- お役立ち記事
- Evaluating Product Protection in Corrosive Environments with Gas Corrosion Tests
月間76,176名の
製造業ご担当者様が閲覧しています*
*2025年3月31日現在のGoogle Analyticsのデータより
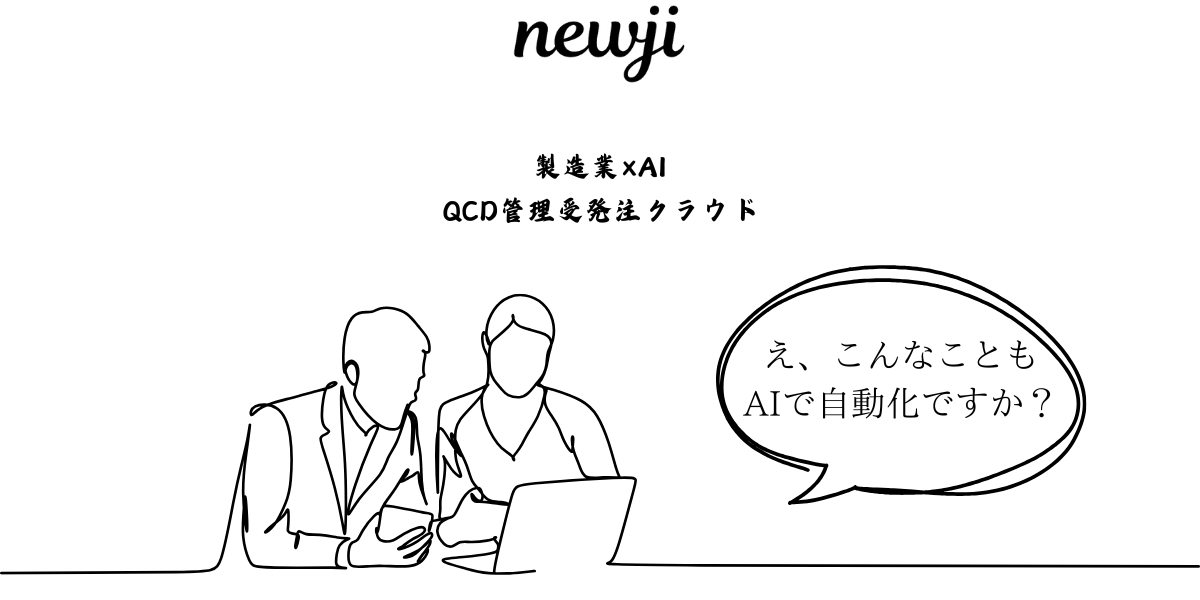
Evaluating Product Protection in Corrosive Environments with Gas Corrosion Tests
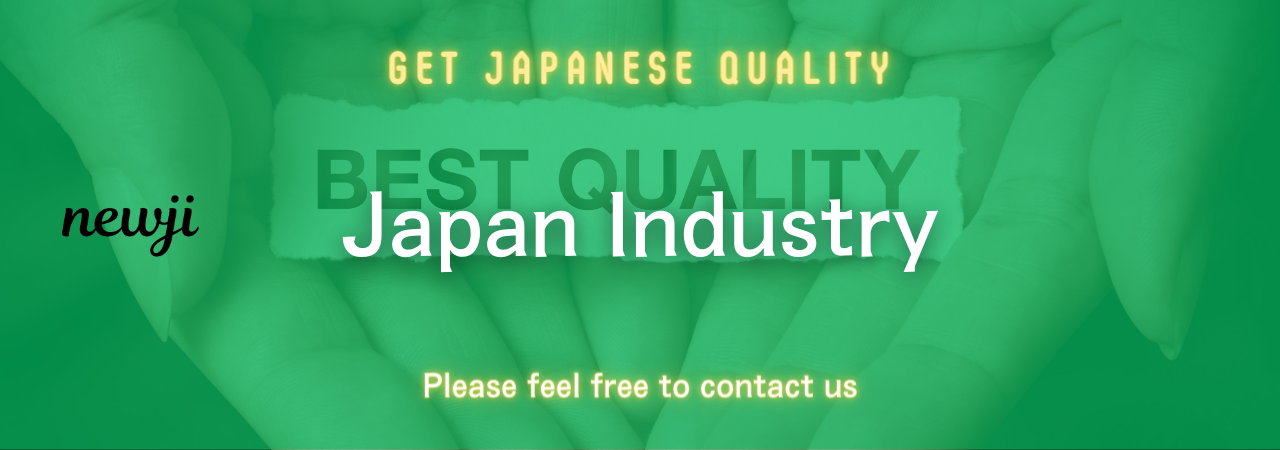
目次
Understanding Gas Corrosion Tests
When we talk about protecting products from damage, it’s crucial to consider the effects of corrosion, especially in environments that have a lot of gases.
These are called corrosive environments.
Gas corrosion tests help us understand how products react to these harsh conditions.
