- お役立ち記事
- Establishing a smooth process for custom parts procurement in the manufacturing industry
月間76,176名の
製造業ご担当者様が閲覧しています*
*2025年3月31日現在のGoogle Analyticsのデータより
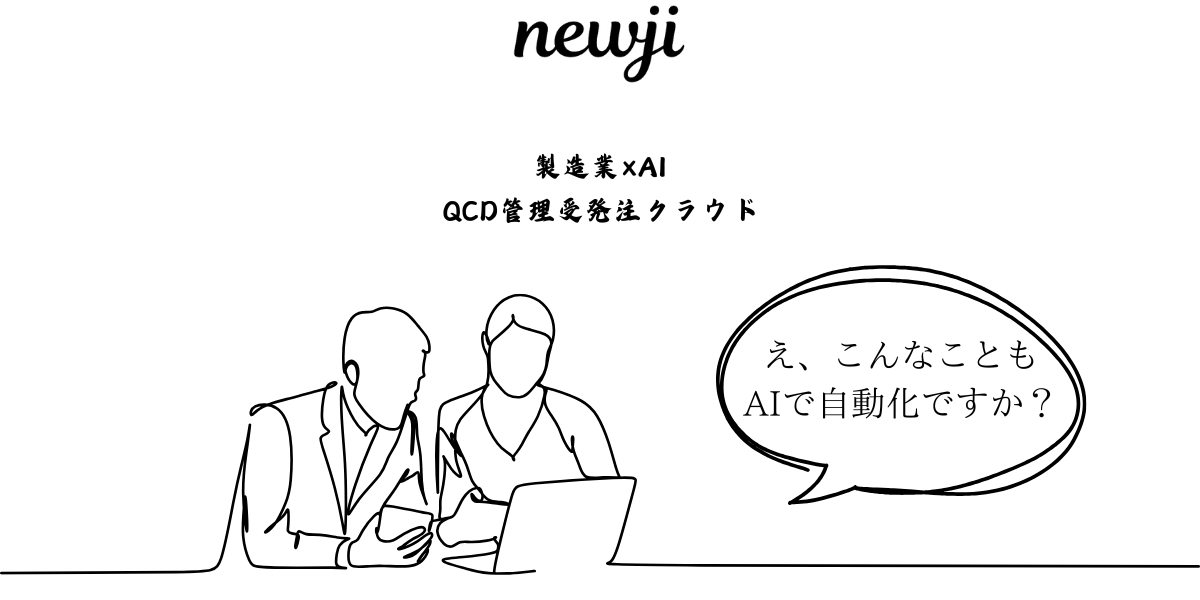
Establishing a smooth process for custom parts procurement in the manufacturing industry
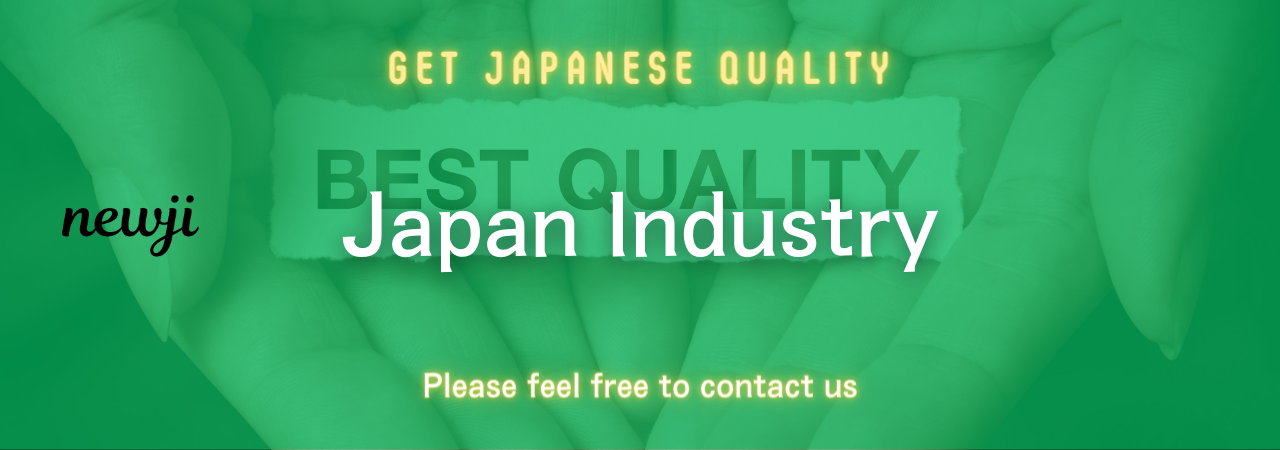
In the ever-evolving manufacturing industry, the procurement of custom parts is essential to meeting unique production needs and maintaining a competitive edge.
Establishing a smooth process for acquiring these custom parts not only aids in efficient production but also ensures the quality and reliability of the final products.
This article delves into practical strategies and steps to streamline the procurement process, enhancing overall manufacturing efficiency.
