- お役立ち記事
- Ensuring Quality and Reliability in Welding for Major Companies
Ensuring Quality and Reliability in Welding for Major Companies
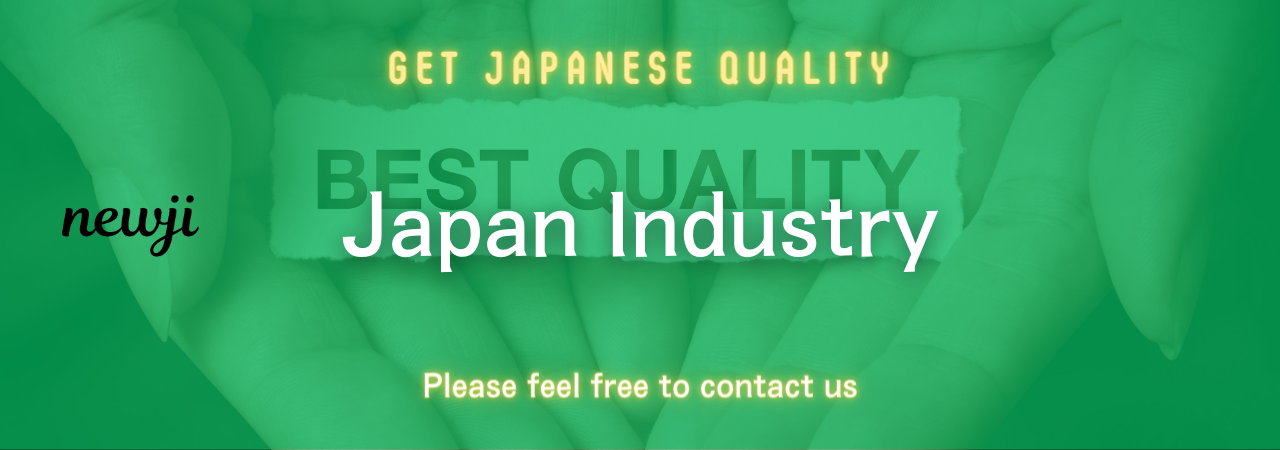
Welding is an essential process in many industries, providing the backbone for everything from skyscrapers to pipelines.
Ensuring the quality and reliability of welding is vital for major companies to maintain safety standards and product integrity.
This article delves into the techniques, best practices, and importance of quality welding.
目次
Why Welding Quality and Reliability Matter
In industries like construction, automotive, and aerospace, welding creates the strong joints necessary for safe and effective operation.
Poor welding practices can lead to structural failures, accidents, and costly repairs.
Companies must prioritize high-quality welding to ensure the durability and safety of their products.
Safety Concerns
Safety is a primary concern where welding is involved.
Flaws in welds can lead to catastrophic failures, endangering both workers and end-users.
By maintaining stringent quality control, companies can mitigate risks and ensure compliance with safety regulations.
Cost Implications
Substandard welding can lead to expensive reworks and repairs.
The financial burden extends beyond direct costs, including potential legal ramifications and damage to a company’s reputation.
Investing in high-quality welding upfront can save substantial resources in the long run.
Key Techniques for Ensuring Welding Quality
Achieving reliable and high-quality welds requires a combination of skilled labor, advanced technology, and rigorous testing.
Skilled Labor
Welders must be highly trained and experienced.
A well-trained welder understands the correct techniques and procedures, reducing the likelihood of errors.
Ongoing training ensures that welders are aware of the latest industry standards and technological advancements.
Advanced Welding Technology
Modern welding equipment and technology play a crucial role in achieving precision.
Automated welding systems can enhance consistency and reduce human error.
Technologies such as laser welding and friction stir welding offer superior control and quality compared to traditional methods.
Rigorous Testing and Inspection
Regular testing and inspection are vital to ensure the integrity of welds.
Non-destructive testing methods, like X-ray and ultrasonic testing, allow for thorough examinations without damaging the welded structures.
These tests help in identifying defects that might compromise the weld’s strength.
Best Practices for Welding Quality Control
Establishing and adhering to best practices is essential for maintaining welding quality.
Here are some recommended practices that major companies follow.
Standard Operating Procedures (SOPs)
Developing comprehensive SOPs for welding processes ensures consistency and quality.
