- お役立ち記事
- Ensuring the Reliability of Electronic Devices with Burn-In Testing
月間76,176名の
製造業ご担当者様が閲覧しています*
*2025年3月31日現在のGoogle Analyticsのデータより
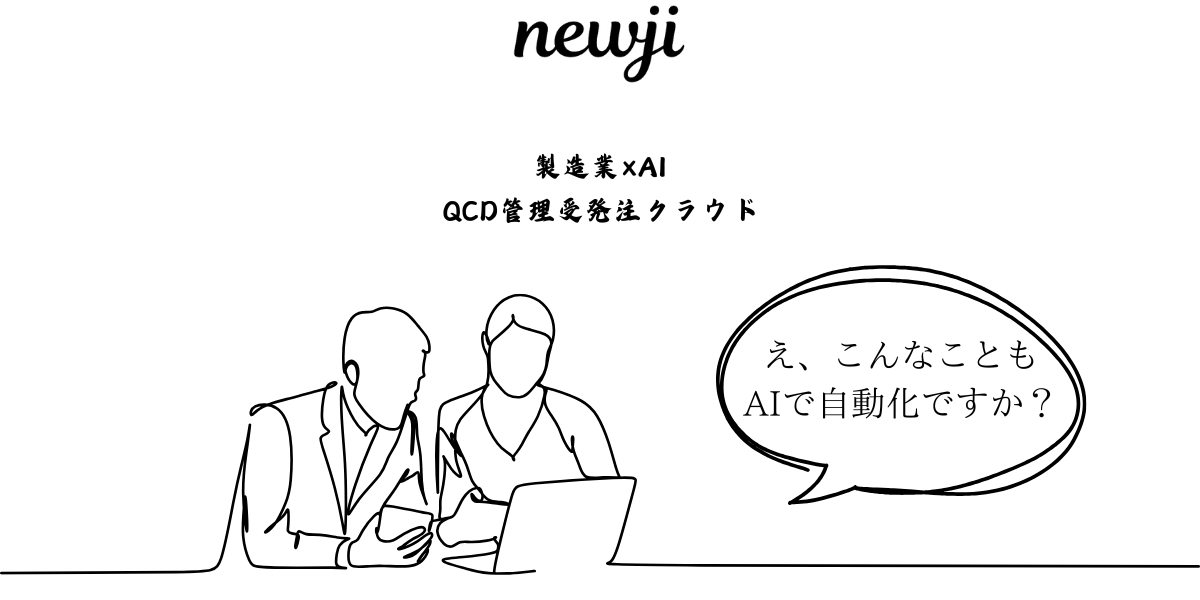
Ensuring the Reliability of Electronic Devices with Burn-In Testing
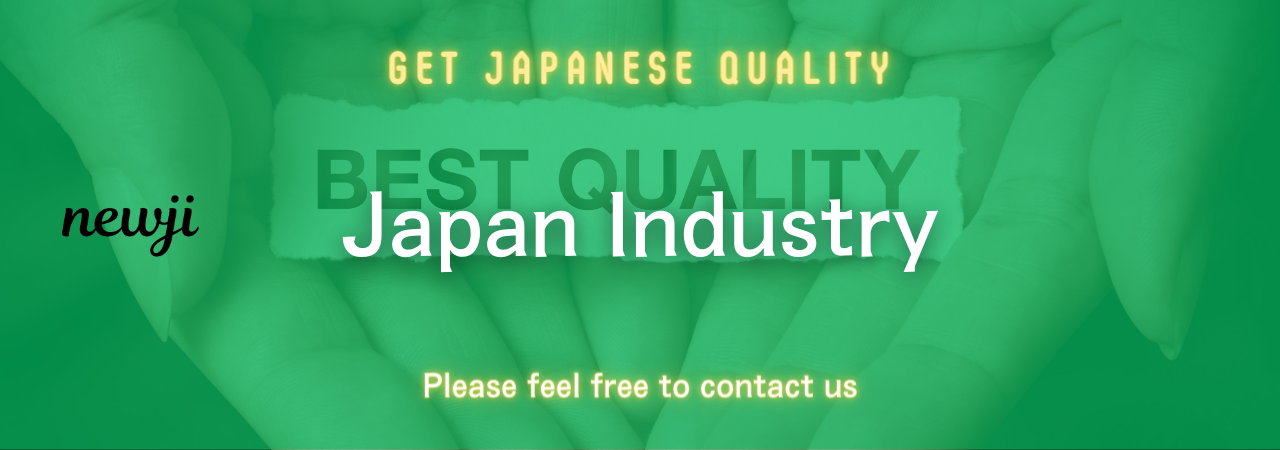
Electronic devices play a significant role in our daily lives, aiding in communication, productivity, and entertainment. As their importance grows, so does the need to ensure their reliability and performance. One of the most effective methods used in the industry to guarantee the durability of electronic devices is burn-in testing.
目次
What is Burn-In Testing?
Burn-in testing is a process designed to detect early failures in electronic devices by exposing them to extreme operating conditions. The primary goal is to push the components beyond their regular operating limits to identify potential defects. This process helps in weeding out early failures, ensuring that the devices shipped to customers are reliable and free from manufacturing defects.
Why is Burn-In Testing Important?
Electronic devices are expected to function flawlessly right out of the box. However, manufacturing defects, component flaws, and other issues can lead to early failures. Burn-in testing helps in identifying and eliminating these weak components before they reach the end user.
