- お役立ち記事
- “Enhancing Safety: Key Accident Prevention Strategies in Japanese Manufacturing”
月間76,176名の
製造業ご担当者様が閲覧しています*
*2025年3月31日現在のGoogle Analyticsのデータより
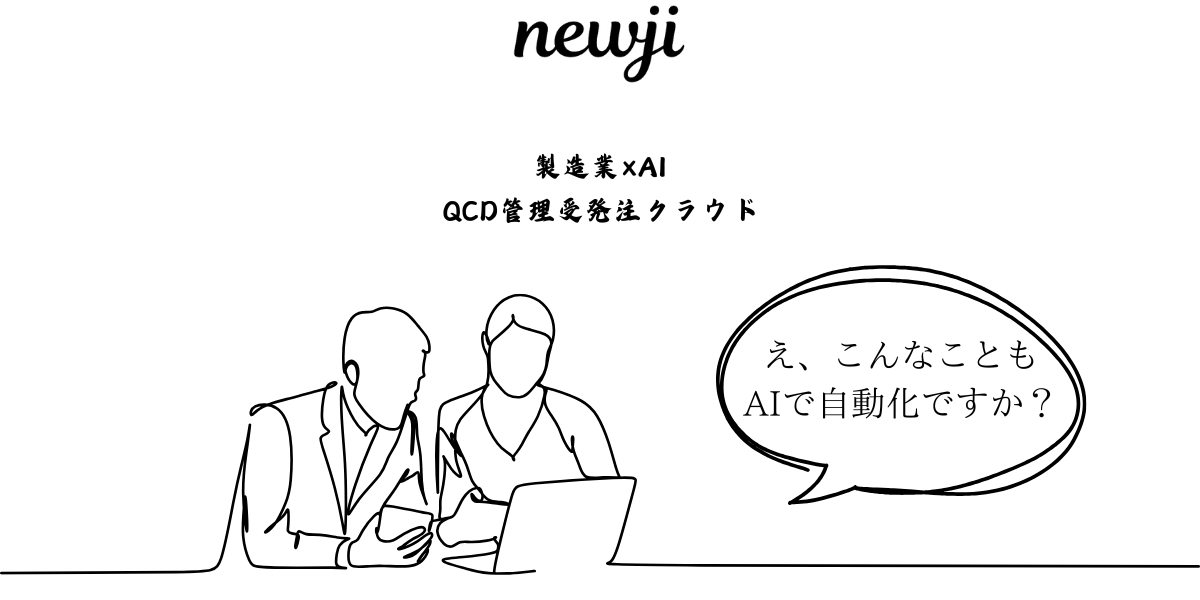
“Enhancing Safety: Key Accident Prevention Strategies in Japanese Manufacturing”
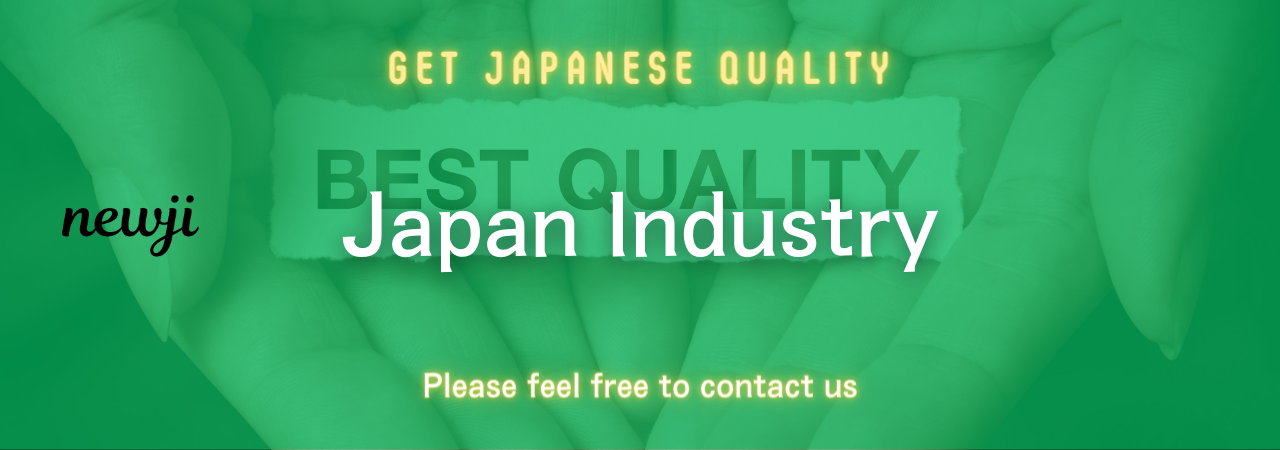
目次
Introduction to Safety in Japanese Manufacturing
Safety in manufacturing is a paramount concern worldwide, but it holds particular significance in Japanese manufacturing due to the industry’s emphasis on quality and efficiency. Japanese manufacturing companies are renowned for their meticulous attention to detail and commitment to creating safe working environments. This dedication not only protects employees but also enhances overall productivity and product quality. Understanding the key accident prevention strategies employed by Japanese manufacturers can provide valuable insights for companies seeking to improve their own safety protocols.
The Importance of Safety in Manufacturing
Safety in manufacturing is not merely a regulatory requirement but a fundamental aspect of operational excellence. A safe workplace reduces the risk of accidents, minimizes downtime, and lowers costs associated with injuries and lost productivity. Moreover, fostering a culture of safety contributes to employee morale and retention, as workers feel valued and protected. In Japanese manufacturing, safety is integrated into every aspect of the production process, reflecting the broader cultural values of respect and continuous improvement.
Key Accident Prevention Strategies Employed in Japanese Manufacturing
Japanese manufacturers implement a variety of strategies to prevent accidents and ensure workplace safety. These strategies are often interrelated, creating a comprehensive approach to safety management.
Implementing Lean Manufacturing
Lean manufacturing focuses on eliminating waste and optimizing processes. By streamlining operations, Japanese manufacturers reduce the chances of accidents caused by cluttered workspaces or inefficient workflows. Lean principles promote organization, clarity, and efficiency, all of which contribute to a safer working environment.
Standardized Work Procedures
