- お役立ち記事
- Ensuring Electrical Safety Through Insulation Resistance Testing
月間76,176名の
製造業ご担当者様が閲覧しています*
*2025年3月31日現在のGoogle Analyticsのデータより
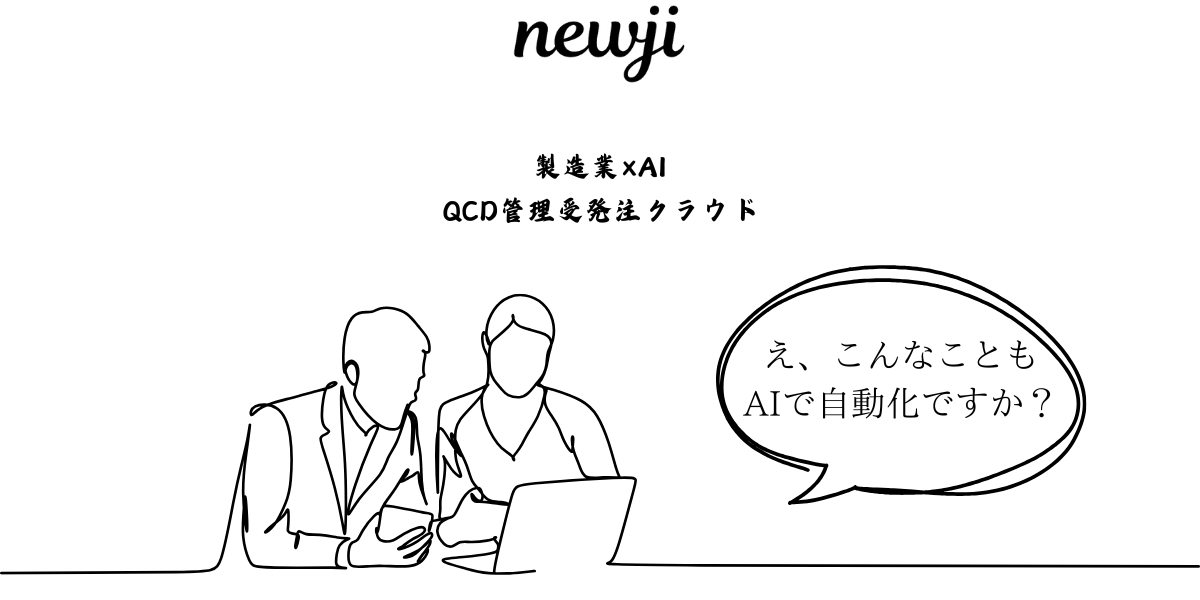
Ensuring Electrical Safety Through Insulation Resistance Testing
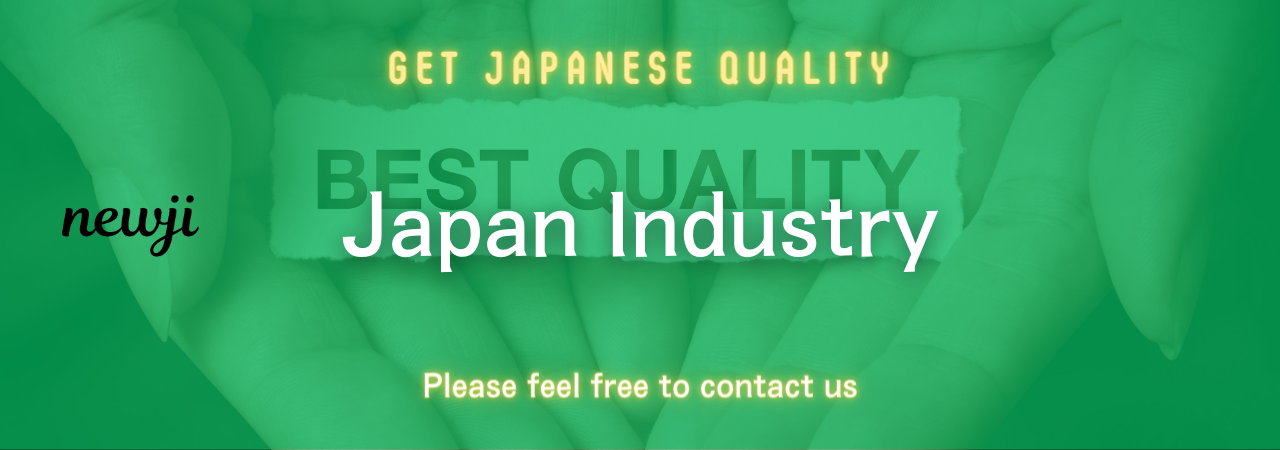
Ensuring electrical safety is crucial in both residential and commercial settings.
One of the most effective ways to maintain this safety is through insulation resistance testing.
This test helps to detect any potential electrical faults that could pose a danger.
In this article, we’ll delve into what insulation resistance testing is, why it’s important, and how it can be conducted for optimal electrical safety.
目次
What is Insulation Resistance Testing?
Insulation resistance testing is a diagnostic process used to measure the resistance of electrical insulation in wiring, motors, transformers, and other electrical equipment.
The test assesses the ability of the insulation to resist electrical flow.
In simpler terms, it checks whether the insulation is doing its job of preventing electricity from escaping the desired path.
The test is crucial in identifying faults in the insulation that could lead to leaks, short circuits, or even fires.
Why is Insulation Resistance Testing Important?
Prevention of Electrical Hazards
First and foremost, insulation resistance testing is essential for preventing electrical hazards.
Faulty insulation can lead to short circuits, fires, or electric shocks, posing significant risks to both property and human life.
