- お役立ち記事
- Establishing Leadership in Manufacturing: Providing Expertise and Industry Insight
Establishing Leadership in Manufacturing: Providing Expertise and Industry Insight
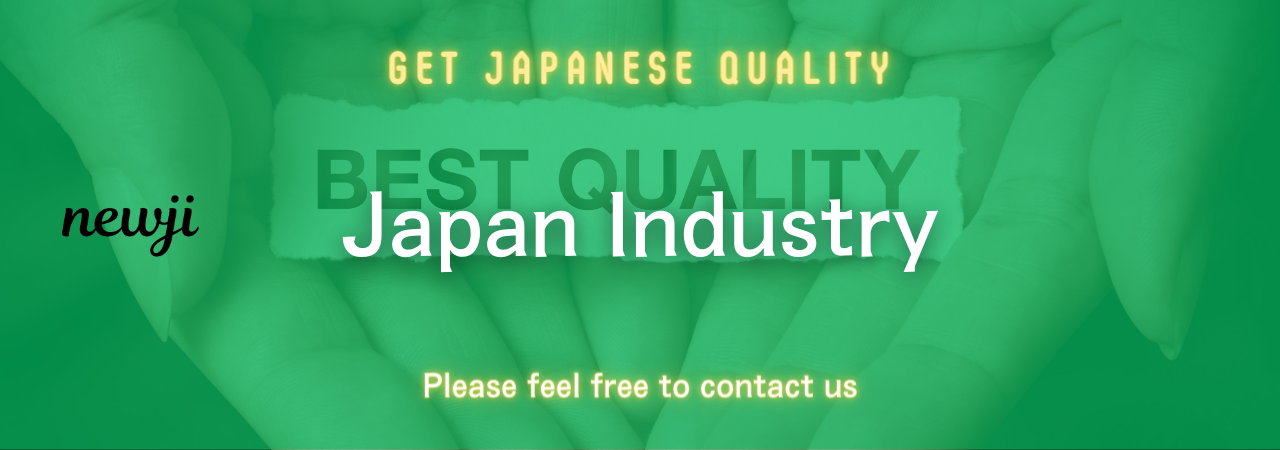
In today’s fast-paced manufacturing industry, strong leadership plays a crucial role in achieving success. Whether you’re a seasoned manager or an aspiring leader, navigating the complex landscape of this sector requires a deep understanding of various aspects, from production processes to effective communication. This article explores the essential elements of establishing leadership in manufacturing, offering valuable expertise and industry insight.
目次
Understanding the Importance of Leadership in Manufacturing
Effective leadership is vital for achieving operational efficiency, driving innovation, and ensuring employee satisfaction. In manufacturing, leaders are responsible for overseeing production lines, managing teams, and meeting customer demands. Without strong leadership, even the most advanced technologies and processes can fall short of their potential. Let’s delve into the key reasons why leadership is so important in manufacturing.
Enhancing Productivity and Efficiency
Leaders play a pivotal role in maximizing productivity and efficiency within a manufacturing facility. They are tasked with identifying bottlenecks, streamlining processes, and implementing strategies to reduce waste and downtime. By fostering a culture of continuous improvement and encouraging teamwork, leaders can drive significant gains in output and quality.
Driving Innovation and Adaptability
The manufacturing industry is constantly evolving, with new technologies and methodologies emerging regularly. Leaders who stay informed about these trends can guide their organizations through transitions effectively. Embracing innovation and flexibility allows manufacturers to stay competitive and meet changing market demands.
Ensuring Employee Engagement and Satisfaction
A motivated and engaged workforce is essential for any manufacturing operation. Leaders who prioritize communication, provide opportunities for growth, and recognize employee contributions foster a positive work environment. This, in turn, leads to higher morale, reduced turnover, and improved overall performance.
Key Qualities of Effective Manufacturing Leaders
To excel as a leader in the manufacturing industry, certain qualities and skills are essential. These attributes enable leaders to navigate challenges, inspire their teams, and drive success.
Technical Expertise
A deep understanding of manufacturing processes, equipment, and technologies is fundamental. Leaders with technical expertise can make informed decisions, troubleshoot issues, and guide their teams effectively. Continuous learning and staying updated with industry advancements are crucial for maintaining this expertise.
Strong Communication Skills
Clear and effective communication is a cornerstone of successful leadership. Manufacturing leaders must communicate expectations, provide feedback, and convey information accurately. Additionally, active listening is vital for understanding the concerns and suggestions of team members.