Standardization is a cornerstone of Japanese manufacturing. Clearly defined work procedures ensure that every employee knows the exact steps to perform their tasks safely and efficiently. Standardized procedures reduce variability, minimize errors, and provide a reliable framework for training new employees, thereby enhancing overall safety.
Continuous Improvement (Kaizen)
Kaizen, or continuous improvement, encourages all employees to contribute to ongoing enhancements in processes and safety measures. By fostering an environment where suggestions for improvement are welcomed and implemented, Japanese manufacturers can identify potential hazards early and address them proactively.
Employee Training and Engagement
Comprehensive training programs are essential for maintaining high safety standards. In Japanese manufacturing, employees undergo regular training to stay updated on safety protocols and best practices. Additionally, engaging employees in safety initiatives empowers them to take ownership of their workplace safety and fosters a collective responsibility for accident prevention.
Use of Technology and Automation
Advanced technology and automation play significant roles in enhancing safety in Japanese manufacturing. Automated systems can perform hazardous tasks, reducing the exposure of workers to potential dangers. Additionally, technology such as sensors and monitoring systems can detect unsafe conditions in real-time, allowing for immediate corrective actions.
Safety Audits and Compliance
Regular safety audits are conducted to ensure compliance with both internal standards and external regulations. These audits help identify areas of improvement, ensure adherence to safety protocols, and maintain a high level of safety awareness throughout the organization.
Supplier Management and Quality Control
In procurement and purchasing, selecting reliable suppliers who adhere to strict safety standards is crucial. Japanese manufacturers often collaborate closely with their suppliers to ensure that all components and materials meet safety requirements. This collaboration extends to quality control processes, where rigorous inspections help prevent defects that could lead to accidents.
