- お役立ち記事
- Ensuring Excellence: How Japan’s Manufacturing Industry Embraces GMP for Superior Quality Control
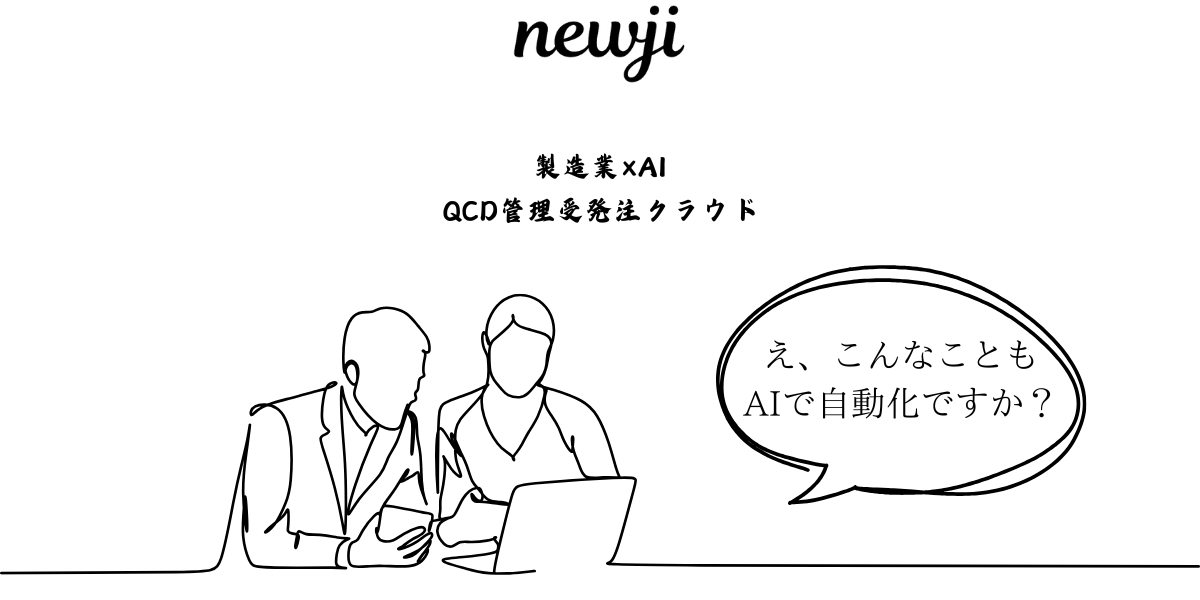
Ensuring Excellence: How Japan’s Manufacturing Industry Embraces GMP for Superior Quality Control
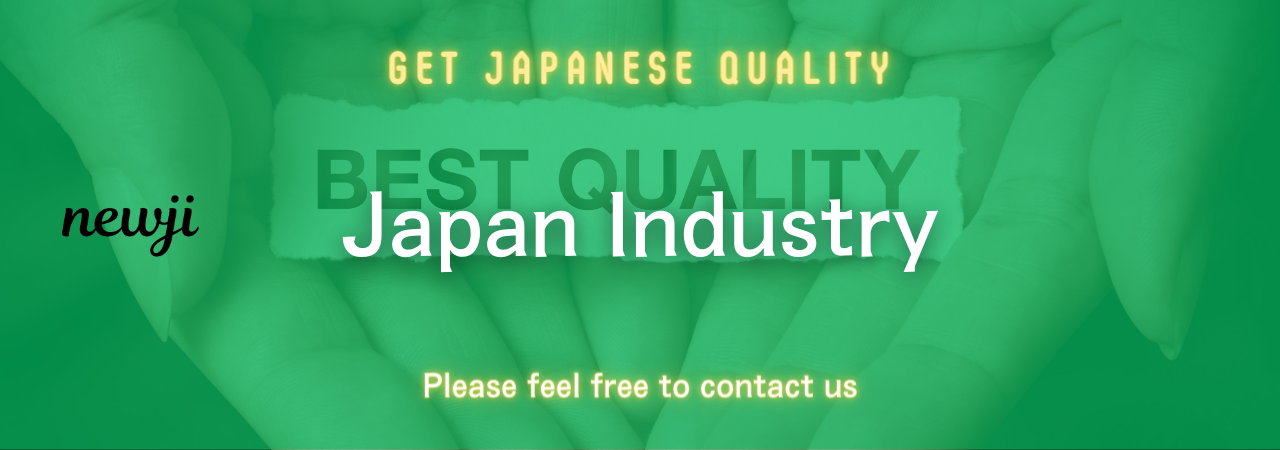
目次
Introduction
Japan’s manufacturing industry has long been revered for its commitment to quality and precision. Central to this reputation is the adoption of Good Manufacturing Practices (GMP), which ensures that products meet consistent standards of quality and safety. In the competitive landscape of global procurement and purchasing, understanding how Japan embraces GMP can provide significant advantages for international companies seeking superior quality control. This article delves into the intricacies of GMP in Japanese manufacturing, exploring its implications for procurement and purchasing, and offering insights into best practices for engaging with Japanese suppliers.