Problem-Solving Abilities
The ability to identify problems, analyze their root causes, and develop effective solutions is a critical skill for manufacturing leaders. This includes being proactive in preventing issues and quickly addressing any disruptions that arise.
Adaptability and Resilience
Manufacturing is a dynamic field that often requires leaders to adapt to changing circumstances. Resilience in the face of challenges and the ability to pivot strategies when necessary are key traits of successful leaders.
People-Centric Approach
Valuing and respecting employees as individuals is essential. Leaders should prioritize their team’s well-being, provide opportunities for professional growth, and create an inclusive and supportive work environment.
Best Practices for Leadership in Manufacturing
Establishing effective leadership in the manufacturing industry involves implementing best practices that align with organizational goals and foster a culture of excellence.
Setting Clear Goals and Expectations
Leaders should establish clear, measurable goals and communicate them to their teams. This ensures everyone understands their roles and responsibilities, contributing to a cohesive effort toward achieving organizational objectives.
Investing in Training and Development
Continuous learning is crucial in manufacturing. Providing training programs and opportunities for skill development helps employees stay updated with the latest technologies and techniques. This investment also demonstrates a commitment to their growth and career progression.
Encouraging Collaboration and Teamwork
Promoting a collaborative environment where team members can share ideas and work together is essential. Regular team meetings, brainstorming sessions, and cross-functional projects enhance synergy and innovation.
Implementing Lean Manufacturing Principles
Lean manufacturing principles focus on minimizing waste and maximizing value. Leaders can adopt these principles to streamline processes, improve efficiency, and reduce costs, driving overall operational excellence.
Recognizing and Rewarding Achievements
Acknowledging and appreciating employees’ hard work is important for motivation and morale. Implementing a recognition program that celebrates achievements, both big and small, fosters a positive work culture and encourages continuous improvement.
The Future of Leadership in Manufacturing
As the manufacturing industry continues to evolve, so too will the demands on its leaders. Staying ahead of trends and technologies will be crucial for maintaining a competitive edge.
Embracing Industry 4.0
Industry 4.0, characterized by the integration of digital technologies and automation, is transforming manufacturing. Leaders who embrace these advancements can drive efficiency, increase production flexibility, and enhance product quality.
Sustainable Manufacturing Practices
Sustainability is becoming increasingly important in manufacturing. Leaders will need to focus on environmentally friendly practices, such as reducing carbon footprints, minimizing waste, and optimizing resource utilization.
Workforce Diversity and Inclusion
A diverse and inclusive workforce brings a wide range of perspectives and ideas. Leaders who prioritize diversity and inclusion can foster innovation, improve decision-making, and create a more dynamic and resilient organization.
Focus on Employee Well-being
The well-being of employees is paramount. Leaders will need to invest in programs and initiatives that support mental health, work-life balance, and overall job satisfaction.
In conclusion, effective leadership is the cornerstone of success in the manufacturing industry. By understanding the importance of leadership, embodying key qualities, and implementing best practices, leaders can drive operational excellence, foster innovation, and ensure a motivated and engaged workforce. As the industry continues to evolve, staying ahead of trends and embracing new technologies will be crucial for maintaining a competitive edge and achieving long-term success.
資料ダウンロード
QCD調達購買管理クラウド「newji」は、調達購買部門で必要なQCD管理全てを備えた、現場特化型兼クラウド型の今世紀最高の購買管理システムとなります。
ユーザー登録
調達購買業務の効率化だけでなく、システムを導入することで、コスト削減や製品・資材のステータス可視化のほか、属人化していた購買情報の共有化による内部不正防止や統制にも役立ちます。
NEWJI DX
製造業に特化したデジタルトランスフォーメーション(DX)の実現を目指す請負開発型のコンサルティングサービスです。AI、iPaaS、および先端の技術を駆使して、製造プロセスの効率化、業務効率化、チームワーク強化、コスト削減、品質向上を実現します。このサービスは、製造業の課題を深く理解し、それに対する最適なデジタルソリューションを提供することで、企業が持続的な成長とイノベーションを達成できるようサポートします。
オンライン講座
製造業、主に購買・調達部門にお勤めの方々に向けた情報を配信しております。
新任の方やベテランの方、管理職を対象とした幅広いコンテンツをご用意しております。
お問い合わせ
コストダウンが利益に直結する術だと理解していても、なかなか前に進めることができない状況。そんな時は、newjiのコストダウン自動化機能で大きく利益貢献しよう!
(Β版非公開)