- お役立ち記事
- Ensuring Safety and Reliability in OEM Manufacturing of AED Devices
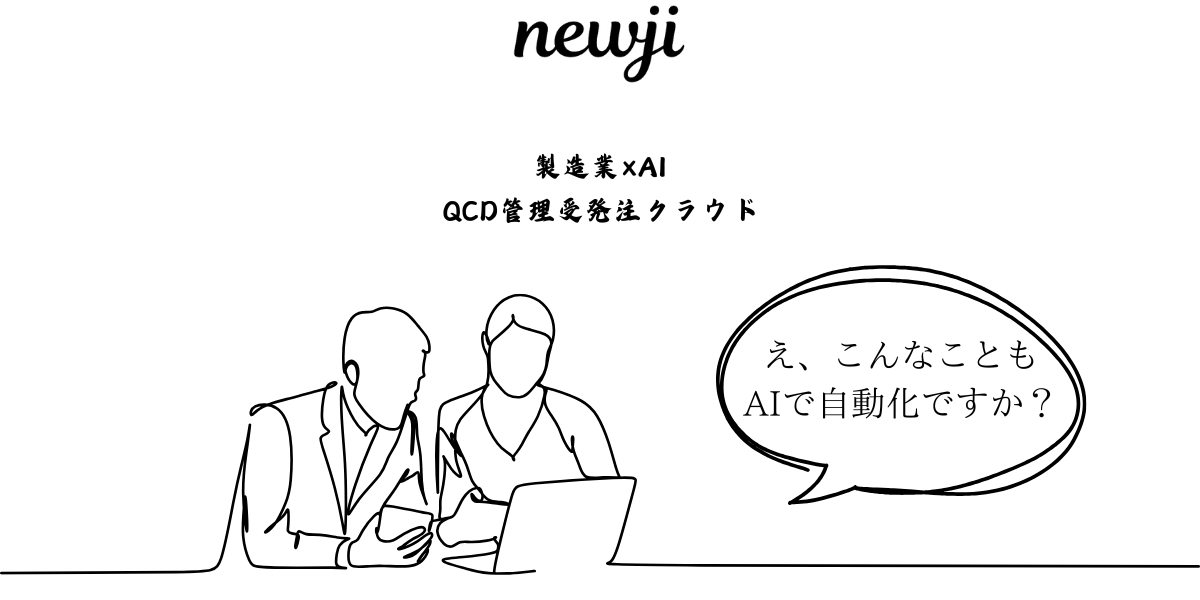
Ensuring Safety and Reliability in OEM Manufacturing of AED Devices
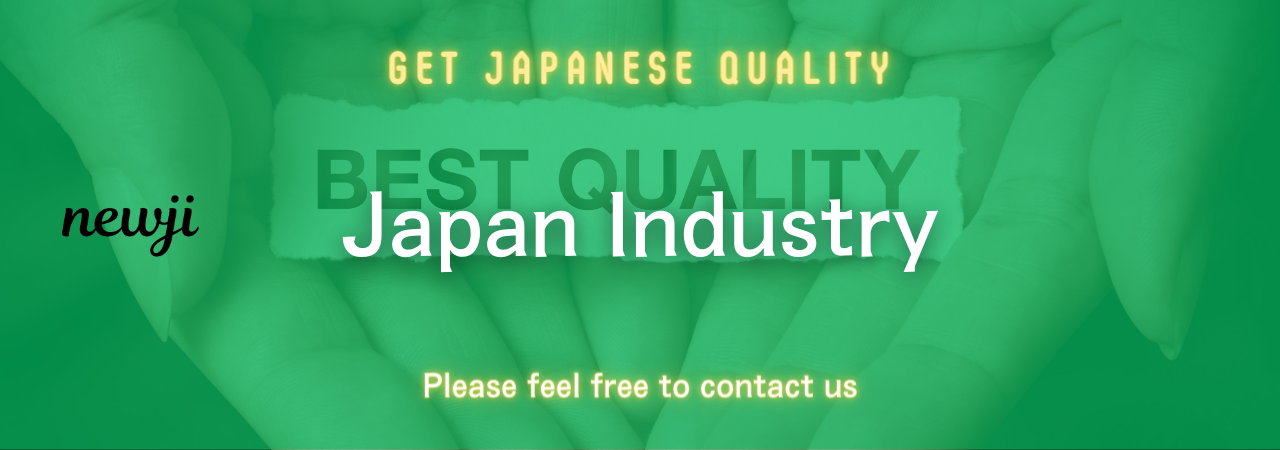
The demand for Automated External Defibrillators (AEDs) continues to grow as public awareness around sudden cardiac arrest increases.
Original Equipment Manufacturer (OEM) companies play a critical role in ensuring that these lifesaving devices are produced with the highest safety and reliability standards.
This article delves into the key aspects that OEMs must consider to maintain the safety and reliability of AED devices.
目次
Understanding OEM Manufacturing of AED Devices
OEM manufacturing involves producing components or complete products that are then marketed under another company’s brand.
In the case of AEDs, this means that the manufacturer creates these devices based on specific guidelines, ensuring that they meet all the required standards and regulations.
The responsibility for the safety and reliability of these devices starts with the OEM manufacturer.
The Importance of Safety in AED Manufacturing
Safety is paramount in AED manufacturing.
