- お役立ち記事
- Essential for Quality Departments! How to Improve Customer Satisfaction with Quality Function Deployment (QFD)
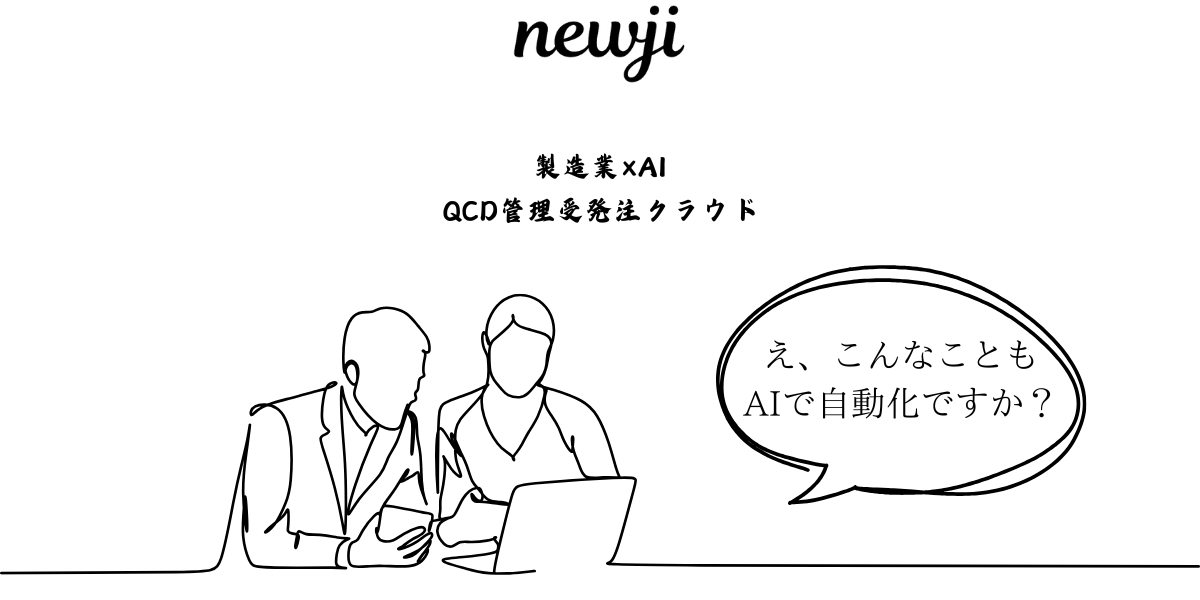
Essential for Quality Departments! How to Improve Customer Satisfaction with Quality Function Deployment (QFD)
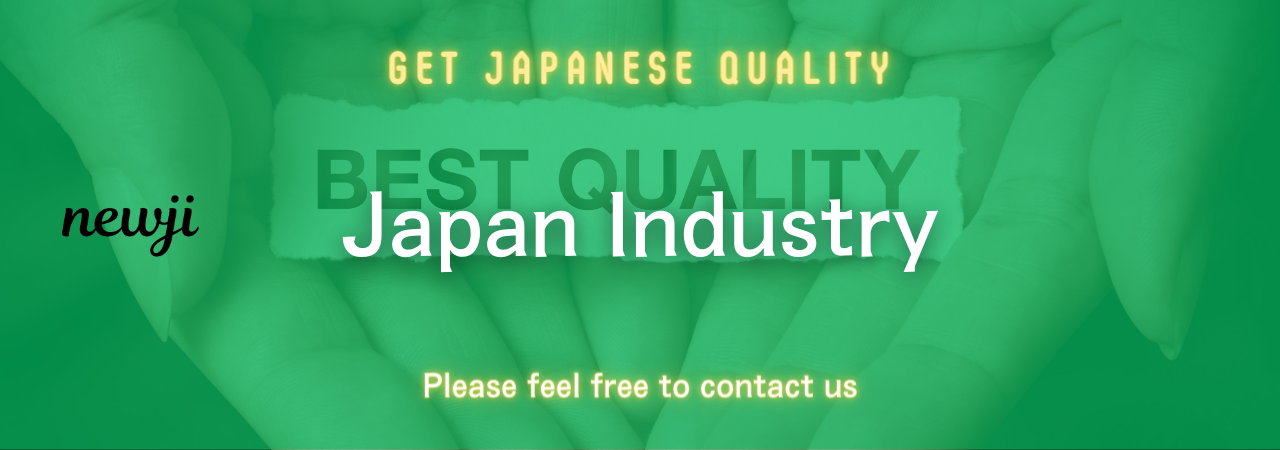
目次
Understanding Quality Function Deployment (QFD)
Quality Function Deployment, or QFD, is a systematic process used by quality departments to ensure that the voice of the customer is heard and incorporated into the product development process.
It translates customer needs (often referred to as the “voice of the customer,” or VoC) into technical requirements, creating a structured approach to meeting customer expectations and enhancing satisfaction.
The fundamental goal of QFD is to bridge the gap between customer expectations and the final product or service.
This is achieved through a series of matrices that help organizations prioritize customer demands and align them with internal processes and production capabilities.
The Importance of Customer Satisfaction
In today’s competitive marketplace, customer satisfaction is more crucial than ever.
