- お役立ち記事
- Enhancing Supplier Evaluation to Strengthen Supply Chains in Manufacturing
月間76,176名の
製造業ご担当者様が閲覧しています*
*2025年3月31日現在のGoogle Analyticsのデータより
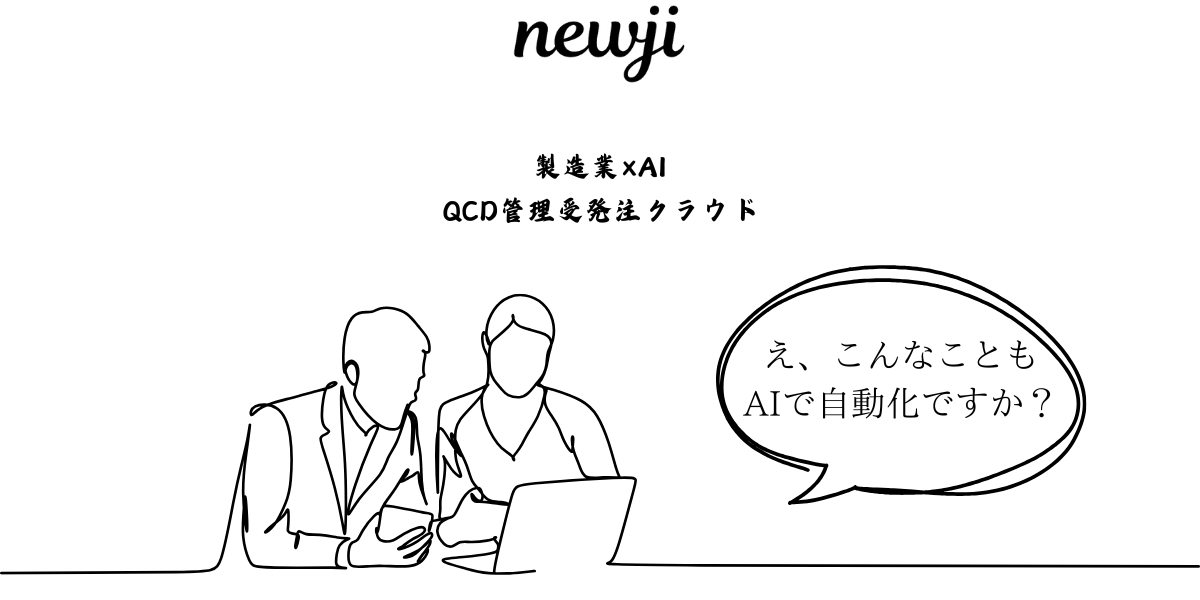
Enhancing Supplier Evaluation to Strengthen Supply Chains in Manufacturing
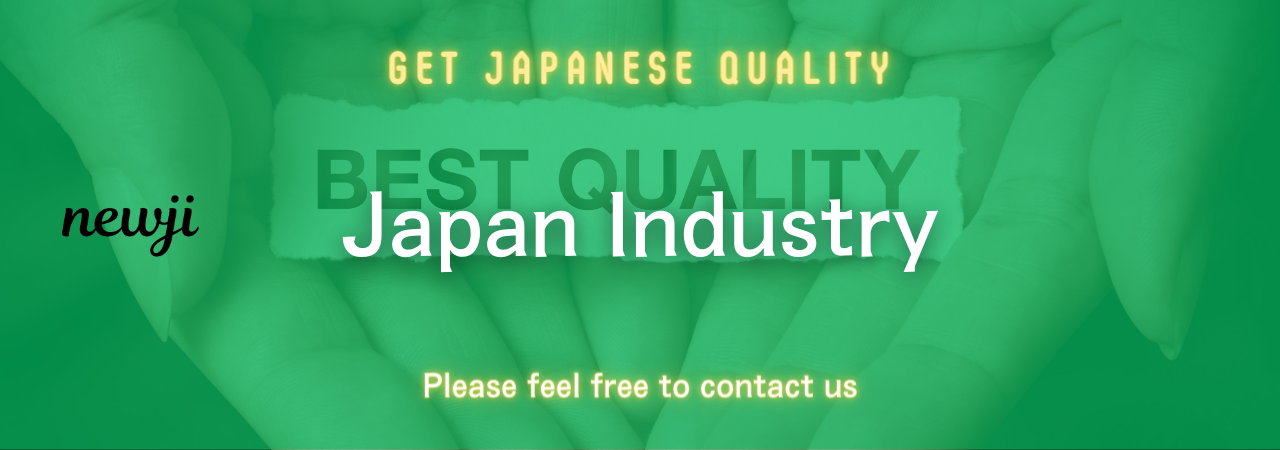
In today’s competitive manufacturing industry, companies are continually looking for ways to improve their operations and stay ahead of the competition. One crucial area that often requires attention is supplier evaluation. By effectively assessing and managing suppliers, manufacturers can ensure a stable and efficient supply chain, which is vital for delivering quality products on time.
目次
Understanding Supplier Evaluation
Supplier evaluation is the process of assessing and approving potential suppliers through various criteria. This evaluation ensures that the suppliers can meet the required standards and deliver goods consistently. A supplier evaluation typically includes examining aspects such as quality, reliability, cost, and delivery timelines.
Importance of Supplier Evaluation
Supplier evaluation is paramount for several reasons. Firstly, it helps identify suppliers who can consistently provide high-quality materials. Quality is integral in manufacturing, as any lapse can result in defective products that can harm a company’s reputation.
Secondly, supplier evaluation assesses the reliability of suppliers. It is crucial to know if a supplier can deliver goods on time and maintain consistency. Reliability in supply chains prevents delays and keeps production flowing smoothly.
