- お役立ち記事
- Ensuring Quality in OEM Easel Procurement
Ensuring Quality in OEM Easel Procurement
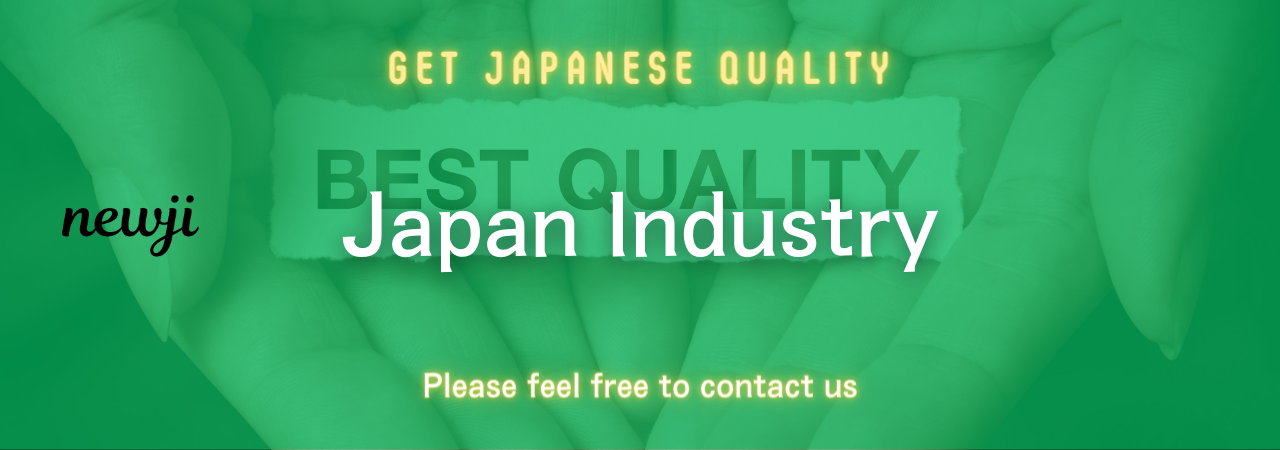
When it comes to procuring OEM easels, maintaining high-quality standards is crucial.
OEM, or Original Equipment Manufacturer, provides easels that often serve diverse industries, from education to professional art studios.
By ensuring quality in procurement, you can ensure that the end-users have a dependable and functional product.
In this article, we’ll cover various aspects of OEM easel procurement, emphasizing quality assurance.
目次
Understanding OEM Easels
OEM easels are designed and manufactured by one company but sold under another company’s branding.
This allows businesses to offer customized products that meet their specific requirements while benefiting from economies of scale.
However, this setup necessitates stringent quality control measures to ensure that the final product aligns with the specified standards.
What to Look for in Quality OEM Easels
When procuring OEM easels, several factors determine their quality:
1. **Material**: The choice of material can significantly impact the durability and functionality of the easel.
Higher-quality woods like oak or premium aluminum can enhance longevity.
Review material specifications carefully.
2. **Design**: A well-designed easel should be stable and adjustable.
Look for features that facilitate ease of use, such as height adjustability and tilting mechanisms.
3. **Finish**: The finish should be smooth and aesthetically pleasing.
This not only adds to the easel’s appeal but also ensures there are no rough edges that could harm the user.
4. **Compatibility**: Ensure the easel is compatible with the intended use, whether it is for classroom settings, professional studios, or presentations.
Setting Quality Benchmarks
To maintain high standards, it is imperative to set clear quality benchmarks.
These benchmarks act as a reference point during the procurement and inspection phases.
Material Inspection
Begin by creating detailed criteria for the materials used in the easels.
Include specifics such as wood type, metal grade, and any additional components.
Regularly inspect incoming materials to verify compliance with these standards.
Manufacturing Process
The manufacturing process should be closely monitored to prevent any deviations from the approved design and material specifications.
Regular audits and third-party inspections can help ensure that the production line maintains consistent quality.
Finished Product Checks
Before an easel is approved for distribution, it should undergo rigorous testing.
Check for structural integrity, stability, and finish quality.
For instance, a wobbling easel or one with a chipped finish should automatically fail the quality check.