Satisfied customers are more likely to become repeat buyers, recommend your products to others, and contribute positively to your brand reputation.
Conversely, dissatisfied customers can quickly harm your business through negative reviews and word-of-mouth.
For quality departments, understanding and enhancing customer satisfaction requires a thorough understanding of what customers truly value.
This is where QFD comes into play.
By systematically translating customer requirements into actionable product and service attributes, organizations can ensure that they are directly addressing customer needs.
The QFD Process
Implementing QFD involves several key steps that guide the team through understanding and meeting customer desires.
1. Identify Customer Requirements
The first step in the QFD process is to gather and identify the needs and expectations of the customer.
This can be done through surveys, interviews, focus groups, and analyzing customer feedback.
The gathered data should be comprehensive and reflect a wide range of customer voices.
2. Prioritize Customer Needs
Not all customer requirements hold the same weight in terms of impact on satisfaction.
Therefore, the next step is to prioritize these needs based on their importance to the customer and their influence on purchasing decisions.
This helps allocate resources efficiently throughout the development process.
3. Develop the House of Quality
The central tool of QFD is the “House of Quality,” a matrix used to translate customer requirements into engineering targets.
This matrix links what the customer wants with how the company will deliver on those desires.
The House of Quality maps out the relationship between customer desires and the company’s ability to meet those needs through specific product features and service attributes.
It includes aspects like customer importance ratings, competitive benchmarking, and technical difficulties of implementation.
4. Determine Technical Requirements
Based on the House of Quality, the organization must specify how technical requirements will achieve customer needs.
This involves setting measurable indicators of performance, such as durability, functionality, or aesthetics, that relate directly to the voice of the customer.
5. Evaluate and Optimize
Finally, the QFD process involves evaluating each aspect of the project to ensure alignment with customer satisfaction goals.
This might involve revisiting earlier steps to refine priorities or methods of implementation, ensuring that the final product meets or exceeds customer expectations.
Benefits of Using QFD
QFD offers numerous benefits that highlight its importance in improving customer satisfaction.
Enhanced Customer Understanding
The structured format of QFD provides a deep understanding of the customer’s perspective, enabling clearer insights into their needs and expectations.
This understanding is critical in creating products and services that resonate with customers.
Improved Cross-Department Collaboration
QFD encourages collaboration across different departments within an organization.
By involving stakeholders from manufacturing, engineering, marketing, and customer service in the QFD process, companies ensure a balanced approach that considers technical feasibility, marketability, and customer service.
Reduced Time to Market
By anticipating customer requirements correctly, QFD can significantly reduce the time and cost involved in product development.
The process minimizes the need for last-minute changes and redesigns that occur when customer needs are misunderstood.
Competitive Advantage
Through its customer-centric orientation, QFD enables businesses to develop products and services that truly stand out in the market.
This can enhance a company’s reputation as a leader in quality and innovation.
Implementing QFD in Quality Departments
For quality departments aiming to implement QFD successfully, a few best practices can enhance the effectiveness of the process.
Commitment at All Levels
QFD requires commitment from top management and alignment across all levels of the organization.
Encouraging a culture that values customer input and continuous improvement is crucial.
Training and Resources
Providing adequate training and resources ensures that teams are well-equipped to implement QFD processes effectively.
Investing in tools and technology that support QFD, such as software for data analysis and process management, can also be beneficial.
Continuous Feedback and Iteration
QFD is not a one-time effort but a continuous process.
Regularly seeking customer feedback and iterating on product development based on this input is essential for maintaining alignment with customer expectations.
Conclusion
Quality Function Deployment is an indispensable tool for quality departments focusing on improving customer satisfaction.
By aligning product development processes with customer needs, QFD ensures that businesses deliver superior value, enhancing customer loyalty and gaining a competitive edge.
For companies dedicated to customer satisfaction, QFD offers a clear path to success, ensuring that quality is embedded into every product and service offered.
資料ダウンロード
QCD調達購買管理クラウド「newji」は、調達購買部門で必要なQCD管理全てを備えた、現場特化型兼クラウド型の今世紀最高の購買管理システムとなります。
ユーザー登録
調達購買業務の効率化だけでなく、システムを導入することで、コスト削減や製品・資材のステータス可視化のほか、属人化していた購買情報の共有化による内部不正防止や統制にも役立ちます。
NEWJI DX
製造業に特化したデジタルトランスフォーメーション(DX)の実現を目指す請負開発型のコンサルティングサービスです。AI、iPaaS、および先端の技術を駆使して、製造プロセスの効率化、業務効率化、チームワーク強化、コスト削減、品質向上を実現します。このサービスは、製造業の課題を深く理解し、それに対する最適なデジタルソリューションを提供することで、企業が持続的な成長とイノベーションを達成できるようサポートします。
オンライン講座
製造業、主に購買・調達部門にお勤めの方々に向けた情報を配信しております。
新任の方やベテランの方、管理職を対象とした幅広いコンテンツをご用意しております。
お問い合わせ
コストダウンが利益に直結する術だと理解していても、なかなか前に進めることができない状況。そんな時は、newjiのコストダウン自動化機能で大きく利益貢献しよう!
(Β版非公開)