- お役立ち記事
- Establishing Technical Standards to Ensure Uniform Product Quality
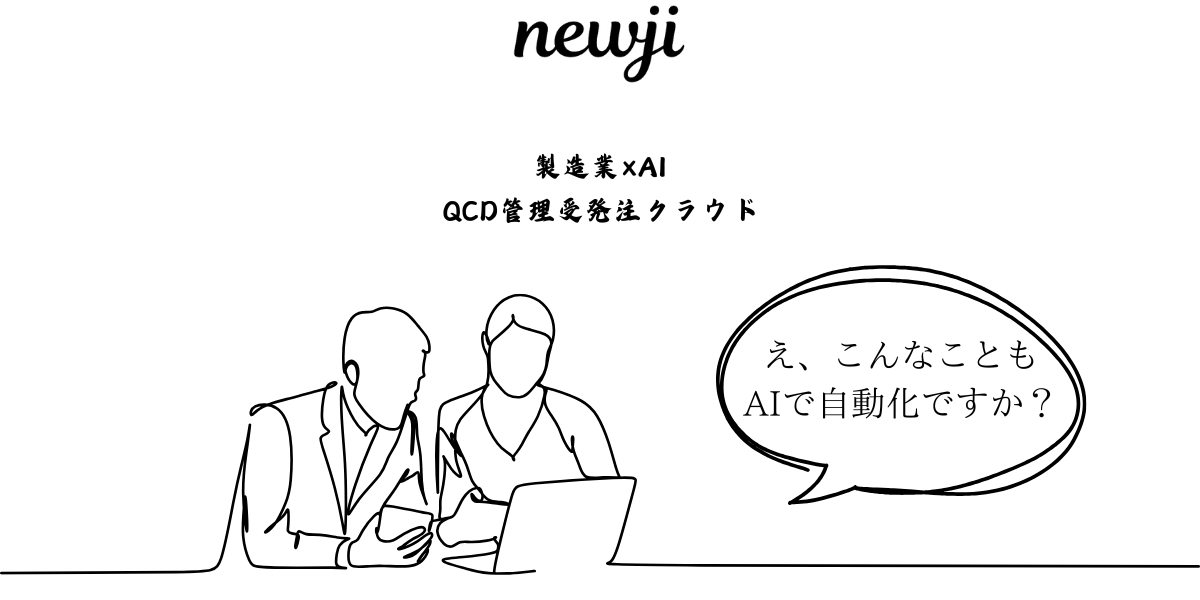
Establishing Technical Standards to Ensure Uniform Product Quality
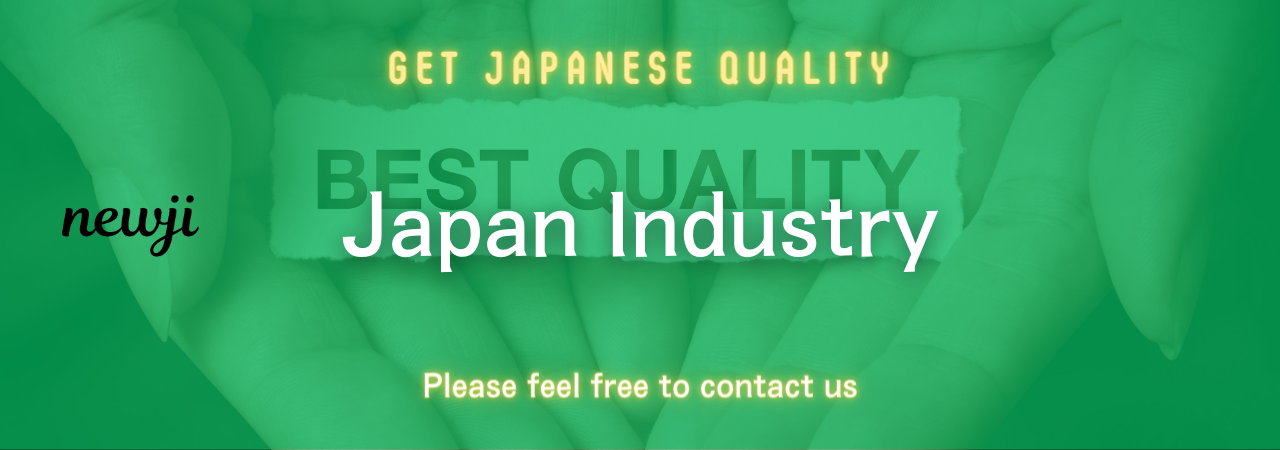
Establishing technical standards is essential for ensuring that products meet specific quality criteria consistently.
This process is crucial across various industries, from manufacturing to software development.
By implementing these standards, businesses can achieve uniformity, reliability, and high-quality products.
But what exactly do technical standards entail, and how can they be effectively established? Let’s explore the key aspects.
目次
What Are Technical Standards?
Technical standards are documented guidelines that provide specifications and criteria to be followed consistently.
They cover various aspects, such as product design, manufacturing processes, quality control measures, and testing protocols.
These standards ensure that products are produced uniformly, which helps in maintaining high quality.
Importance of Technical Standards
Technical standards serve as a benchmark for quality.
They help in reducing variability in products, ensuring that each item meets the required specifications.