By evaluating the product’s resistance, companies can ensure long-lasting quality and performance.
What is Corrosive Gas?
Corrosive gases are harmful gases that can cause metals or other materials to deteriorate.
Some common examples are sulfur dioxide, hydrogen sulfide, and chlorine gas.
When products are exposed to these gases, they can start to corrode, which means they gradually break down.
The Importance of Gas Corrosion Tests
Gas corrosion tests are essential because they help determine how resistant a product is to corrosive gases.
This information is vital for many industries, including manufacturing, automotive, and electronics.
If a product fails to resist corrosion, it can lead to failures, safety hazards, and costly replacements.
How Do Gas Corrosion Tests Work?
Preparing the Sample
First, a sample of the product is prepared.
This sample should represent the product’s material and coatings accurately.
Controlled Exposure
Next, the sample is placed in a controlled environment where it is exposed to specific corrosive gases.
The concentration, temperature, and humidity levels are carefully monitored to simulate real-world conditions.
Duration of the Test
The test can last for different durations, depending on the requirements.
It might run for a few hours to several weeks.
The goal is to observe how the sample reacts over time.
Evaluating Test Results
Visual Inspection
After the test, the sample is inspected visually.
Any changes, like discoloration, rust, or cracks, are noted.
Weight Loss Measurement
In some cases, the sample’s weight is measured before and after the test.
The difference in weight can indicate how much material has corroded.
Microscopic Analysis
A more detailed analysis might involve looking at the sample under a microscope.
This helps to understand the extent and type of corrosion that has occurred.
Choosing the Right Materials
The results of gas corrosion tests can guide material selection.
Materials like stainless steel, coated metals, and specific alloys can offer better corrosion resistance.
Understanding which materials perform well can help in designing durable products.
Applications of Gas Corrosion Tests
Electronics Industry
In the electronics industry, corrosion can lead to failure of circuits and connections.
Gas corrosion tests help ensure that components like connectors and circuit boards can withstand corrosive environments.
Automotive Industry
Vehicles often operate in environments where they are exposed to gases like sulfur dioxide from exhaust.
Gas corrosion tests help ensure that critical components like brake systems and fuel lines are protected.
Construction Industry
Buildings and structures might be exposed to corrosive gases, especially in industrial areas.
Testing materials used in construction can help in choosing the right paints and coatings to prevent damage.
Improving Product Design
Gas corrosion tests also contribute to improving product design.
By understanding how and where corrosion occurs, designers can make informed decisions.
This might involve adding protective coatings, using corrosion-resistant materials, or altering the product’s shape to minimize exposure.
Environmental Considerations
It’s not just about protecting products.
Understanding gas corrosion can also help in environmental protection.
For instance, industries can take steps to minimize emissions of corrosive gases.
This can benefit surrounding communities and ecosystems.
Common Standards and Protocols
Many industries follow standard protocols for gas corrosion tests.
These standards ensure that tests are consistent and reliable.
Some widely recognized standards include ASTM (American Society for Testing and Materials) and ISO (International Organization for Standardization).
Future of Gas Corrosion Testing
With advances in technology, gas corrosion tests continue to evolve.
New methods and equipment make testing more accurate and efficient.
We can expect even better insights into how to protect products from corrosion in the future.
Conclusion
Gas corrosion tests are a vital part of ensuring product durability and performance in corrosive environments.
By understanding and addressing the challenges posed by corrosive gases, industries can create safer, longer-lasting products.
Whether it’s in electronics, automotive, or construction, these tests play a crucial role in quality assurance.
Through continuous improvement and adherence to standards, the future of gas corrosion testing looks promising.
資料ダウンロード
QCD管理受発注クラウド「newji」は、受発注部門で必要なQCD管理全てを備えた、現場特化型兼クラウド型の今世紀最高の受発注管理システムとなります。
ユーザー登録
受発注業務の効率化だけでなく、システムを導入することで、コスト削減や製品・資材のステータス可視化のほか、属人化していた受発注情報の共有化による内部不正防止や統制にも役立ちます。
NEWJI DX
製造業に特化したデジタルトランスフォーメーション(DX)の実現を目指す請負開発型のコンサルティングサービスです。AI、iPaaS、および先端の技術を駆使して、製造プロセスの効率化、業務効率化、チームワーク強化、コスト削減、品質向上を実現します。このサービスは、製造業の課題を深く理解し、それに対する最適なデジタルソリューションを提供することで、企業が持続的な成長とイノベーションを達成できるようサポートします。
製造業ニュース解説
製造業、主に購買・調達部門にお勤めの方々に向けた情報を配信しております。
新任の方やベテランの方、管理職を対象とした幅広いコンテンツをご用意しております。
お問い合わせ
コストダウンが利益に直結する術だと理解していても、なかなか前に進めることができない状況。そんな時は、newjiのコストダウン自動化機能で大きく利益貢献しよう!
(β版非公開)