, protecting workers and ensuring a safer working environment. For example, safety interlocks can ensure that machinery does not operate unless all safety guards are in place.
Cost Savings
By reducing defects and rework, poka-yoke leads to significant cost savings. Companies spend less on fixing errors and dealing with customer complaints, improving their bottom line.
Steps to Implement Poka-Yoke
To successfully integrate poka-yoke into your manufacturing processes, consider the following steps:
Identify Key Processes
Begin by identifying the critical processes that have the most significant impact on product quality. Focus on areas where errors are most likely to occur or have the most severe consequences.
Analyze Potential Errors
Conduct a thorough analysis of the potential errors that could occur in these processes. Understand the root causes of these errors and how they can impact the final product.
Design Poka-Yoke Solutions
Develop practical poka-yoke solutions tailored to the specific errors identified. Aim to create both prevention and detection mechanisms to cover all bases.
Implement and Test
Implement the poka-yoke measures in your production process and run tests to ensure they are effective. Make adjustments as necessary to optimize their performance.
Train Employees
Ensure that all employees are trained on the new poka-yoke measures. Educate them on the importance of these tools in maintaining product quality and safety.
Monitor and Improve
Continuously monitor the effectiveness of your poka-yoke measures and look for opportunities to improve. Regularly review your processes and update poka-yoke solutions as needed.
Real-World Examples of Poka-Yoke
Many successful manufacturing companies use poka-yoke principles to maintain high-quality standards. Here are a few examples:
Toyota
Toyota has long been a leader in applying poka-yoke techniques. One notable example is the use of color-coded components that ensure correct assembly. If parts are not correctly matched, the assembly process cannot continue, preventing errors from occurring.
Intel
Intel uses poka-yoke in the production of microprocessors. They employ test fixtures that automatically detect and reject defective units. This swift identification of errors helps maintain the overall quality of their products.
Ford
Ford employs poka-yoke in their vehicle manufacturing processes. For instance, they use sensors to ensure that each car’s door is properly aligned before welding. This prevents misalignment issues, which could compromise the vehicle’s structural integrity.
Challenges in Implementing Poka-Yoke
While poka-yoke offers significant advantages, there can be challenges in its implementation:
Initial Costs
Setting up poka-yoke mechanisms can require an initial investment in new equipment and training. However, these costs are typically offset by the long-term savings from reduced defects and increased efficiency.
Resistance to Change
Employees may be resistant to changes in their workflow. Effective communication and training are essential to gain their buy-in and help them understand the benefits of poka-yoke.
Complexity
In highly complex processes, identifying and designing effective poka-yoke solutions can be challenging. It may require a deep understanding of the process and innovative thinking to develop workable solutions.
Conclusion
Implementing poka-yoke is a powerful way to enhance quality management in manufacturing. By focusing on error prevention and detection, companies can produce high-quality products more consistently.
While there are challenges in implementation, the benefits of improved product quality, increased efficiency, enhanced safety, and cost savings make it a worthwhile investment. By following a systematic approach and continuously seeking improvements, manufacturers can leverage poka-yoke to gain a competitive edge in the market.
資料ダウンロード
QCD調達購買管理クラウド「newji」は、調達購買部門で必要なQCD管理全てを備えた、現場特化型兼クラウド型の今世紀最高の購買管理システムとなります。
ユーザー登録
調達購買業務の効率化だけでなく、システムを導入することで、コスト削減や製品・資材のステータス可視化のほか、属人化していた購買情報の共有化による内部不正防止や統制にも役立ちます。
NEWJI DX
製造業に特化したデジタルトランスフォーメーション(DX)の実現を目指す請負開発型のコンサルティングサービスです。AI、iPaaS、および先端の技術を駆使して、製造プロセスの効率化、業務効率化、チームワーク強化、コスト削減、品質向上を実現します。このサービスは、製造業の課題を深く理解し、それに対する最適なデジタルソリューションを提供することで、企業が持続的な成長とイノベーションを達成できるようサポートします。
オンライン講座
製造業、主に購買・調達部門にお勤めの方々に向けた情報を配信しております。
新任の方やベテランの方、管理職を対象とした幅広いコンテンツをご用意しております。
お問い合わせ
コストダウンが利益に直結する術だと理解していても、なかなか前に進めることができない状況。そんな時は、newjiのコストダウン自動化機能で大きく利益貢献しよう!
(Β版非公開)