Risk Assessment and Management
Comprehensive risk assessments are conducted to identify potential hazards in the manufacturing process. By evaluating risks systematically, Japanese manufacturers can implement appropriate control measures to mitigate them. Risk management is an ongoing process, ensuring that safety measures remain effective as operations evolve.
Advantages of Japanese Safety Strategies
The safety strategies employed in Japanese manufacturing offer numerous advantages that contribute to the overall success of the organization.
Enhanced Productivity
A safe working environment reduces the likelihood of accidents and disruptions, leading to consistent productivity levels. Employees can focus more on their tasks without the constant worry of potential hazards, resulting in more efficient operations.
Improved Quality
Safety and quality are intertwined in Japanese manufacturing. By maintaining safe processes, manufacturers can ensure that products are made to the highest standards. Reducing accidents also minimizes the potential for defective products, enhancing overall quality.
Employee Morale and Retention
Prioritizing safety demonstrates that a company values its employees, which boosts morale and job satisfaction. High employee morale leads to better retention rates, as workers are more likely to stay with a company that prioritizes their well-being.
Regulatory Compliance
Adhering to strict safety protocols ensures compliance with local and international regulations. This compliance prevents legal issues and potential fines, safeguarding the company’s reputation and financial stability.
Challenges and Disadvantages
While Japanese safety strategies are highly effective, they are not without challenges and potential disadvantages.
High Implementation Costs
Implementing comprehensive safety measures can be costly. Investments in technology, training programs, and safety audits require significant financial resources, which may be a barrier for smaller manufacturers.
Resistance to Change
Introducing new safety protocols can sometimes meet resistance from employees accustomed to existing processes. Overcoming this resistance requires effective communication and ongoing training to demonstrate the benefits of the new strategies.
Complexity of Coordination
Coordinating safety measures across different departments and ensuring supplier compliance adds complexity to the manufacturing process. Managing these relationships and maintaining consistent safety standards can be challenging.
Potential for Overemphasis on Safety
While safety is crucial, an overemphasis on safety can potentially slow down production or stifle innovation. Balancing safety with efficiency and other operational goals is essential to maintain overall productivity and competitiveness.
Supplier Negotiation Techniques Related to Safety
Effective supplier negotiation is vital to ensure that all partners uphold the necessary safety standards. Japanese manufacturers employ several techniques to achieve this.
Building Long-term Relationships
Japanese business culture emphasizes long-term partnerships. By fostering strong relationships with suppliers, manufacturers can ensure ongoing collaboration and commitment to safety standards. Trust and mutual respect facilitate smoother negotiations and better adherence to safety protocols.
Setting Clear Expectations
Clearly communicating safety requirements and expectations from the outset helps prevent misunderstandings. Japanese manufacturers provide detailed specifications and guidelines to suppliers, ensuring that safety standards are understood and met.
Collaborative Improvement Efforts
Japanese manufacturers often work collaboratively with suppliers to improve safety measures. Sharing best practices and jointly addressing safety challenges fosters a cooperative environment where both parties benefit from enhanced safety.
Performance-Based Contracts
Incorporating safety performance metrics into contracts incentivizes suppliers to maintain high safety standards. Suppliers are rewarded for meeting or exceeding safety criteria, ensuring that safety remains a priority.
Regular Audits and Assessments
Conducting regular audits and assessments of suppliers’ safety practices helps maintain compliance and identify areas for improvement. These evaluations provide objective insights into suppliers’ adherence to safety standards and inform ongoing negotiations.
Market Conditions Affecting Safety Strategies
Various market conditions influence the implementation and effectiveness of safety strategies in Japanese manufacturing.
Globalization and Supply Chain Complexity
As supply chains become more global and complex, maintaining consistent safety standards across different regions becomes challenging. Manufacturers must navigate diverse regulatory environments and cultural differences, which can impact safety practices.
