- お役立ち記事
- Etching rate control and process stabilization that new employees in the process technology department of the semiconductor industry should learn
Etching rate control and process stabilization that new employees in the process technology department of the semiconductor industry should learn
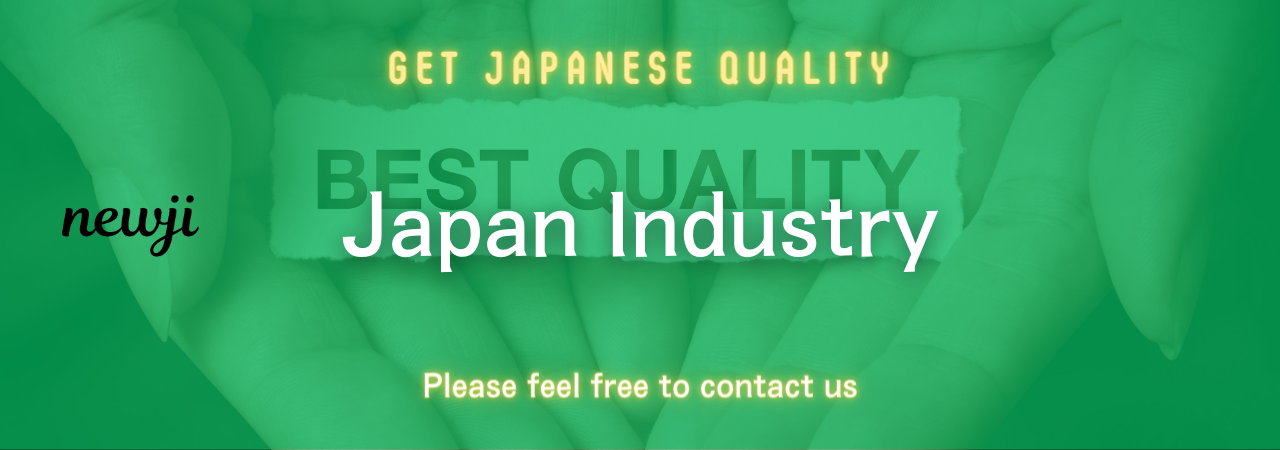
目次
Understanding Etching in Semiconductor Manufacturing
Etching is a critical process in semiconductor manufacturing, where it is used to precisely remove layers from the surface of a silicon wafer.
This function allows for the creation of intricate patterns that form the circuits in electronic devices.
Effective etching is pivotal for ensuring the quality and functionality of semiconductors.
New employees in the process technology department must grasp the fundamentals of etching to contribute to process stabilization and improvement.
The Basics of Etching Rate
The etching rate refers to how quickly material is removed from the wafer during the etching process.
It is an essential metric that needs to be consistently controlled to achieve desired outcomes.
Factors influencing the etching rate include the type of chemical used, the temperature of the process, and the etching method—be it wet or dry etching.
Understanding these factors enables process engineers to tweak conditions and stabilize production lines for superior quality control in semiconductor manufacturing.
Factors Affecting Etching Rate
Chemical Composition
The choice of chemical or gas can dramatically affect the etching rate.
For instance, certain chemicals might be faster at removing specific materials but could pose challenges with precision and uniformity.
An in-depth knowledge of chemistry can aid in predicting and controlling these variances.
Temperature Control
Temperature is another critical factor impacting the etching rate.
Higher temperatures typically increase the etching rate, but they might endanger the quality and precision of the etching.
Process stabilization relies on maintaining optimal temperature ranges to avert overheating while ensuring efficient removal of unwanted layers.
Exposure Time
The time a wafer is exposed to the etching chemicals or plasma also determines the etching rate.
Longer exposures might lead to over-etching, while insufficient exposure can result in incomplete pattern formation.
Balancing exposure time is crucial for achieving precise semiconductor structures.
Methods of Controlling Etching Rate
Maintaining accurate control over the etching rate is a major focus for process engineers.