Cost-effectiveness is another critical factor in supplier evaluation. It allows manufacturers to determine if they are getting the best value for their investment. While cheaper options may be appealing, it is essential to ensure costs do not compromise quality and reliability.
Key Factors in Supplier Evaluation
When evaluating suppliers, manufacturers need to focus on a few key factors. These factors ensure a comprehensive assessment that covers all crucial aspects of the supplier’s capabilities and performance.
Quality Standards
Adhering to high-quality standards is non-negotiable in the manufacturing industry. Manufacturers must verify that suppliers maintain stringent quality control measures. This can be done by reviewing certifications and conducting periodic audits.
Delivery Performance
Timely delivery is a critical component in maintaining an efficient supply chain. Manufacturers should assess a supplier’s historic delivery performance and their ability to meet deadlines. Consistent delays can lead to production halts and unmet customer expectations.
Cost Efficiency
While it is necessary to manage costs, manufacturers should aim for a balanced approach. The cheapest supplier may not always be the best choice if they compromise on quality or reliability. It’s essential to evaluate the total cost of partnership, including hidden costs.
Financial Stability
A supplier’s financial health is a good indicator of their long-term viability. Financially unstable suppliers might face challenges that affect their ability to deliver products consistently. Manufacturers should check the financial records and credit ratings of potential suppliers.
Technological Capabilities
In an era where technology is rapidly advancing, a supplier’s capacity to adapt and innovate is crucial. Manufacturers should evaluate whether suppliers use up-to-date technologies and whether they can scale their operations to meet increasing demands.
Steps to Conduct a Thorough Supplier Evaluation
Carrying out a thorough supplier evaluation requires a systematic approach. The following steps outline a clear process to ensure that all important aspects are covered.
Define Evaluation Criteria
The first step is to define what criteria will be used for evaluation. This involves deciding on the specific metrics that align with the company’s goals. Common criteria include quality, cost, delivery, and reliability.
Collect Data and Information
Gathering data is critical to the evaluation process. This can be done through supplier questionnaires, audits, and reviewing performance records. The aim is to collect as much relevant information as possible.
Analyze and Compare Suppliers
Once data is collected, it must be analyzed to make comparisons. Manufacturers should use quantitative methods to rate suppliers against each criterion. This helps in identifying the strengths and weaknesses of each supplier.
Conduct On-site Audits
On-site audits provide an opportunity to see the supplier’s operations firsthand. These audits help verify the information provided and assess the working environment, quality control processes, and workforce competence.
Establish a Feedback Loop
Post-evaluation, it is important to establish a feedback loop with suppliers. Communicating the findings and areas for improvement fosters a collaborative relationship. It helps suppliers understand expectations and work towards meeting them.
Review and Monitor Performance
Supplier evaluation doesn’t end once a supplier is approved. Continuous monitoring and periodic reviews are essential to ensure ongoing compliance and performance. Regular evaluations help in maintaining quality and identifying potential issues early on.
Benefits of Enhanced Supplier Evaluation
Improving supplier evaluation processes can bring numerous benefits to manufacturers.
Strengthened Supply Chain
A refined supplier evaluation process ensures that only reliable and capable suppliers are part of the supply chain. This strengthens the overall supply chain, making it more efficient and resilient to disruptions.
Cost Savings
By thoroughly evaluating suppliers, manufacturers can identify the most cost-effective options that do not compromise on quality. This results in significant cost savings and adds value to the overall operations.
Improved Product Quality
Ensuring that suppliers adhere to high-quality standards means that the raw materials and components used in manufacturing will be of superior quality. This directly translates to better final products.
Enhanced Supplier Relationships
A transparent and systematic supplier evaluation process fosters better relationships between manufacturers and suppliers. Clear communication and feedback mechanisms build trust and encourage long-term partnerships.
Risk Mitigation
Evaluating suppliers thoroughly helps in identifying potential risks early. This proactive approach allows manufacturers to mitigate risks before they escalate into major issues.
In conclusion, enhancing supplier evaluation processes is a strategic approach to strengthening supply chains in the manufacturing industry. By focusing on key factors such as quality, delivery, cost, financial stability, and technological capabilities, and by following a systematic evaluation procedure, manufacturers can ensure a reliable and efficient supply chain.
Continuous improvement and monitoring will further add value, leading to cost savings, improved product quality, and strengthened supplier relationships.
資料ダウンロード
QCD管理受発注クラウド「newji」は、受発注部門で必要なQCD管理全てを備えた、現場特化型兼クラウド型の今世紀最高の受発注管理システムとなります。
ユーザー登録
受発注業務の効率化だけでなく、システムを導入することで、コスト削減や製品・資材のステータス可視化のほか、属人化していた受発注情報の共有化による内部不正防止や統制にも役立ちます。
NEWJI DX
製造業に特化したデジタルトランスフォーメーション(DX)の実現を目指す請負開発型のコンサルティングサービスです。AI、iPaaS、および先端の技術を駆使して、製造プロセスの効率化、業務効率化、チームワーク強化、コスト削減、品質向上を実現します。このサービスは、製造業の課題を深く理解し、それに対する最適なデジタルソリューションを提供することで、企業が持続的な成長とイノベーションを達成できるようサポートします。
製造業ニュース解説
製造業、主に購買・調達部門にお勤めの方々に向けた情報を配信しております。
新任の方やベテランの方、管理職を対象とした幅広いコンテンツをご用意しております。
お問い合わせ
コストダウンが利益に直結する術だと理解していても、なかなか前に進めることができない状況。そんな時は、newjiのコストダウン自動化機能で大きく利益貢献しよう!
(β版非公開)