Consumers can trust that products adhering to these standards will perform as expected.
Moreover, technical standards facilitate smoother collaboration among different stakeholders, including suppliers, manufacturers, and regulators.
Steps to Establish Technical Standards
Creating effective technical standards involves several key steps.
Let’s break down the process:
1. Identify the Need for Standards
The first step is to recognize areas where standardization is needed.
This could be due to inconsistent product quality, customer complaints, or regulatory requirements.
Identifying these pain points will help in defining the scope of the standards.
2. Gather Relevant Data
Collect data from various sources, such as industry benchmarks, customer feedback, and internal quality reports.
This information will provide a solid foundation for developing standards that address specific concerns.
3. Involve Stakeholders
Engage key stakeholders, including engineers, quality assurance teams, and management.
Their input is invaluable in creating standards that are practical and comprehensive.
Collaborative efforts ensure that all perspectives are considered.
4. Develop the Standards
Draft the technical standards, detailing specifications, tolerances, and procedures.
Use clear, concise language to avoid ambiguity.
Including diagrams, flowcharts, and examples can enhance understanding and usability.
5. Review and Test
Before finalizing the standards, conduct thorough reviews and tests.
This step ensures that the standards are feasible and effective.
Seek feedback from stakeholders and make necessary revisions.
6. Implement the Standards
Once the standards are finalized, communicate them to all relevant parties.
Provide training and resources to ensure seamless adoption.
Clear communication is crucial for successful implementation.
7. Monitor and Update
Regularly monitor the effectiveness of the standards.
Gather feedback and make updates as needed to adapt to new challenges or technological advancements.
Continuous improvement is key to maintaining high-quality standards.
Examples of Technical Standards
Technical standards vary across industries.
Here are a few examples:
Manufacturing Industry
In manufacturing, standards might include specifications for materials, product dimensions, and safety requirements.
For instance, the ISO 9001 standard focuses on quality management systems, ensuring consistent product quality and customer satisfaction.
Software Development
In software development, standards might cover coding practices, testing protocols, and security measures.
The ISO/IEC 27001 standard, for example, provides guidelines for information security management.
Healthcare Sector
In healthcare, standards ensure the safety and efficacy of medical devices and pharmaceuticals.
The FDA (Food and Drug Administration) sets rigorous standards for the approval and monitoring of medical products.
Benefits of Establishing Technical Standards
Adhering to technical standards offers numerous benefits.
Here are some key advantages:
Consistency in Quality
Technical standards ensure that every product meets the same high-quality criteria.
This consistency builds customer trust and loyalty.
Improved Efficiency
Standardized processes streamline production, reducing errors and rework.
This leads to cost savings and improved efficiency.
Regulatory Compliance
Meeting industry standards often aligns with regulatory requirements.
This helps in avoiding legal issues and fines.
Enhanced Market Competitiveness
High-quality products differentiate a company from its competitors.
Technical standards can serve as a marketing tool, highlighting a commitment to excellence.
Challenges in Establishing Technical Standards
While the benefits are clear, establishing technical standards can be challenging.
Here are some common obstacles:
Resistance to Change
Employees may resist adopting new standards, especially if they are used to existing practices.
Overcoming this resistance requires effective change management and communication.
Resource Constraints
Developing and implementing standards require time and resources.
Small businesses may struggle to allocate the necessary resources.
Keeping Up with Technological Advances
Technology evolves rapidly, and standards need to adapt accordingly.
Staying updated with the latest advancements is crucial but can be demanding.
Conclusion
Establishing technical standards is a critical step in ensuring uniform product quality.
It involves a systematic approach, from identifying the need to monitoring and updating the standards.
While challenges exist, the benefits—consistency in quality, improved efficiency, regulatory compliance, and enhanced competitiveness—make the effort worthwhile.
By committing to technical standards, businesses can deliver high-quality products that meet customer expectations and stand out in the market.
The journey towards standardization may be demanding, but the rewards in terms of quality, trust, and market success are substantial.
資料ダウンロード
QCD調達購買管理クラウド「newji」は、調達購買部門で必要なQCD管理全てを備えた、現場特化型兼クラウド型の今世紀最高の購買管理システムとなります。
ユーザー登録
調達購買業務の効率化だけでなく、システムを導入することで、コスト削減や製品・資材のステータス可視化のほか、属人化していた購買情報の共有化による内部不正防止や統制にも役立ちます。
NEWJI DX
製造業に特化したデジタルトランスフォーメーション(DX)の実現を目指す請負開発型のコンサルティングサービスです。AI、iPaaS、および先端の技術を駆使して、製造プロセスの効率化、業務効率化、チームワーク強化、コスト削減、品質向上を実現します。このサービスは、製造業の課題を深く理解し、それに対する最適なデジタルソリューションを提供することで、企業が持続的な成長とイノベーションを達成できるようサポートします。
オンライン講座
製造業、主に購買・調達部門にお勤めの方々に向けた情報を配信しております。
新任の方やベテランの方、管理職を対象とした幅広いコンテンツをご用意しております。
お問い合わせ
コストダウンが利益に直結する術だと理解していても、なかなか前に進めることができない状況。そんな時は、newjiのコストダウン自動化機能で大きく利益貢献しよう!
(Β版非公開)