- お役立ち記事
- Evaluating Mechanical Strength in Manufacturing
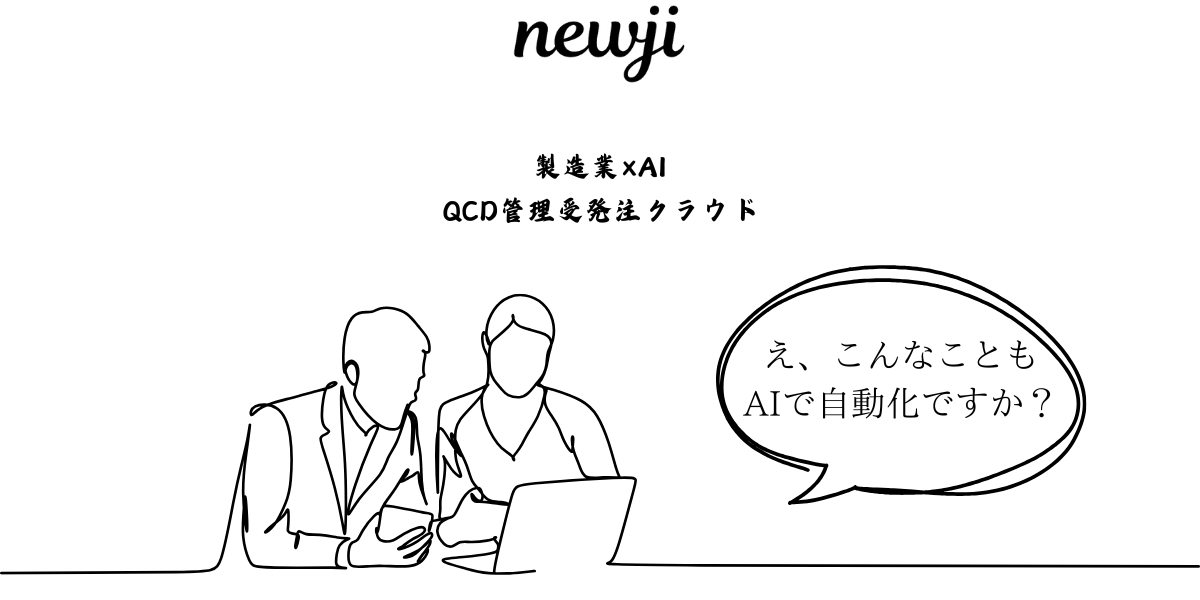
Evaluating Mechanical Strength in Manufacturing
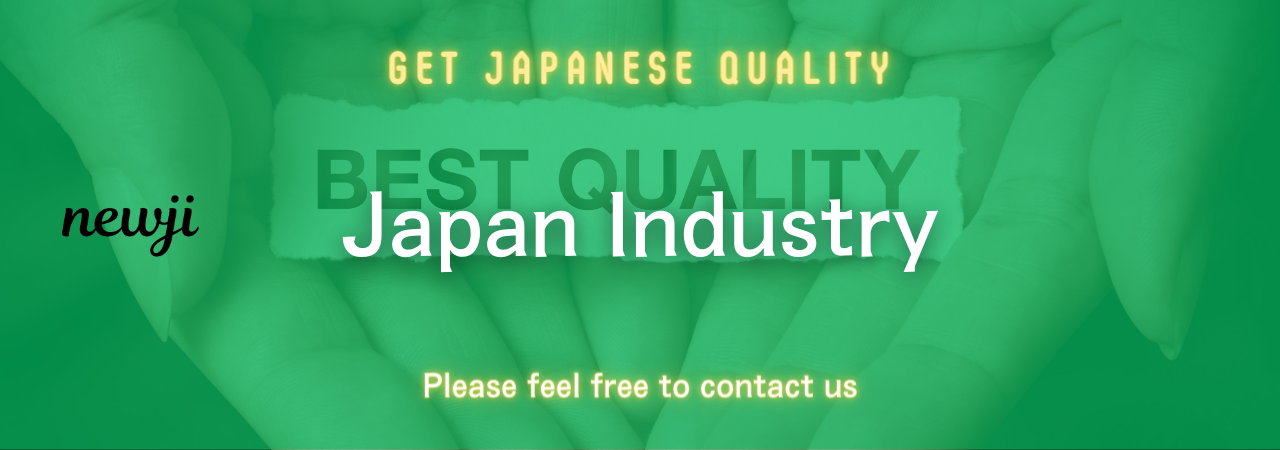
目次
Understanding Mechanical Strength in Manufacturing
Manufacturing is a pivotal industry that shapes the backbone of economies worldwide.
One of the critical aspects that determine the success and reliability of manufacturing products is mechanical strength.
Mechanical strength refers to the ability of a material or component to withstand forces without breaking or deforming.
In this article, we’ll explore the significance of mechanical strength in manufacturing and how it is evaluated to ensure safety and durability in products.
Importance of Mechanical Strength
Mechanical strength is fundamental in manufacturing because it determines how a product will perform under stress.
From the frame of an aircraft to the shell of a smartphone, every component must meet specific strength criteria to function safely and effectively.
Products with adequate mechanical strength have a longer lifespan, provide safety to users, and reduce the potential for costly replacements or repairs.