Understanding Good Manufacturing Practices (GMP)
Definition and Importance
Good Manufacturing Practices (GMP) encompass a set of guidelines and principles that ensure products are consistently produced and controlled according to quality standards. Originating in the pharmaceutical and food industries, GMP has expanded to various sectors, including electronics, automotive, and consumer goods. The primary objectives of GMP are to minimize risks involved in production that cannot be eliminated through testing the final product. This includes maintaining clean facilities, precise equipment calibration, meticulous record-keeping, and comprehensive employee training.
Adhering to GMP is crucial as it directly impacts product quality, safety, and efficacy. Non-compliance can lead to product recalls, regulatory penalties, and damage to a company’s reputation. For international buyers, understanding a supplier’s GMP compliance is essential to ensure that sourced products meet the required standards and reduce the risk of defects or safety issues.
GMP in Japanese Manufacturing Industry
Japan’s manufacturing sector has integrated GMP deeply into its operational framework. This commitment stems from a cultural emphasis on precision, continuous improvement (Kaizen), and a meticulous attention to detail. Japanese manufacturers often exceed baseline GMP requirements, incorporating additional quality control measures to ensure excellence.
The adoption of GMP in Japan is supported by robust regulatory frameworks and industry standards. Organizations such as the Japan Pharmaceutical Manufacturers Association (JPMA) and the Ministry of Health, Labour and Welfare (MHLW) play pivotal roles in enforcing GMP compliance. Furthermore, many Japanese companies pursue international certifications, such as ISO 9001, to demonstrate their adherence to global quality standards.
Japanese manufacturers leverage advanced technology and automation to maintain GMP standards. Cleanroom facilities, automated inspection systems, and comprehensive quality management software are commonplace, ensuring that every stage of production meets stringent quality criteria. This dedication not only enhances product quality but also fosters trust and reliability among international partners.
Procurement and Purchasing in Japanese Manufacturing
Role of GMP in Procurement
In the realm of procurement and purchasing, GMP serves as a critical criterion for supplier selection and evaluation. Companies sourcing components or finished products from Japan prioritize GMP compliance to ensure that their supply chain meets the necessary quality standards. This is particularly important in industries such as pharmaceuticals, electronics, and automotive, where product quality and safety are paramount.
GMP compliance signals that a supplier has established robust quality management systems and adheres to best practices in production. For procurement professionals, this reduces the risk of defects, ensures consistency in product quality, and facilitates smoother regulatory approvals in their home markets. Additionally, GMP-compliant suppliers are often more transparent and reliable, fostering long-term partnerships built on trust and quality assurance.
Advantages of Procuring from GMP-Compliant Japanese Suppliers
Procuring from GMP-compliant Japanese suppliers offers several advantages:
1. **High-Quality Products**: GMP ensures that products meet stringent quality and safety standards, reducing the likelihood of defects and recalls.
2. **Consistency and Reliability**: Japanese suppliers adhere to standardized processes, ensuring consistent product quality across different batches and production runs.