These devices are often used in high-stress, emergency situations where every second counts.
Any malfunction or failure could mean the difference between life and death.
Therefore, OEM manufacturers must adhere to rigorous safety standards throughout the production process.
Regulatory Compliance
Ensuring regulatory compliance is one of the first steps in maintaining safety.
OEM manufacturers must comply with guidelines set by regulatory bodies like the FDA in the United States, CE marking in Europe, and similar entities around the world.
These guidelines cover various aspects of manufacturing, including material use, testing procedures, and quality control measures.
Compliance ensures that the AED devices are safe for use and meet international health and safety standards.
The Role of Testing in Ensuring Reliability
Reliable AEDs are crucial, as they are potential lifesavers.
OEM manufacturers must implement stringent testing protocols at every stage of production to ensure the reliability of these devices.
Initial Design and Prototyping
The first stage of testing begins with the design and prototyping phase.
Engineers must design AEDs to function correctly under various conditions.
Prototype models undergo various evaluations to ensure they meet design specifications and can perform reliably in real-world situations.
Component Testing
After the initial design stage, each component used in manufacturing the AED undergoes thorough testing.
Components such as batteries, circuit boards, and electrodes must meet specific performance standards.
Testing each part individually ensures that every element of the AED functions correctly and is reliable.
Software Validation
Many modern AEDs incorporate software to perform diagnostic checks, deliver the shock, and provide user instructions.
Therefore, software validation is a crucial part of the testing process.
OEM manufacturers need to test the software extensively to ensure it runs smoothly and without errors in an emergency.
Final Product Testing
The last stage of testing involves the final product.
OEM manufacturers must test the assembled AEDs under various simulated real-world conditions to ensure they function correctly.
This includes verifying that the device can deliver the necessary shock, perform diagnostic checks, and guide the user through the rescue process.
Final product testing helps identify any defects or issues before the AEDs are released to the market.
Quality Control Throughout the Manufacturing Process
Maintaining high-quality control standards throughout the manufacturing process is essential for ensuring the safety and reliability of AEDs.
Material Selection
Selecting the right materials is the first step in ensuring product quality.
OEM manufacturers need to use materials that are durable, safe, and comply with regulatory requirements.
Quality control checks during material selection help prevent issues later in the production process.
Manufacturing Process Control
Implementing strict process control measures during manufacturing is vital.
OEM manufacturers should have detailed production plans and protocols, including step-by-step procedures for assembling the AEDs.
Frequent inspections and quality control checks should be performed throughout the production process to identify any deviations from the set standards.
Post-Production Quality Assurance
Once manufacturing is complete, post-production quality assurance measures are necessary.
This includes conducting final inspections, functional tests, and verifying that all regulatory requirements have been met.
Any issues identified during post-production quality assurance need to be addressed before the AEDs are distributed.
Training and Certification for OEM Personnel
Training and certifying OEM personnel involved in AED manufacturing is also crucial.
Properly trained staff can adhere to safety and quality standards more effectively.
Comprehensive Training Programs
OEM manufacturers should develop comprehensive training programs that cover all aspects of AED manufacturing.
This includes training on the latest regulatory requirements, quality control procedures, and testing protocols.
Regular updates and refresher courses can help keep personnel informed about the latest industry standards and best practices.
Certification and Continuing Education
Certifying OEM personnel ensures they have the necessary skills and knowledge to perform their tasks effectively.
Continuing education programs can help personnel stay updated with the latest advancements in AED technology and manufacturing processes.
By investing in personnel training and certification, OEM manufacturers can maintain high standards of safety and reliability in their AED devices.
Conclusion
Ensuring the safety and reliability of AED devices in OEM manufacturing is a multifaceted process.
From adhering to regulatory compliance and rigorous testing protocols to maintaining stringent quality control measures and investing in personnel training, OEM manufacturers play a critical role.
By focusing on these key aspects, they can guarantee that their AEDs are reliable, safe, and ready to save lives in emergency situations.
資料ダウンロード
QCD調達購買管理クラウド「newji」は、調達購買部門で必要なQCD管理全てを備えた、現場特化型兼クラウド型の今世紀最高の購買管理システムとなります。
ユーザー登録
調達購買業務の効率化だけでなく、システムを導入することで、コスト削減や製品・資材のステータス可視化のほか、属人化していた購買情報の共有化による内部不正防止や統制にも役立ちます。
NEWJI DX
製造業に特化したデジタルトランスフォーメーション(DX)の実現を目指す請負開発型のコンサルティングサービスです。AI、iPaaS、および先端の技術を駆使して、製造プロセスの効率化、業務効率化、チームワーク強化、コスト削減、品質向上を実現します。このサービスは、製造業の課題を深く理解し、それに対する最適なデジタルソリューションを提供することで、企業が持続的な成長とイノベーションを達成できるようサポートします。
オンライン講座
製造業、主に購買・調達部門にお勤めの方々に向けた情報を配信しております。
新任の方やベテランの方、管理職を対象とした幅広いコンテンツをご用意しております。
お問い合わせ
コストダウンが利益に直結する術だと理解していても、なかなか前に進めることができない状況。そんな時は、newjiのコストダウン自動化機能で大きく利益貢献しよう!
(Β版非公開)