Technological Advancements
Rapid technological advancements offer new tools for enhancing safety but also require continuous adaptation. Keeping up with the latest technologies ensures that safety measures remain effective and up-to-date.
Economic Fluctuations
Economic conditions can impact the resources available for implementing safety measures. During economic downturns, manufacturers may face budget constraints that affect their ability to invest in safety improvements.
Regulatory Changes
Changes in safety regulations require manufacturers to stay informed and adapt their practices accordingly. Proactive compliance with evolving regulations helps prevent legal issues and maintain high safety standards.
Best Practices for Implementing Safety Strategies in Manufacturing
Adopting best practices is essential for effectively implementing safety strategies in manufacturing settings.
Leadership Commitment
Strong commitment from leadership is crucial for fostering a culture of safety. Leaders should actively promote safety initiatives and lead by example, demonstrating the importance of safety to all employees.
Comprehensive Training Programs
Investing in thorough training programs ensures that employees are well-versed in safety protocols and procedures. Regular training sessions keep safety knowledge current and reinforce the importance of adherence.
Employee Involvement
Engaging employees in safety initiatives encourages ownership and accountability. Involving workers in safety planning and decision-making leads to more effective and practical safety solutions.
Continuous Monitoring and Evaluation
Regularly monitoring safety performance and evaluating the effectiveness of safety measures helps identify areas for improvement. Continuous evaluation ensures that safety strategies remain relevant and effective over time.
Integration of Safety into Business Processes
Embedding safety into all aspects of business operations ensures that it is a core value rather than an afterthought. Integrating safety considerations into procurement, production, and other processes enhances overall safety management.
Use of Data and Analytics
Leveraging data and analytics provides valuable insights into safety performance and potential risks. Analyzing incident data and safety metrics helps in making informed decisions and proactively addressing safety challenges.
Collaboration with Industry Partners
Collaborating with industry partners and participating in safety networks can enhance knowledge sharing and innovation in safety practices. Learning from peers and adopting industry best practices strengthens overall safety efforts.
Conclusion
Enhancing safety in Japanese manufacturing involves a multifaceted approach that integrates lean manufacturing, standardized procedures, continuous improvement, and advanced technology. The emphasis on employee training, supplier management, and proactive risk assessment creates a robust safety culture that not only prevents accidents but also drives overall operational excellence. While challenges such as high implementation costs and the complexity of coordination exist, the advantages of improved productivity, quality, and employee morale make these strategies highly valuable. By adopting best practices and understanding the nuances of supplier negotiation and market conditions, manufacturers can effectively implement and sustain safety strategies that protect their workforce and enhance their competitive edge in the global market.
資料ダウンロード
QCD管理受発注クラウド「newji」は、受発注部門で必要なQCD管理全てを備えた、現場特化型兼クラウド型の今世紀最高の受発注管理システムとなります。
ユーザー登録
受発注業務の効率化だけでなく、システムを導入することで、コスト削減や製品・資材のステータス可視化のほか、属人化していた受発注情報の共有化による内部不正防止や統制にも役立ちます。
NEWJI DX
製造業に特化したデジタルトランスフォーメーション(DX)の実現を目指す請負開発型のコンサルティングサービスです。AI、iPaaS、および先端の技術を駆使して、製造プロセスの効率化、業務効率化、チームワーク強化、コスト削減、品質向上を実現します。このサービスは、製造業の課題を深く理解し、それに対する最適なデジタルソリューションを提供することで、企業が持続的な成長とイノベーションを達成できるようサポートします。
製造業ニュース解説
製造業、主に購買・調達部門にお勤めの方々に向けた情報を配信しております。
新任の方やベテランの方、管理職を対象とした幅広いコンテンツをご用意しております。
お問い合わせ
コストダウンが利益に直結する術だと理解していても、なかなか前に進めることができない状況。そんな時は、newjiのコストダウン自動化機能で大きく利益貢献しよう!
(β版非公開)