3. **Regulatory Compliance**: Suppliers compliant with GMP are better equipped to meet the regulatory requirements of various international markets, simplifying the approval process.
4. **Enhanced Reputation**: Partnering with reputable GMP-compliant suppliers enhances the buyer’s credibility and reliability in the market.
5. **Continuous Improvement**: The Japanese focus on Kaizen encourages suppliers to continuously improve their processes and products, leading to ongoing enhancements in quality and efficiency.
6. **Risk Mitigation**: GMP compliance reduces the risk of supply chain disruptions related to quality issues, ensuring a more stable and dependable supply.
Challenges and Disadvantages
While there are numerous benefits to procuring from GMP-compliant Japanese suppliers, there are also challenges to consider:
1. **Higher Costs**: The rigorous standards and advanced technologies required for GMP compliance can result in higher production costs, which may be reflected in the pricing of goods.
2. **Longer Lead Times**: Comprehensive quality control processes can extend production and delivery timelines, potentially affecting supply chain flexibility.
3. **Cultural and Communication Barriers**: Differences in language, business practices, and cultural norms can complicate negotiations and ongoing supplier relationships.
4. **Strict Compliance Requirements**: Maintaining GMP compliance necessitates continual monitoring and audits, which can be resource-intensive for both suppliers and buyers.
5. **Limited Supplier Pool**: The stringent requirements for GMP compliance reduce the number of eligible suppliers, potentially limiting sourcing options and increasing competition for top-tier partners.
Supplier Negotiation Techniques with Japanese Manufacturers
Building Relationships and Trust
Establishing strong relationships is fundamental when negotiating with Japanese manufacturers. The Japanese business culture places significant emphasis on trust, respect, and long-term partnerships. Building rapport involves demonstrating commitment, reliability, and a genuine interest in mutual success. Participating in face-to-face meetings, understanding cultural nuances, and showing respect for Japanese business etiquette can lay the foundation for successful negotiations.
Communication Strategies
Effective communication is key to successful negotiations. Given the language barrier, employing skilled translators or bilingual representatives can facilitate clearer discussions. It’s important to communicate expectations explicitly and ensure that both parties have a mutual understanding of terms and conditions. Active listening and patience are also crucial, as the Japanese may prefer thorough deliberation over quick decision-making.
Negotiating Quality Standards
When negotiating quality standards, it’s essential to align on GMP requirements and how they will be met. Clearly defining quality expectations, conducting regular quality audits, and setting up detailed quality agreements can help ensure that both parties are on the same page. Discussing mechanisms for continuous quality improvement and problem resolution can also strengthen the partnership.
Contractual Agreements and Compliance
Drafting comprehensive contractual agreements that outline GMP compliance requirements, quality standards, and performance metrics is vital. These contracts should also include clauses for regular audits, compliance checks, and penalties for non-compliance. Ensuring that both parties understand and agree to these terms can prevent misunderstandings and enforce accountability.
Market Conditions Affecting Japanese Manufacturing Procurement
Economic Factors
Japan’s economy significantly influences its manufacturing sector. Economic stability, currency fluctuations, and trade policies can impact procurement costs and supply chain dynamics. Understanding these economic factors is essential for anticipating changes in pricing, ensuring budget adherence, and managing financial risks associated with international procurement.
Technological Advancements
Japan is at the forefront of technological innovation, particularly in automation, robotics, and advanced manufacturing technologies. These advancements enhance productivity, product quality, and supply chain efficiency. Staying abreast of technological trends can help procurement professionals leverage cutting-edge solutions and collaborate with suppliers who utilize the latest innovations to maintain GMP standards.
Regulatory Environment
Global and local regulations influence procurement strategies. Compliance with international standards such as GMP, ISO, and sector-specific regulations is mandatory. Additionally, changes in trade agreements, import/export restrictions, and environmental regulations can affect sourcing decisions. Keeping informed about the regulatory landscape ensures that procurement practices remain compliant and adaptive to new requirements.
