- お役立ち記事
- Essential differences between FMEA and DRBFM
月間76,176名の
製造業ご担当者様が閲覧しています*
*2025年3月31日現在のGoogle Analyticsのデータより
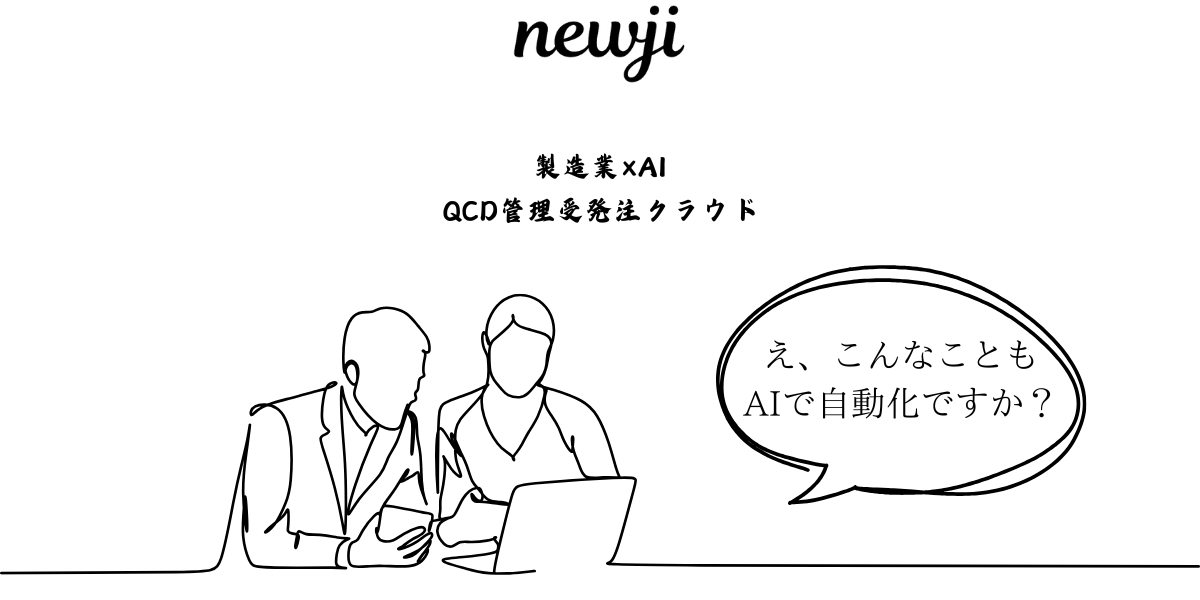
Essential differences between FMEA and DRBFM
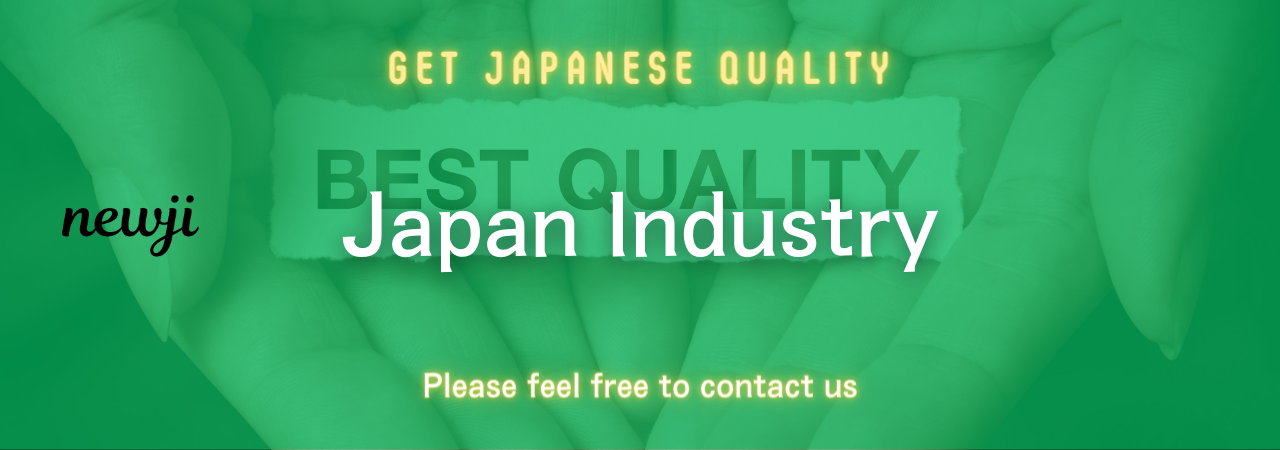
目次
Understanding FMEA and DRBFM
Failure Modes and Effects Analysis (FMEA) and Design Review Based on Failure Mode (DRBFM) are crucial tools in the engineering and manufacturing industries.
Both methodologies aim to improve product reliability and safety by identifying potential failure points, but they differ significantly in their approaches and applications.
Understanding these differences can help organizations choose the right method for their specific needs and ultimately enhance their design and manufacturing processes.
What is FMEA?
FMEA is a systematic approach used to pinpoint where and how a design might fail in function.