In industries such as aerospace, automotive, and construction, mechanical strength is not just a preference; it is a necessity that complies with safety standards and certifications.
Understanding Stress and Strain
To fully understand mechanical strength, it is essential to grasp the concepts of stress and strain.
Stress refers to the internal force exerted by a material, calculated by dividing the force applied by the area over which it is distributed.
Strain, on the other hand, measures the deformation or displacement experienced by the material.
When evaluating mechanical strength, engineers assess how a material reacts to these forces, which informs them of any potential weaknesses.
Methods to Evaluate Mechanical Strength
Evaluating mechanical strength involves different methods, each serving specific purposes and industries.
The most common tests include tensile testing, compression testing, and impact testing.
Tensile Testing
Tensile testing involves stretching a material to assess its response to pulling forces.
During this test, a sample material is subjected to a controlled tension in a tensile testing machine until it breaks.
The data collected include the material’s tensile strength, which is the maximum stress it can withstand before failure.
Tensile testing provides crucial insights into a material’s elasticity and plasticity, helping manufacturers understand how materials will behave under real-world conditions.
Compression Testing
Compression testing is conducted to evaluate a material’s behavior under compressive forces.
In this test, a material is compressed with increasing force until it yields or breaks.
The results reveal critical information about the material’s compression strength, helping to determine its suitability for bearing loads.
This evaluation is particularly important in the construction industry, where materials like concrete and metals are often subjected to significant compressive stresses.
Impact Testing
Impact testing assesses a material’s ability to resist sudden heavy impacts.
This test involves striking a material with a weight to measure its toughness and ability to absorb energy.
Impact testing is crucial in industries where accidental impacts can occur, such as automotive and aerospace sectors, to ensure components can withstand unforeseen forces without catastrophic failure.
Materials and Their Mechanical Properties
Different materials possess varying mechanical properties; therefore, understanding these properties helps manufacturers select the appropriate materials for their products.
Common materials used in manufacturing include metals, polymers, ceramics, and composites.
Metals
Metals such as steel, aluminum, and titanium are known primarily for their tensile and compression strength.
They are widely used in industries where durability and strength are crucial, such as construction and automotive.
The mechanical strength of metals can be enhanced through processes like heat treatment and alloying.
Polymers
Polymers, including plastics and rubbers, provide flexibility and resilience.
While they may not always match the mechanical strength of metals, their lightweight nature and capacity to absorb energy make them ideal for certain applications like packaging and consumer goods.
Ceramics
Ceramics are renowned for their high compression strength and excellent heat resistance.
These materials are suitable for applications involving high temperatures, such as in the production of tiles and certain aerospace components.
However, ceramics can be brittle and may not withstand high tensile forces.
Composites
Composites are engineered materials composed of two or more distinct materials.
They combine the mechanical strengths of their constituent materials, often resulting in superior performance.
Composite materials are increasingly used in industries like aerospace, where a high strength-to-weight ratio is critical.
Implementing Quality Control in Manufacturing
To ensure the mechanical strength of products, industries implement rigorous quality control measures throughout the manufacturing process.
These measures include routine testing, inspection, and adherence to industry standards.
Standardization and Certification
Adhering to international standards such as ISO and ASTM ensures products meet universal quality benchmarks.
In addition, certifications can enhance consumer trust, indicating that the products have passed stringent mechanical strength evaluations.
Continuous Improvement
Engaging in continuous improvement processes helps manufacturers enhance the mechanical strength of their products.
This involves researching new materials, refining testing methods, and adopting advanced technologies for more accurate evaluations.
Conclusion
Understanding and evaluating mechanical strength in manufacturing is crucial for producing high-quality and reliable products.
By employing various testing methods and adhering to strict quality controls, manufacturers can ensure their products meet industry standards and perform effectively under stress.
Ultimately, focusing on mechanical strength helps safeguard users, extend the life of products, and uphold the reputation of the manufacturing industry.
資料ダウンロード
QCD調達購買管理クラウド「newji」は、調達購買部門で必要なQCD管理全てを備えた、現場特化型兼クラウド型の今世紀最高の購買管理システムとなります。
ユーザー登録
調達購買業務の効率化だけでなく、システムを導入することで、コスト削減や製品・資材のステータス可視化のほか、属人化していた購買情報の共有化による内部不正防止や統制にも役立ちます。
NEWJI DX
製造業に特化したデジタルトランスフォーメーション(DX)の実現を目指す請負開発型のコンサルティングサービスです。AI、iPaaS、および先端の技術を駆使して、製造プロセスの効率化、業務効率化、チームワーク強化、コスト削減、品質向上を実現します。このサービスは、製造業の課題を深く理解し、それに対する最適なデジタルソリューションを提供することで、企業が持続的な成長とイノベーションを達成できるようサポートします。
オンライン講座
製造業、主に購買・調達部門にお勤めの方々に向けた情報を配信しております。
新任の方やベテランの方、管理職を対象とした幅広いコンテンツをご用意しております。
お問い合わせ
コストダウンが利益に直結する術だと理解していても、なかなか前に進めることができない状況。そんな時は、newjiのコストダウン自動化機能で大きく利益貢献しよう!
(Β版非公開)