- お役立ち記事
- Ensuring Workplace Safety Through Environmental Measurement
Ensuring Workplace Safety Through Environmental Measurement
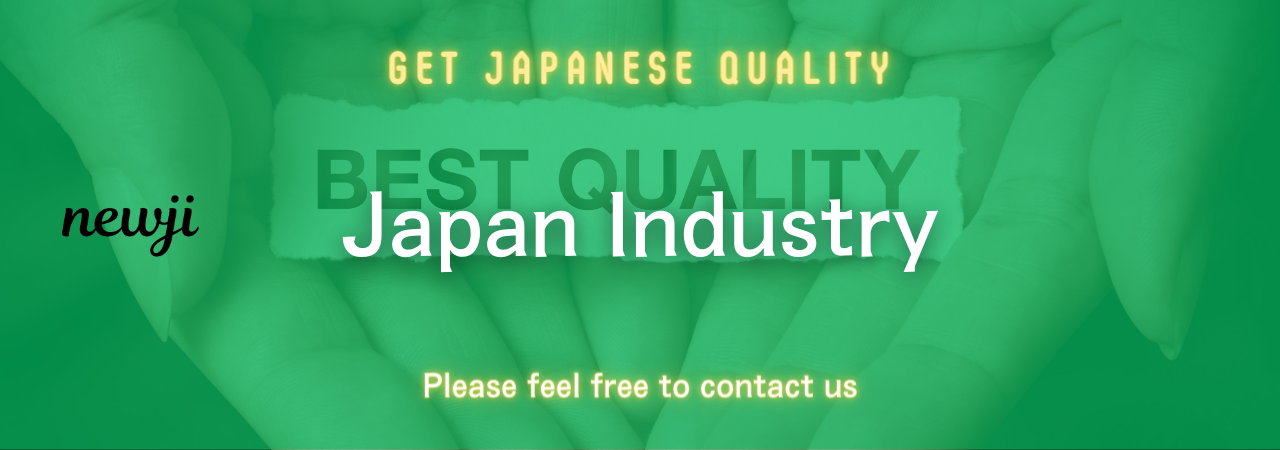
Ensuring a safe work environment is crucial for the health and well-being of employees.
One key aspect of maintaining safety in the workplace is through environmental measurement.
This practice involves assessing various factors in the work setting to identify and mitigate potential hazards.
By understanding and managing these elements, employers can create a safer and more productive work environment.
目次
Understanding Environmental Measurement
Environmental measurement refers to the process of collecting data about different physical, chemical, and biological elements in a work area.
This may include air quality, noise levels, vibration, lighting, and exposure to hazardous substances.
The goal is to evaluate these factors, understand their impacts, and implement measures to control any risks identified.
Air Quality
Air quality is a critical component of a healthy workplace.
Poor air quality can lead to several health issues, such as respiratory problems, allergies, and even severe conditions like asthma.
To ensure good air quality, regular monitoring of pollutants like dust, fumes, and gases is essential.
Employers can use various tools, such as air sampling pumps and gas detectors, to measure these pollutants.
Once potential hazards are identified, steps like improving ventilation, using air purifiers, or changing work processes can be taken to enhance air quality.
Noise Levels
Excessive noise in the workplace can lead to hearing loss, increased stress, and reduced productivity.
Measuring noise levels involves using sound level meters to identify areas with potentially harmful noise exposure.
Standards and guidelines by organizations like the Occupational Safety and Health Administration (OSHA) provide limits for safe noise levels.
If noise levels exceed these limits, employers can implement control measures, such as using sound-dampening materials, providing ear protection, or redesigning the workspace to minimize noise.
Vibration
Workplace vibration can come from machinery, tools, or equipment and can cause health issues like hand-arm vibration syndrome (HAVS) or whole-body vibration (WBV).
Monitoring vibration levels involves using devices like accelerometers to assess the intensity and frequency of vibrations.
If measurements indicate a risk, employers can take actions such as using vibration-dampening equipment, maintaining machinery properly, and giving workers appropriate breaks to reduce exposure.
Lighting
Proper lighting is essential for both safety and efficiency in the workplace.
Insufficient or excessive lighting can cause eye strain, headaches, and increase the risk of accidents.
Measuring lighting levels involves using light meters to ensure that all areas of the workplace are adequately illuminated according to the tasks performed there.
Employers should also consider factors like glare and reflections, which can affect visibility.