Supplier Relationships
Quality in OEM easel procurement is also highly dependent on your relationship with the suppliers.
Engaging with a reliable supplier can streamline the quality assurance process.
Choosing the Right Supplier
Begin by researching potential suppliers.
Look for companies with a proven track record in manufacturing high-quality easels.
Check reviews, ask for samples, and even visit their manufacturing facilities if possible.
Establishing Clear Contracts
Your contract with the supplier should clearly outline the quality expectations.
Include detailed specifications, agreed benchmarks, and penalty clauses for non-compliance.
This sets a clear standard from the outset.
Regular Communication
Maintain open and regular communication with your supplier.
This helps promptly address any issues that may arise and ensures that both parties are aligned on quality expectations.
The Role of Technology
Incorporating technology in quality assurance processes can significantly enhance the reliability of your OEM easels.
Automated Testing
Invest in automated testing equipment that can carry out detailed inspections on the easels.
This ensures consistency and accuracy in quality checks.
Data Analytics
Utilize data analytics to track quality trends and identify recurring issues.
This enables you to address root causes more efficiently.
Supply Chain Management Software
Use supply chain management software to oversee the entire procurement process.
This helps in tracking materials, adhering to timelines, and ensuring overall quality.
Cost Versus Quality
A common challenge in procurement is balancing cost with quality.
However, prioritizing quality can lead to long-term savings by reducing product returns and customer complaints.
Understanding the Trade-Offs
While lower-cost options might seem appealing, they often come with hidden costs, such as repairs, replacements, and potential damage to your brand’s reputation.
It is crucial to understand these trade-offs and make informed decisions.
Investing in Quality
Consider quality an investment rather than an expense.
High-quality easels tend to have longer lifespans and better user satisfaction, which translates to lower costs over time.
Feedback Mechanisms
Establishing feedback mechanisms allows you to gather valuable insights from end-users that can be used to further improve quality.
Customer Feedback
Encourage customers to provide feedback on their experience with the easels.
This information can pinpoint specific areas for improvement or confirm that existing measures are effective.
Internal Reviews
Conduct regular internal reviews involving all stakeholders in the procurement process.
These reviews should focus on identifying areas for improvement in quality assurance measures.
Training and Development
Ensure that everyone involved in the procurement process is well-trained in quality assurance protocols.
Workshops and Training Sessions
Organize regular workshops and training sessions for your procurement team.
This helps them stay updated on the best practices and emerging trends in quality assurance.
Continuous Improvement
Encourage a culture of continuous improvement.
Regularly review and update quality protocols based on new knowledge and technologies.
Conclusion
Ensuring quality in OEM easel procurement involves meticulous attention to materials, manufacturing processes, and supplier relationships.
By setting clear benchmarks, leveraging technology, and prioritizing customer feedback, businesses can secure high-quality easels that meet their specific needs.
In the long run, investing in quality not only enhances customer satisfaction but also contributes to overall cost savings and brand reputation.
資料ダウンロード
QCD調達購買管理クラウド「newji」は、調達購買部門で必要なQCD管理全てを備えた、現場特化型兼クラウド型の今世紀最高の購買管理システムとなります。
ユーザー登録
調達購買業務の効率化だけでなく、システムを導入することで、コスト削減や製品・資材のステータス可視化のほか、属人化していた購買情報の共有化による内部不正防止や統制にも役立ちます。
NEWJI DX
製造業に特化したデジタルトランスフォーメーション(DX)の実現を目指す請負開発型のコンサルティングサービスです。AI、iPaaS、および先端の技術を駆使して、製造プロセスの効率化、業務効率化、チームワーク強化、コスト削減、品質向上を実現します。このサービスは、製造業の課題を深く理解し、それに対する最適なデジタルソリューションを提供することで、企業が持続的な成長とイノベーションを達成できるようサポートします。
オンライン講座
製造業、主に購買・調達部門にお勤めの方々に向けた情報を配信しております。
新任の方やベテランの方、管理職を対象とした幅広いコンテンツをご用意しております。
お問い合わせ
コストダウンが利益に直結する術だと理解していても、なかなか前に進めることができない状況。そんな時は、newjiのコストダウン自動化機能で大きく利益貢献しよう!
(Β版非公開)