Originating in the aerospace industry in the 1940s, FMEA has since become a standard practice in automotive, industrial, and healthcare industries as well.
The primary goal of FMEA is to anticipate failure before it occurs, minimize risk by prioritizing failures based on their severity, probability of occurrence, and detectability.
The FMEA process involves several steps.
First, a team identifies all possible failure modes of a product or process.
Next, they assess the effects of each failure mode, assigning a risk priority number (RPN) based on severity, occurrence, and detection ratings.
Higher RPN values indicate higher-risk failure modes requiring immediate corrective actions.
By systematically addressing these potential failures, FMEA helps in designing more resilient and efficient processes and products.
What is DRBFM?
DRBFM is a method developed by Toyota that focuses specifically on design changes and their implications.
The name “Design Review Based on Failure Mode” reflects its core purpose – to deeply scrutinize any changes to a design to mitigate potential failures.
Unlike FMEA, which covers the entire design and process, DRBFM is primarily concerned with changes and the small details that might be overlooked.
DRBFM encourages engineers to ask detailed questions about the intentional changes made and presume the potential failure modes associated with them.
This method emphasizes the philosophy that all changes, no matter how minor, can alter failure modes significantly.
The process of DRBFM typically starts with a thorough discussion of the design change, followed by a detailed review to anticipate problems and plan for potential contingencies.
The structured review leads to more informed decision-making and a better understanding of how changes could influence overall product reliability.
Key Differences Between FMEA and DRBFM
While FMEA and DRBFM aim to prevent failures, they differ in scope and methodology.
Understanding their unique characteristics can help organizations effectively implement the right strategy.
Scope and Focus
FMEA takes a broad approach, assessing the entire system or product design for potential failure modes.
Its comprehensive nature makes it suitable for new product designs and entire systems where multiple components interact.
Conversely, DRBFM has a narrower focus and is used for examining specific changes within an existing design.
DRBFM is most effective when applied to incremental design modifications rather than new products or entirely redesigned systems.
Philosophy and Application
FMEA is rooted in statistical analysis and risk assessment, emphasizing the quantification of potential failures using risk priority numbers.
Its structured, data-driven methodology provides a clear picture of risk levels, allowing for targeted interventions.
On the other hand, DRBFM is more qualitative, encouraging a thorough discussion of potential issues with a keen focus on small changes.
DRBFM relies more on expert judgment through intensive discussions rather than quantitative data.
This philosophical difference means DRBFM often uncovers issues that might not be apparent through traditional FMEA analysis.
Implementation Process
FMEA involves assembling a cross-functional team to conduct a systematic review focusing on possible failure modes throughout the design or process.
The team uses historical data to calculate and assign RPN, making the process relatively lengthy due to its detailed nature.
DRBFM, in contrast, revolves around discussions and brainstorming sessions.
Engineers explore hypothetical scenarios and deeply question every aspect of the proposed changes, making the process more dynamic and rapid.
The discussion-driven nature fosters collaboration and often encourages creativity in problem-solving.
Choosing Between FMEA and DRBFM
The decision to use FMEA, DRBFM, or a combination of both depends on the specific context of the project and the goals of the organization.
FMEA is particularly beneficial at the early stages of product development when introducing complex new designs or systems.
Its structured analysis provides a high level of detail and helps prioritize resources efficiently against potential risks across the entire system.
DRBFM is ideal for projects involving existing designs undergoing modifications.
The detailed focus on design changes ensures that even minimal adjustments are thoroughly vetted for possible failure points.
DRBFM’s collaborative approach also makes it a good choice when fostering innovation within teams focused on iterative product development.
Conclusion
Both FMEA and DRBFM play significant roles in enhancing the reliability and safety of products and systems.
Although they share a common goal, their differences in approach, focus, and implementation make each suitable for specific scenarios.
By understanding these methodologies and their unique strengths, organizations can make informed decisions and effectively mitigate risk throughout the design and development process to deliver better, more reliable products.
資料ダウンロード
QCD管理受発注クラウド「newji」は、受発注部門で必要なQCD管理全てを備えた、現場特化型兼クラウド型の今世紀最高の受発注管理システムとなります。
ユーザー登録
受発注業務の効率化だけでなく、システムを導入することで、コスト削減や製品・資材のステータス可視化のほか、属人化していた受発注情報の共有化による内部不正防止や統制にも役立ちます。
NEWJI DX
製造業に特化したデジタルトランスフォーメーション(DX)の実現を目指す請負開発型のコンサルティングサービスです。AI、iPaaS、および先端の技術を駆使して、製造プロセスの効率化、業務効率化、チームワーク強化、コスト削減、品質向上を実現します。このサービスは、製造業の課題を深く理解し、それに対する最適なデジタルソリューションを提供することで、企業が持続的な成長とイノベーションを達成できるようサポートします。
製造業ニュース解説
製造業、主に購買・調達部門にお勤めの方々に向けた情報を配信しております。
新任の方やベテランの方、管理職を対象とした幅広いコンテンツをご用意しております。
お問い合わせ
コストダウンが利益に直結する術だと理解していても、なかなか前に進めることができない状況。そんな時は、newjiのコストダウン自動化機能で大きく利益貢献しよう!
(β版非公開)