These procedures provide detailed guidelines on material preparation, equipment setup, welding techniques, and post-weld treatments.
Adhering to SOPs minimizes variations that could affect weld quality.
Material Quality
Using high-quality materials is fundamental to achieving reliable welds.
Poor-quality materials can compromise the weld, regardless of the technique or equipment used.
Companies should source materials from reputable suppliers and conduct regular quality checks.
Environmental Control
The welding environment significantly impacts the weld quality.
Factors such as temperature, humidity, and cleanliness should be controlled to prevent contaminants from affecting the weld.
Proper ventilation is also crucial to ensure the safety of the welders and the integrity of the welded joints.
Case Studies of Quality Welding in Major Companies
Examining how major companies ensure welding quality can provide valuable insights and practical lessons.
Boeing: Precision in Aerospace
In the aerospace industry, precision and reliability are paramount.
Boeing employs advanced welding techniques and rigorous quality control measures to ensure every weld meets stringent standards.
Non-destructive testing is a routine part of their quality assurance process, ensuring that components can withstand the stresses of flight.
ExxonMobil: Reliability in the Oil and Gas Industry
ExxonMobil relies on welding to construct and maintain pipelines and refineries.
To guarantee the reliability of their welds, they implement comprehensive training programs and advanced welding technologies.
Regular inspections and maintenance schedules help them address potential issues before they escalate, ensuring uninterrupted operations.
Tesla: Innovation in Automotive Manufacturing
Tesla has revolutionized the automotive industry with its innovative production techniques.
They utilize robotic welding systems to achieve consistent and high-quality welds.
By integrating automation into their manufacturing process, Tesla has been able to maintain high standards while increasing production efficiency.
The Future of Welding
The welding industry continues to evolve with technological advancements.
The future promises even greater precision, efficiency, and safety in welding practices.
Automation and Robotics
The integration of automation and robotics in welding processes is set to increase.
Automated systems reduce human error and increase consistency, leading to higher quality welds.
Robots can perform tasks that are dangerous or difficult for humans, improving overall safety.
Advanced Materials and Techniques
The development of new materials and welding techniques will further enhance weld quality.
For instance, additive manufacturing techniques, like 3D printing, are being integrated with welding to create complex structures with high precision.
These advancements will expand the possibilities for what can be achieved with welding.
Enhanced Training Programs
As technology evolves, so will the training programs for welders.
Virtual reality (VR) and augmented reality (AR) are being used to provide immersive training experiences.
These tools help trainees to practice welding techniques in a controlled environment, improving their skills before they work on actual projects.
Ensuring quality and reliability in welding is crucial for major companies to maintain safety, reduce costs, and uphold their reputation.
Through skilled labor, advanced technology, and rigorous quality control measures, companies can achieve high standards in their welding practices.
As the industry progresses, continued innovations and best practices will further enhance the reliability and quality of welding processes.
資料ダウンロード
QCD調達購買管理クラウド「newji」は、調達購買部門で必要なQCD管理全てを備えた、現場特化型兼クラウド型の今世紀最高の購買管理システムとなります。
ユーザー登録
調達購買業務の効率化だけでなく、システムを導入することで、コスト削減や製品・資材のステータス可視化のほか、属人化していた購買情報の共有化による内部不正防止や統制にも役立ちます。
NEWJI DX
製造業に特化したデジタルトランスフォーメーション(DX)の実現を目指す請負開発型のコンサルティングサービスです。AI、iPaaS、および先端の技術を駆使して、製造プロセスの効率化、業務効率化、チームワーク強化、コスト削減、品質向上を実現します。このサービスは、製造業の課題を深く理解し、それに対する最適なデジタルソリューションを提供することで、企業が持続的な成長とイノベーションを達成できるようサポートします。
オンライン講座
製造業、主に購買・調達部門にお勤めの方々に向けた情報を配信しております。
新任の方やベテランの方、管理職を対象とした幅広いコンテンツをご用意しております。
お問い合わせ
コストダウンが利益に直結する術だと理解していても、なかなか前に進めることができない状況。そんな時は、newjiのコストダウン自動化機能で大きく利益貢献しよう!
(Β版非公開)