- お役立ち記事
- Establishment of soldering defect generation mechanism and “soldering mounting process” to prevent defects
月間77,185名の
製造業ご担当者様が閲覧しています*
*2025年2月28日現在のGoogle Analyticsのデータより
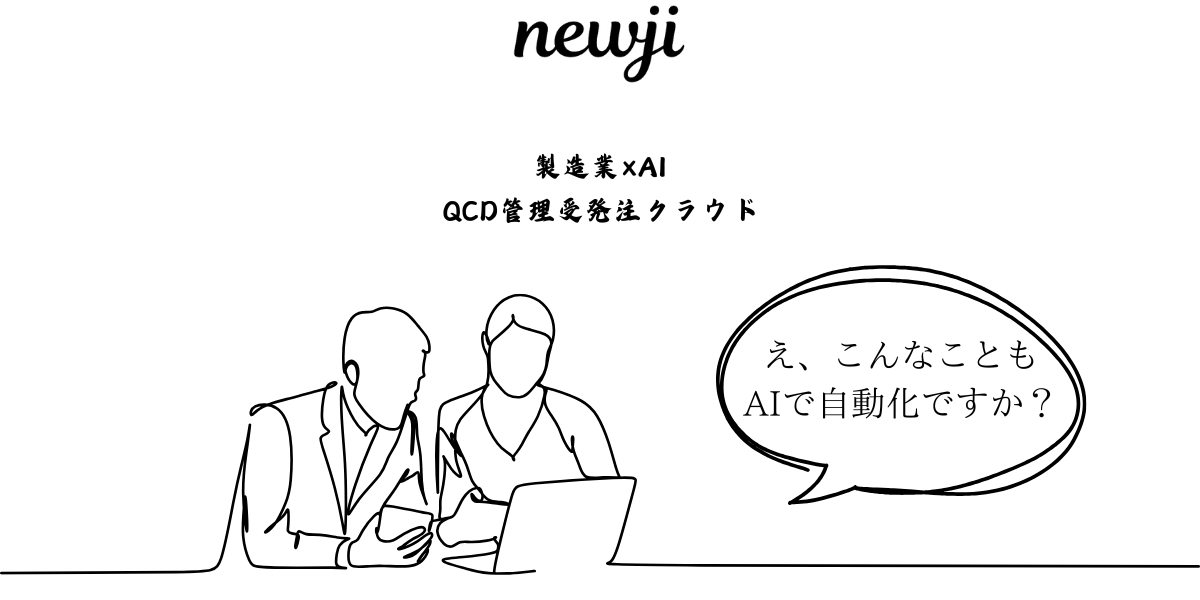
Establishment of soldering defect generation mechanism and “soldering mounting process” to prevent defects
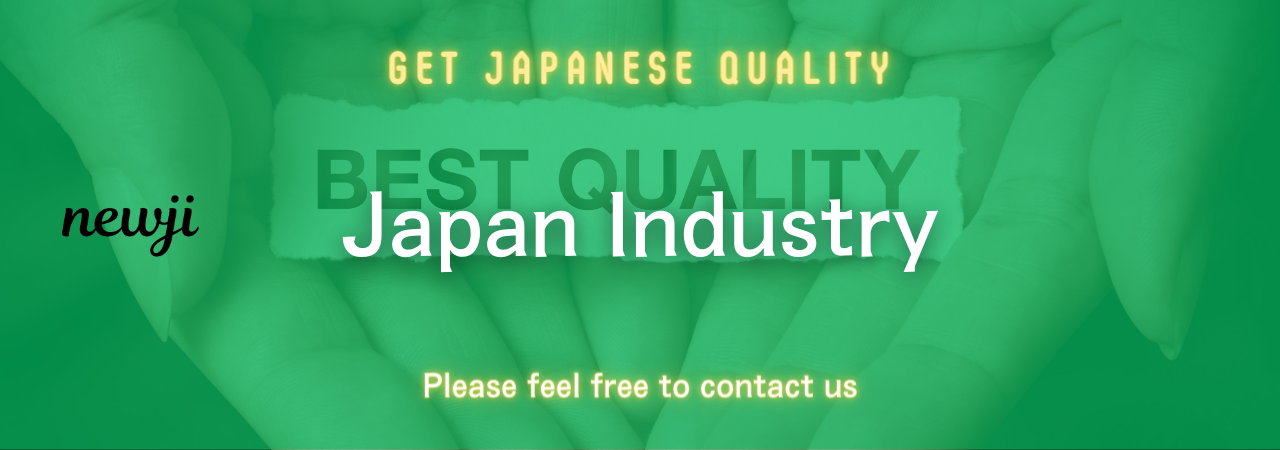
目次
Understanding Soldering Defects
Soldering is a fundamental process in the manufacturing of electronic devices.
Despite its widespread use and relatively straightforward nature, soldering is not without its challenges.
Understanding soldering defects is crucial for ensuring the reliability and quality of electronic assemblies.
Soldering defects can occur due to a variety of reasons, including improper temperature control, poor component placement, contamination, and inadequate flux application.
These defects can lead to circuit failure, impacting the performance and longevity of electronic devices.
Therefore, identifying and addressing the root causes of these defects is essential for manufacturers aiming to produce high-quality products.