It involves sophisticated techniques and a thorough understanding of various influencing factors.
Monitoring and Real-Time Adjustments
Using advanced monitoring systems, engineers can track the etching process in real time.
These systems use sensors to update operators on crucial parameters like temperature, pressure, and chemical concentration.
Real-time data facilitates immediate adjustments, ensuring a consistent etching rate and contributing significantly to process stabilization.
Recipe Optimization
Each semiconductor production run follows a predefined set of instructions known as a “recipe.”
Recipe optimization involves refining these instructions to achieve the desired etching outcomes with greater consistency.
Engineers systematically adjust variables such as chemical concentrations and exposure times to perfect these recipes.
Process Calibration and Validation
Regular calibration of the etching equipment and validation of the process can prevent deviation from desired etching rates.
This involves routine maintenance checks and testing prototypes through trial runs, which help establish benchmarks for process optimization.
Importance of Process Stabilization
Achieving process stabilization is crucial in semiconductor fabrication as it ensures predictable and repeatable outcomes.
Stable processes not only enhance yield but lead to cost reduction by minimizing material wastage and rework.
A stabilized etching process also improves device reliability, which is vital for maintaining competitive parity in the semiconductor market.
Consistency and Quality
Process stabilization leads to greater product uniformity and consistency.
Consistent etch rates create circuits with precise and accurate dimensions, which is essential for ensuring the electronic performance of semiconductor devices.
Enhancing Efficiency
Stable processes minimize delays and downtime, thereby increasing throughput.
Employees who understand how to manage the etching process contribute to operational efficiency, which is a key performance indicator for success in semiconductor manufacturing.
Learning and Growth for New Employees
New employees should actively engage with both theoretical learning and hands-on experience to gain a comprehensive understanding of etching processes.
Training Programs
Attend training programs and workshops organized by the company to understand the latest technologies and methodologies associated with etching.
These programs can also provide insights into troubleshooting and process improvement techniques.
Mentorship Opportunities
Leverage mentorship opportunities with seasoned professionals in the industry.
Mentors can offer invaluable advice, share practical experiences, and guide new employees through complex troubleshooting processes in a real-world setting.
Conclusion
In the semiconductor industry, new employees in the process technology department play a crucial role in controlling the etching rate and achieving process stabilization.
Their understanding of etching dynamics impacts the quality and performance of semiconductor devices significantly.
Through appropriate training and continuous learning, employees can make meaningful contributions toward more efficient and effective manufacturing processes.
By prioritizing these aspects, companies can maintain their competitive edge in the rapidly evolving semiconductor market.
資料ダウンロード
QCD調達購買管理クラウド「newji」は、調達購買部門で必要なQCD管理全てを備えた、現場特化型兼クラウド型の今世紀最高の購買管理システムとなります。
ユーザー登録
調達購買業務の効率化だけでなく、システムを導入することで、コスト削減や製品・資材のステータス可視化のほか、属人化していた購買情報の共有化による内部不正防止や統制にも役立ちます。
NEWJI DX
製造業に特化したデジタルトランスフォーメーション(DX)の実現を目指す請負開発型のコンサルティングサービスです。AI、iPaaS、および先端の技術を駆使して、製造プロセスの効率化、業務効率化、チームワーク強化、コスト削減、品質向上を実現します。このサービスは、製造業の課題を深く理解し、それに対する最適なデジタルソリューションを提供することで、企業が持続的な成長とイノベーションを達成できるようサポートします。
オンライン講座
製造業、主に購買・調達部門にお勤めの方々に向けた情報を配信しております。
新任の方やベテランの方、管理職を対象とした幅広いコンテンツをご用意しております。
お問い合わせ
コストダウンが利益に直結する術だと理解していても、なかなか前に進めることができない状況。そんな時は、newjiのコストダウン自動化機能で大きく利益貢献しよう!
(Β版非公開)