Increasing Product Reliability
The reliability of a product is paramount for both manufacturers and consumers. Continuous failures can lead to customer dissatisfaction and damage a brand’s reputation. By implementing burn-in testing, manufacturers can assure a higher level of reliability, decreasing the likelihood of product returns and warranties.
Identifying Flaws Before They Escalate
Early detection of flaws is critical in preventing long-term damage or failures. Burn-in testing accelerates the aging process of components, enabling engineers to observe how devices behave under stress. This allows for timely interventions, reducing the risk of malfunctions once the product is deployed.
Cost Savings
While burn-in testing may seem like an additional expense, it can lead to significant cost savings in the long run. By identifying defects early, companies can avoid the high costs associated with recalls, repairs, and lost customer trust. Ultimately, a small investment in testing can lead to substantial financial benefits.
How Does Burn-In Testing Work?
The burn-in testing process can vary depending on the type of electronic device and the specific requirements of the manufacturer. However, the general principles remain the same. Here’s a breakdown of how it typically works.
Setting Up the Test Environment
Firstly, the devices are placed in a controlled environment where temperature, humidity, and other conditions are strictly monitored. This environment is often more extreme than normal operating conditions to push the devices to their limits.
Operational Stress
The devices are then subjected to continuous operation. This involves running the device at full capacity to simulate real-world usage. By doing so, potential failures can be identified more quickly.
Monitoring and Data Collection
Throughout the testing period, various parameters like voltage, temperature, and response times are recorded. These data points help in identifying trends and any signs of distress within the components.
Post-Test Analysis
Once the testing phase is complete, the collected data is thoroughly analyzed. Any devices that show signs of failure are inspected, and the root cause of the problem is determined. This information is invaluable for improving the manufacturing process and enhancing product design.
Applications of Burn-In Testing
Burn-in testing is essential across various industries where electronic devices are a critical component. Below are some key applications.
Consumer Electronics
Smartphones, laptops, and other consumer electronics undergo burn-in testing to ensure they can handle the rigors of everyday use. Given the high expectations of modern consumers, any failure can result in significant dissatisfaction and brand damage.
Automotive Industry
Vehicles today are heavily reliant on electronics for everything from engine control to in-car entertainment systems. These components must be extremely reliable, as failures can lead to severe consequences. Burn-in testing ensures that only the most robust components make it into vehicles.
Aerospace and Defense
In aerospace and defense, reliability is non-negotiable. Burn-in testing helps in verifying that electronic components can withstand the extreme conditions they will face in these critical applications. The margin for error is extremely slim, making rigorous testing essential.
Medical Devices
Medical devices are lifesaving tools that must function without fail. Burn-in testing in the medical field ensures that devices such as pacemakers, diagnostic equipment, and other critical tools are reliable and safe for use.
Challenges in Burn-In Testing
While burn-in testing is highly effective, it’s not without its challenges. Here are some common issues faced during the process.
Testing Duration
One of the main challenges is the duration of the testing process. Depending on the complexity and intended usage of the device, burn-in testing can take from several hours to a few weeks. This extended time frame can impact production schedules and time-to-market.
Resource Allocation
Burn-in testing requires significant resources, including specialized equipment and environmental chambers. These resources must be efficiently managed to ensure timely and thorough testing.
Interpreting Results
Collecting data is one thing; interpreting it correctly is another. Engineers must carefully analyze the data to distinguish between actual failures and anomalies. Misinterpretation can lead to either overlooking defects or rejecting good components, both of which are undesirable outcomes.
The Future of Burn-In Testing
Advancements in technology continue to shape the future of burn-in testing. Automated systems and AI are making it easier to conduct comprehensive tests more efficiently. These innovations help in reducing testing time while increasing accuracy.
Additionally, as electronic devices become more complex, the need for rigorous testing methodologies like burn-in will only grow. Ensuring reliability in an ever-evolving technological landscape will remain a top priority for manufacturers.
Burn-in testing remains an essential practice for ensuring the reliability of electronic devices. By subjecting components to extreme conditions, manufacturers can identify and eliminate potential failures before products reach consumers. As technology advances, the methods and tools used for burn-in testing will continue to evolve, helping to ensure that the electronic devices we rely on remain dependable and efficient.
資料ダウンロード
QCD管理受発注クラウド「newji」は、受発注部門で必要なQCD管理全てを備えた、現場特化型兼クラウド型の今世紀最高の受発注管理システムとなります。
ユーザー登録
受発注業務の効率化だけでなく、システムを導入することで、コスト削減や製品・資材のステータス可視化のほか、属人化していた受発注情報の共有化による内部不正防止や統制にも役立ちます。
NEWJI DX
製造業に特化したデジタルトランスフォーメーション(DX)の実現を目指す請負開発型のコンサルティングサービスです。AI、iPaaS、および先端の技術を駆使して、製造プロセスの効率化、業務効率化、チームワーク強化、コスト削減、品質向上を実現します。このサービスは、製造業の課題を深く理解し、それに対する最適なデジタルソリューションを提供することで、企業が持続的な成長とイノベーションを達成できるようサポートします。
製造業ニュース解説
製造業、主に購買・調達部門にお勤めの方々に向けた情報を配信しております。
新任の方やベテランの方、管理職を対象とした幅広いコンテンツをご用意しております。
お問い合わせ
コストダウンが利益に直結する術だと理解していても、なかなか前に進めることができない状況。そんな時は、newjiのコストダウン自動化機能で大きく利益貢献しよう!
(β版非公開)