目次
Understanding the Importance of Custom Parts Procurement
The demand for custom parts arises due to specific requirements that standard components cannot fulfill.
These needs could stem from unique design specifications, materials, or functionality tailored to a particular product line.
Ensuring a seamless procurement process for these parts is crucial, as delays or errors can have cascading effects on production timelines and costs.
Effective procurement helps in maintaining inventory levels, reducing lead times, and optimizing production schedules.
Identifying the Right Suppliers
Finding reliable suppliers who can meet the specific needs of custom parts is the cornerstone of successful procurement.
Manufacturers should conduct thorough research, evaluating potential suppliers based on their capability to deliver quality, adherence to timelines, and cost-effectiveness.
Building long-term relationships with suppliers can lead to more tailored and flexible terms, ensuring they can adjust to your evolving manufacturing demands.
Regular audits and feedback mechanisms can help maintain quality standards, fostering continuous improvement in supplier performance.
Implementing Technology in Procurement
The integration of technology in the procurement process can significantly enhance efficiency and transparency.
Adopting digital procurement platforms allows manufacturers to streamline ordering processes, track shipments, and manage supplier communications more effectively.
These platforms can also facilitate better data management, providing insights into spending patterns and supplier performance, aiding in strategic decision-making.
Utilizing Automation and AI
Automation tools can handle routine tasks such as order processing and inventory management, reducing human error and freeing up valuable time for strategic tasks.
Incorporating Artificial Intelligence (AI) can further optimize procurement by predicting demand trends, evaluating supplier reliability, and suggesting optimizations in ordering cycles.
These technological advancements contribute to a more responsive and resilient procurement strategy, capable of adjusting to fluctuations in demand and supply chain disruptions.
Developing a Robust Procurement Strategy
A successful procurement strategy is underpinned by detailed planning and clear objectives.
Manufacturers should define key performance indicators (KPIs) that align procurement goals with overall business objectives.
These KPIs might include cost savings, lead time reductions, and supplier quality ratings.
Regularly reviewing these metrics can help identify areas for improvement and guide adjustments in procurement tactics.
Fostering Cross-Department Collaboration
Procurement does not operate in isolation, and effective collaboration with other departments such as design, engineering, and finance is vital.
Regular communication ensures that procurement teams are aware of design changes or upcoming production needs that could affect parts requirements.
This collaboration also allows for a more holistic approach to problem-solving, leveraging insights from across the organization to enhance procurement efficiency and effectiveness.
Ensuring Quality and Compliance
Maintaining the quality and compliance of custom parts is essential for safeguarding product integrity and brand reputation.
Manufacturers should implement rigorous quality checks and adhere to industry standards and regulations throughout the procurement process.
Supplier contracts should clearly outline quality expectations and penalties for non-compliance, providing a framework for accountability and continuous improvement.
Managing Risks in Procurement
Risk management is a critical component of a smooth procurement process.
Identifying potential risks, such as supplier insolvencies, international trade issues, or material shortages, allows teams to develop contingency plans.
Diversifying the supplier base and exploring alternative sourcing strategies can mitigate these risks, ensuring stable supply chains even in volatile markets.
Regularly revisiting risk assessments and updating plans is essential to adapt to new challenges and opportunities in the manufacturing landscape.
Conclusion: Achieving Procurement Excellence
Establishing a smooth process for custom parts procurement in the manufacturing industry is a multifaceted endeavor.
It requires a strategic approach that incorporates technology, fosters collaboration, and emphasizes quality and risk management.
By focusing on these key areas, manufacturers can enhance their procurement processes, leading to more efficient production cycles, reduced costs, and increased customer satisfaction.
With the right strategies in place, companies can not only meet but also anticipate the evolving demands of the manufacturing industry, securing their position as leaders in innovation and quality.
資料ダウンロード
QCD管理受発注クラウド「newji」は、受発注部門で必要なQCD管理全てを備えた、現場特化型兼クラウド型の今世紀最高の受発注管理システムとなります。
ユーザー登録
受発注業務の効率化だけでなく、システムを導入することで、コスト削減や製品・資材のステータス可視化のほか、属人化していた受発注情報の共有化による内部不正防止や統制にも役立ちます。
NEWJI DX
製造業に特化したデジタルトランスフォーメーション(DX)の実現を目指す請負開発型のコンサルティングサービスです。AI、iPaaS、および先端の技術を駆使して、製造プロセスの効率化、業務効率化、チームワーク強化、コスト削減、品質向上を実現します。このサービスは、製造業の課題を深く理解し、それに対する最適なデジタルソリューションを提供することで、企業が持続的な成長とイノベーションを達成できるようサポートします。
製造業ニュース解説
製造業、主に購買・調達部門にお勤めの方々に向けた情報を配信しております。
新任の方やベテランの方、管理職を対象とした幅広いコンテンツをご用意しております。
お問い合わせ
コストダウンが利益に直結する術だと理解していても、なかなか前に進めることができない状況。そんな時は、newjiのコストダウン自動化機能で大きく利益貢献しよう!
(β版非公開)