- お役立ち記事
- Equipment diagnosis technology using digital twin and its application to remaining life prediction
月間76,176名の
製造業ご担当者様が閲覧しています*
*2025年3月31日現在のGoogle Analyticsのデータより
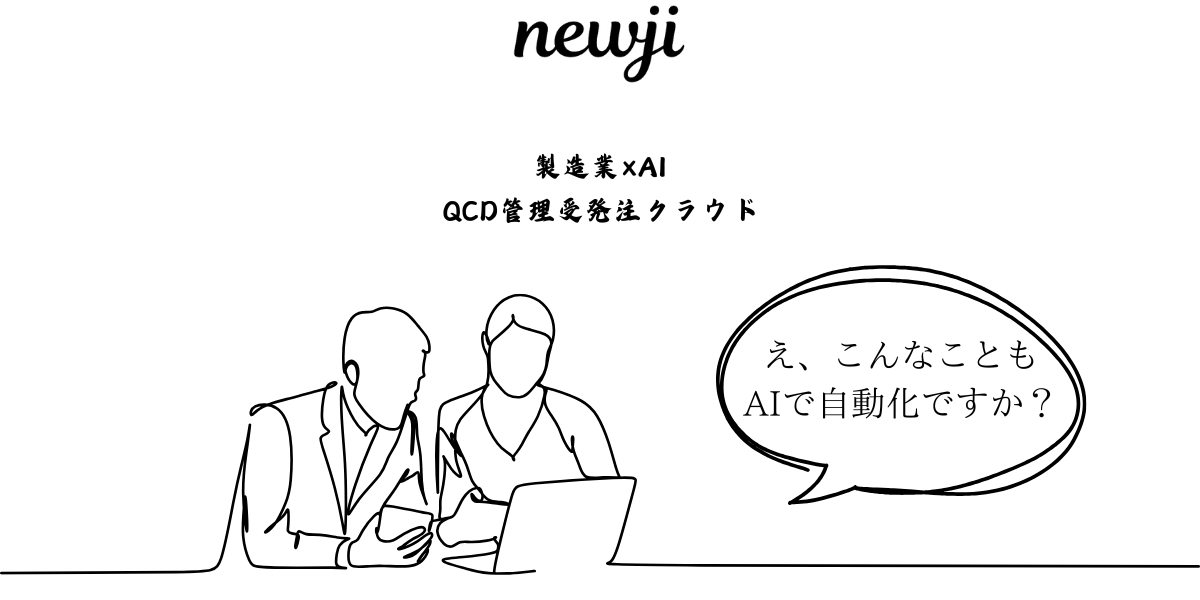
Equipment diagnosis technology using digital twin and its application to remaining life prediction
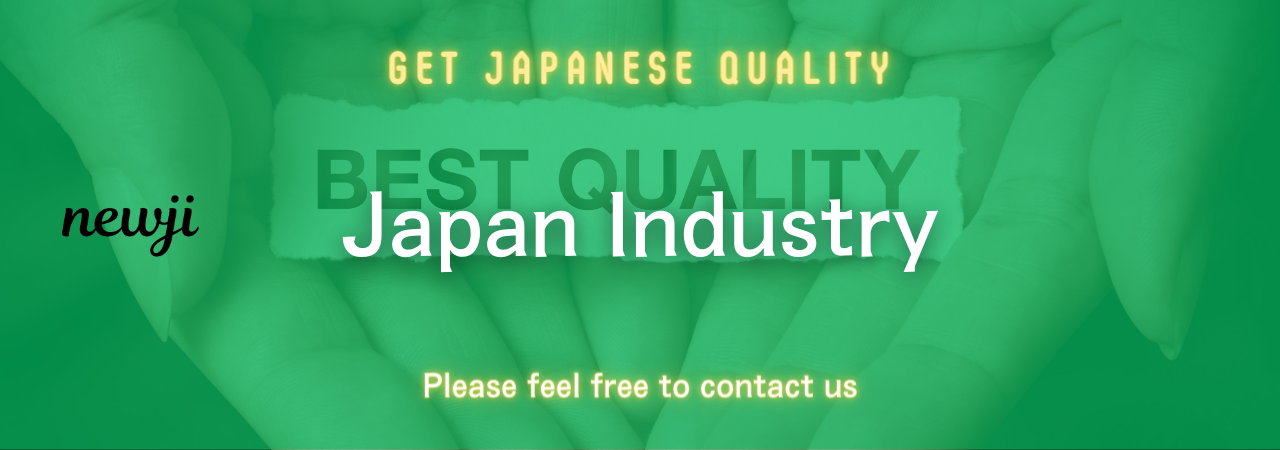
目次
Understanding Digital Twins in Equipment Diagnosis
Digital twin technology has emerged as a revolutionary tool in the field of equipment diagnostics.
By creating a virtual model of a physical asset, a digital twin allows engineers and technicians to monitor and analyze the performance, maintenance, and even predict the future state of the equipment.
This powerful technology is transforming traditional equipment management processes, enhancing decision-making, and improving operational efficiency.
The core idea behind a digital twin involves integrating real-time data from sensors and other devices installed on the equipment.
This data is then used to simulate the equipment’s behavior and identify any potential issues before they become critical.
The concept of a digital twin is increasingly being adopted across various industries, including manufacturing, aerospace, automotive, and healthcare, to name just a few.
The Role of Digital Twins in Equipment Diagnosis
Digital twins play a crucial role in equipment diagnostics by providing a detailed visualization of the equipment’s current state.