Global Supply Chain Dynamics
The interconnectedness of global supply chains means that disruptions in one region can have cascading effects worldwide. Factors such as geopolitical tensions, natural disasters, and pandemics can disrupt supply chains, affecting procurement from Japanese manufacturers. Diversifying suppliers, maintaining buffer stocks, and developing contingency plans are strategies to mitigate these risks and ensure supply chain resilience.
Best Practices for Procuring from Japanese GMP-Compliant Suppliers
Due Diligence and Supplier Evaluation
Conducting thorough due diligence is essential when selecting Japanese GMP-compliant suppliers. This involves evaluating their compliance certifications, reviewing quality management systems, and assessing their production capabilities. Site visits, third-party audits, and references from other international clients can provide valuable insights into a supplier’s reliability and quality standards.
Establishing Clear Quality Requirements
Clearly defining quality requirements from the outset ensures that suppliers understand expectations and can meet them consistently. This includes specifying GMP standards, product specifications, tolerances, and testing protocols. Comprehensive quality agreements that outline these requirements and the procedures for quality assurance help prevent misunderstandings and maintain product integrity.
Continuous Improvement and Feedback
Implementing a system of continuous improvement fosters a collaborative relationship with suppliers. Regular feedback on performance, sharing of best practices, and joint efforts to optimize processes can lead to enhancements in quality and efficiency. Encouraging open communication and a culture of continuous improvement aligns both parties towards common goals.
Leveraging Cultural Insights
Understanding Japanese business culture can significantly enhance procurement interactions. Respect for hierarchy, consensus-based decision-making, and the importance of maintaining harmony are key cultural elements to consider. Adapting negotiation and communication styles to align with Japanese norms can facilitate smoother interactions and strengthen partnerships.
Risk Management Strategies
Developing robust risk management strategies is crucial to mitigate potential disruptions in the supply chain. This includes identifying potential risks, assessing their impact, and implementing mitigation measures such as diversifying suppliers, maintaining safety stock, and establishing contingency plans. Regularly reviewing and updating risk management plans ensures ongoing preparedness for unforeseen challenges.
Conclusion
Japan’s unwavering commitment to Good Manufacturing Practices has cemented its position as a global leader in manufacturing excellence. For international companies engaged in procurement and purchasing, collaborating with GMP-compliant Japanese suppliers offers unparalleled advantages in product quality, reliability, and regulatory compliance. However, navigating the complexities of cultural differences, higher costs, and stringent compliance requirements necessitates a strategic and informed approach.
By understanding the foundational principles of GMP, leveraging effective negotiation techniques, staying attuned to market conditions, and adopting best practices in supplier management, procurement professionals can harness the strengths of Japan’s manufacturing industry. This not only ensures superior quality control but also fosters long-term, mutually beneficial partnerships that drive sustained success in the global marketplace.
資料ダウンロード
QCD調達購買管理クラウド「newji」は、調達購買部門で必要なQCD管理全てを備えた、現場特化型兼クラウド型の今世紀最高の購買管理システムとなります。
ユーザー登録
調達購買業務の効率化だけでなく、システムを導入することで、コスト削減や製品・資材のステータス可視化のほか、属人化していた購買情報の共有化による内部不正防止や統制にも役立ちます。
NEWJI DX
製造業に特化したデジタルトランスフォーメーション(DX)の実現を目指す請負開発型のコンサルティングサービスです。AI、iPaaS、および先端の技術を駆使して、製造プロセスの効率化、業務効率化、チームワーク強化、コスト削減、品質向上を実現します。このサービスは、製造業の課題を深く理解し、それに対する最適なデジタルソリューションを提供することで、企業が持続的な成長とイノベーションを達成できるようサポートします。
オンライン講座
製造業、主に購買・調達部門にお勤めの方々に向けた情報を配信しております。
新任の方やベテランの方、管理職を対象とした幅広いコンテンツをご用意しております。
お問い合わせ
コストダウンが利益に直結する術だと理解していても、なかなか前に進めることができない状況。そんな時は、newjiのコストダウン自動化機能で大きく利益貢献しよう!
(Β版非公開)