Common Types of Soldering Defects
There are several common types of soldering defects that manufacturers need to be aware of.
One of the most frequent defects is insufficient solder, which happens when there is not enough solder to make a reliable connection between the components.
This can lead to weak joints that may easily break or fail.
Another common defect is solder bridging, where excess solder forms an unintended connection between adjacent pads or tracks on a circuit board.
Solder bridging can cause electrical shorts and potentially damage the circuit.
Cold solder joints are also a prevalent issue, characterized by a grainy or dull appearance.
These joints occur when the solder does not reach the proper temperature to form a strong bond with the components and the circuit board.
Causes of Soldering Defects
Understanding the causes of soldering defects is the first step towards developing a strategy to prevent them.
One major cause is improper temperature control during the soldering process.
Each type of solder has a specific melting point, and failing to reach this temperature can result in cold joints.
Another common cause is contamination, which can occur when dust, oils, or other foreign substances are present on the soldering site.
Such contamination can prevent the solder from properly adhering to the components and the circuit board.
Poor component placement is also a significant contributor to soldering defects.
If components are not accurately positioned on the board, they may not form solid connections with the solder, leading to weak joints.
Additionally, inadequate flux application can prevent solder from flowing correctly, resulting in incomplete or poor-quality joints.
Preventing Soldering Defects
Preventing soldering defects requires a systematic approach that addresses the root causes.
One critical step is ensuring proper temperature control during the soldering process.
Using precision temperature-controlled soldering equipment can help maintain the ideal temperature for the type of solder being used.
Maintaining a clean work environment is also essential.
Regular cleaning of the components, circuit boards, and soldering equipment can prevent contamination, which could otherwise lead to soldering defects.
Accurate component placement is crucial for defect prevention.
Automated pick-and-place machines can precisely place components on the circuit board, minimizing the risk of misalignment and weak joints.
Using the proper amount and type of flux can significantly improve solder quality and prevent defects.
Flux helps prepare component surfaces, promoting better solder flow and adhesion.
Soldering Mounting Process
The soldering mounting process is a series of steps designed to ensure reliable and high-quality solder joints.
It begins with the preparation of the circuit board and components.
This involves cleaning all surfaces to remove any contaminants that could interfere with solder adhesion.
Next, the components are placed onto the board, typically using automated equipment for precision.
This step is critical, as accurate placement ensures that components are correctly aligned for soldering.
The soldering process itself involves heating the solder to the appropriate temperature to create strong, durable joints.
Proper temperature control is vital to avoid cold joints or overheating, which can damage components.
Finally, the soldered joints are inspected for quality.
Visual inspection and testing methods such as X-ray or automated optical inspection can help identify any defects that occurred during the soldering process.
Using Technology to Improve Soldering
Advancements in technology have provided tools and techniques that significantly improve the soldering process.
For instance, reflow soldering ovens offer automated temperature control, ensuring that each section of the circuit board receives the correct amount of heat.
This helps to avoid defects such as cold joints or overheating.
Machine vision technology in automated optical inspection systems allows for real-time analysis of solder joints, identifying any defects quickly and efficiently.
These systems can detect issues that might be missed by the human eye, leading to higher reliability in electronic assemblies.
Importance of Training and Skill Development
While technology plays a crucial role in preventing soldering defects, skilled operators are equally important.
Proper training and skill development programs ensure that those involved in the soldering process understand the mechanics of soldering and the importance of precise operation.
Skilled operators can identify potential issues before they lead to defects, improving the overall quality of the soldering process.
Conclusion
Understanding the mechanisms behind soldering defects and implementing a robust soldering mounting process are vital for producing high-quality electronic devices.
By addressing the root causes of defects, such as temperature control, contamination, and inaccurate placement, manufacturers can significantly improve the reliability of their products.
Technology and skilled operators play a crucial role in this process, ensuring each solder joint meets exacting standards.
資料ダウンロード
QCD管理受発注クラウド「newji」は、受発注部門で必要なQCD管理全てを備えた、現場特化型兼クラウド型の今世紀最高の受発注管理システムとなります。
ユーザー登録
受発注業務の効率化だけでなく、システムを導入することで、コスト削減や製品・資材のステータス可視化のほか、属人化していた受発注情報の共有化による内部不正防止や統制にも役立ちます。
NEWJI DX
製造業に特化したデジタルトランスフォーメーション(DX)の実現を目指す請負開発型のコンサルティングサービスです。AI、iPaaS、および先端の技術を駆使して、製造プロセスの効率化、業務効率化、チームワーク強化、コスト削減、品質向上を実現します。このサービスは、製造業の課題を深く理解し、それに対する最適なデジタルソリューションを提供することで、企業が持続的な成長とイノベーションを達成できるようサポートします。
製造業ニュース解説
製造業、主に購買・調達部門にお勤めの方々に向けた情報を配信しております。
新任の方やベテランの方、管理職を対象とした幅広いコンテンツをご用意しております。
お問い合わせ
コストダウンが利益に直結する術だと理解していても、なかなか前に進めることができない状況。そんな時は、newjiのコストダウン自動化機能で大きく利益貢献しよう!
(β版非公開)