By conducting regular tests, you can identify weaknesses in the insulation before they become critical issues.
Prolonging Equipment Life
This type of testing also helps to prolong the life of electrical equipment.
Insulation deterioration often goes unnoticed until it reaches a critical point.
Regular testing enables early detection, allowing for timely intervention and thereby extending the lifespan of your equipment.
Compliance with Safety Standards
Many industrial standards and regulations require regular insulation resistance testing to ensure workplace safety.
Failure to comply with these standards can result in penalties and increased risks of electrical hazards.
By adhering to these regulations, you not only ensure safety but also avoid potential legal issues.
Cost-Effective Maintenance
Regular testing can save you money in the long run.
By identifying issues early, you can avoid costly repairs and replacements.
Preventive maintenance is almost always less expensive than reactive repairs.
In addition, well-maintained equipment is generally more energy-efficient, resulting in lower operating costs.
How to Conduct Insulation Resistance Testing
Preparation
Before you start the test, it’s crucial to prepare properly.
Ensure that the equipment or system to be tested is powered down.
Disconnect any electrical loads and isolate the equipment.
Gather all necessary tools, including an insulation resistance tester, safety gear, and documentation for recording results.
Set Up the Tester
Connect the insulation resistance tester’s leads to the equipment or wiring to be tested.
The tester typically has two leads: one for the high-voltage output and one for the ground.
Ensure that connections are secure to get accurate readings.
Set the tester to the appropriate voltage level, which can vary depending on the equipment being tested.
Conduct the Test
Once everything is set up, you can initiate the test by pressing the start button on the tester.
The tester will apply a high voltage to the insulation and measure the resistance.
Observe the readings and compare them to the manufacturer’s specifications or industry standards.
A higher resistance value generally indicates good insulation, while a lower value suggests potential issues.
Interpret the Results
Interpreting the test results is crucial for identifying any faults.
A sudden drop in resistance or values significantly below the manufacturer’s specifications usually indicate degraded or faulty insulation.
Document all readings carefully and maintain records for future reference and compliance purposes.
Post-Test Actions
After completing the test, ensure you power down the tester and carefully disconnect the leads.
Re-evaluate the equipment and perform any necessary maintenance or repairs based on the test results.
Keep detailed records of all tests and actions taken to maintain a history of your equipment’s electrical health.
Common Issues and Solutions
Deteriorating Insulation
One of the most common issues identified through insulation resistance testing is deteriorating insulation.
This can happen due to age, environmental conditions, or mechanical damage.
In such cases, replacing or repairing the damaged insulation is essential to restore safety and functionality.
Moisture Intrusion
Moisture is another common culprit behind poor insulation resistance.
Water and other fluids can penetrate insulation, leading to a significant drop in resistance.
Drying the equipment, improving seals, or using moisture-resistant materials can help mitigate this issue.
Contamination
Dust, dirt, and other contaminants can also affect insulation performance.
Regular cleaning and proper maintenance can help to reduce this risk.
In some cases, using insulating materials with higher resistance to contamination might be advisable.
Best Practices for Insulation Resistance Testing
Frequent Testing
One best practice is to conduct insulation resistance testing regularly.
Depending on the equipment and its usage, this could be monthly, quarterly, or annually.
Frequent testing ensures timely detection of potential problems.
Calibrated Equipment
Always use calibrated and well-maintained testing equipment.
Inaccurate readings can lead to false conclusions, posing risks to both safety and efficiency.
Regularly calibrate your insulation resistance tester according to the manufacturer’s guidelines.
Training and Safety
Ensure that all personnel involved in insulation resistance testing are adequately trained.
They should understand how to use the tester correctly and interpret the results safely.
Personal protective equipment (PPE) such as gloves and goggles should always be used when conducting these tests.
Conclusion
Insulation resistance testing is a critical component in ensuring electrical safety in any environment.
By preventing hazards, prolonging equipment life, ensuring compliance with safety standards, and providing cost-effective maintenance, it offers numerous benefits.
Conducting these tests properly and interpreting the results accurately can help you maintain a safe, efficient, and compliant electrical system.
Make it a regular part of your maintenance routine to ensure ongoing electrical safety.
With the information provided, you can now make more informed decisions about the importance and implementation of insulation resistance testing.
Remember, safety first!
資料ダウンロード
QCD管理受発注クラウド「newji」は、受発注部門で必要なQCD管理全てを備えた、現場特化型兼クラウド型の今世紀最高の受発注管理システムとなります。
ユーザー登録
受発注業務の効率化だけでなく、システムを導入することで、コスト削減や製品・資材のステータス可視化のほか、属人化していた受発注情報の共有化による内部不正防止や統制にも役立ちます。
NEWJI DX
製造業に特化したデジタルトランスフォーメーション(DX)の実現を目指す請負開発型のコンサルティングサービスです。AI、iPaaS、および先端の技術を駆使して、製造プロセスの効率化、業務効率化、チームワーク強化、コスト削減、品質向上を実現します。このサービスは、製造業の課題を深く理解し、それに対する最適なデジタルソリューションを提供することで、企業が持続的な成長とイノベーションを達成できるようサポートします。
製造業ニュース解説
製造業、主に購買・調達部門にお勤めの方々に向けた情報を配信しております。
新任の方やベテランの方、管理職を対象とした幅広いコンテンツをご用意しております。
お問い合わせ
コストダウンが利益に直結する術だと理解していても、なかなか前に進めることができない状況。そんな時は、newjiのコストダウン自動化機能で大きく利益貢献しよう!
(β版非公開)