Adjusting lighting fixtures, using appropriate lighting for specific tasks, and ensuring regular maintenance of lighting systems can help maintain optimal lighting conditions.
Chemical Exposure
Many workplaces involve the use of chemicals that can pose significant health risks if not properly managed.
Regular environmental measurement includes monitoring the presence and concentration of hazardous chemicals to ensure they are within safe limits.
Methods such as gas chromatography or mass spectrometry can be used to detect and quantify chemical exposures.
Implementing safety protocols, providing proper personal protective equipment (PPE), and conducting regular training on handling chemicals can help minimize risks.
Benefits of Environmental Measurement
Conducting regular environmental measurements in the workplace offers numerous benefits.
Improved Health and Safety
The primary benefit is the enhancement of health and safety for employees.
By identifying and controlling environmental hazards, employers can prevent accidents, injuries, and long-term health issues.
Increased Productivity
A safe and comfortable work environment boosts employee morale and productivity.
When workers are healthy and feel safe, they are more likely to perform better and be more engaged in their tasks.
Regulatory Compliance
Regular environmental measurement helps organizations comply with health and safety regulations.
Failure to adhere to these regulations can result in legal consequences and financial penalties.
Cost Savings
Investing in environmental measurement and safety measures can lead to cost savings in the long run.
Preventing accidents and health issues reduces costs associated with medical treatments, workers’ compensation claims, and loss of productivity due to sick leave.
Enhanced Reputation
A commitment to workplace safety enhances an organization’s reputation.
It shows that the company values its employees’ well-being, which can attract top talent and foster trust among clients and partners.
Implementing an Effective Environmental Measurement Program
Creating and maintaining an effective environmental measurement program requires careful planning and execution.
Assess the Workplace
Begin by conducting a thorough assessment of the workplace to identify potential hazards.
This includes evaluating all areas where employees work, including offices, production floors, and storage spaces.
Set Objectives
Define clear objectives for the environmental measurement program.
Determine what factors will be measured, how often measurements will be taken, and what methods will be used.
Use the Right Tools
Select appropriate tools and equipment for measuring different environmental factors.
Ensure that these tools are regularly calibrated and maintained for accurate measurements.
Train Employees
Provide training for employees responsible for conducting measurements.
They should be knowledgeable about the tools and techniques used and understand how to interpret results.
Take Action
Based on the measurement results, implement necessary control measures to mitigate identified risks.
This may involve changes in processes, equipment, or work practices.
Review and Improve
Regularly review the environmental measurement program to ensure its effectiveness.
Make improvements based on feedback, new regulations, or advancements in measurement technology.
Environmental measurement is a vital practice for ensuring workplace safety and health.
By regularly assessing and managing air quality, noise levels, vibration, lighting, and chemical exposure, employers can create a safe and productive work environment.
This practice not only improves employee well-being but also offers benefits like increased productivity, regulatory compliance, cost savings, and an enhanced reputation.
Implementing a robust environmental measurement program with clear objectives, proper tools, employee training, and regular reviews will help organizations maintain a safe and healthy workplace.
資料ダウンロード
QCD調達購買管理クラウド「newji」は、調達購買部門で必要なQCD管理全てを備えた、現場特化型兼クラウド型の今世紀最高の購買管理システムとなります。
ユーザー登録
調達購買業務の効率化だけでなく、システムを導入することで、コスト削減や製品・資材のステータス可視化のほか、属人化していた購買情報の共有化による内部不正防止や統制にも役立ちます。
NEWJI DX
製造業に特化したデジタルトランスフォーメーション(DX)の実現を目指す請負開発型のコンサルティングサービスです。AI、iPaaS、および先端の技術を駆使して、製造プロセスの効率化、業務効率化、チームワーク強化、コスト削減、品質向上を実現します。このサービスは、製造業の課題を深く理解し、それに対する最適なデジタルソリューションを提供することで、企業が持続的な成長とイノベーションを達成できるようサポートします。
オンライン講座
製造業、主に購買・調達部門にお勤めの方々に向けた情報を配信しております。
新任の方やベテランの方、管理職を対象とした幅広いコンテンツをご用意しております。
お問い合わせ
コストダウンが利益に直結する術だと理解していても、なかなか前に進めることができない状況。そんな時は、newjiのコストダウン自動化機能で大きく利益貢献しよう!
(Β版非公開)