This visualization aids in quickly identifying any performance deviations or anomalies.
One of the significant advantages of digital twin technology is its ability to perform sophisticated analyses and predictions, enabling proactive maintenance rather than reactive fixes.
In traditional equipment diagnosis, determining the root cause of a malfunction can be time-consuming and costly.
Digital twins, however, allow for a comprehensive examination of the equipment’s components and operations.
By analyzing historical data alongside real-time inputs, digital twins can help pinpoint faults and propose potential solutions more efficiently.
Another essential function of digital twins in diagnostics is their ability to simulate different scenarios.
This simulation capability allows technicians to predict how the equipment will respond to various conditions or changes, which is particularly helpful in planning maintenance activities and avoiding unexpected downtimes.
Benefits of Using Digital Twins for Equipment Diagnosis
The adoption of digital twin technology in equipment diagnostics brings a multitude of benefits.
One of the primary advantages is enhanced predictive maintenance capability.
By continuously monitoring the equipment’s condition, digital twins help predict failures before they occur, significantly reducing downtime and maintenance costs.
Moreover, digital twins improve asset performance and efficiency.
As these virtual models provide insights into how equipment operates under different conditions, companies can optimize processes to extend the lifespan of the equipment and reduce energy consumption.
Additionally, digital twins facilitate better decision-making.
With accurate simulations and predictions, businesses can make data-driven decisions about investments in equipment upgrades, replacements, or process changes.
Digital twins also serve as an excellent training tool.
Engineers and operators can use these virtual models to practice handling equipment, learning the impact of various settings, and gaining insights into the effects of different operating conditions without risking damage to the actual equipment.
Application of Digital Twins in Remaining Life Prediction
One of the most promising applications of digital twins is in predicting the remaining useful life (RUL) of equipment.
RUL prediction involves estimating the time the equipment can continue operating before it requires maintenance or replacement.
Accurate RUL predictions enable organizations to plan maintenance schedules effectively, order spare parts in advance, and avert potential failures.
Digital twins enhance RUL predictions by combining data from multiple sources and employing advanced algorithms and machine learning techniques.
They analyze historical and real-time data to identify patterns and trends that correlate with equipment degradation or failure.
Moreover, digital twins have the capability to incorporate environmental and operational variables into their analysis.
Factors such as temperature, pressure, load, and vibration can significantly impact the equipment’s lifespan.
By accounting for these variables, digital twins deliver more accurate RUL predictions.
The precise RUL predictions offered by digital twins help companies avoid unnecessary replacement or maintenance, leading to cost savings and better resource allocation.
Additionally, knowing the equipment’s RUL allows for the timely implementation of improvements and upgrades, enhancing overall operational efficiency.
Real-World Examples and Impact
Several industries have already begun to reap the benefits of digital twin technology for equipment diagnosis and RUL prediction.
For instance, in the aerospace industry, digital twins are used to monitor engine performance, helping airlines schedule maintenance and reduce the risk of in-flight malfunctions.
In the automotive sector, manufacturers utilize digital twins to optimize vehicle performance and predict wear and tear on components, such as brakes and tires, thus improving safety and reducing maintenance expenses.
The energy sector is another area where digital twins are making a significant impact.
Wind turbine and power plant operators use digital twins to predict and prevent equipment failures, ensuring a continuous supply of energy and reducing operational costs.
The Future of Equipment Diagnosis with Digital Twins
The future of equipment diagnosis with digital twins looks promising as technology continues to evolve.
With advancements in artificial intelligence, machine learning, and IoT, digital twins are becoming more sophisticated and capable.
As the integration of these technologies deepens, digital twins will offer even more accurate diagnostics and predictions.
This evolution will lead to smarter, more autonomous maintenance systems that require minimal human intervention.
Furthermore, the widespread adoption of digital twin technology will drive further innovation and development in the fields of equipment manufacturing and maintenance.
As more companies recognize the value of digital twins, we can expect to see increased investments in research and the development of new applications.
In conclusion, digital twins are revolutionizing equipment diagnosis and maintenance practices.
By providing detailed insights and predictive capabilities, they empower organizations to optimize operations, reduce costs, and enhance equipment lifespan.
As technology progresses, the role of digital twins in predicting the remaining life of equipment will continue to grow, setting new standards for efficiency and reliability in various industries.
資料ダウンロード
QCD管理受発注クラウド「newji」は、受発注部門で必要なQCD管理全てを備えた、現場特化型兼クラウド型の今世紀最高の受発注管理システムとなります。
ユーザー登録
受発注業務の効率化だけでなく、システムを導入することで、コスト削減や製品・資材のステータス可視化のほか、属人化していた受発注情報の共有化による内部不正防止や統制にも役立ちます。
NEWJI DX
製造業に特化したデジタルトランスフォーメーション(DX)の実現を目指す請負開発型のコンサルティングサービスです。AI、iPaaS、および先端の技術を駆使して、製造プロセスの効率化、業務効率化、チームワーク強化、コスト削減、品質向上を実現します。このサービスは、製造業の課題を深く理解し、それに対する最適なデジタルソリューションを提供することで、企業が持続的な成長とイノベーションを達成できるようサポートします。
製造業ニュース解説
製造業、主に購買・調達部門にお勤めの方々に向けた情報を配信しております。
新任の方やベテランの方、管理職を対象とした幅広いコンテンツをご用意しております。
お問い合わせ
コストダウンが利益に直結する術だと理解していても、なかなか前に進めることができない状況。そんな時は、newjiのコストダウン自動化機能で大きく利益貢献しよう!
(β版非公開)